Introduction to Tribology
Wear
Wear is the loss of materials, usually due to sliding. Typically wear is undesirable as it can lead to increased friction and ultimately to component failure. Like friction, wear is typically minimized by using a lubricant to separate the two bodies so that they do not directly touch one another.
The two most common types of wear are abrasive, in which a harder material removes material from a softer one, and adhesive, in which two bodies adhere to one another locally, so that material is transferred from one to the other. These two wear modes are illustrated below. In adhesive wear, the two sliding surfaces, or features on those surfaces, called asperties, temporarily form junctions between the two materials. Then, as sliding continues, those junctions have to be broken. If a junction is weak enough, shear will occur at the original interface between the two bodies and there will be negligible wear. However, if a junction is stronger than one of the two materials, then shear may occur within the material, resulting in adhesive wear. Abrasive wear occurs when a harder material ploughs into a softer surface, removing material from it. This mode of wear tends to be more severe than adhesive wear in most cases. In abrasive wear, if ploughing is done by an asperity on the harder material, the process is called two-body wear; if ploughing occurs through contact with a wear particle or debris, then the process is called three-body wear.
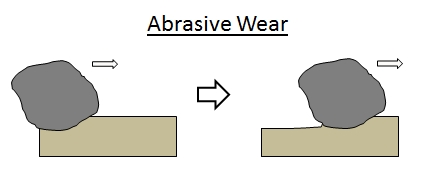
The amount of wear can be measured in several different ways, most of which involve measurement of either mass change or the size of a worn region. The latter is more common since it can be applied for any case where there is a worn region (wear scar) that is large enough to measure. Wear scar size can be measured using an optical image, such as that shown below, or using profilometry. In the case of an optical image, parameters such as the wear depth or wear volume must be calculated using a measured wear scar dimension and the known geometry of the contacting body. A profilometer can give a direct measurement of both the in-plane dimensions and depth of the wear scar. Wear can be reported simply as a volume or as one of the in-plane dimensions of the wear scar, such as the wear depth shown in the example below. In this example, the wear increases with number of cycles, as expected, and one of the samples exhibits more wear resistance than the other.
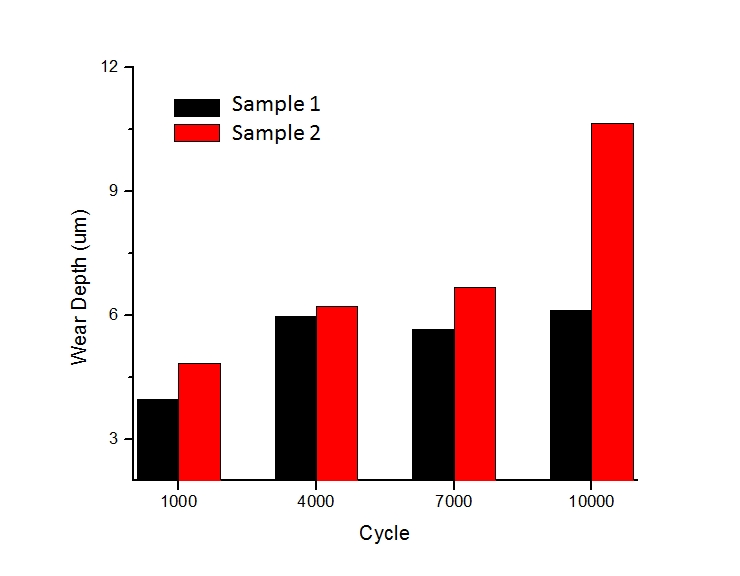
Wear is typically quantified using what is called a wear rate, which is how fast material is removed from the surface. Although several different units for wear rate are acceptable, a common unit is volume, V, per distance, d. In this form, the wear rate (V/d) can be described by Archard's wear law: V/d = K W / H, where W is the load, H is material hardness and K is a material-specific wear coefficient. This expression states that, as expected, there will be more wear at higher loads and on softer materials. To facilitate comparison between tests performed at different loads, the wear rate is often normalized by the load such that wear is reported in units of volume per distance per load. The other term in Archard's wear law is the wear coefficient. There is much discussion about this coefficient since its value varies by orders of magnitude and is highly dependent on materials, surface features as well as operating and environment conditions. However, generally speaking, the trends predicted by the simple Archard wear equation have been found to describe experimental observations well in many cases.
In addition to adhesion and abrasion, another common wear mode in mechanical components is surface fatigue. Fatigue is, as the name implies, a process that occurs after many sliding cycles. It is common in components that have rolling elements where subsurface stresses lead to cracks within the material. These cracks grow towards the surface over time, eventually resulting in worn material, a process known as pitting. Other modes of wear that can occur in some components and under some conditions are impact by erosion or percussion, chemical wear (such as corrosion), and electrical-arc-induced wear.
Click here to return to Introduction to Tribology