Introduction to Tribology
Lubricants and Lubrication
Lubricants are primarily used to separate two sliding surfaces to minimize friction and wear. They also perform other functions, such as carrying heat and contaminants away from the interface. Lubricants are often liquids, typically consisting of oil and added chemicals, called additives, which help the oils better perform specific functions. However, there are some applications where lubricants can be gases or even solids.
The basic premise of liquid lubrication is that, although there is resistance to shear within the fluid due to its viscosity, that viscous resistance is much smaller than the frictional resistance during dry sliding. The performance of a lubricated contact is therefore largely determined by viscosity. Viscosity is a fluid's resistance to flow and is the ratio of shear stress to shear strain rate. A fluid in which viscosity is a constant, i.e. there is a linear relationship between stress and strain rate, is called Newtonian. However, in reality, many lubricants experience changes in viscosity due to temperature, pressure and shear rate during operating, and so behave as non-Newtonian fluids under some conditions. Controlling these variations is important because viscosity plays a key role in determining lubricant film thickness. A very small viscosity will result in a film that is too thin to prevent surface asperities from coming into contact, while a very large viscosity will result in sufficient surface separation, but may also lead to unacceptably high viscous friction. In general, we want to use the least viscous fluid that results in complete surface separation. Viscosity is measured using an instrument called a rheometer such as the one in our lab shown below.
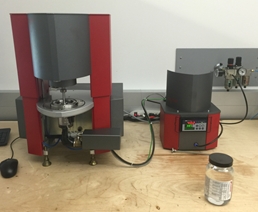
Although the friction in lubricated interfaces is typically less than that without a lubricant, there is still friction, and the magnitude of that friction depends on the fluid viscosity and operating conditions. The effects of relative speed, load and viscosity on friction are described by the Stribeck curve shown below. This curve also identifies three key lubrication regimes: boundary, mixed and full film. At low speed, low viscosity, or high load, the fluid cannot support the load and there is direct surface-surface contact. This is called boundary lubrication, where only lubricant molecules adsorbed on the surface provide any friction reduction, and the friction is relatively high under any conditions. At high speed, high viscosity, or low load, the fluid completely separates the two surfaces. This is called the full film or hydrodynamic lubrication regime. In this regime, friction increases with speed, viscosity and the inverse of load because those conditions result in more viscous resistance to shear. Between boundary and full film lubrication, there is a regime called mixed lubrication where some parts of the interface are separated by fluid and others are not. Various components operate in one or more of the lubrication regimes during operation.
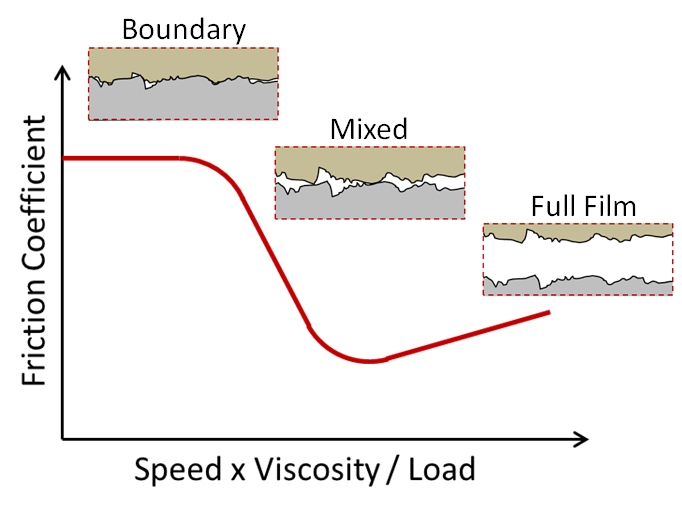
Lubricants are formulated to meet the demands of a wide variety of applications. Formulations begin with one or more mineral or synthetic base oils. Base oils can be derived from several sources, including crude oil, natural gas, and plants or animals, where the source of the base oil will determine many of the formulated fluid's final properties. Most base oils are fortified with chemical additives to enable optimum performance. Additives may be dissolved or suspended in the fluid and typically comprise between 0.1 and 30 percent of the total oil volume. There are additives to perform a variety of functions, including minimizing the variation of viscosity with operating conditions, minimizing boundary friction, increasing chemical stability, and controlling contamination.

Liquid lubricants are extremely effective and are certainly the most widely used types of lubrication. However, there are some conditions or components where liquids are not an option. In some cases, particularly those where light weight is important and the loads are low, an interface can be lubricated by a gas. For example, in air bearings, a thin film of pressurized air can provide a low-friction, load-bearing interface. Another alternative is using solids as a lubricant. Solid lubricants are typically materials that provide low friction because there is little resistance to shear within the materials themselves. For example, materials such as graphite or molybdenum disulfide are layered and so can accommodate shear between their atomic layers. Other solid lubricants are based on soft materials, such as noble metals, whose inherent resistance to shear stress is low. Although solid lubricants are not viable in some cases, the number and variety of applications that might use them, either instead of or in addition to a liquid, is growing rapidly due to recent advancements in materials tribology.
Click here to return to Introduction to Tribology