Tribological Properties of Lubricating Oil Upcycled from Plastic Wastes (LOUP) Under Electrified Conditions
By Seungjoo Lee | TLT Fellowship Research April 2025
Texas A&M University
Editor’s Note: This month TLT profiles the 2024 recipient of The Elmer E. Klaus Fellowship, Seungjoo Lee (Texas A&M University). The Klaus Fellowship, along with The E. Richard Booser Scholarship, are awarded annually to graduate and undergraduate students, respectively, who have an interest in pursuing a career in tribology. As a requirement for receiving an STLE scholarship, students are given the opportunity to participate in a tribology research project and to submit a report summarizing their research. For more information on the Elmer E. Klaus Fellowship, visit www.stle.org.
Seungjoo Lee is a doctoral student in the Department of Mechanical Engineering at Texas A&M University. Prior to Texas A&M University, Lee graduated with bachelor’s and master’s degrees from the Department of Mechanical Engineering of Korea University, Republic of Korea. Lee’s current research focuses on tribological and tribochemical studies of interfaces under electrified environments and lubricants including plastic derived lubricating oils, coatings and solid lubricants, unraveling their unique fundamental tribological mechanisms under dry and lubricated conditions. Lee can be reached at seungjoo0820@tamu.edu.

Seungjoo Lee
Abstract
Plastic pollution is one of the critical environmental issues worldwide mostly due to improper disposal and inefficient recycling methods. In this study, a new class of Lubricating Oils Upcycled from Plastic wastes (LOUPs) were developed and studied for their tribological performance. More specifically, as interest in the development of electric vehicle technology has increased tremendously in recent years, friction and wear performance of LOUP were investigated using a pin-on-disk tribometer under ASTM G99 test conditions with and without electrification. It was found that at moderate currents (0.1 and 0.5 A), thick oxide layers of magnetite formed on the sliding contact surfaces, and at higher currents (1 and 3 A), the extent of tribo-oxidation and hence wear was reduced dramatically. Finally, a protic ionic liquid (PIL) was blended with LOUP for friction and wear reduction. Test results showed that blending LOUP with PIL indeed reduced the wear losses by as much as 27% compared to using pure LOUP under the same condition.
1. Introduction
Even though plastics significantly enhanced industrial advancement and our quality of life, their improper disposal to our environment resulted in a plastic pollution issue by endangering all living species on our planet, including humans.[1, 2] The Organization for Economic Cooperation and Development (OECD) reported that less than 10% of plastic waste is recycled globally while 22% is mismanaged.[3] To ease plastic pollution issues, a variety of mechanical and chemical recycling technologies were developed and used. Mechanical recycling is one of the oldest methods which includes collecting waste plastics, then sorting them accordingly to remanufacture them into the same kind of products.[4] Chemical recycling, such as pyrolysis, is another method where plastic wastes can be broken down into molecular levels to convert into forms of solid, liquid, and gaseous products.[5-7] However, due to operational costs, chemical recycling methods may not be very efficient or effective within a circular economy.[8]
Meanwhile, the automotive companies have lately been spurring the development of battery electric vehicles (BEVs), hybrid electric vehicles (HEVs), plug-in hybrid electric vehicles (PHEVs), and fuel cell electric vehicles (FCEVs) as energy-efficient and environmentally friendly alternatives to the internal combustion engine vehicles (ICEVs). Thereby, research interests in EV technology, including batteries, drivetrain components, and clutches, have lately increased tremendously.[9] Since most lubricants are designed for ICEV applications, newly formulated lubricants are being developed to meet the requirements of EV drivetrains, such as extreme operational conditions of high loads, torques, speeds, temperatures, and high resistance to degradations by electrical discharges.[10] Yet, unknown pending tribological issues still exist when stray electricity flows through the moving components, which is detrimental to the overall performance of EVs.
In this study, a catalytically mediated hydrogenolysis process was employed as a green solution to produce “Lubricating Oil Upcycled from Plastic” (LOUPs) waste. Additionally, this study aims to focus on evaluating the performance and usability of LOUP for electromobility applications. Due to the strong dielectric properties of plastics[11], their role in electromobility, particularly in addressing tribological issues associated with stray electricity passing through tribological interfaces, is of paramount importance. Initial investigations have indicated that the friction and wear properties of lubricating oils derived from plastic wastes, assessed through pin-on-disk experiments, showed comparable or superior performance to conventional lubricants under non-electrified conditions.[12] This research is anticipated to yield insights into the mechanisms and types of tribofilm or oxidation layers generated during sliding conditions when different electrical currents are applied between the contact interfaces. Finally, the tribological properties of LOUP blended with protic ionic liquids will be discussed for potential solutions to mitigate tribological issues under electrified conditions.
2. Materials and Methods
2.1 Lubricating Oil Upcycled from Plastic Wastes (LOUP)
Centrifuge tubes of formulated iPP purchased from Fisher Scientific were shredded in pieces and loaded in a 1-L semi-batch Parr reactor.[13] Then the continuous hydrogenolysis reaction was performed with Pt/SrTiO3 catalyst under 190 psig H2 flowing at 100 SCCM heated at 320°C. Liquid lubricating oil products were then collected in the condensing separator during the reaction and treated to remove possible contaminations from the catalyst. The molar mass distribution of the LOUP sample was Mn= 310 Da and Mw = 440 Da. In addition, a viscometer (Anton Paar, SVM) was used to identify the lubricating properties of LOUP as a lubricant compared to conventional lubricants. Table 1 shows the comparison of lubricants’ properties using different types of base oils. It was found that all lubricating properties of LOUP obtained from the viscometer lay in between those of PAO 2 and PAO 4.
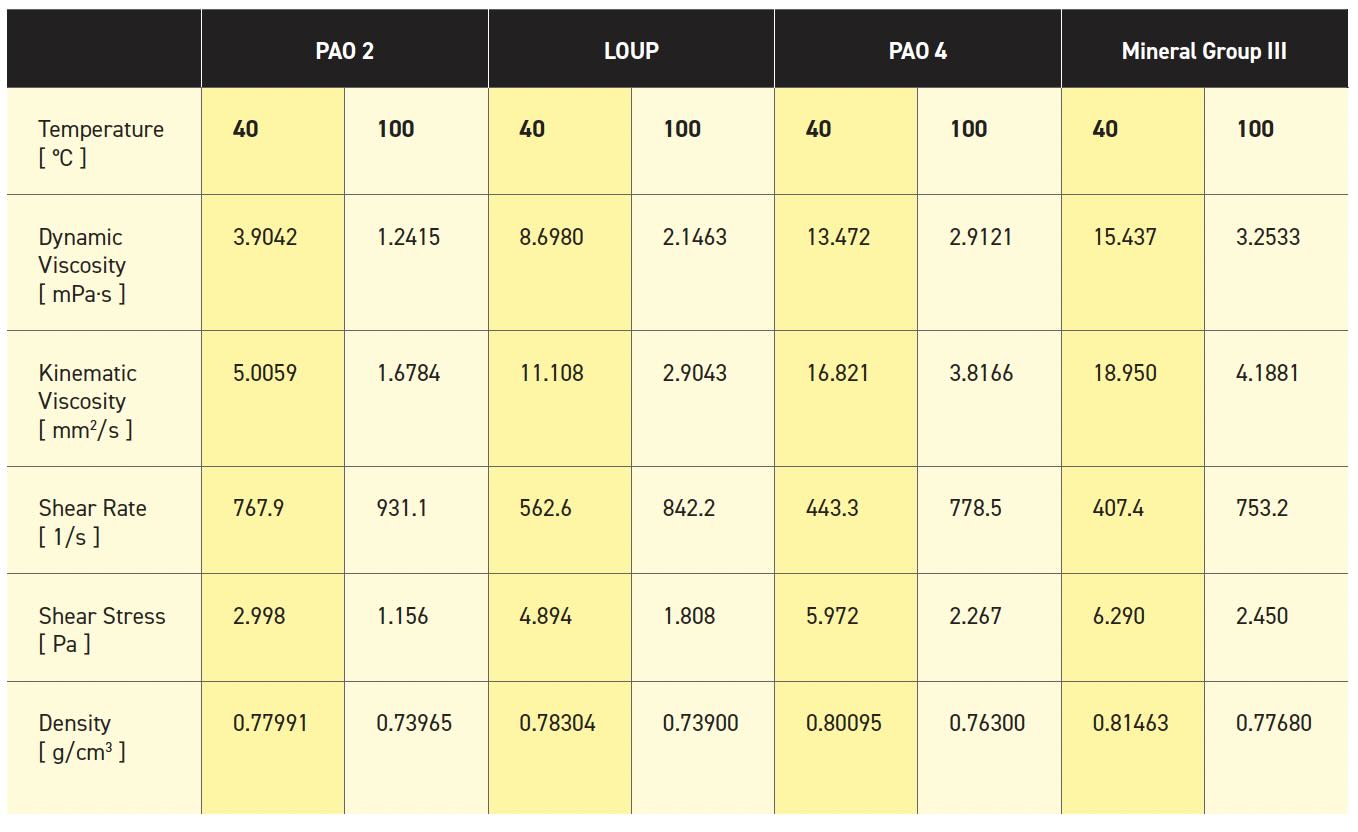
Table 1. Lubricating properties of different types of base oils
Tribological properties of the LOUP as a base oil under unelectrified conditions were initially evaluated and compared to those of the PAO 4 oil. Ball-on-disk experiments were conducted under ASTM G99 conditions where 52100 alloy steel balls and disks were used with a normal of 5 N (maximum Hertzian pressure of 0.8 GPa) with a 0.1 m/s speed for a total distance of 360 m. As illustrated in Figure 1, despite the lower viscosity measurements compared to that of PAO 4, LOUP showed superior friction and wear properties. LOUP’s capabilities of maintaining firm tribofilm between the contact interfaces under extreme load conditions provided steady frictional behavior and reduced wear loss volume than PAO 4, where tribofilm breakdown of PAO 4 increased the metal-to-metal contact, aggravating the fluctuation of frictional forces and wear performance.
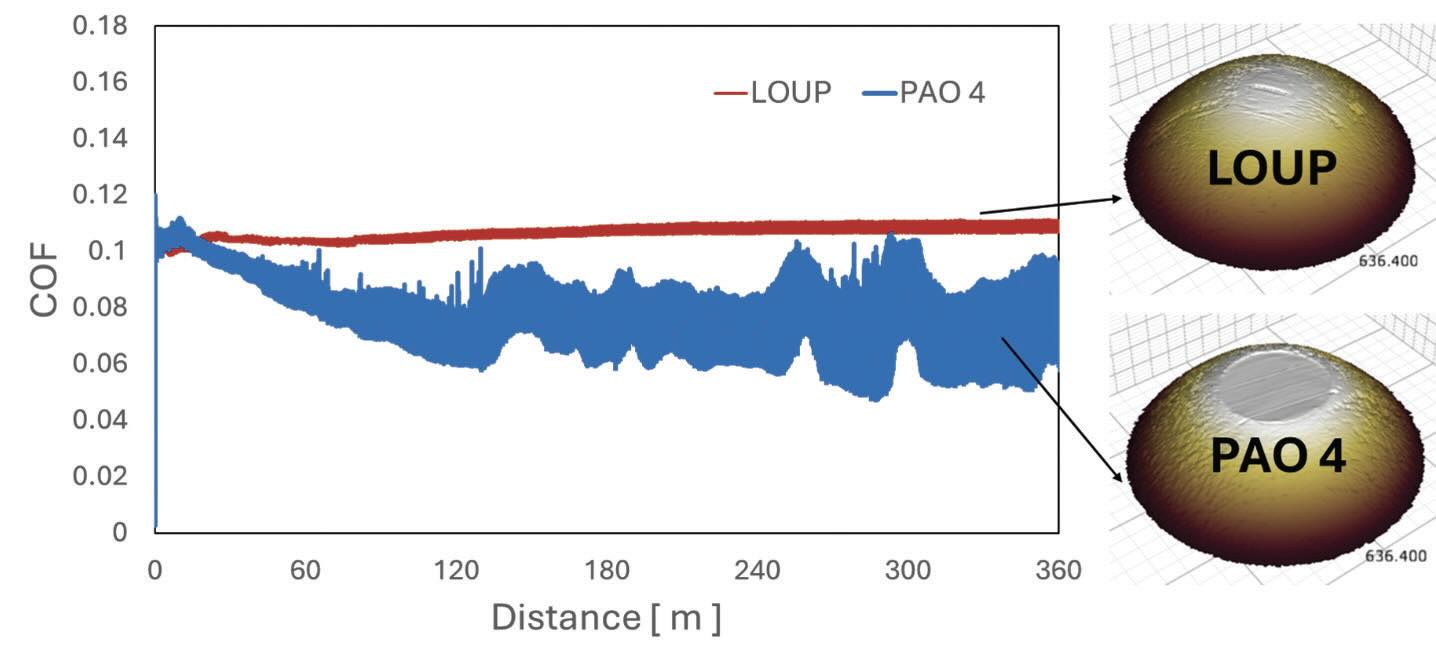
Figure 1. COF trends comparison between LOUP and PAO 4 under unelectrified conditions.
2.2 Sample Preparation and Test Methods
Hardened 52100 alloy steel disks and 100 mm balls with HRC 60 were prepared for the tribo-testing. Specimens were cleaned in ultra sonicating bath with the acetone-isopropanol mixed solution. Ball-on-disk experiments were conducted using the Anton Parr Tribometer (TRB3) under ASTM G99 conditions. A normal load of 5 N with 0.1 m/s velocity (Maximum Hertzian Pressure: 0.8 GPa) for a total distance of 365 m was used for each experiment where all tribo-tests could be tested in a boundary lubrication regime. In each test, 10 µL of LOUP was applied on the wear tracks. The tribometer was specifically designed to perform tribological tests under electrified conditions. To demonstrate the electricity flow from the ball to the disk, the fixed wire was connected to the ball holder, and a carbon brush was implemented on the side of the disk to ensure constant contact during the rotations. DC power supply manufactured by Keithley (Keithly 2230-30-1) was used for supplying electrical DC current. DC current was chosen because it is easy to control, allowing for the observation of tribological behaviors at different electrified conditions. Tribo-test experiments under unelectrified, 0.1, 0.5, 1, and 3 amperes were conducted with at least two repetitions of each condition. After the tribo-test, balls were taken out and rinsed in the heptane to remove organics. Wear properties of the specimen were then analyzed using a non-contact optical profilometer (Bruker, Contour GTK), and surface characterizations were conducted using a Secondary Electron Microscope (JEOL, JSM-IT200) and Raman Spectroscopy (Renishaw inVia™) with UV laser of 532 nm.
3. Results and Discussion
3.1 Tribological Properties
Average Coefficient of Friction (COF) values and frictional behaviors during the tribo-tests obtained using LOUP at different currents are shown in Figure 2. The average COF value obtained under the unelectrified conditions was 0.109 and gradually increased as the current increased, where the highest average COF value of 0.137 was obtained when 3 A was applied. While unelectrified conditions with LOUP showed very stable frictional trends throughout the tribo-test, different behaviors were observed during the experiments under electrified conditions. Under 0.1 A electrified condition, stable frictional behavior was observed in the early stage, although the average COF value slightly increased to 0.117. However, as the tribo-test reached the completion stage, the tribofilm generated by LOUP may have broken down, causing increased frictional fluctuations. The part of the fluctuation may have been caused by the generation and the accumulation of debris particles between the sliding interfaces, which will be discussed later. When the current increased from 0.1 to 0.5 A, a steep increase in wear was also observed.
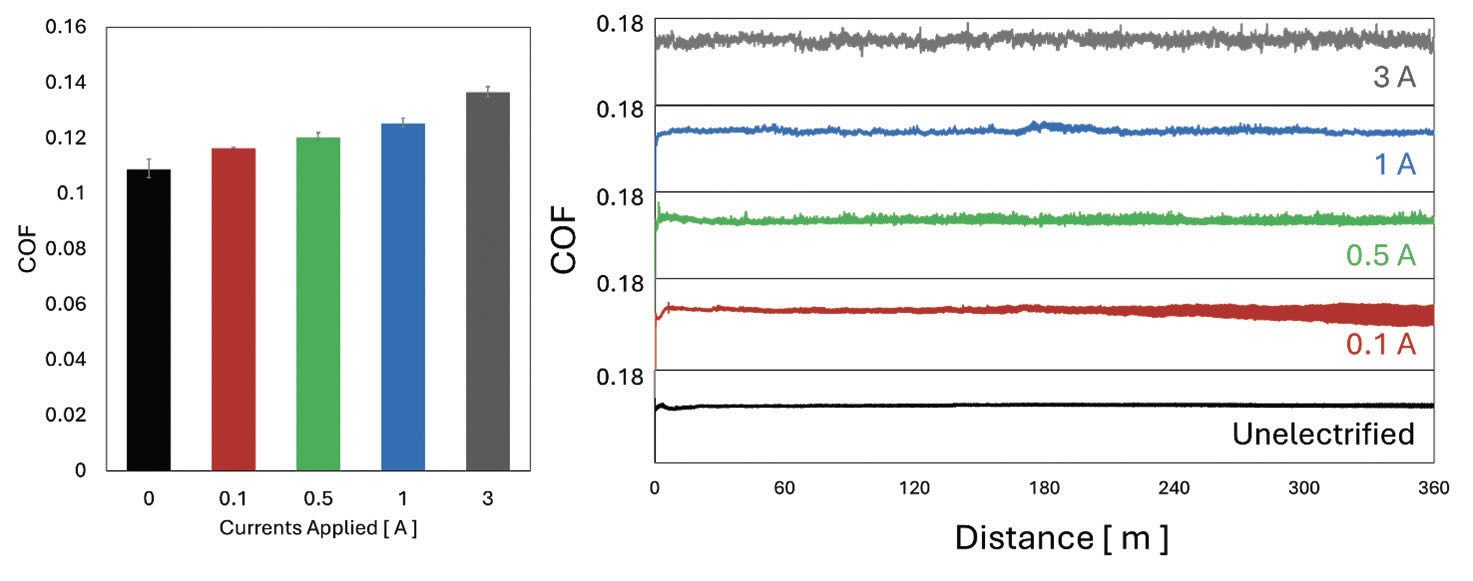
Figure 2. Comparison of average COF values (left) and frictional behaviors (right) at different electrified conditions.
Unlike the frictional results, where progressive increases were observed with increasing electrical currents, wear properties showed a very different and somewhat unusual trend. Figure 3 summarizes the average wear loss volume comparison obtained from the ball under different electrified conditions and their 3D surface profiles. Under unelectrified conditions, no significant wear was noticed, but some abrasive wear marks were observed in the direction of sliding. When 0.1 A current was applied, the wear loss volume increased due to much more severe abrasive wear as manifested by much deeper wear marks. Under 0.5 A electrified conditions, wear loss volume increased tremendously. Along with the abrasive wear, a layer, presumed to have generated as a thick layer but partially detached during the sliding contact was observed by 3D profile. Thicker oxide layers generated on the contact interfaces turned into abrasive wear debris, which caused severe third-body wear and a high wear loss volume at 0.5 A. In contrast to 0.5 A electrified condition, under 1 and 3 A electrified conditions, significant reductions in wear loss volumes were observed as shown in Figure 3.
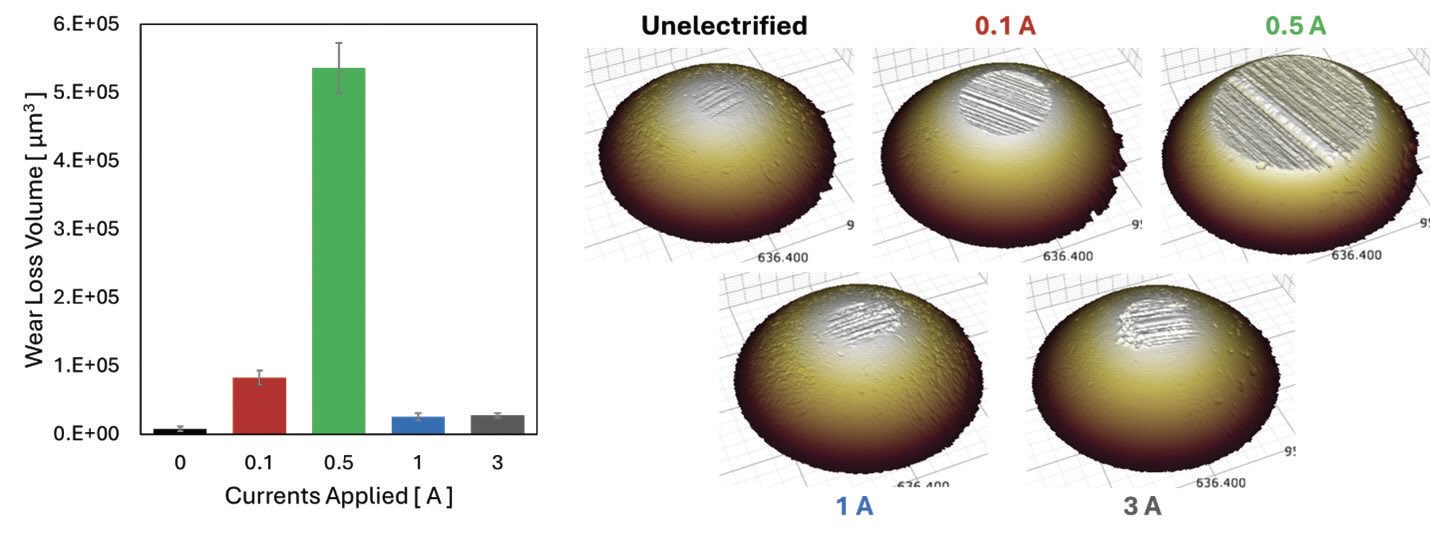
Figure 3. Comparison of average wear loss volumes (left) and 3D profile of the balls (right) at different electrified conditions.
The wear loss volume trend at different electrical current flowing conditions observed in the experiment was not a unique nature of LOUP but showed the same trends over the conventional lubricants. Figure 4 shows the comparison of wear loss volume at different electrified conditions using Mineral Group III, PAO 5, and LOUP. All base oils tested under 0.5 A electrified conditions showed severe wear loss volume while significant reductions were observed when current intensity increased to 1 A.
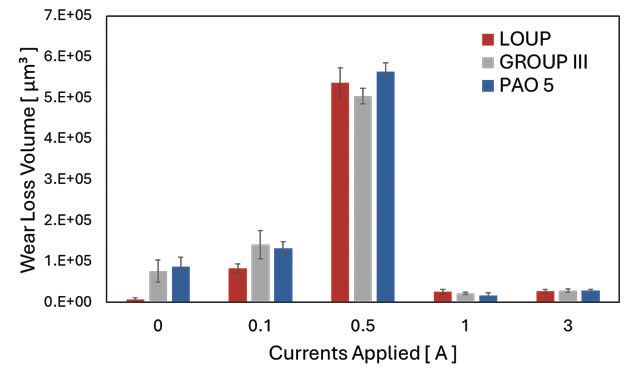
Figure 4. Comparison of wear loss volumes using different base oils under various electrified conditions.
3.2 Surface Analysis
Scanning Electron Microscopy and Raman Spectroscopy were conducted on rubbing surfaces to investigate unique characteristics under different electrified conditions. Figure 5 shows the EDS mapping of the tested balls at different electrified conditions, which were taken in the same magnification with accelerating voltage 5.0 kV and 60nA probe current. As shown in Figure 5, mild oxidative components were observed on the contact surfaces where carbon-related components were the most dominant on the debris under unelectrified conditions, indicating that a carbon-tribofilm and thin protective oxide layer were formed during the tribo-test. It was further confirmed by the Raman spectrum (see Figure 6) that the strong peaks at 223, 293, 410, 655, and 1315 cm-1, which corresponds to the hematite (α-Fe2O3), were found on the oxide layer on the contact surface under unelectrified conditions. Under 0.1 A electrified condition, on the other hand, rich-oxide layers were formed and fully covered on the contact surface, as shown in the SEM-EDS. In addition, thick blue layers on the top of the contact interfaces were found in microscopic images, as shown in Figure 6. Raman spectrum revealed that the layer showed the highest Raman peak of 302, 536, and 670 cm-1, corresponding to the magnetite (Fe3O4). This indicates that a thick oxide tribolayer consisting of magnetite was formed and accumulated on the contact interfaces under 0.1 A electrified condition. Similar oxidative layers were also found when 0.5 A current was applied, as shown in Figure 6. However, unlike 0.1 A electrified condition where thick oxidative layers consisting of magnetite were distributed throughout the contact interface as shown in SEM-EDS and Raman, a relatively smaller portion of those was presented under 0.5 A electrified condition. Another portion of the contact interfaces was found to be 52100 alloy steel, and there were no distinguishable Raman peaks for the bare surface of 52100. Based on the surface analysis using SEM and Raman spectroscopy, both under 0.1 and 0.5 A electrified conditions presented thick oxidative layers, which promoted more severe wear. Once the accumulated thick oxidative layers break down from the contact surfaces due to their brittleness and poor adhesion, broken particles may act as abrasive debris particles, aggravating the abrasive wear and third-body wear processes. Subsequently, these processes will repeat starting with the severe oxidative wear on the metal surface, accelerating the overall wear properties as sliding time increases. Both under 1 and 3 A electrified conditions, fewer oxidative components were found on the contact surfaces, and iron-related components were identified more through the SEM-EDS. Instead, most of the oxide related components were found on the debris. Furthermore, Raman spectrum showed that the contact surface evenly showed hematite and 52100 Raman peaks with a small portion of magnetite. The transition of the wear mechanism from 0.5 A to 1 A electrified conditions (severe wear to mild wear) can be attributed to the increased joules heating and tribo-electrical and -chemical reaction, which may need further investigation.
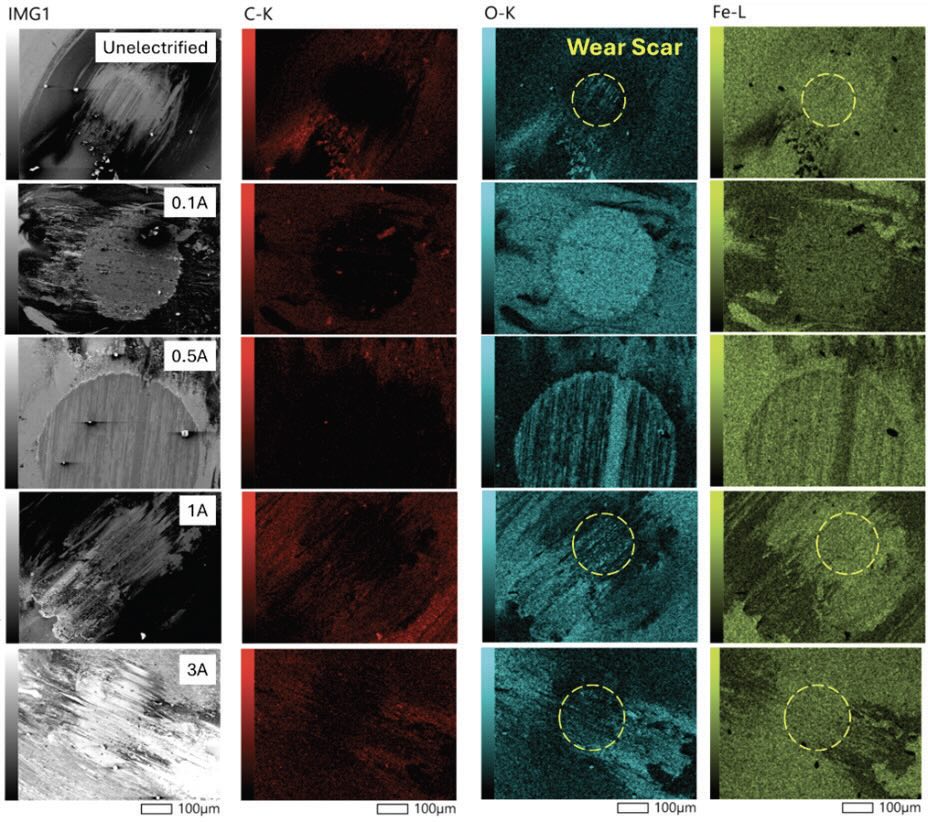
Figure 5. SEM-EDS Mapping of LOUP at different electrified conditions.
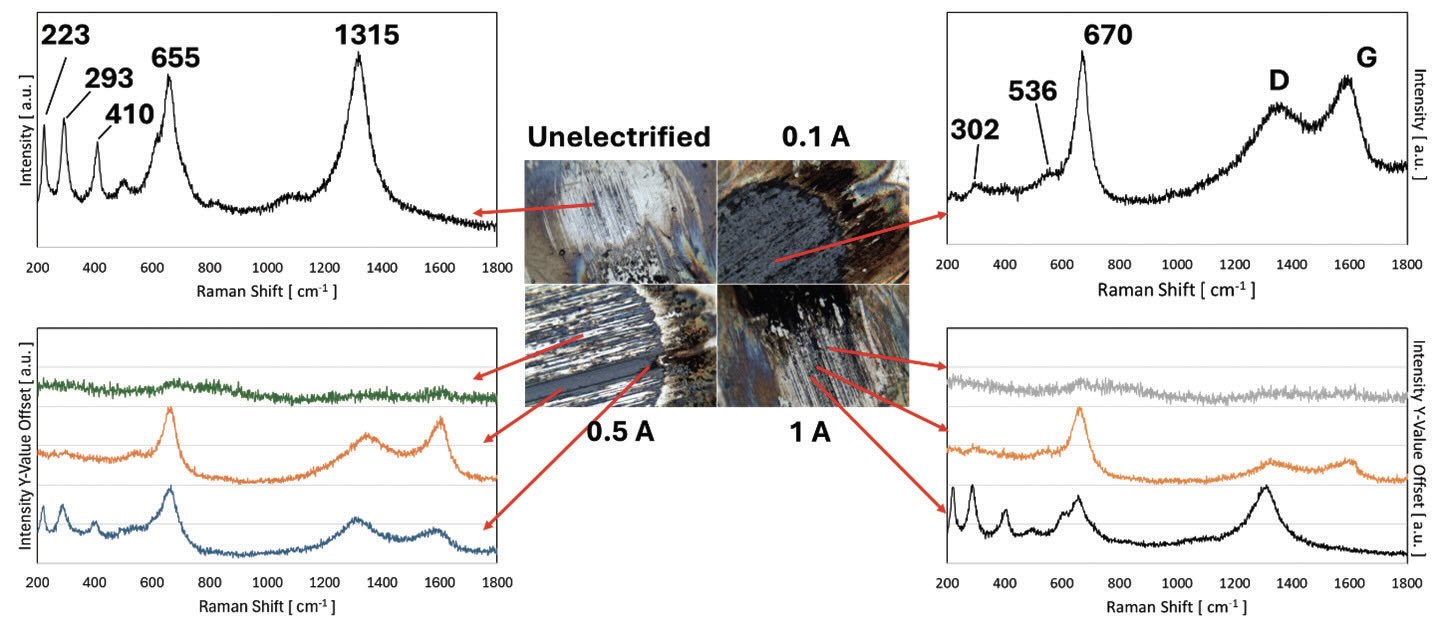
Figure 6. Raman spectrums at different electrified conditions.
3.4 Enhancement of Wear Properties by a Protic Ionic Liquid (PIL) Additive
In recent years, Ionic Liquids have been recognized as a promising lubricant for friction and wear reductions due to their physical, chemical, and rheological properties for extreme tribological conditions.[14] Among them, studies on PILs have recently been attracting attention due to their high electrical conductivity, reduced oxidation, and excellent thermal stabilities.[15, 16] In addition, unlike the Aprotic Ionic Liquids (APILs) with fluorine- or chorine-containing anions, which produce corrosive and toxic acids when exposed to water molecules or moisture[17], PILs are more environmentally friendly, making them promising additives or lubricants by themselves. Here, 2-hydroxyethylammonium 2-ethylhexanoate PIL synthesized at Rochester Institute of Technology [18, 19] was added to LOUP as an additive to investigate the performance enhancement under electrified conditions. 1 wt.% of PIL was added into LOUP and blended using magnetic stirrer and ultrasonicating bath at the temperature of 60°C for 2 hours. Tribo-tests under electrified conditions using LOUP with PIL were conducted in the same experimental parameters as mentioned above, and tribological properties were compared with those of using pure LOUP.
Preliminary results showed improved tribological properties when PIL was added into LOUP. COF values at different electrified conditions using LOUP with PIL showed no significant reduction in COF compared to pure LOUP. However, as shown in Figure 7, where 0.5 A electrical current was applied, COF of PIL-added LOUP showed more stable frictional traces, whereas sharp frictional peaks or spikes had been observed during the test using pure LOUP. Furthermore, a marked reduction in wear loss volume was observed. Under 0.5 A electrified conditions, wear loss volume reduction using LOUP with PIL compared to that of using pure LOUP was 26%. All other conditions except for 0.1 A electrified condition showed wear loss reductions ranging from 16 to 27% when PIL was added to LOUP. Further investigation into the effect of adding PIL will be necessary to identify the specific wear mechanism involved in each of these cases and is currently underway in our laboratory.
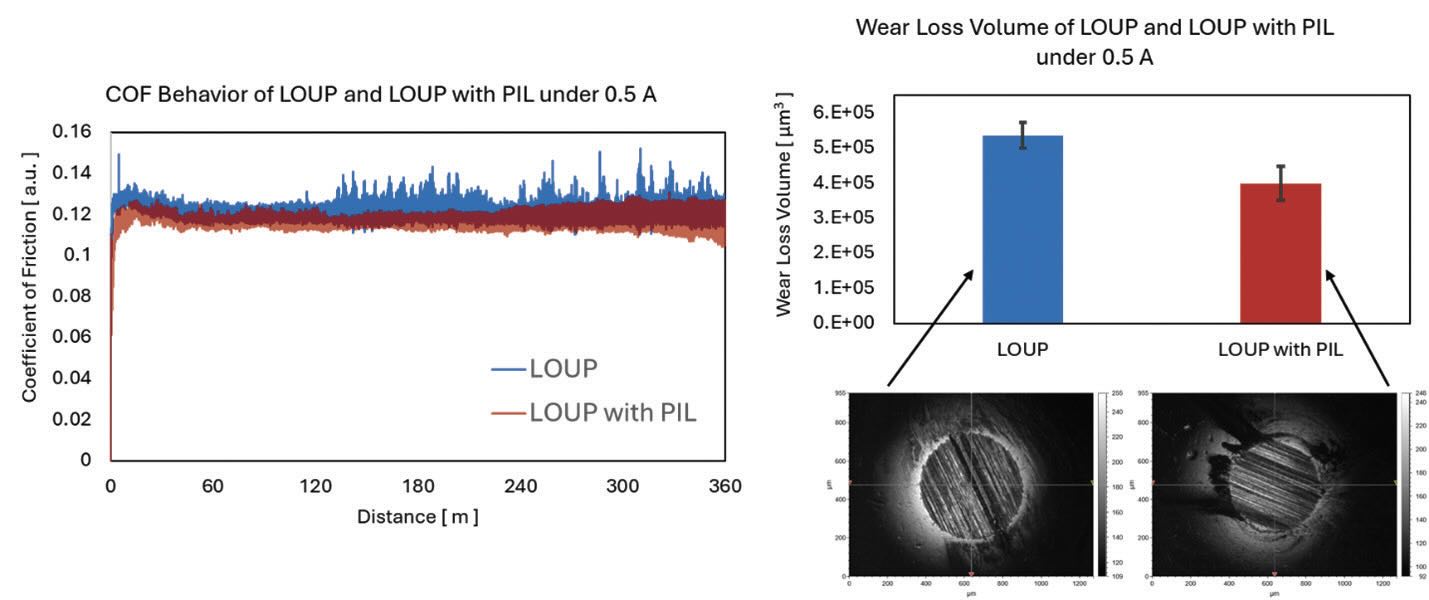
Figure 7. Comparison of frictional behaviors (left) and wear loss volumes (right) using LOUP and LOUP with PIL under 0.5 A electrified conditions.
4. Conclusion
This study explored the tribological properties under different electrified conditions when using LOUP as a lubricant. The outcome of this research will benefit various moving mechanical assemblies, including the driveline components of electric vehicles and several other demanding tribological applications. The following are the final conclusions of my study:
1. Under electrified sliding conditions, different types of oxide layers were generated under the influence of electrical currents, and they had a strong effect on wear transitions and associated mechanisms. At relatively lower current levels (0.1 and 0.5 A), thick oxide layers were generated and accumulated at the contact interface. At higher current levels (1 and 3 A), on the other hand, thick oxide layers were not found, perhaps due to rapid removal from the contact interface, thus, resulting in less third-body wear.
2. Tribological properties of LOUP under electrified conditions showed comparable results to the conventional base oils.
3. By adding a PIL into LOUP, the tribological performance was improved compared to using pure LOUP alone. High thermal and electrical stability of PIL may have reduced the intensity of tribo-oxidation which resulted in more stable frictional behaviors and reduced wear loss.
Acknowledgement
The author would like to thank STLE for the support provided by the 2024 Elmer E. Klaus Fellowship. This work was funded by the U.S. Department of Energy’s Office of Energy Efficiency and Renewable Energy (EERE) under the Advanced Manufacturing Projects for Emerging Research Exploration award number DE-EE009300. Research at Argonne National Laboratory was performed under Contact No DE-AC02-06CH11357. The author would like to express sincere thanks to Dr. Ali Erdemir for his exceptional guidance and support throughout the project. The authors also convey special thanks to those people from Iowa State University (Chao Meng, Yolanda Wang, Wenyu Huang, and Aaron D Sadow), Argonne National Laboratory (Magali S. Ferrandon and Massimiliano Delferro), Rochester Institute of Technology (Patricia Iglesias Victoria), and Tecnologico de Monterrey (Leonardo Israel Farfan Cabrera).
References
1. Vethaak, A.D. and H.A. Leslie, Plastic Debris Is a Human Health Issue. Environmental Science & Technology, 2016. 50 (13): p. 6825-6826.
2. Courtene-Jones, W., N.J. Clark, and R.C. Thompson, Plastic pollution: the science we need for the planet we want. Emerging Topics in Life Sciences, 2022. 6 (4): p. 333-337.
3. Massa, G.M. and V.M. Archodoulaki, An Imported Environmental Crisis: Plastic Mismanagement in Africa. Sustainability, 2024. 16 (2).
4. Ragaert, K., L. Delva, and K. Van Geem, Mechanical and chemical recycling of solid plastic waste. Waste Management, 2017. 69: p. 24-58.
5. Alam, S.S., A.H. Khan, and N.A. Khan, Plastic waste management via thermochemical conversion of plastics into fuel: a review. Energy Sources Part a-Recovery Utilization and Environmental Effects, 2022. 44 (3): p. 1-20.
6. Ray, R. and R.B. Thorpe, A comparison of gasification with pyrolysis for the recycling of plastic containing wastes. International Journal of Chemical Reactor Engineering, 2007. 5.
7. Pal, S., et al., Recent Advances in Catalytic Pyrolysis of Municipal Plastic Waste for the Production of Hydrocarbon Fuels. Processes, 2022. 10 (8).
8. Fivga, A. and I. Dimitriou, Pyrolysis of plastic waste for production of heavy fuel substitute: A techno-economic assessment. Energy, 2018. 149: p. 865-874.
9. Farfan-Cabrera, L.I., Tribology of electric vehicles: A review of critical components, current state and future improvement trends. Tribology International, 2019. 138: p. 473-486.
10. Ahmed, N.S. and A.M. Nassar, Lubricating Oil Additives. Tribology - Lubricants and Lubrication, 2011: p. 249-268.
11. Tokoro, T., M. Nagao, and M. Kosaki, High-field dielectric property of polypropylene with superposition of ac and dc field. Ieee 1995 Annual Report - Conference on Electrical Insulation and Dielectric Phenomena, 1995: p. 316-319.
12. Hackler, R.A., et al., Synthetic Lubricants Derived from Plastic Waste and their Tribological Performance. Chemsuschem, 2021. 14 (19): p. 4181-4189.
13. Wang, Y.Y., et al., Catalytic Hydrogenolysis of Polyethylene Under Reactive Separation. Acs Catalysis, 2024. 14 (3): p. 2084-2094.
14. Grace, J., et al., Ionic Liquids as Additives of Coffee Bean Oil in Steel-Steel Contacts. Lubricants, 2015. 3 (4): p. 637-649.
15. Sierra, A., M.G. Coleman, and P. Iglesias, Tribological Properties of Borate-Based Protic Ionic Liquids as Neat Lubricants and Biolubricant Additives for Steel-Steel Contact. Lubricants, 2022. 10 (10).
16. Guo, H., et al., Linear alkyl-benzenesulfonate-based protic ionic liquids: Physicochemical properties and tribological performance as lubricant additives to a non-polar base oil. Journal of Molecular Liquids, 2022. 361.
17. Al Kaisy, G.M.J., et al., Tribological performance of low viscosity halogen-free ammonium based protic ionic liquids with carboxylate anions as neat lubricants. Tribology International, 2021. 160.
18. Guo, H., A.R. Adukure, and P. Iglesias, Effect of Ionicity of Three Protic Ionic Liquids as Neat Lubricants and Lubricant Additives to a Biolubricant. Coatings, 2019. 9 (11).
19. Guo, H., et al., Influence of Hydrogen Bonding and Ionicity of Protic Ionic Liquids on Lubricating Steel-Steel and Steel-Aluminum Contacts: Potential Ecofriendly Lubricants and Additives. Tribology Letters, 2020. 68 (4).