KEY CONCEPTS
•
There is no shortage of methods for quantifying sustainability—both in general and as they apply to tribological processes. However, there is currently no scientific agreement as to what constitutes a sustainable lubricant.
•
Some of these methods are guidelines and others are regulations that either are enforced or have the potential to be enforced.
•
In terms of tribology, reduction of friction and wear (and energy loss) is key to achieving sustainability, and this can be quantified in several ways.
In order to avoid having the term “sustainability” devolve into a buzzword, credible (and enforceable) means of quantification are essential. They must involve measuring and assessing all the environmental, societal and economic impacts of processes to ensure they meet or exceed sustainable development goals. Several of these quantification protocols are in place today.
STLE member Dr. Peter Lee, institute engineer and chief tribologist, Southwest Research Institute, says, “In its broadest sense, sustainability is the ability to support or maintain a process over time. To be complete it needs to consider economic, environmental and social aspects with the goal of creating a sustainable path forward for both the planet and humankind.”
Quantifying sustainability in general
STLE member Dr. Hannes Grillenberger, product manager engineering tools, Schaeffler Technologies, advises starting with the United Nation’s (UN’s) 17 UN Sustainability Development Goals (SDGs). “Each of the defined 17 dimensions includes something to be quantified,” he says. “However, the concerns are how to quantify these goals, the order importance and how to use resources efficiently
(see 17 UN Sustainability Development Goals [SDGs]).”
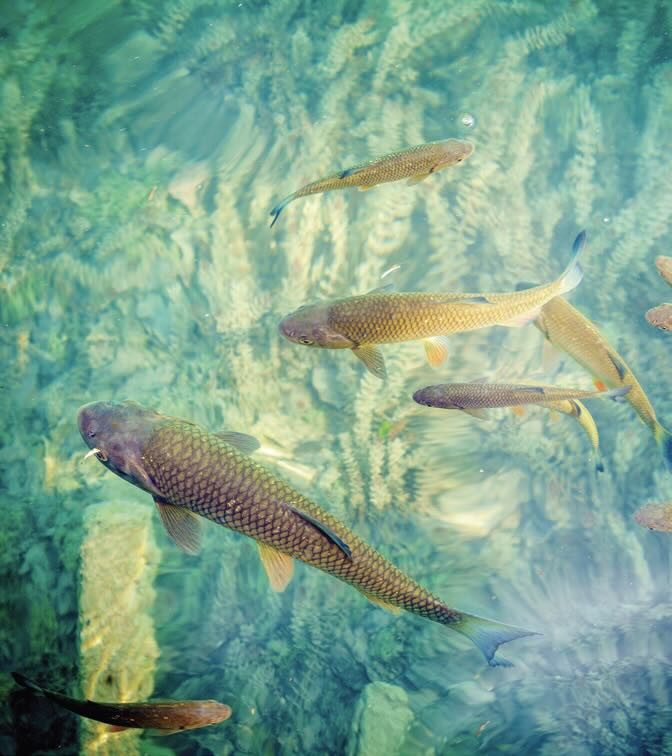
17 UN Sustainability Development Goals (SDGs)A
Established as part of the 2030 Agenda for Sustainable Development, the 17 UN Sustainability Development Goals (also referred to as “dimensions of sustainability”) are as follows:
1.
No Poverty
2.
Zero Hunger
3.
Good Health and Well-being
4.
Quality Education
5.
Gender Equality
6.
Clean Water and Sanitation
7.
Affordable and Clean Energy
8.
Decent Work and Economic Growth
9.
Industry, Innovation and Infrastructure
10.
Reduced Inequalities
11.
Sustainable Cities and Communities
12.
Responsible Consumption and Production
13.
Climate Action
14.
Life Below Water
15.
Life on Land
16.
Peace, Justice and Strong Institutions
17.
Partnerships for the Goals
A.
From
https://sdgs.un.org/goals.
Quantification parameters, he suggests, are landfill volume, deforestation, CO
2 emissions, usage of fresh water, etc. “In my opinion, the only correct way to measure, however, is also the hardest: cradle-to-grave since it takes the complete life cycle and value chain into account,” he adds
(see Five Product Life Cycle Stages).
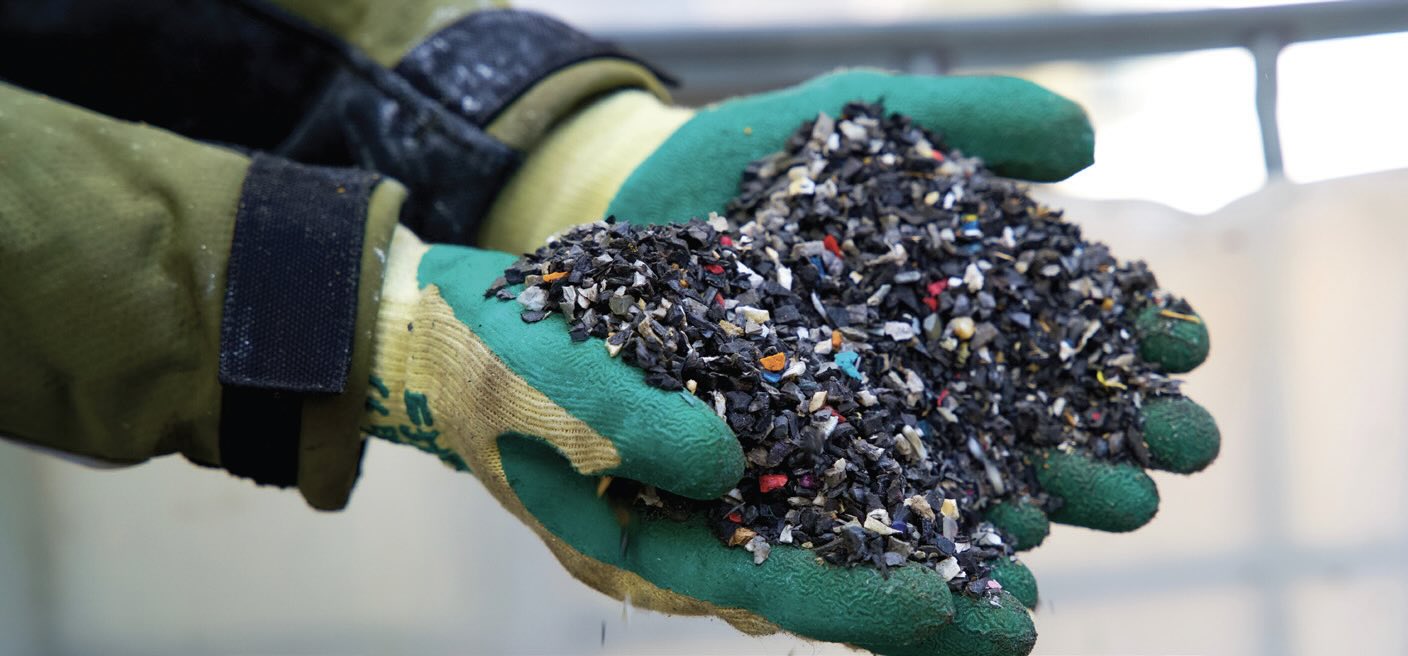
Five product life cycle stagesB
The following five life cycle stages of a product are used to define and evaluate the environmental impact of a product or service from creation to disposal.
1.
Raw Material Extraction (Resource Acquisition)
2.
Manufacturing and Production
3.
Distribution and Transportation
4.
Use and Operation
5.
End-of-Life (Disposal or Recycling)
B.
From
https://ecochain.com/blog/life-cycle-assessment-lca-guide/.
When it comes to lubricants, STLE Fellow Mathias Woydt, managing partner, MATRILUB Materials, Tribology, Lubrication, points out that a major barrier to quantification is that there is currently no scientifically accepted agreement on what constitutes a sustainable lubricant. His suggestions include:
1.
Sustainability throughout the chain by sourcing renewable raw materials and circular business models.
2.
Low carbon intensity or carbon neutral lubricants (base oils and additives), some of which may even have a negative footprint.
3.
In-use benefits of low-friction lubricants and longevity, avoiding carbon emissions in the use phase.
The product carbon footprint (PCF) is an estimation of the embedded CO
2 footprint throughout the upstream process
(see Upstream, Downstream). Base oils derived from recycled plastics or re-refining cut the PCF. In addition, tribological products and lubricants can have unique properties that allow them to offer great carbon savings downstream.
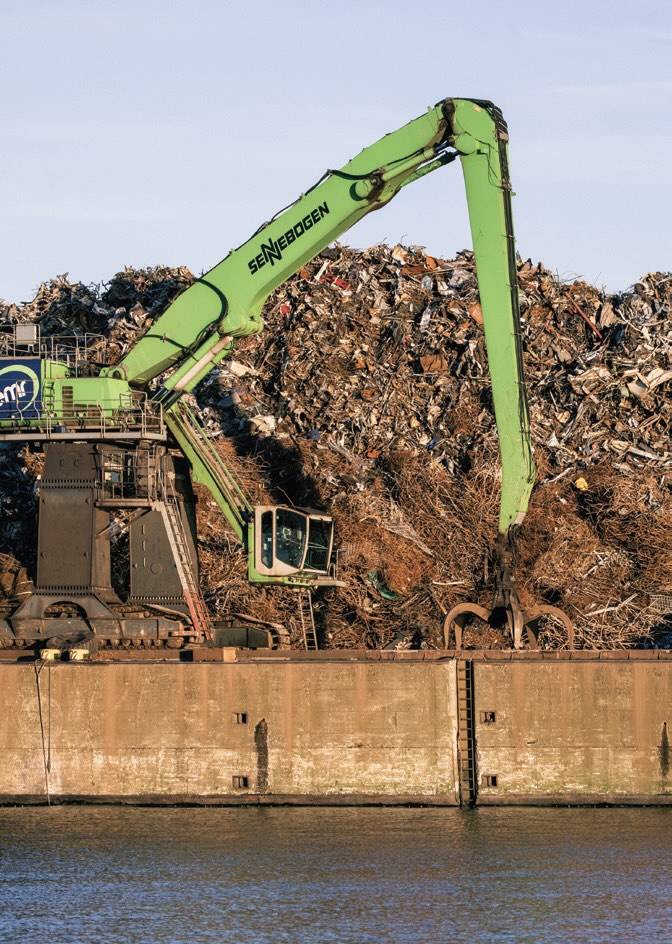
Upstream, downstream
•
Upstream refers to the activities involved in sourcing raw materials and producing a product, including resource extraction, manufacturing and transportation—essentially the supply chain leading up to the end product.
•
Downstream refers to the activities that occur after production, such as product usage, disposal and recycling. It includes the entire life cycle of a product from its origin to its end of life. It’s focused on the impact after the product is sold to the consumer.
“The most striking consequence is that the use phase clearly dominates the PCF,” Woydt explains. “Reduction in friction and extension of longevity in the use phase can more than compensate for the monetary investment in low-friction designs and high-performance lubricants.” The use phase is the period of a product’s life cycle when it is being put into service by end-users.
He adds, “The big issue of claiming ‘avoided emissions’ is that it’s seen by politicians and agencies as being unverifiable and includes issues such as double counting, the choice of a baseline, cherry-picking system boundaries and methodological approaches that are inaccurate. That´s likely why politicians and international organizations refrain from accepting ‘avoided emissions’ as a measurement of sustainability.”
1
The methodology to quantify efficiency gains by switching to an energy-efficient or highly shear-resistant multigrade hydraulic fluid was assessed at an average of 10% and can be determined with ASTM D7721-22. ASTM D7721-22 provides guidelines for assessing how specific hydraulic fluids affect the efficiency of hydraulic systems and their components. It is applicable to all types and grades of hydraulic fluids for laboratory and field evaluations. It does not prescribe a specific efficiency test methodology.
STLE Fellow Dr. Vasilios Bakolas, Schaeffler Technologies AG & Co. KG, observes that there is currently a well-established basis for quantifying sustainability. He cites ISO standards and the Greenhouse Gas (GHG) Protocol that both provide ways to quantify the sustainability of a product, organization or company.
“The Global Warming Potential (GWP), expressed in kg CO
2e (carbon dioxide equivalent), is currently the most attention-grabbing metric,” he says, adding that tools are available that allow for the calculation of the CO
2 emissions of products and other environmental indicators such as acidification and eutrophication. Eutrophication is the process during which a body of water becomes overly enriched with nutrients, leading to excessive plant life. “The major challenge in quantifying sustainability lies not in the general methods, guidelines or tools, but rather in the data required to perform the calculations,” he advises.
“Everything can be quantified using a metric such as: CO
2 emissions, tons of landfill, percentage loss or acreage of rain forest, percentage of people in poverty, earth temperature rise, etc.,” Lee says. “The correct combination of metrics can be assembled to quantify sustainability in terms of what is to be measured.”
Quantifying the contribution of tribology to sustainability
Regarding tribology, reduction of friction and wear (and energy loss) is key to achieving sustainability. This energy saving can be quantified—for example, by improved fuel economy or reduced electricity consumption by battery electric vehicles. “Tribology can also be used to ensure fuels developed from sustainable sources can operate correctly in equipment without causing increased wear, thereby reducing carbon emissions,” Lee says. “The extraction and processing of resources inevitably generates CO
2, and if equipment can operate twice as long, that reduces CO
2 emissions for those processes by half.”
Lee adds, “By understanding and influencing tribological mechanisms, tribology may contribute to sustainability by developing and optimizing all interactions of the surfaces with new products, coatings or lubricants. This would lead to better compatibility, lower friction and thus energy savings, and less wear.”
Woydt points out that friction and wear occur all along the value chain. “Friction is the worst enemy of efficiency—the ability of a machine or a system to maximize output with a minimal expense of energy. On a societal level, the German Society for Tribology (GfT e.V.) estimates the long-term mitigation potentials by:
1.
Friction reduction (= energy efficiency) between 2.0-8.1 gigatons of CO
2e/yr.
2.
Longevity (= resource efficiency and resource conservation) between >1.7->2.6 (>4,6) gigatons of CO
2e./yr in relation to fossil (anthropogenic) CO
2 emissions in 2019 of 33.6 gigatons of CO
2 or 59.1±5.9 gigatons of CO
2e
Low carbon tribology achieved through reducing friction and longevity depends on the value of saved energy and/or CO
2 allowances with respect to the investment. These are monetized as savings either in CO
2 allowances or simply as costs for energy or physical resources.
“The avoided emissions (total CO
2 or total CO
2e) of goods and services represent a monetary value,” Woydt explains. “Low rolling resistance tires, low viscosity and high viscosity index engine and gear oils, low-friction sliding seals and ball bearings all save energy and reduce CO
2e emissions.”
Sustainability in terms of bearings
Bearings are designed to reduce friction and thus contribute positively to sustainability. Although the emissions during their production and the energy loss during their use are small when considering a single bearing, the large number of installed bearings worldwide makes bearings significant in terms of sustainability. “Any improvement in the production of bearings, for example, by using green steel, or in their energy efficiency would have a significant impact on global emissions,” Bakolas says.
He clarifies that the calculation of the cradle-to-gate emissions of bearings is well defined in the Product Category Rules (PCR) for bearings published in 2023. Cradle-to-gate is the total GHG emissions from the extraction of raw materials to when a product leaves the factory. All relevant rules regarding cut-off, allocation, etc., can be found in this PCR document. “This ensures not only the calculation of cradle-to-gate emissions but also makes sure that the results from different manufacturers are comparable,” Bakolas says. “Estimating the gate-to-grave emissions is much more challenging. The wide range of applications for bearings makes it practically impossible to determine the use phase emissions accurately. Only for specific applications, where the operating conditions are known, can the use phase emissions be estimated. To estimate the global use phase emissions of bearings, it would be necessary to simplify assumptions. To date, no widely accepted assumptions exist.” Gate-to-grave considers a product’s environmental impact from the beginning of its life cycle to the end.
Bakolas reiterates that a key element in estimating the sustainability of bearings is the existence of the PCR. “The bearing industry has made significant progress in defining a set of rules to quantify the sustainability contribution of bearings,” he says. “This PCR should be reviewed and updated regularly to ensure it meets the requirements of bearing customers.”
Sustainability in terms of the chemical industry
As a key supplier of raw materials for lubricants, the chemical industry is challenged in regard to saving energy and reducing emissions by the high degree of energy required to produce base stocks and additives on a commercial scale. Lee explains, “The chemical industry is quantifying sustainability by focusing on reducing Scope 1, Scope 2 and Scope 3 emissions, and saving energy. The aim is to reduce pollution and save energy using environmentally driven approaches.”
Scope 1 emissions originate directly from company-owned sources such as vehicles and machinery. Scope 2 emissions are attributed to purchased energy, such as electricity used in company facilities, which is generated by a third-party power plant. Scope 3 emissions encompass all other indirect emissions throughout the company’s value chain, including raw material production, transportation, waste disposal and consumer usage.
He continues, “Major chemical companies are determining how to lower the energy intensity of their processes to reduce Scope 1 emissions. This requires consideration from the design stage to select less energy-intensive processes as well as improving those processes. Energy losses originate from heat transfer and exchange during manufacturing. Minimizing carbon, varnish and residue in oil circuits and limescale in water-cooling systems can help make these processes more efficient. A movement toward cost-competitive renewable energy sources (solar and wind power) is underway in an effort to reduce Scope 2 emissions. Through careful selection of environmentally friendly raw materials, increased attention to minimizing waste disposal through recycling and working with customers, the chemical industry is decreasing Scope 3 emissions, which has the added benefit of reducing the PCF of lubricant suppliers.”
Grillenberger concurs, “Processes in the chemical industry often are energy intensive, may use a lot of fresh water and some of them—especially in the lubricant industry—rely on mineral oil. In all these fields of operation, quantifying according to the UN definition in a cradle-to-grave scenario would be the most ethical way to go. However, this can be a big challenge, since the usage of products and extent of recycling is unclear. The in-plant processes may be the best starting point.”
Issues with existing methods
Although a number of methods exist for quantifying sustainability, none are perfect. Per Bakolas, they tend to focus on the upstream—supply chain and production—cycle of a product. “While this may be adequate for many consumer products, such as clothes, it totally misses the point when we are talking about engineering products and their components,” he says. “For the latter, the majority of the emissions produced during their life cycle comes from their use, which are captured by the downstream emissions. For most engineering products, the ratio between upstream and downstream emissions is 1:80 and above,” he says.
“In order for sustainability to be measured correctly and fully, the resources required to bring an item into existence, transport it to its end use, its use and its end-of-life effects all need to be considered, cradle-to-grave, not just part of this cycle,” Lee advises. “If any part of the full cycle is missed it does not give a true metric and does not allow complete comparison between products.”
Woydt warns that climate-related disclosures used in ads are voluntary claims and can devolve into the very definition of greenwashing per the U.S. Federal Trade Commission’s (FTC) Green Guide
2 or future European Directive on Greenwashing.
3
“Both climate-related disclosures and green claims in advertisements need data,” he says. “The key questions are who has the power of authority to develop such certification schemes and where does reliable, comprehensive and consistent data come from. As per the FTC, the answer is clear. FTC accepts ‘voluntary consensus standards’ or ‘technical standards’ developed or adopted by voluntary consensus standards bodies, both domestic and international.”
4
The Green Guide defines a voluntary consensus standards body as having the following attributes:
•
Openness
•
Balance of interest
•
Due process
•
An appeals process
•
Consensus, which is defined as general agreement, but not necessarily unanimity
5
Woydt notes that ASTM D7721-22 “Practice for Determining the Effect of Fluid Selection on Hydraulic System or Component Efficiency” is such an example. “This practice from a voluntary consensus standardization body defines minimum technical requirements for conducting energy efficiency performance comparisons of two or more hydraulic fluids in controlled laboratory or field evaluations,” he explains. “The savings in energy consumption in kW-hr/year can be converted into saved CO
2e emissions by using the local emissions factor of electricity or the Environmental Protection Agency’s (EPA’s) online calculator.”
“Getting the correct data is a big thing,” Grillenberger says, “and not claiming something you could be liable for. This forces you to be transparent and open regarding what you do.”
Bakolas believes that the main argument for not calculating the downstream emissions is that the multitude of applications—where these products are being used—doesn’t allow for sensible assumptions to be made for the calculation of their emissions. “This argument only holds if someone would wish to calculate exactly the emissions of the use phase of all the engineering products,” he says. “The main question, though, is what we want to achieve with these calculations. If we wish to establish a benchmark, to record engineering progress and thus the reduction of use phase emissions over time, the only thing needed is an agreed upon set of operating conditions for every product family. When we are able to estimate the use phase emissions in any way, we can finally shift our focus toward where it counts: the increase of the energy efficiency of products and the subsequent reduction of their emissions.”
Preferred methodologies
Which sustainability quantification method is best depends on the application and also on the jurisdiction of any regulatory bodies. Woydt observes that different schema or frameworks for GHG reporting are on the table, such as the Global Reporting Initiative (GRI), International Financial Reporting Standards/International Sustainability Standards Board (IFRS/ISSB), Carbon Disclosure Project (CDP) and Task Force on Climate-Related Financial Disclosures (TCFD).
Woydt says that the release of “The Enhancement and Standardization of Climate-Related Disclosures for Investors,” March 2024, by U.S. Securities and Exchange Commission (U.S. SEC) seems to be the safe harbor for regulatory compliance.
6 Other quantification frameworks he cites include:
•
International Financial Reporting Standards (IFRS)
•
Partnership for Carbon Accounting Financials (PCAF)
•
Oil and Gas Methane Partnership 2.0 (OGMP 2.0)
“To me, the attitude, a real commitment and honesty are more important than the methodology itself,” Grillenberger concludes. “Working, producing and living in a sustainable way should be the goal of every society, company and individual in order to ensure a meaningful life for future generations.”
REFERENCES
1.
Avoided emissions, proposed as Scope 4, are described in:
a.
ISO TR 14069-2013, section 3.1.5 “avoided emissions”
b.
U.S. CFR, title 10–Energy, Chapter II, subchapter B, § 300.2 “Definitions”
c.
GHG Protocol, Product Life Cycle Accounting and Reporting Standard, September 2011, Definition for “avoided emissions,” chapter 11.3.2 “Offsets and avoided emissions”
2.
October 2012, under review.
3.
COM (2022) 143 final.
4.
See U.S. FTC circular no. A-119, revised, February 10, 1998, and in “Federal Participation in the Development and Use of Voluntary Consensus Standards and in Conformity Assessment Activities,”
Federal Register, 77 (62), Friday, March 30, 2012, pp. 19357-19360.
5.
Guides for the Use of Environmental Marketing Claims, 16 CFR Part 260, 77 (197), Thursday, October 11, 2012, section III “Certifications and Seals of Approval,” footnote 15, pp. 62122-62132.
6.
U.S. SEC, The Enhancement and Standardization of Climate-Related Disclosures for Investors, final rule,
Federal Register, 89 (61), Thursday, March 28, 2024, pp. 21668-21921,
www.govinfo.gov/content/pkg/FR-2024-03-28/pdf/2024-05137.pdf.