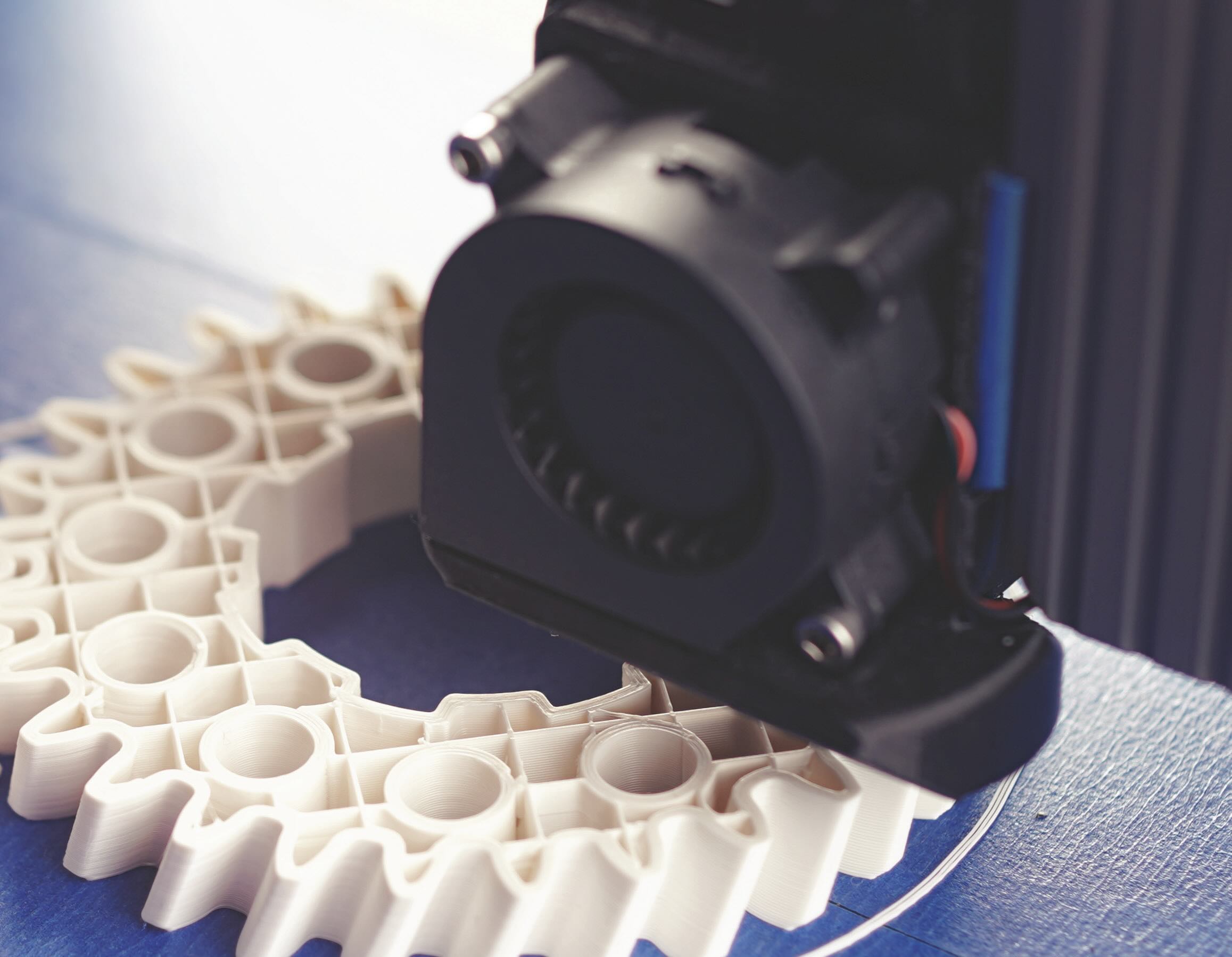
Meet the Presenter
This article is based on a webinar presented by STLE Education on Oct. 11, 2023. Additive Manufacturing Technologies is available at www.stle.org: $39 for STLE members, $59 for all others.
Dave Follette is the director of the Advanced Digital Design and Fabrication Lab (ADDFab) at the University of Massachusetts Amherst, Massachusetts (UMass). Prior to coming to UMass, Follette worked for Carbon 3D in California developing a new kind of 3D printing for manufacturing with high performance polymers using an ultraviolet (UV) curable resin. He has worked in 3D printing for eight years, although the process has been around much longer. He also has experience as a mechanical engineer, designing hybrid transit buses, concentrated solar PV systems, robotics, automation, truck aerodynamics and 3D printers. Follette holds an undergraduate degree in mechanical engineering from Princeton University, a master’s degree in mechanical engineering from Massachusetts Institute of Technology (MIT) and a master of business administration (MBA) from MIT’s Sloan School of Management. You can reach him at follette@umass.edu.
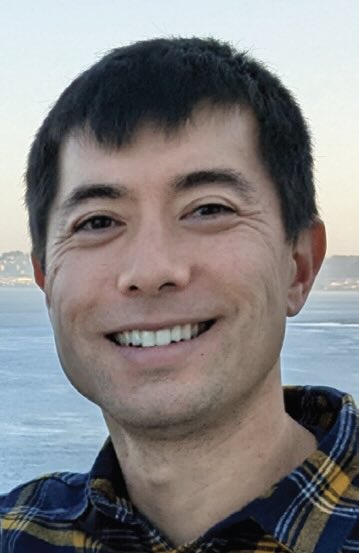
Dave Follette
KEY CONCEPTS
•
Additive manufacturing can be a fast, convenient and cost-effective way to create designs that may be impossible to manufacture using subtractive methods.
•
The field of additive manufacturing is growing rapidly, and the current methods each have their own strengths and weaknesses.
•
Some limitations to additive manufacturing can include cost, part density, surface finish, warping and process speed, depending on the specific part.
Additive manufacturing (AM), also known as 3D printing, begins with powder, filament or liquids that are solidified to build up into a part. While people are most familiar with 3D printing using plastics, it is possible to also create metal parts this way. In contrast with subtractive manufacturing where material is removed from a primitive shape to create a part, additive manufacturing has the potential to create lighter and more refined parts. Depending on the process used and the end product needs, additive manufacturing can be faster and cheaper than subtractive methods.
This article is based on an STLE webinar presented by Dave Follette, director of the Advanced Digital Design and Fabrication Lab (ADDFab) at the University of Massachusetts Amherst in Amherst, Mass., titled Additive Manufacturing Technologies. See Meet the Presenter for more information.
Research on expanding additive manufacturing applications and methods is continuing, but existing 3D printing processes already show great potential to make parts that are lighter, smaller, more refined and less expensive than traditional manufacturing methods.
Additive versus subtractive
Most people don’t use the word subtractive, but it means any cutting, drilling, grinding or any process where material is removed or subtracted. Typically the process begins with a block or other primitive shape (e.g., cylinder, sphere, cube, rectangular prism) and material is cut out of the shape to end up with the needed part. The more material that is removed, the more the process costs.
In contrast, with additive manufacturing, the process builds up into a part from powder, filament or liquids. In an additive process, the more material that is added, the more the process costs. This incentivizes the process to use as little material as possible to make something lighter and smaller. Typically using less material and making lighter parts is a design advantage. Additive manufacturing can be a fast and convenient way to make parts, but the real benefits are that it opens new areas for design and for manufacturing while also saving money. Geometries that were previously
impossible to manufacture can be printed.
Additive advantages
The additive process saves money as well. Before additive manufacturing, a fuel injector nozzle for a jet engine was manufactured from 20 different parts that were sourced from different manufacturers. The different parts had to be inventoried and assembled, which required a lot of work. In contrast, additive manufacturing allows this part to be printed in one piece, which is then refined through several post-processing steps. In the end, the additive manufacturing process saves the company about 20% by weight and 20% in cost, which are great wins for them. Patent drawings available to the public show how complicated the piece is on the inside and how difficult the piece might be to manufacture.
Another advantage of additive manufacturing is the impact of the tool and mold costs in traditional manufacturing. Injection molding requires a mold, which itself costs money to make. If the mold is only good for so many parts, each part carries on the mold cost. Making multiple parts at once requires storing them, keeping track of those parts, maintaining them in a storage facility, etc. In contrast, with a digital file in a cloud where the part is only printed as needed, both the mold and tracking system become unnecessary. Considerations include:
•
Is a warehouse full of inventory needed, or could the part instead only be printed when needed?
•
Is a prototype different from a final product?
•
If there is no difference between prototyping and production, can production start immediately?
In addition, as the tool is digital, the process is not locked into a particular design. Changes can be made easily to the digital design. In contrast, changes are much harder to make to a physical mold and physical part. Digital design also allows for changes to be made to customize a part. For example, many hearing aids are 3D printed because one person’s ear canal is not the same as anyone else’s ear canal. The same applies to dental liners, where the power of 3D printing was realized very early.
While many people think of the primary advantage of 3D printing as only of rapid prototyping, there are many other advantages, including low volume production and customized products where each part can be a unique design. Follette notes that creating complex geometries is where 3D printing gets interesting as there are no tooling costs and the limitations of traditional subtractive methods are removed.
How additive manufacturing works
Most 3D printing involves stacking up layers. For example, pieces of wood can be cut out and stacked up to create different shapes. The model is turned into 2D slices that are stacked up one by one. Note that the thinner the layers of wood, the smoother the end product becomes.
Follette shows a sample part printed in metal that was designed to be easy to print in 3D but would be challenging to create using a subtractive method or even a casting method
(see Figure 1). The original computer aided design (CAD) model of the part is shown on the left side of Figure 1, one slice of the model is shown in the middle and the final part is shown on the right side. Traditional manufacturing would be challenged to create this type of part.
Figure 1. Converting the 3D world into 2D slices and back to 3D. Figure courtesy of University of Massachusetts Amherst.
One concern often expressed with 3D printing is cost. However, Follette notes that as a part’s complexity increases, 3D printing becomes more affordable. Selective laser melting (SLM) costs become cheaper as the part becomes more complex. There are situations where a part made with additive manufacturing is less expensive to make than a similar subtractively processed part. Follette notes that there are definitely opportunities for additive manufacturing to be less expensive than traditional manufacturing.
Additive technologies
ASTM standards have taken the world of 3D printing and put it into 7 + 1 families
(see Table 1). The seven families explained in Table 1 are vat photopolymerization, powder bed fusion (PBF), binder jetting, material jetting, sheet lamination, material extrusion and directed energy deposition (DED). The +1 is a hybrid process, which combines additive and subtractive technologies in one machine, providing the best of both worlds. Follette notes that the field of additive manufacturing is growing every day.
Follette explains that the University of Massachusetts Amherst (UMass) has a direct metal laser sintering (DMLS) system that uses metal powder and a laser to create parts. A layer of powder is put down on a base plate, the laser melts the layer to form the part, another layer is added and the process repeats. This process can take time. Excess powder is sifted off from the final product and can be reused. The final part can be removed from the base using different techniques (e.g., a bandsaw, hammer and chisel), but UMass uses a wire electrical discharge machine (EDM) to remove the part from the base plate.
DED is also called a laser engineered net shaping (LENS) process. Four welding nozzles blow a mixture of stainless steel powder and argon gas. The laser melts the powder and deposits stainless steel where it is needed.
Hybrid machines include more than one process. Follette gives the example of a machine that combines DED and computer numerical control (CNC) at the industrial level, noting that these are large machines, and this process is very complex with lots of programming involved
(see Figure 2). There is generally a five-axis CNC with a metal depositing head (DED) in its tool changer. This hybrid can create machine finished parts, which can save time and money compared with traditional subtractive methods only. Another advantage of this process is that the amount of subtraction that needs to occur is limited, which preserves the benefits of subtractive tools compared to traditional subtractive methods. Programming for this type of system is very complex but can generate a stainless steel part in a relatively short period of time, using less material overall.
Figure 2. A machine that combines DED and CNC at the industrial level. Figure courtesy of University of Massachusetts Amherst.
Follette notes that metal injection molding has been around for a long time and is potentially cheaper than subtractive technologies. The steps in the process include mixing metal powder, molding that powder in a mold, debinding the part and sintering the part. Metal injection molding can be made into an additive process by using inkjet nozzles to carefully deposit the binder, then sintering the part, applying optional finishing methods and with the supports finally removed by hand. This method is not yet ready to be office based, although it is a relatively compact system.
In the selective laser melting process, a fine powder is melted by a laser. The molten powder solidifies and forms a solid material layer, and the collected layers build up to form a 3D object. In binder jetting, an inkjet head deposits tiny droplets of liquid binder in the precise location on each layer to build the part. The resulting component is then heated to a temperature where the binder burns off and the metal sinters into a solid mass. The advantage of the binder jetting process is time and cost, and with less heat there is less warping and less thermal stress of the final part. It is also possible to use sand instead of metal to additively manufacture sand molds for sand casting of metal.
Limitations
Depending on the part and the best process for manufacturing it, cost can be an issue in additive manufacturing. Part density, surface finish, warping and process speed are all potential limitations. The tensile strength of a part that is additively manufactured is similar to that of traditionally manufactured parts. However, Follette observes that fatigue cracking can occur more quickly with an additive part. More research is needed to better understand and reduce fatigue effects.
Follette notes that computers are needed to perform finite element analysis so that as little material as possible is used while still meeting the loading requirements for the particular part. Finite element analysis can illustrate where the higher and lower stresses occur on and in the part. The latest generative design software does this analysis repeatedly to generate structures that end up looking organic, like a tree. While this process can result in very efficient designs, in terms of manufacturing, until additive manufacturing existed, making these complex shapes was not possible. Now, it is possible to consider manufacturing these types of parts.
Comparing different additive processes
Table 2 shows a comparison of the strengths and weaknesses of different additive manufacturing metal processes. Each method has pros and cons and users must do their research to determine what is the most effective production method for a particular metal part.
Conclusions
Additive manufacturing offers rapid prototyping, low volume production, customized products and the potential for complex part geometries that can all be advantages in today’s manufacturing world. While it is important to do research to identify which metal additive manufacturing process will be most effective for a particular need, the process has great potential to create metal parts that are cheaper, as well as offering the potential benefits of making parts more quickly and better than traditional methods.
Andrea R. Aikin is a freelance science writer and editor based in the Denver area. You can contact her at pivoaiki@sprynet.com.