KEY CONCEPTS
•
Compressors and turbines place high demands on lubricants that often accelerate varnish formation.
•
Oxygen-containing base oils help keep varnish precursors in solution, and their degradation products do not form varnish.
•
The right lubricant formulation and proper maintenance can extend a lubricant’s service life significantly.
Sometimes solving one problem creates another one, but sometimes it provides unexpected benefits instead. For example, base oils for compressors and turbine lubricants went through a “problem period” before arriving at a selection of even better products.
When rotary screw compressors were first invented in the 1960s, says Will Hurley, owner and president of Fluid Metrics, a compressor oil, oil purification and oil additive company, synthetic oils were not readily available, so they were lubricated with mineral oils. These included API Group I oils, which contain sulfur and aromatic compounds that help to keep varnish precursors in solution. The average life of the mineral oil was about 1,000 hours, or about six weeks of continuous operating time. Varnish compound formation tends to proceed gradually and linearly in Group I oils, which can be monitored and replaced after predictable intervals, before deposits get out of hand.
1
Varnish problems in compressors and turbines began to increase as lubricant manufacturers moved away from Group I oils in favor of more highly refined hydrocarbon oils in API Groups II and III, as well as synthetic Group IV oils like polyalphaolefins (PAOs). These oils are more oxidatively stable than Group I oils. However, even very pure hydrocarbons can oxidize over time, especially during extended high-temperature operations. The resulting polar oxidation products have limited solubility in highly nonpolar base oils. Highly refined hydrocarbon oils and synthetic oils can function well until their antioxidant additives begin to fail, and then they can oxidize very quickly, forming varnish deposits.
2
Synthetic oils in API Group V, including polyalkylene glycols (PAGs) and polyol esters (POEs), are made from oxygen-containing organic compounds that increase the solubility of oxidation byproducts in the oil. For example, branched polyol ester base oils,3 a recent entry to the compressor and turbine lubricant industry, have a high density of oxygen-containing ether and ester bonds. When PAG and POE oils oxidize and degrade, they often form smaller molecules rather than the large molecular clusters—precursors to varnish deposits—that form in hydrocarbon oils, says Martin Greaves, chief technology officer of VBASE Oil Co.
Turbine and compressor challenges
“Compressed air is the fourth utility in an industrial plant,” in addition to electricity, water and natural gas, says Hurley. Oil-flooded rotary screw air compressors are “as common as forklifts” in industrial operations, he adds, noting that almost every operation requires a reliable supply of compressed air, which in turn relies on compressors with reliable lubrication
(see Figure 1).
Figure 1. Air compressors are a common sight in most industrial facilities. Figure courtesy of Fluid Metrics.
For pumps, turbines or gearboxes, the lubricating oil is in a separate cavity from the mechanical components. In contrast, a 100-horsepower rotary screw air compressor pushes about 500 cubic feet per minute of ambient air through a fixed volume of oil. “You couldn’t have a more aerated mixture,” Hurley says. “The big challenge for any lubricant or oil is oxidation,” Hurley says. “Can you think of a more extreme oxygenated environment than pumping air directly into the oil?” The compressed air-oil mixture exits the compressor at a temperature of about 180 to 200°F, then goes to a downstream tank that separates the air from the oil, and then to an after-cooler and moisture separator that removes the liquid water. The saturated compressed air, which also contains parts-per-million concentrations of oil mist, is then piped through downstream air dryers and coalescing filters before heading throughout the plant, where it is used to power moving mechanical components like cylinders and actuators. The hot oil remaining in the separator tank is also cooled, filtered and injected back into the compressor. “Minus the oil, the discharge air coming out of the compressor is generally cleaner than what’s coming in,” Hurley says, because “the compressor acts like a scrubber and the oil has taken out most of the contaminants.”
Contaminants in the ambient air ingested by a rotary screw air compressor can include particulates, water vapor and harmful fumes from chemicals made or used in the plant, algicides in the cooling water, welding fumes or combustion exhausts. Although the compressor’s inlet filter catches the particulates in the intake air, it doesn’t stop the gaseous contaminants from entering the oil-filled rotary screw housing. And the heat generated by compressing the air increases the solubility of these contaminants in the oil. Many gaseous contaminants are either intrinsically acidic, or they become acidic on contact with water. For example, “acid gas” pollution from diesel exhaust contains sulfur and nitrous oxides that form sulfuric and nitric acids inside the compressor.
Although turbines, like compressors, involve rapidly rotating parts and high temperatures, they have different requirements. Turbines can drive generators for steam or electricity (including hydroelectric generators), drive fluids down pipelines or drive large compressors for applications including liquefied natural gas production and transport. Large rotary screw air compressors may hold about 55 gallons of oil, but a power generator turbine uses thousands of gallons. Turbines often sit outdoors in their own housings. And, unlike compressors, they do not ingest the gases and particulates from plant operations, but they are exposed to ambient temperature and humidity changes. Turbine oil is isolated from heated gas or steam in the system. Filters remove particulates, but the oil does take in ambient moisture.
Research by turbine manufacturers, power companies and oil suppliers has shown that an increased use of Group II base oils in turbine lubricants and an increase in steam turbine peaking operation (turbines that run only during peak demand times) are behind lubricant problems including entrained air and foam, decreased demulsibility and varnish formation.
4
The varnish problem
Varnish is a particular problem for turbines and compressors. “Lots of things can function as lubricants and coolants in compressors and turbo equipment, but there are only a few things that don’t make varnish,” says Daryl Beatty, the founder of Diamond Blue Fluids. Lubricating oils are prone to oxidation at the high temperatures typical of compressors and turbines. Over time, oxidized hydrocarbon oil lubricants can form large, polar molecules that come out of solution as sticky deposits. These deposits can adhere to metal surfaces and harden into a hard-to-remove coating called varnish. Varnish precursors dissolved in oil can catalytically accelerate oil degradation and further varnish formation. Polar varnish precursors have limited solubility in highly nonpolar mineral base oils, which increases their tendency to come out of solution and form deposits that trap dirt and wear particles that can abrade mechanical components.
5
Varnish deposits can obstruct valve inlets and filter pores, and they can impede or block lubricant flow into tight-tolerance spaces like bearing raceways, causing an increase in friction
(see Figure 2). Varnish also affects cylinder rods, gears, turbine shafts and heat exchangers. Varnish deposits on servo, fuel and inlet guide vane valves in electrical power generation turbines can cause the valves to perform erratically. This can cause the turbine to shut down, and in severe cases, a power station can go offline until the situation is remedied. Excessive amounts of varnish can require lengthy equipment shutdowns for removing the deposits, or it may be necessary to replace expensive machine parts.
Figure 2. Varnish deposits on a bearing. Figure courtesy of Daryl Beatty.
Although some publications distinguish between varnish, sludge and lacquer, many people use “varnish” as a collective term for any type of deposit on a lubricated solid surface. The chemistries of these deposits vary widely, however, depending on the mode of lubricant degradation. “If you have water contamination in a steam turbine, the deposits are completely different than what you would have in deposits on a bearing from an extreme pressure (EP) formulated turbine oil in a compressor application,” says STLE member Greg Livingstone, chief innovation officer for Fluitec. “You’ll have completely different chemistries, but everyone still just calls it varnish.” Before any attempts to eliminate varnish deposits, it’s important to understand the source and characteristics (e.g., chemical composition and adhesion) of the varnish deposits. Mitigation efforts can involve solvency-enhancing additives, conventional filtration or ion exchange resins.
6
Some oxygen-containing synthetic lubricants can remove existing varnish that has not been allowed to harden, Beatty says, but the best approach is to keep varnish from forming in the first place
(see Figure 3). He notes that a varnish coating that is only about 8 micrometers thick can interfere with the operation of a rotor with an inside clearance of 25 micrometers. The result can be rotor instability and vibration, which reduces efficiency, increases bearing temperatures and increases the risk of damage or failure.
Figure 3. Localized deposits, like the partially hardened varnish shown here, are common in journal bearings. Figure courtesy of Fluitec.
Centrifugal compressors are the type most sensitive to varnish, says Beatty, followed by rotary screw compressors, which can tolerate some varnish, but eventually experience problems. Varnish deposits in rotary screw compressors can quickly cause the compressor to fail because the clearance between the screw and housing is tight to maintain compression efficiency. Varnish blockages can impede oil flow, starve bearings of lubrication and ultimately lock down the air-end and shear the shaft in a compressor, Hurley says. Insulating varnish coatings also affect the performance of cooling systems, causing machinery to run hotter and lubricating oil to degrade faster and further accelerate varnish formation.
Turbines are more prone to varnish formation than other mechanical systems. In one survey, 40% of 192 power plants experienced varnish-related problems. Newer, more efficient turbines require higher operating temperatures and smaller reservoirs, which place greater demands on a lubricant. Production loss from a single varnish-induced valve sticking event in a gas turbine can easily cost as much as $480,000 a day. Downtime and repair costs associated with a shutdown caused by stuck servo valves can range from $100,000 to millions of dollars.
5
Today’s turbine lubricants are most commonly mineral oils, says Livingstone, but some electrical power plants in the U.S. use PAG lubricants for their gas turbines because of OEM specifications. This wasn’t always the case, he adds. When Group II and Group III oils began to replace Group I oils some 20 years ago, the antioxidant chemistries in use at the time were one of the main contributors to varnish formation, he says. When antioxidants degraded and depleted, polar oxidation products in the oil formed sludge in the system, which eventually formed varnish.
At the time, Livingstone continues, OEMs did not provide specifications for low-varnish turbine oils or varnish potential testing and monitoring. The cost of PAG lubricants at that time could be twice to three times that of mineral oil lubricants, and turbine systems required 6,000 to 8,000 gallons. Converting a plant from mineral oils to synthetics required extensive flushing because of the incompatibility of the two types of oils. However, one valve tripping offline because of varnish deposits could cost $30,000 or more to repair, and a major outage could run into the hundreds of thousands of dollars. Thus, PAG fluids provided a significant advantage over highly refined mineral oils. Given the cost of an equipment failure, he says, converting to PAG oils was considered well worth the investment.
Costs and benefits today
As varnish problems began to increase across the turbine and compressor industries, lubricant formulators and OEMs began to pay more attention to varnish prevention. A greater focus was put on oil condition monitoring and equipment monitoring, as well as techniques for removing varnish deposits. In addition, test methods began to emerge to monitor and predict oil varnish formation potential. Oil formulators also improved antioxidant additives
(see Figure 4), and the less expensive hydrocarbon oils became more competitive with PAG oils for turbine fluids, although compressors still rely on PAGs, primary and branched POEs and PAG-POE blends.
Figure 4. Seven commercially available turbine oils in API Groups I through IV were oxidized for 12 weeks at 120°C with iron and copper catalysts. Deposit control was largely dependent on the balance of additives rather than just the base oil. Figure courtesy of Fluitec.
Oxygen-containing synthetic oils have made some more recent inroads into turbine operations. The first OEM to include PAG lubricants in its gas turbine specifications did so after one of its customers decided on their own to switch two turbines to PAG fluids in 2007. “The same [PAG] fluid that was put in those two turbines back then is still running today, 17 years later, without any varnish mitigation,” says Kevin Kovanda, president of American Chemical Technologies. He adds that PAG fluids for large turbines are similar to those used in compressors, but with a lower viscosity.
Although mineral oil formulations for turbine lubricants have improved and their lower cost is still a factor, the extended life expectancy for PAG fluids can still pay off over the life of the lubricant. Kovanda notes that PAG turbine fluids have about a 10-year half-life, judging from 10-year-old samples they have taken from operating equipment in the field, and it’s not unrealistic to predict a 20- to 30-year service life, which would essentially make PAG turbine fluids fill-for-life.
Because PAG fluids decompose into smaller, soluble molecules, PAG-based turbine fluids remain liquid as they age rather than forming solid varnish deposits, Kovanda says. Thus, these fluids do not need the varnish monitoring and mitigation measures that mineral oils require. He estimates that a mineral oil that costs $10 per gallon and lasts five years also requires $15,000 annually per turbine in monthly varnish testing costs, in addition to mitigation measures like ion exchange. Further, he says, a mineral oil change requires chemical flushing and cleaning the system and disposal of the old oil, which adds another $75,000 to $125,000.
Kovanda notes that today’s larger gas turbines generate more power but place greater stresses on mechanical components and lubricating fluids. “Peaker” turbines, which operate during spikes in power demand, experience greater system demands than base-load units, due to their start-and-stop operation. Cooldown periods allow oxidation products to come out of solution, affecting the reliability of the next startup.
7 Lubricants that are less prone to varnish formation can offer an even greater advantage during an extended equipment shutdown. He cites the example of a steel mill that went bankrupt and closed their plant. The plant sat idle for two years before another company bought the mill. PAG hydraulic fluid samples taken from the reservoirs showed that the fluid remaining in the system was still in good condition, so the buyer started the pumps, and everything ran normally. “PAGs offer a chemical solution to a chemistry problem,” he says.
Even in systems that operate continuously, varnish problems might go undetected, since test samples taken from a fluid reservoir might not reflect the conditions elsewhere in the system. Valves, bearings and other tight-tolerance components are especially sensitive to even small varnish accumulations. Kovanda notes that in hydraulic systems, where rod-and-cylinder components push fluids back and forth, fluids tend to stay in one region of the line for extended periods (sometimes months) rather than circulating all through the system and returning to the reservoir. Thus, it’s important to take samples from the valve stand as well as the reservoir. “Your fluid has to perform in the environment you’re putting it in,” he says.
Just add oxygen
PAGs (sometimes called polyglycols) and some POEs, Group V base oils commonly used in the turbine and compressor industries, are oxygen-containing organic compounds. Oxygen-rich oils have high volumetric heat capacities, Greaves says—an important factor for systems like compressors that use the same oil for thermal management and for lubrication. Their low heat of combustion is also an advantage for fire safety—these oils release less heat than many other types of oil if they do catch fire, which mitigates the amount of damage that results.
PAG fluids offer moderate film strength, good lubricity, high viscosity indices (180 to 280), good stability and good high-temperature performance. PAGs have intrinsic detergency and solvency toward a variety of oil additives and oxidation byproducts, which helps to prevent varnish buildup. PAGs also entrain less air than hydrocarbon oils, an important consideration because any varnish deposits that do form can increase air release times, which can cause microdieseling, pump cavitation, premature oxidation, component wear and further varnish formation.
7 Also, because PAGs are inherently polar, they are less prone to electrostatic discharge.
The most common PAG lubricants are made from ethylene oxide, propylene oxide, butylene oxide or copolymers of those oxides. Viscosity and solubility are controlled by adjusting the ratio and sequence (block or random copolymers) of the oxides in the polymer. Homopolymers of propylene oxide (that is, 100% oxopropylene groups) are insoluble in both water and oil. Copolymers of propylene oxide and ethylene oxide containing 50 to 75 weight percent oxyethylene are water soluble at ambient temperatures. Although water-soluble PAGs are stable against hydrolysis, they can damage paints and seals, and mixing water-soluble PAGs with mineral oils makes a gelatinous substance.
Oil-soluble PAGs, which are more expensive and less commonly used, are made from butylene oxide.8 Greaves notes that oxygen-rich base oils such as oil-soluble PAGs or branched POEs can be used as co-base oils or additives in formulating hydrocarbon-based lubricants. Their inclusion can help solubilize oxidation byproducts of hydrocarbon oils as they age, providing an extra level of protection in mitigating varnish formation. Specially formulated PAG oil additives can reduce a mineral oil’s varnish potential until it reaches the end of its target service life. At that time, the system can be switched over entirely to PAG oils if so desired.7 Including these oils into a hydrocarbon-based formulations can also provide a bridge between the lower price of traditional hydrocarbon lubricants and full synthetics.
Silicone oils have been sold as “lifetime fluids” in compressors, Hurley says, because they do not oxidize or form acids. However, they can cause corrosion and viscosity problems, and they are not good at preventing water vapor from condensing inside the compressor. Silicone oils have fallen out of favor, he explains, because their high cost, inclination to leak excessively and as “lifetime fluids,” contaminants will accumulate without supplemental purification. After a customer uses a silicone oil, he continues, it is nearly impossible to convert to another type of oil because the silicone penetrates the pores of the metal, making it almost impossible to remove. This often results in foaming problems, even after multiple flushes. However, a very small amount of silicone oil is often used as a defoamer for PAG oils, he adds.
Diesters have been used as reciprocating compressor lubricants because of their low coking tendency above 400°F. Diesters offer excellent solvency and detergency, but they can be aggressive toward elastomers, seals and hoses.
8 Hurley notes that some synthetic oils (PAOs, PAGs and others) are blended with diesters to reduce costs, but they have a tendency to hydrolyze in the presence of water, which is always present in compressor oils, and form sludge deposits.
Because of these negative factors, polyol esters have largely replaced diesters in high-temperature applications such as aircraft engines, high-temperature gas turbines, hydraulic fluids and heat exchange fluids. POE fluids offer good oxidative stability, and they can be blended with PAO base stocks to enhance additive solubility and reduce the PAO’s tendency to shrink and harden elastomers.8 PAG oils can be blended with a POE (typically about a 70-30 ratio) to increase solvency for polar species in the oil, Hurley says, which helps to prevent varnish deposits.
Synthetic ester base oils provide good lubricity, and recent formulations offer improved oxidative stability and better pour point performance, but they can also be incompatible with some seals and paints, and they can tend to hydrolyze. Some ester-based lubricants require a high concentration of unsaturated fatty acid esters to achieve good low-temperature performance and build viscosity, but the unsaturation also makes them prone to oxidation. Neopentylglycol esters made from short-chain saturated acids avoid these issues, but the stable saturated esters have a limited viscosity range (ISO VG 46 and below). Branched polyol ester base oils are designed to provide a wide range of viscosities. They offer good hydrolytic stability, miscibility with hydrocarbon oils and compatibility with seals and coatings, as well as high viscosity indices and good low-temperature performance, even when they are synthesized from saturated fatty acids.
3
Testing and monitoring
Improvements in test methods and condition monitoring keep turbine operators apprised of the condition of the oil in their systems, Livingstone says. Membrane patch colorimetry tests and other methods give an indication of the potential of an oil to produce varnish by showing the characteristics of the oil in the sample. The actual amount of varnish deposits in the system could be higher or lower, but the tests can track changes in varnish potential over time.
The only way that PAG fluids produce varnish, Kovanda says, is to run them at 250°C or higher, where the more volatile components begin to evaporate. Although you could do this in laboratory experiments, he says, you wouldn’t run across this temperature in an operating environment because elastomers, babbitt alloys and other materials would start to fail long before the PAG lubricant. Because PAG fluids do not produce varnish, he says, the only needed routine lab tests are viscosity, acid number, particle counts and water content. He estimates that these tests, which are run every six months, cost about $100 per turbine.
Even under the most pristine conditions, however, oxygen in the air will oxidize a lubricating oil to produce acids, especially under high temperatures and pressures. In an industrial plant environment, regular monitoring of the oil’s acid number (AN) is critical, says Hurley. A two-stage titration procedure, he adds, is sometimes used to determine strong acid number (SAN) and AN and distinguish the effects of the commonly used barium sulfonate corrosion inhibitor (which also acts as a pH buffer) from acidic oil degradation products.
Synthetic oils resist varnish formation until the additives become sufficiently depleted and oxidation starts to affect the base oils, Hurley says. As acids accumulate in the oil, they have a catalytic effect that accelerates the oxidation reaction and produces more and more acids at a faster and faster rate. As the antioxidants continue to deplete and acid levels increase, the oil reaches a point where it becomes “brittle”; that is, degradation begins to increase exponentially and the oil will rapidly fail. AN monitoring is critical for all air compressor lubricants but is especially important for food grade compressor oils used in the food processing industry, he says. The additives approved for food grade oils are not as robust as those used for general industrial compressor oils, which causes them to deplete sooner, and need to be replaced after only 4,000-6,000 hours of operation before they rapidly fail.
Sustainability factors
PAGs, like many other synthetics, mostly originate from non-renewable fossil sources including natural gas. Because of the large amount of processing that goes into manufacturing them, they have a higher carbon footprint than mineral oils. However, some PAG varieties are biodegradable, which mitigates their environmental impact.
POEs are sometimes made from plant-based fatty acids reacted with polyol alcohols, but they may also come from fossil sources. Compressor and turbine lubricants made mainly from POEs are under development, and these may become more common if challenges associated with production scale-up and pricing can be overcome, Kovanda says. Government regulations like those coming into effect in the European Union may influence the pace of industries adopting plant-based POE fluids for applications that can use them, he adds. Branched POE base oils, an emerging product, are manufactured from biobased fatty acids and are non-toxic and readily biodegradable, Greaves notes. These base oils show promise as formulation components for equipment subject to high thermal stresses, where they provide increased detergency in full synthetic lubricants or in semi-synthetics that are based on hydrocarbon oils.
Fuel and energy efficiency is another aspect of sustainability. At present, synthetics are commonly used to improve fuel efficiency in engine oils. Synthetics also reduce friction and improve efficiency in gear oils and hydraulic oils. However, the energy-saving mechanism in those applications is different than the active mechanism in rotating equipment like turbines and compressors, Livingstone says. The primary efficiency driver for turbines and compressors is specific gravity, and PAGs and POEs have a higher specific gravity than mineral oils like PAOs. Thus, while PAGs and other synthetics can enable significant efficiency improvements in other applications, the gains are much smaller in turbines.
Sustainability factors also include service lifetime, recycling and disposal considerations and potential pollutants associated with production, disposal and incidental or accidental exposure to the environment. Here, the long service life of synthetic lubricants based on oxygen-rich oils can minimize oil waste and reduce the toxicity of the original fluids and their decomposition products.
“Researchers in our industry are paying more attention to a lubricant’s thermophysical properties, and the body of knowledge here continues to grow,” says Greaves. The high volumetric heat capacity of oxygenated base oils helps them transport heat away from machinery, which helps both the lubricant and the machinery to run cooler. This, Greaves says, could lower oxidation rates, extend fluid life, lower oil waste and provide a more sustainable solution.
Using the same lubricant for a longer time can also reduce downtime and costs. The usual practice has been to use turbine oil for five to 10 years, until the antioxidants are consumed, and then to replace the oil. But the base oil can still be in good shape, Livingstone says. “One of the trends that we’re seeing is that a lot of users now are replenishing the antioxidants in the oil and allowing that oil to be used several times longer,” he adds. This practice, common for compressor oils, is less frequently used for turbine oils. However, replenishing the antioxidants on a semi-regular basis can allow a mineral-based turbine oil to last for decades, which is no small thing in a system that can contain up to 20,000 gallons of oil, he says.
Although commercial replenishment packages are not currently available for turbine oils, some users are adopting this practice on their own and using testing and monitoring to mitigate any associated risks. Livingstone notes that OEMs support this practice because it lowers the carbon footprint of the oil, and he anticipates that lubricant manufacturers seeking to decarbonize and lower their environmental impact will become more supportive in the future. Commercial additive replenishment packages are readily available for compressor oils, and these can significantly extend the base fluid’s life, says Hurley, noting that PAG/POE compressor oils are ideally suited for additive replenishment because of their non-varnishing and high solvency properties.
PAG oils have exceptionally long service lifetimes, says Beatty. One of his development projects involved monitoring the ANs for PAG oils in centrifugal compressors over a period of years. The initial AN was about 0.2 milligrams of KOH titrant per gram of oil, and he planned to change the oil after it reached 1.0. However, he monitored some of the machines for eight years, and the AN had only gone up to about 0.4. At that rate, he says, the fluid was on track to last 30 years in that machine. Not many fluid manufacturers would want to make one sale every 30 years, but cutting costs by making a lower-performing fluid could have resulted in unpredictable degradation rates. Recommending fluid changes after an intermediate time span is better for sales, he says, while providing the customer with an ample margin of safety.
Rotary compressors, which run for about 12,000 hours over an 18-month period, are an especially demanding application. Beatty notes that typical OEM fluids must be changed about every 8,000 hours, but current formulations of PAG-based lubricants routinely last 12,000 hours, depending on the type of fluid and the operating conditions. To make a PAG or other oxygenated oils last even longer, they can be run through an acid-absorbing ion exchange resin cartridge housed in a kidney loop in the oil stream
(see Figure 5). Depending on the application and environment, PAG/POE fluids that have been run through these compressor oil purifiers and have had their additives periodically replenished have been shown to last for up to 80,000 hours (about 10 years) before they need to be changed—a major step forward for sustainability and cost savings.
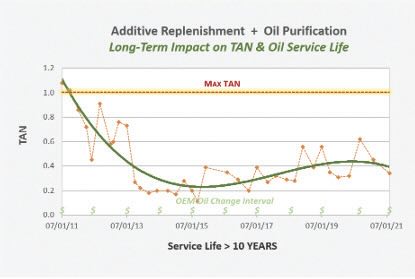
Figure 5. Additive replenishment and oil purification can significantly extend a lubricant’s service life. Shown here: total acid number (left) and pH (right) of an oil sample measured over ten years of service. The TAN should remain below 1.0 and the pH above 4.5 to ensure proper performance. Dollar signs indicate the OEM's recommended oil change intervals. Figure courtesy of Fluid Metrics.
Greaves notes that, in contrast to the extensive work done on recycling and reconditioning of hydrocarbon oils in the past 30 years, less work has been done on recycling Group V synthetics, which include the oxygen-containing synthetic oils. “There is a lot more room for innovation in that space,” he says. “You can certainly recycle esters by chemically taking them apart and rebuilding them. It’s more difficult to do with polyalkylene glycols.” He adds that Group V base oil manufacturers can learn from existing recycling and reconditioning research for hydrocarbon feedstocks. However, the long service life of many synthetic oils makes recycling them a less frequent necessity.
Greaves adds, “The relative simplicity of formulations using Group V base oils offers another advantage. Unlike hydrocarbon oils, these synthetics often do not require viscosity index improvers, pour point depressants, dispersants and detergents. Eliminating them from formulations can reduce a lubricant’s manufacturing footprint and reduce the complexity of supply chains, which also contributes to more sustainable lubricant solutions.”
Special applications
For most turbine operations, fire safety is not a major issue when selecting an oil. However, it is a consideration for steam turbine electrohydraulic control systems, which provide emergency stops and prevent the turbines from running too fast. Synthetic fluids can be practical for these critical braking systems. Fire safety is also critical for steam turbines because they operate at very high pressures. Leaking fluids can spray oil onto a hot steam pipe, which could ignite a fire. “In steel applications or any applications where there’s a lot of heat, there’s absolutely a benefit with PAGs and POEs over mineral oils,” Livingstone says. Lighter viscosity fluids are more flammable, Kovanda says, so larger molecules are preferred for their higher flash points and fire points.
For turbines in hydroelectric plants, the risk of turbine oil escaping into the water supply adds to the attraction of using synthetic turbine oils. Biobased esters are being developed for hydroelectric turbines to mitigate the environmental risks of oil leaks, Livingstone says.
The main use of polyol esters is in turbine fluids for jet aircraft, where they are valued for their stability at high temperatures and their lack of tendency to make varnish, Beatty says. Aircraft lubricant formulators face stringent requirements because of the criticality of their lubricants to the safety of human lives and liability for expensive aircraft and cargo.
Another application for synthetic oils is in operations that are prone to shear stress deposits, Livingstone says
(see Figure 6). Shear stress can show up as a rising sawtooth pattern, independent of load, in a bearing’s temperature trend plot. Severe shear stress can produce localized deposits called hot varnish, which doesn’t show up in tests of bulk fluid samples.
9 These localized deposits form in fast-moving bearings under heavy loads, a situation that is common in some compressor applications. Mineral oils can’t avoid these deposits, Livingstone says, so synthetics offer a benefit in areas like offshore platforms, liquefied natural gas trains and other very expensive applications where lubricant cost is less of a factor.
Figure 6. Localized deposits are most often caused by shear stress degradation. The tilting journal bearing pad deposits and wear shown here are an example of the often strong correlation between the two effects. Figure courtesy of Fluitec.
Making the transition (or not)
If oxygenated oils prevent varnish, last longer between fluid changes and help prevent machinery failure, why doesn’t everyone use them? For one thing, not everyone needs this level of performance, Beatty says. PAGs and related oils are similar in price to other synthetic oils like PAOs, but they are more expensive than mineral oils. For machinery that operates at lower temperatures or where the clearances are larger, price may dictate staying with conventional lubricants.
Although it is possible to convert a system that has been running with a PAO lubricant to a PAG lubricant, the two types of fluid offer different advantages and limitations for different demands. Considerations for choosing one type of fluid over the other include technical and regulatory requirements, equipment and site conditions and labor and maintenance resources.
10
PAO-based lubricants may be preferable when mineral oil compatibility is a priority, including when the existing system is using a mineral oil lubricant and the time and expense of taking the system down and thoroughly cleaning it in preparation for a PAG lubricant is impractical. PAO lubricants also work well with existing seals and paints that are compatible with mineral oils. If the system is not prone to environmentally damaging oil leaks, fire resistance is not a requirement and water ingression into the system is not an issue, PAO lubricants can work well.
10
“Varnish protection is really a critical criterion for selecting turbine oils,” Livingstone says. “Consequently, virtually every oil manufacturer has optimized and iterated their formulation and really designed their turbine oils, not only for long service life, but also minimal deposits. Today, there are far fewer varnish problems than there were 20 years ago.” He adds that synthetics provided an essential stopgap technology while the major oil companies were optimizing their formulations during the transition to Group II and Group III base oils.
Benchmark tests for dozens of commercially available turbine oils have shown a significant improvement in mineral-based turbine oil performance over the past couple of decades, Livingstone says. He adds that today’s mineral oil formulations, which include improved antioxidants, exhibit performance and service life similar to PAGs, even in large-frame gas turbine applications. Small amounts of co-solubilizers in today’s mineral-based turbine oils keep polar degradation products in solution to further reduce sludge and varnish. Co-solubilizers include oil-soluble PAGs, water-insoluble PAGs, alkylated naphthalenes and esters. These developments enable Group II and Group III oils to last longer and protect against varnish better than Group I oils and to rival the performance of PAG fluids for a much lower price, he says.
Because Group V synthetics are currently more expensive than hydrocarbon oils, they tend to be used in applications like compressors and turbines, where equipment operates continuously under high temperatures and pressures, and for applications where equipment failure is especially expensive or hazardous. Because these applications are so demanding, lubricants must go through a lengthy testing and approval process before they are cleared for use.
PAG-based lubricants offer environmental benefits, especially in situations where leaks could pollute water supplies or in food production operations. These lubricants are also fire resistant, and they can hold water that enters the system in solution. PAG lubricants can improve the efficiency of equipment operation and energy usage, and they do not form varnish as the fluids age.
10
Oxygen-containing lubricants are well established in the compressor industry, and to a lesser extent, the turbine industry. Branched POE base oils, an emerging technology, build on the industry’s experience with PAGs and their functionality, says Greaves. “If you look across our industry, for the last many decades, not many companies have succeeded in bringing to market a new base fluid technology that is not only technically superior to what is available today but is economically attractive as well and aligns with the sustainability goals of our industry. The appetite for change and innovation in our industry is high.”
REFERENCES
1.
Day, L. (2008), “Solving varnish problems in gas turbine lubricants,” TLT,
64 (1), pp. 32-38.
2.
Livingstone, G. and Oakton, D. (2010), “The emerging problem of lubricant varnish,”
ME Maintenance and Asset Management, July/August,
25 (2), pp. 37-42.
3.
Hunt, Z. (2022), “VBASE Base Oils: A new class of high-performance, environmentally friendly fluids,” TLT,
78 (11), pp. 96-99. Available
here.
4.
Whitby, R. D. (2013), “Varnish deposits from steam turbine oils,” TLT,
69 (11), p. 104. Available
here.
5.
Hong, S.-H. and Jang, E. K. (2023), “Varnish formation and removal in lubrication systems: A review,”
Materials, 16, 3737,
https://doi.org/10.3390/ma16103737.
6.
Rensselar, J. V. (2023), “Varnish: Root causes, detection and remediation,” TLT,
79 (4), pp. 52-56. Available at
here.
7.
Kovanda, K. “The end of varnish: Advances in turbine fluid technology to improve gas turbine performance,” American Chemical Technologies white paper.
8.
Beatty, D. and Greaves, M. (2006), “Polyalkylene glycol synthetic PAG oil explained,”
Machinery Lubrication, September 2006. Available
here.
9.
Livingstone, L. and Evans, C. (2023), “Understanding and detecting shear-stress induced deposits,”
Machinery Lubrication, November 2023. Available
here.
10.
Sherman, J. et al. (2021), “Understanding PAG- and PAO-based lubricants,”
Power. Available
here.