TLT: How long have you worked in a lubrication-related field, and how did you decide to pursue a career in the lubricants industry?
Lang: I have been working in the lubrication-related field for over 13 years. My journey began during my academic studies, where I developed a keen interest in fluid dynamics and their applications in various industries. The lubricants sector particularly fascinated me, especially the field of fluid treatment and filtration due to its critical role in enhancing efficiency and reducing wear in machinery. During my early career, I recognized the significant impact that innovative filter solutions could have on both performance and sustainability for all kinds of machinery and equipment. This realization motivated me to pursue a career in the filtration business, where I could contribute to developing cutting-edge technologies to suit certain applications. At HYDAC, already from the beginning I had the opportunity to work on exciting projects that address the evolving needs of the hydraulic and lubricating market, further fueling my passion for this field.
TLT: What has led you to combine industrial work with scientific endeavors?
Lang: Combining industrial work with scientific endeavors has always been a key focus in my daily work. My passion for engineering and research drives me to explore how theoretical principles and modern engineering technologies can be applied to solve real-world challenges.
A very good example is the use of modern multiphase computational fluid dynamics (CFD) simulation that allows us to model the complexity of fluid systems and explore the effect of developed products on the architecture of hydraulic systems in real-world conditions
(see Figure 1).
Figure 1. Multiphase computational-fluid-dynamic simulation of a hydraulic tank system.
In the industrial environment, I have witnessed firsthand the complexities and practical needs of various technical solutions, particularly in the hydraulic and lubrication technology sectors. This experience has shown me the importance of grounding scientific research in practical applications to achieve tangible results.
Electrostatic discharge (ESD) in hydraulic and lubricating systems is a great example here. Some years ago this phenomena was unknown to the industry. With the employment of low conductive fluids, the first cases of ESD occurred. Through the years the phenomenon has been investigated by extensive field investigations, using scientific equipment like high voltage test heads and oscilloscopes. Proper scientific research led to the development of electrostatically optimized filter element technology by the material science approach
(see Figure 2).
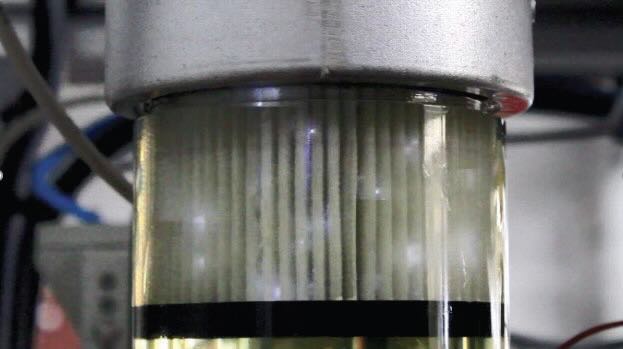
Figure 2. (a) Arcing in a filter element and (b) on the outside of a filter housing.
Like the example described prior, during my daily work I have the unique opportunity to bridge the gap between science and industry while developing satisfactory products and advanced fluid treatment solutions tailored to market requirements. By collaborating with cross-functional teams, we can integrate innovative research findings into products and solutions, ultimately enhancing performance and sustainability.
TLT: What would you say was your most significant achievement?
Lang: I think my most significant achievement has been the development of new filter element technology. In combination with the previously developed tank optimization solutions, these innovations may stand for a substantial leap in the efficiency of filtration and the sustainable use of hydraulic systems in general.
The filter mesh pack is providing electrostatically optimized filter media and due to its unique recipe dynamic filter stability well over 106 load cycles at the same time.
With the new technology, we created a filtration solution that not only meets stringent cleanliness requirements but also emphasizes sustainability through the use of ecofriendly materials and a pressure drop reduction of 30% during operation in comparison to previous solutions. The technology significantly extends filter service life and reduces machines energy consumption, aligning with the growing demand for environmentally responsible practices in industrial operations.
Additionally, we were able to improve the sustainability of hydraulic systems by reducing the carbon footprint of machines. The deaeration of hydraulic oil is covered by the special functionality of the filter and the need to be addressed by providing large oil surface area in the reservoir anymore. Together, these developments contribute to a more sustainable and efficient use of resources, making an impact on machine designs while addressing environmental challenges. I think this holistic approach to filtration and fluid management is the right way forward toward more efficient and sustainable hydraulic machine architectures.
TLT: How do you see further development of filter media in industrial applications?
Lang: The development of filter media in industrial applications is an exciting and rapidly evolving field. As industries increasingly prioritize efficiency, sustainability and compliance with stricter environmental regulations, the demand for advanced filtration solutions is on the rise.
I foresee several key trends shaping the future of filter media. Firstly, the integration of smart technologies will enable real-time monitoring and optimization of filtration processes. This will enhance operational efficiency and predictive maintenance, reducing downtime. Secondly, the focus on sustainability will drive innovation in materials used for filter media. We can expect to see a shift toward biodegradable and recyclable materials that minimize environmental impact while maintaining high performance.
Lastly, the customization of filter solutions to meet specific application requirements will become more prevalent. Tailored filter media designed for particular industries or fluid characteristics will help achieve better filtration efficiency and longer service life.
I think we have to be committed to exploring these developments and incorporating cutting-edge technologies to deliver superior filtration solutions that meet the evolving needs of hydraulic and lubricating systems.
TLT: What are the current driving factors toward further development of filter media?
Lang: In my opinion, the current development of filter media is influenced by several key driving factors:
•
Environmental regulations. Stricter regulations concerning emissions and waste management are pushing industries to adopt more efficient filtration solutions. Companies are increasingly required to minimize their environmental footprint, leading to innovations in filter media that improve performance while adhering to regulatory standards, e.g., REACH conformity.
•
Sustainability. There is a growing demand for sustainable materials in filtration systems. This includes the development of biodegradable and recyclable filter media. Moreover, smart technologies, including sensors, are enabling real-time monitoring and analytics, allowing for proactive maintenance and optimization.
•
Industry-specific needs. Different industries have unique challenges that require tailored filtration solutions. As industries evolve, the demand for specialized filter media that can handle specific contaminants or operating conditions is increasing.
•
Economic efficiency. The need for cost-effective solutions drives innovation. Industries are looking for filter media that not only provide superior performance but also reduce operational costs through longer service life and lower energy consumption.
TLT: What is the No. 1 piece of advice you would give to a person who might be interested in starting a career in the lubricants industry?
Lang: The No. 1 piece of advice I would give to anyone interested in starting a career in the lubricants industry is to cultivate a strong foundation in both theoretical knowledge and practical application.
Understanding the fundamental principles of fluid dynamics, chemistry and materials science is essential, as these will provide the groundwork for your expertise. Additionally, seek hands-on experience through internships, projects or collaborations within the industry. This practical exposure will help you grasp the complexities of lubrication technology and its applications in various sectors. Networking also is crucial. Connect with professionals in the field, attend industry conferences and participate in relevant organizations. Building relationships can provide valuable insights and opportunities for mentorship, which can significantly impact your career trajectory.
Finally, stay curious and open to continuous learning. The lubricants industry is constantly evolving with new technologies and sustainability initiatives, so being adaptable and proactive about expanding your knowledge will set you apart.
You can reach Timo Lang at Timo.Lang@hydac.com.