HIGHLIGHTS
•
Microplastic fibers, no more than 500 microns in length, are generated during repeated washings of fabrics and are sources of marine pollution.
•
Abrasive friction, created by the mechanical interaction between textiles during the washing process, is the primary source of microplastic fibers.
•
Application of a two-layer fabric finish to nylon and polyester fabrics significantly reduced the formation of microplastic fibers.
Sustainability impacts a significant number of applications where lubricants are used. One application which is of significant consequence to individuals is the clothing worn. Among the questions are: Can a specific type of clothing provide more comfort during periods of high temperatures, and what happens when worn clothing is washed?
In a previous TLT column,
1 the first question is addressed as a new composite fiber based on boron nitride and polyvinyl alcohol exhibits good thermal conductivity when woven into a fabric. The composite fiber was produced through the use of a 3D printer. Subjecting the composite fabric to a laser was used to assess thermal conductivity. Polyvinyl alcohol and cotton fibers were used for comparison purposes. Testing showed that the composite displayed the lowest maximum temperature increase and the highest thermal conductivity.
Preparing a fiber that can be used in wearable fabrics to help individuals stay cool is very useful, but there can be concern about what happens to the fabric after repeated washings. Kevin Golovin, assistant professor in the mechanical and industrial engineering department of the University of Toronto in Toronto, Ontario, Canada, says, “Repeated washings of fabrics can produce significant quantities of microplastic fibers which are sources of pollution that can negatively impact marine organisms such as fish and shellfish. Such issues as inflammation, organ damage and hormonal disruption can occur. In addition, these marine organisms can be consumed by individuals leading to potentially harmful health effects associated with harmful chemicals and toxins attached to the microplastic fibers.”
Approximately 0.19 million metric tons of microplastic fibers are discharged from wastewater treatment facilities. The reason is these fibers are no more than 500 microns in length.
The primary source of these microplastic fibers is synthetic textile garments prepared from such materials as polyester and nylon. Both of these fibers account for more than 90% of synthetic apparel produced. Golovin explains, “Microplastic fibers are generated through the mechanical interaction between textiles during the washing process and also when the fabrics rub against the washing machine drum. Abrasive friction is created between fibers leading to the formation of the microplastic fibers.”
Attempts to minimize this effect through altering individual’s laundry habits or using washing machine filters do not eliminate the root cause. One approach that has been devised is to add a coating to the synthetic fabric to reduce abrasive friction. Golovin says, “Pectin, a natural polysaccharide found in orange juice, has been added to fabric. Initial results were promising as abrasive friction declined, but the problem is the coating rubs off after a short period of time.”
Golovin and his colleagues have now developed a new approach to prevent microplastic fiber release by using a novel coating.
Two-layer fabric finish
The researchers initially tried to coat both nylon and polyester with polydimethylsiloxane (PDMS), polyethylene glycol (PEG) and perfluoropolyether (PFPE). In all three cases, the coatings readily wore off during washing as they were not well bonded to the substrate.
Golovin says, “We determined that to significantly reduce abrasive friction a new strategy needed to be developed to ensure the coating is strongly bonded to both nylon and polyester. Our approach involved finding a molecule that can bond to both the fiber and to the three potential lubricant candidates.”
This two-layer fabric finish starts by reacting polyester with 3-aminopropyltriethoxysilane and nylon with a sulphonic acid-terminated trimethoxysilane. The terminal functionalities of each polymer readily react with the three coatings (PDMS, PEG and PFPE) to produce polymer bristles with liquid-like flexibility that impart a low friction surface to both nylon and polyester.
Fabrics coated with the three candidates were evaluated through five consecutive laundry washing cycles at 40°C for one hour. Nylon and polyester fabrics that are not coated were used as controls. The researchers found that microplastic fiber release declined by at least 88% for the three coatings with the nylon substrate and at least 86% for the polyester substrate.
To assess the relationship between abrasive friction and reduction in microplastic fiber release, coefficient of friction data was generated using a conventional pin-on-disk machine. Golovin says, “We used conventional pin-on-disk tribology with nylon and polyester used for both pieces of the tribometer. Dry friction and wet friction were obtained with detergent in water used to coat both the pin and the disk.”
The researchers found that reducing the wet coefficient of friction below 0.25 is associated with a sharp reduction in the release of microplastic fibers. Scanning electron microscopy illustrated the effectiveness of using the two-layer fabric finish. Figure 3 shows an image of an uncoated nylon fabric’s surface fibers containing many broken fibers that are released as microplastic fibers during washing. In contrast in Figure 4, nylon fabric coated with PDMS remain pristine with no evidence of any breakage.
Figure 3. Many broken fibers are present in a scanning electron microscopy image of an uncoated nylon fabric’s surface fiber after repeated washings. Figure courtesy of the University of Toronto.
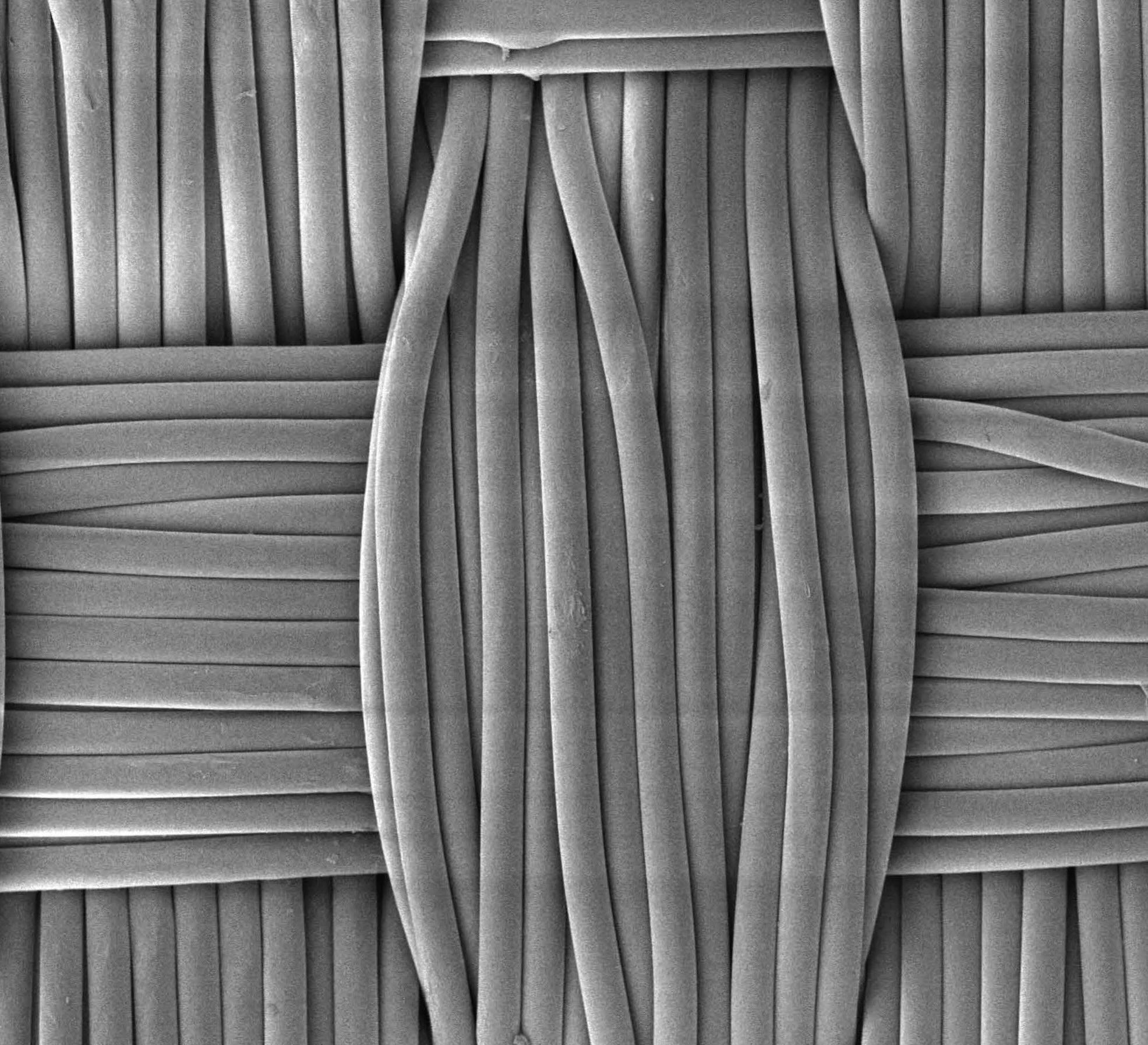
Figure 4. Repeated washing of fabrics coated with a two-layer fabric finish affords no evidence of any breakage as noted in this scanning electron microscopy image. Figure courtesy of the University of Toronto.
The potential of using tribology to reduce microplastic fiber pollution is an example of using tribology to make a process more sustainable. Golovin and his colleagues are continuing to determine the viability of commercializing the two-layer fabric finish. He says, “We are currently evaluating the durability of the fabric finish by washing coated samples for eight-to-nine laundry cycles. A second aspect is to determine how to apply the coatings in an aqueous medium instead of the currently used solvent.”
Golovin also intends to evaluate fiber blends as many garments are prepared from combinations of fibers including cotton, nylon and polyester. Additional information can be found in a recent article
2 or by contacting Golovin at kevin.golovin@utoronto.ca.
REFERENCES
1.
Canter, N. (2018), “Keeping cool with wearable textiles,” TLT,
74 (2), pp. 14-15. Available at
www.stle.org/files/TLTArchives/2018/02_February/Tech_Beat_II.aspx.
2.
Lahiri, S., Dijvejin, Z., Gholamreza, F., Shabanian, S., Khatir, B., Wotherspoon, L. and Golovin, K. (2024), “Liquidlike, low-friction polymer brushes for microfibre release prevention from textiles,”
Small, 20 (33), 2400580.