KEY CONCEPTS
•
Dancers rely on specific types of shoes and floors to perform breathtaking moves safely.
•
Special stage effects and outdoor venues bring unpredictability to live performances.
•
A new generation of dancers is more receptive to quantified insights on materials, biomechanics and motion studies.
Ballet dancers launch themselves into the air, spin on the tips of their toes and lift, catch and balance their dance partners. Tap dancers shuffle, brush and pound out rhythms on hard floors, sand or corrugated metal. Breakers master sudden stops and starts as well as slides and spinning on the tops of their heads. Dancers need smooth surfaces for ease of movement and friction for stability and safety—all during the same performance. “If something goes wrong, it can be career ending for a dancer,” says Suzi Kilbourne, production stage manager for the Washington (D.C.) Ballet and technical director for Percussion Discussion Productions, a consortium of tap dance companies in the Washington, D.C. area. “These people are elite athletes, and the floor is their foundation.”
How do friction, momentum, torque, impact force, surface roughness, chemical solubility, ambient environment and all the rest of the science and engineering that goes into other athletic endeavors translate into a more gravity-defying jump or an extra turn or two in a pirouette? How much traction is needed between a dance shoe (or a sock or a bare foot) and a stage floor? The answer is, “It depends.”
Art meets science
In August, elite athletes of many kinds convened in Paris for the Summer Olympics. A small army of scientists and engineers worked to provide them with a competitive edge measured in centimeters or in hundredths—or thousandths—of a second. They competed in lightweight, springy shoes designed to offer stability and support. Runners set new records on tracks designed to reduce impact and vibration, as well as boosting their forward momentum. Electronic devices assisted athletes in perfecting their form during training and recorded their performance metrics with ever-increasing precision.
The world of dance performance, especially classical dance, takes a different approach. Dancers also are highly trained, and the jumps, turns and lifts they perform require high levels of physical strength and control to amaze audiences and avoid career-ending disasters. Like their Olympic counterparts, dancers rely heavily on training and intuition to help them position their bodies and move through space. They develop a “feel” for how sticky, soft or resilient specific floors are and adjust their approach accordingly. However, they are less likely to augment this “feel” with numerical data and analysis, says Glenna Clifton, assistant professor of biology, University of Portland (Oregon).
Clifton takes a multidisciplinary approach to studying the biomechanics of how animals move. Her undergraduate senior thesis, titled “The Coefficient of Friction of the Pointe Shoe and Implications for Current Manufacturing Processes,” focused on one particular type of animal, the human ballet dancer.1 As a part of her undergraduate project, Clifton quantified the coefficients of friction for various brands of pointe shoes against various samples of flooring. She also calculated how rotational friction changed due to shifts in shoe–floor contact area for pointe shoe designs over the years. Recently she has returned to dance biomechanics research in collaboration with Kathleen Bieryla, a mechanical engineer (see Figure 1).
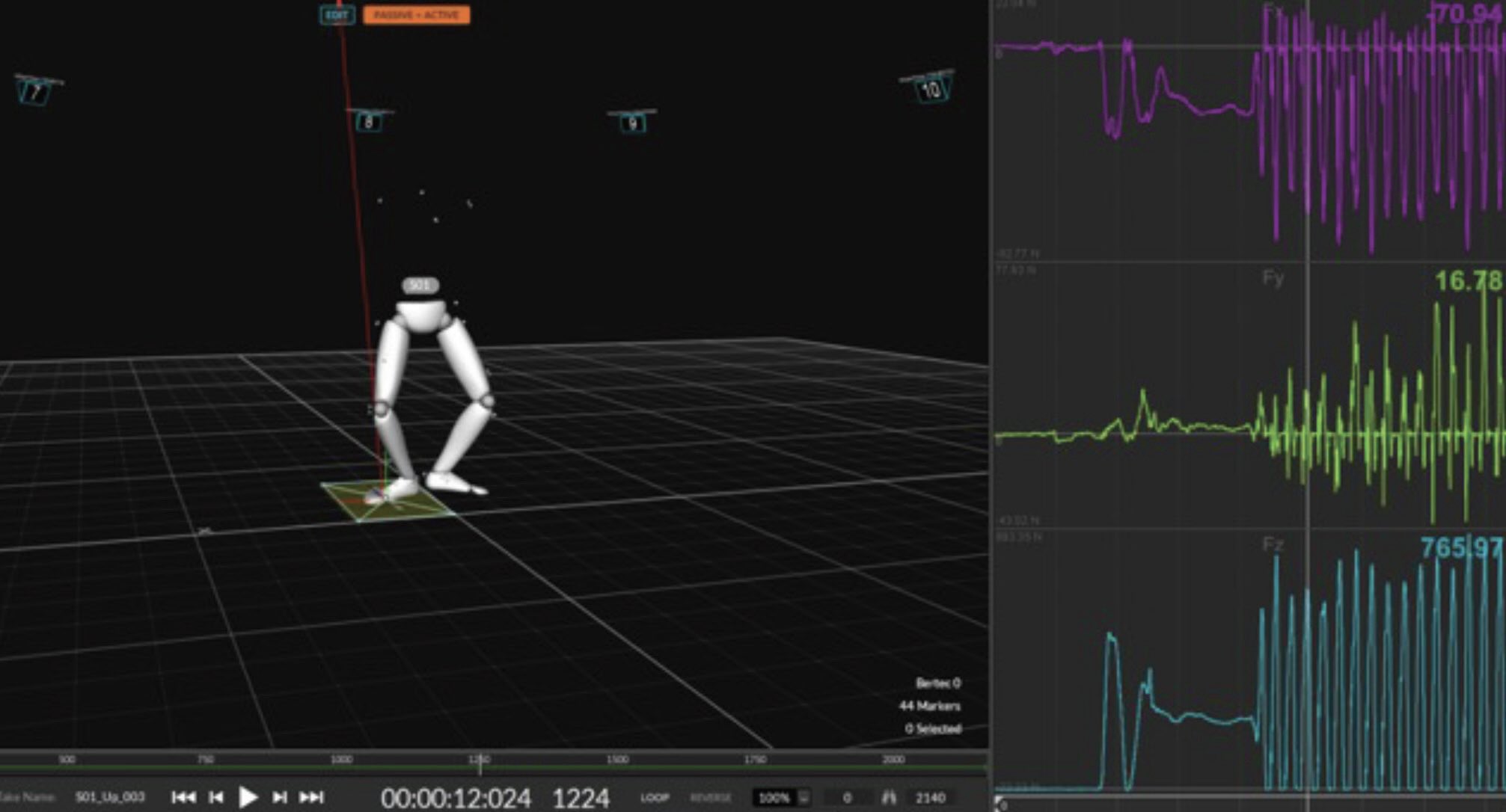
Figure 1. Videos of dancers jumping are used to create computer models for biomechanics studies. Figure courtesy of Glenna Clifton.
For quantitative analyses to be useful for dancers, Clifton says, there must be a way for scientists and engineers to communicate their results to and receive meaningful feedback from the dancers. Biomechanics researchers are currently studying track and field athletes and people with mobility problems, and flooring designers are working on safer surfaces for hospitals and public places. As a part of this work, they have learned to get feedback from users who are more conversant in intuitive terms than in scientific terminology. This type of communication, she adds, also could work in introducing a more scientific approach to dance floor surfaces.
Like their colleagues who focus on Olympic athletes, scientists and engineers who want to delve into dance floor tribology must first understand what various types of dance demand from performers. The reward could be not only more impressive performances but also fewer injuries—the catastrophic variety and the small strains and injuries that accumulate over the course of a career.
Dancing of any kind involves combinations of linear and angular motion. Force is needed to start or stop motion or to change speed or direction. Gravity provides a downward force, the floor provides support and the dancer’s contact with the floor or with another dancer enables the changes in speed and direction. For example, dancers need friction to begin a leap, pushing downward and backward against the floor to accelerate forward and upward into the leap. A floor with too little friction might cause the dancer to slip.2
Twisting and rotating motions require torque to generate angular acceleration—the dancer pushes the floor one way, and the friction between the leg and the floor pushes the other way. The dancer balances their body at the center of mass, which must be directly above the area of contact with the floor. The smaller this area of contact (e.g., the toe of a pointe shoe), the more difficult it is to maintain this balance.
Although the physical principles remain the same, various styles of dance apply them in very different ways. The major flooring manufacturers promote qualities like shock absorbance and slip resistance, Clifton says, and they offer different types of flooring for different styles of dance. “But I haven’t seen anything tested or any data from them. I don’t know if this is a qualitative investigation that they are doing or if there is quantitative research. It isn’t open to the public, as far as I can tell,” she says. She adds that a quantitative analysis of friction coefficients as a function of humidity, for example, could test commonly held assumptions to see how accurate they are.
Dancers are especially prone to lower extremity injuries. In sports, both flooring and footwear reduce the incidence of these injuries, but ballet and contemporary dancers get little in the way of protection from their footwear. Thus, they must rely on flooring to absorb shocks and reduce acute and cumulative damage.
Vinyl dance flooring is available in various surface finishes to accommodate different types of dance performance and shoes. A “fast” floor has a harder, smoother, lower-friction surface than a “slow” floor. Classical ballet dancers often prefer a slower floor and soft-soled shoes for slip resistance and for muffling sounds. Tap dancers prefer faster floors and hard-soled shoes that allow them to move quickly across the surface and to produce sharper, more percussive sounds.
Ballet: A feeling of floating
The trend in ballet choreography during the early 19th century was to make dancers appear weightless by having them dance on their toes, and pointe shoes had tapered tips to enhance the effect. The first ballet pointe shoes, Clifton says, were lightly reinforced silk slippers, barely more than a flat ballet slipper. By the turn of the 20th century, wider toe boxes, which enabled dancers to stay en pointe longer, became more accepted. Vinyl floors, also introduced during the 20th century, were padded for shock absorption, and they also muffled the sound of a dancer’s footsteps, adding to the illusion of weightlessness.
Ballet requires adequate friction between shoes and floors to allow a dancer to push off from the floor into a jump and to land safely without slipping. However, too much friction requires them to work harder to maintain the spin of a pirouette. The entire surface of the floor must provide a “just-right” degree of friction, performance after performance, so that dancers can rely on a consistent surface as they perform their moves.
Electromyography has been used to measure muscle responses as dancers perform repeated sautés (symmetrical double-footed jumps) on hardwood and reduced-stiffness floors.3 Not surprisingly, a hard floor returns more of the force of the landing to the dancers’ lower extremities, while a reduced-stiffness floor absorbs some of this force, elongating the period of force absorption. This, in turn, slows the muscle activation rate, which reduces the risk of injury. However, a reduced-stiffness floor also requires the dancers to exert more force to achieve the same jump amplitude. Despite the extra work involved, dancers who evaluated floor surfaces with various quantified mechanical properties preferred floors with greater force reduction magnitudes than required by European standard specifications for sports surfaces.4
Today’s ballet floors typically consist of a semi-sprung deck under a thick vinyl flooring layer.5 Wood battens, foam backing or rubber pads provide a certain amount of “give” for impact cushioning, which helps prevent injuries, including repetitive stress injuries. The heavy-duty vinyl surface layer, typically referred to as a Marley floor, provides the right amount of slip resistance and sound muffling. (Although “Marley” is now used as a generic term, the floor type is named after the company, no longer in existence, that introduced the floor in the 1960s.)
Marley flooring is rolled out in wide strips across the subfloor and held in place using fabric gaffer’s tape that matches the color of the floor. “Tape is tricky,” Kilbourne says. Sometimes dancers select the location where they do a turn or a jump based on the differences in texture between the tape and the flooring. The strength of the adhesive and the slipperiness of the tape can vary from batch to batch, even from the same manufacturer. When the tape is taken up after a performance, it can leave a gooey residue on the flooring, or it can be dry and crumbly. If the tape sealing the seams in the flooring is too slick, the stage crew will sometimes use dish scrubbers to roughen up the surface, she says. Gaffer’s tape has a shelf life typically two to three years for double-faced tape and three to four months for top tape. Flooring expands and contracts with changes in temperature, and if tape is allowed to stay in place until it fails, the floor can fracture.6
Karen Storms, formerly the director of production for the Washington (D.C.) Ballet, says that various ballet companies use different types of floors, depending on preferences and dance types. Dancers in resident companies become accustomed to their home theater’s flooring and the sprung deck below, and the rehearsal studios and stage use similar materials to provide a similar feel. For performances at other venues, the company can use the sprung deck at that venue or bring their own portable deck. “Dancers are very sensitive to small differences,” she says, noting that difficult leaps and turns require a high degree of precision to execute safely and well. “They are putting their entire bodies at risk” (see Figure 2).
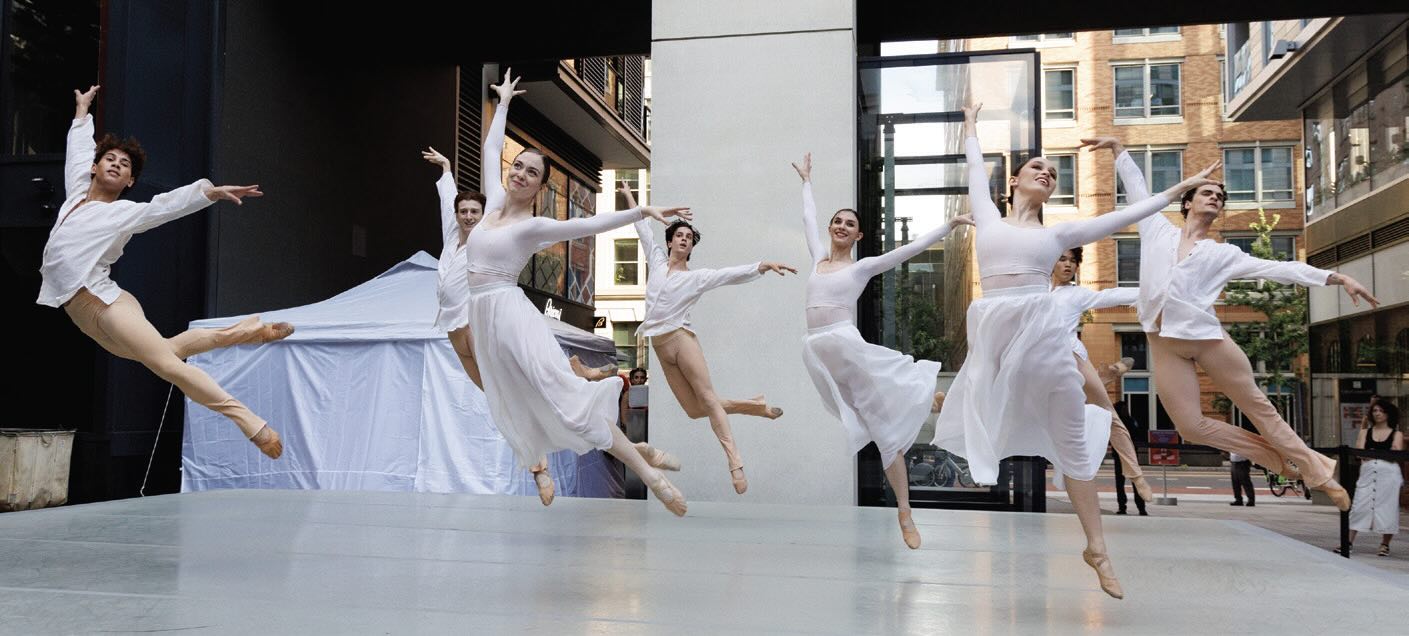
Figure 2. The Washington Ballet Studio Company performs “Ghostlight” at CityCenterDC in June 2024. Figure courtesy of The Washington Ballet and xmbphotography.
Flooring texture helps determine the amount of friction between the floor and the dancers’ shoes, and a thin padded underlayer gives dancers’ feet a bit more grip as they land on the floor. Shoe soles affect friction as well. “I want a miracle chemical,” Kilbourne says. “Something that offers the slip resistance of rosin, but that doesn’t transfer onto the floor.” Rosin, made from hardened pine sap ground into a coarse powder, adds extra traction to the soles of pointe shoes or ballet slippers. Some dancers also put rosin inside their shoes to keep their feet from slipping or on their hands for partnering to ensure a better grip for difficult or dangerous maneuvers. However, not all dance venues and companies allow the use of rosin, which can cause sticky spots on the floor, Storms says. Rosin that is ground into the floor over time can become polished and slick, and the random combination of slick and sticky spots presents a hazard to the dancers. Also, rosin is hard to clean off the floor, resulting in floors being replaced more often.
Routine floor maintenance includes keeping the floor clean and free of dirt, rosin residue, body lotion, perspiration and other substances that affect the floor’s coefficient of friction (see Floor Cleaners). Buffing a rough floor will remove its textured surface, making the floor “faster.” Keeping the ambient environment between 60°F and 80°F and the humidity level near 50% at all times also helps maintain a consistent surface.7
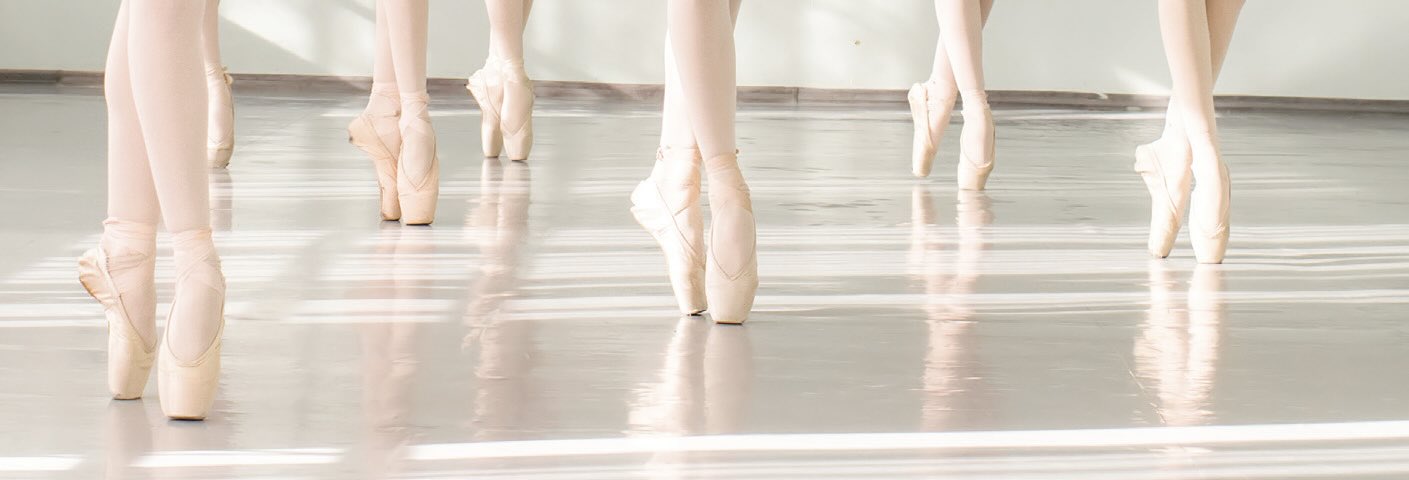
Floor cleaners
Commercial ballet floor mopping solutions remove dirt and other contaminants and provide some stickiness. Volatile components are an important consideration because dancers exert themselves and breathe deeply, amplifying the effects of inhaling cleaning product fumes. Each company and venue is likely to have its own special combination. Preferences are very personal, and as varied as ballet itself, Storms says.
Dance floor manufacturers warn against using ammonia, vinegar, alcohol, bleach, acetone or household cleaning products. Most dance floor surfaces do not have a factory finish, and these substances can dissolve the surface of the flooring, requiring it to be replaced more often. Damage can include pitting, scratching or breakdown of the plasticizer, which can cause the surface to harden.6
One friction-increasing method that is seldom used now is to mop the floor with diluted Coca-Cola to deposit a sticky layer. Over time, however, the acid can soften and damage the vinyl, and the sugar can attract insects. Various dance enthusiasts and production specialists unanimously agree that the cumulative effect is “gross” and “disgusting.”
Shoes make a difference, too. Ballet shoes typically have leather, canvas or suede soles and rigid shanks along the shoe soles for arch support. Pointe shoes have flat, reinforced toe boxes that allow dancers to bear their entire body weight on the tips of their toes. One pointe shoe company has stopped making pointe shoes using the traditional layers of fabric, paper and paste for the toe box. “They use plastics and new materials, and they test those materials,” Clifton says. Although other companies have started making innovative shoes as well, she says, “there’s been really strong pushback against them. I’ve been wearing those pointe shoes for close to two decades now, and they have become more accepted in the world of ballet, but there’s still a lot of resistance.”
Even with the evolution in choreography and shoe designs, ballet remains a traditional art form with a certain amount of resistance to change, Clifton says. She contrasts this attitude with that of runners in the Olympics, who quickly adopt new developments that could give them a competitive edge. This resistance, she explains, is part of the reason why there hasn’t been more scientific work done on shoe and floor design. The traditional part says, “this is how we’ve always done it, and we’re going to keep it that way.” The artistic part says, “there’s something to this that shouldn’t be quantified or dissected scientifically,” she explains.
Ground contact: Modern dance and breaking
Floors for modern dance, which focus less on airiness and sound muffling than classical ballet, also can be suitable for hip-hop, jazz, breaking, aerobics classes and Zumba. Because performers are often barefoot or wearing floor-gripping trainer shoes, and they perform spins and slides with various parts of their bodies in contact with the floor, the floors they use tend to be smoother and harder than those used for classical ballet.
One particularly challenging flooring situation arose in 2018, when the German group Da Rookies toured with their breakdance version of “The Nutcracker.” Their performance combined hip-hop, capoeira (an acrobatic Afro-Brazilian martial art), breakers in trainer shoes and classical ballet dancers in pointe shoes. The widely varying needs of the dancers required them to acquire specialty flooring designed for multiple dance styles for their 2019-2020 tour.8
It’s not just the type of floor in use, Clifton says, it’s the condition of the floor and how recently it’s been cleaned. Unlike classical ballet, modern dance emphasizes contact with the ground, including running, sliding, walking, jumping and falling. “You can always tell if there was a modern dance class [in the rehearsal room] before you because there might be sweat and the oils from people’s skin, and that can really influence the flooring,” Clifton says. Modern ballet and contemporary choreography often feature barefoot dancers. “Barefoot dancing is difficult,” she says, “because you don’t want too much resistance.” You actually want less friction to help prevent blisters, she adds. Some dancers use half-socks that cover the front parts of their feet, she says, but others build up calluses “through many, many blisters.”
Breaking (sometimes called break dancing) was included in the Summer Olympics for the first time this year. Breakers, whose moves include spins and slides on the floor, avoid wearing shirts with printed lettering or images on the back to reduce friction between the shirt and the floor, and they may also wear long sleeves if they plan to slide on their elbows.9 Breakers who do headspin maneuvers typically wear hats to provide padding and to reduce friction between their heads and the floor.
Unlike pole vaulters, breakers don’t gain momentum from a running start, but rather create it using their floor movements.10 Breakers master the positioning of their center of mass, building angular momentum around an axis of rotation to execute maneuvers like the Windmill (see Figure 3). This “down rock” move involves rolling the shoulders and upper torso on the floor, around an imaginary vertical rotation axis centered on the point of contact with the floor. The legs are extended upward in a V shape and the hands push against the floor to provide propulsion. When this move is executed in the middle of a routine, the breaker must flow smoothly into the move and then out of it and into the next move.
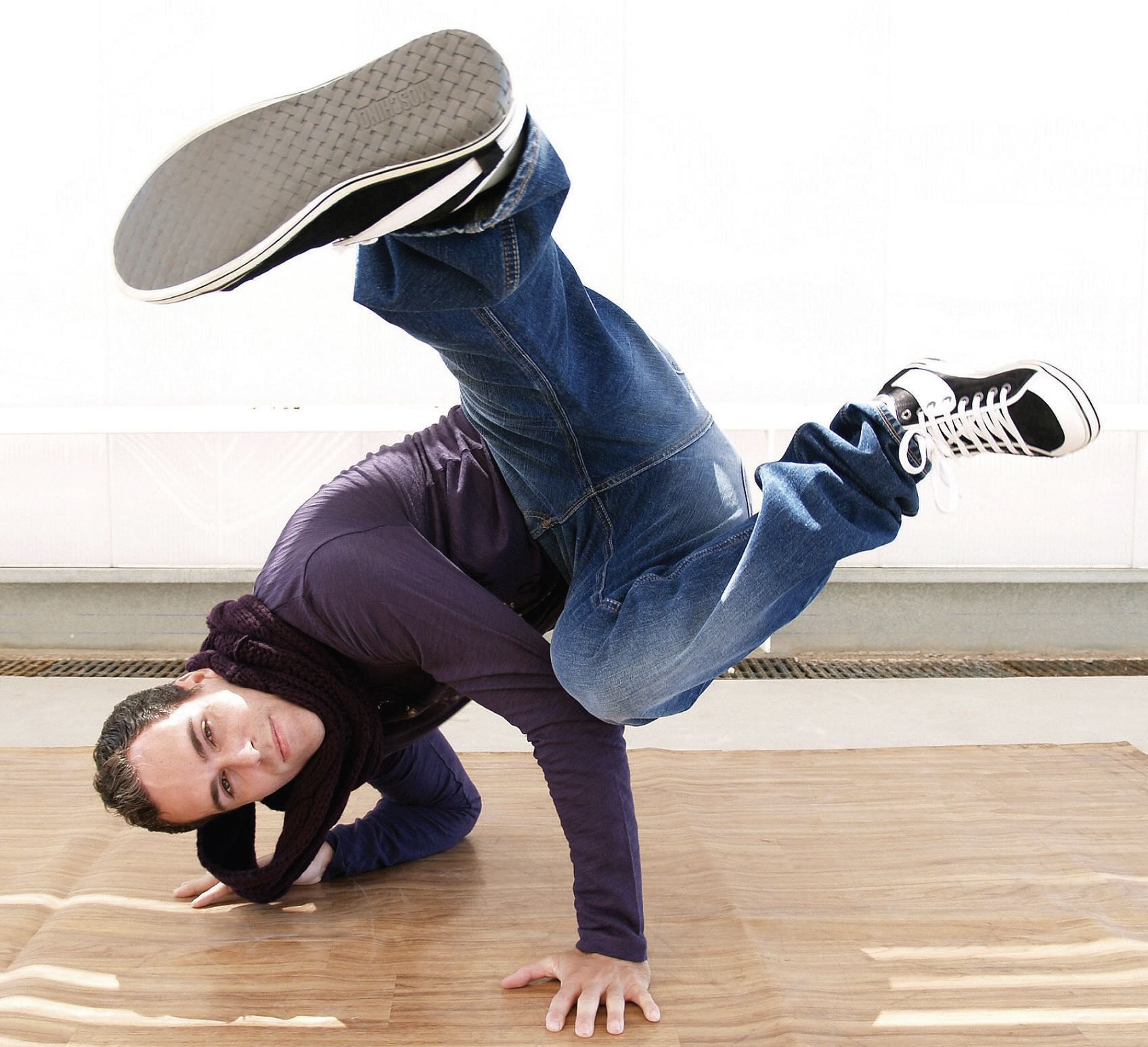
Figure 3. Alberto Pardo Vela, a Spanish professional dancer who performs as EXTREMO, demonstrates a breaking move called the Windmill. Figure courtesy of Nenini06, CC BY-SA 3.0, via Wikimedia Commons.
Physics also comes into play when a breaker executes a one-handed spin. The free hand propels them around the spin, creating friction and torque around an axis centered at the palm that stays on the floor. The breaker keeps their body in a straight line centered over this axis to maintain their balance. Even feet-on-the floor “top rock” moves involve friction and momentum. During quick steps and abrupt stops, inertia causes the breaker’s body to continue moving in the direction they were traveling. The breaker relies on muscle engagement and friction between shoes and floor to keep themselves from falling forward.9
Tap dance: Bring in ’da Noise
“Ballet is the look, tap is the sound,” Kilbourne says. She explains that although tap dancers’ bodies are loose and relaxed as they dance, the sounds they make are crisp and precise. Interest in tap dance experienced a resurgence in the 1990s with the aggressively percussive, hip-hop influenced musical “Bring in ’da Noise, Bring in ‘da Funk.”
Tap dance, flamenco and Irish dancing are all types of “percussive” dances, involving hard shoe soles against hard floors. In contrast to ballet, tap dancers want to maximize the rhythmic sound of their dance steps or shoes brushing against the floor, and they prefer smoother floors that allow them to shuffle and slide freely. “Tap dancers are percussionists who use their bodies as their instruments,” Kilbourne says (see Figure 4). Tap flooring can be made of maple parquet, which provides a heavy, hard surface. Lighter materials for portable floors include plywood or masonite. It’s not just the flooring on the stage that matters, she says. “We have to be careful backstage,” she adds, because metal shoe taps can pick up wax from linoleum floors, making the taps slippery.
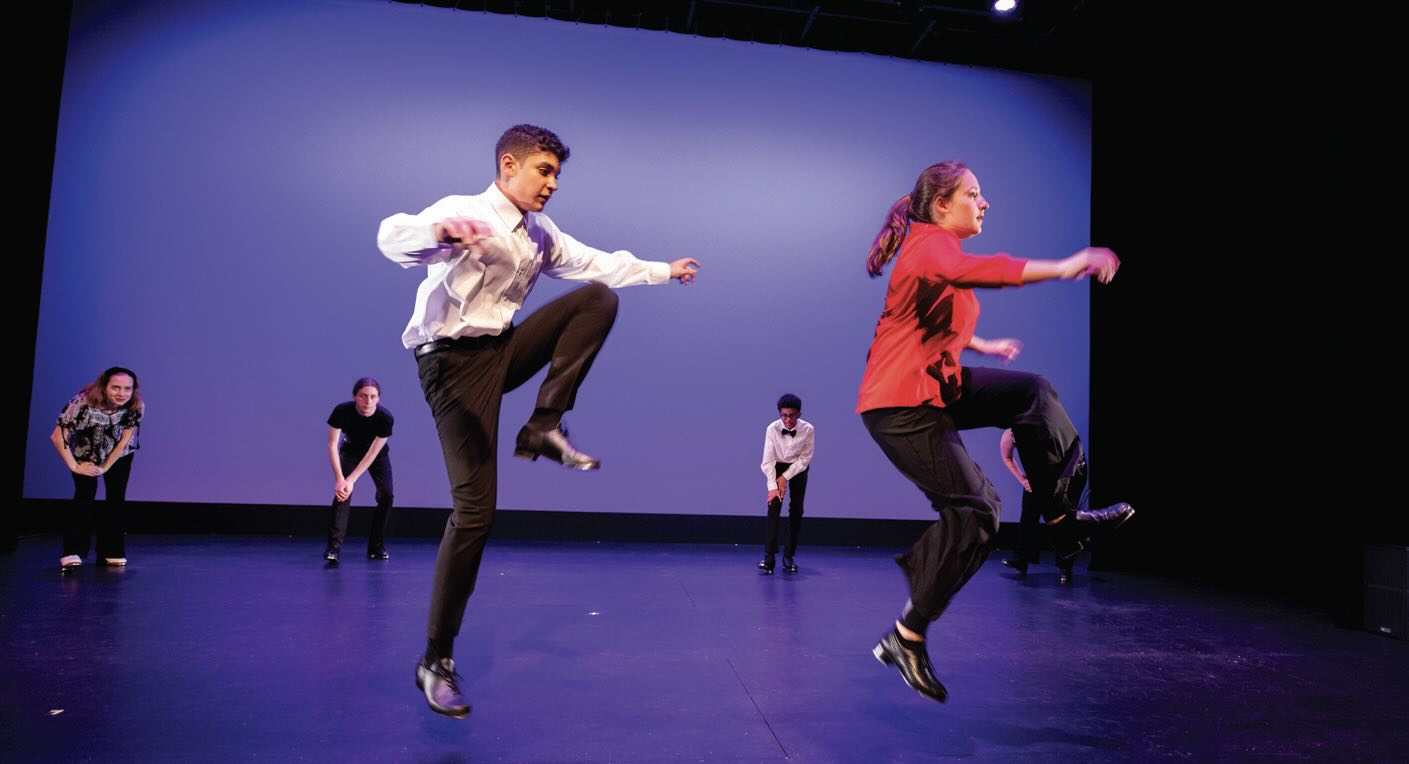
Figure 4. Tap dancers performing on a masonite floor without a sprung deck. Figure courtesy of Percussion Discussion.
Tap dancers wear leather oxford shoes or “character shoes” (mary-jane style shoes with heels of varying heights). Various types of shoes produce different sounds. “Leathers” refer to shoes without metal taps, and they can be used for sand dancing, which involves slides and shuffles on a floor or in a shallow box containing a thin layer of sand. Aluminum taps attached to the shoe sole provide a sharper, more percussive sound and dancing on wood, smooth metal or even corrugated metal adds even more variety to the sounds a dancer can produce. “It’s almost like having a drum kit,” Kilbourne says.
Tap shoes are more durable than ballet shoes, but aluminum taps do wear down. A well-worn tap floor can take on a silvery gray color from the aluminum particles embedded in the wood, Kilbourne says. Toe taps usually wear faster than heel taps because heel taps move up and down, providing the bass notes, she explains, while toe taps provide the treble notes as they brush back and forth across the floor. Taps can be “tuned” by adjusting how tightly they are fastened to the shoes. Looser taps provide more reverb, she says.
Irish dance shoes can have soft soles or hard fiberglass soles, depending on the type of dance. One study showed that when Irish dancers “rock” (shift from side to side on their toes), they can experience a force through their ankles that is as much as 14 times their body weight, far more force than ballet dancers experience when dancing en pointe. Thus, well-fitting shoes, good choreography and proper form are necessary to reduce the risk of injury.2
Live performances and special effects
“Live theater is unpredictable,” Kilbourne says, but the stage crew takes every precaution to ensure the safety of the dancers. Touring dance companies routinely load their trucks into the theater on a Monday in preparation for a Wednesday opening night, she adds. But the setup must be done right.
Outdoor performances, popular during the summer months, present their own challenges. Heat and humidity change the traction and give of vinyl flooring, which is often sold in heat-absorbing dark colors. Dancers have been known to burn themselves when bare skin touches hot vinyl. Spraying the floor with water helps, but this makes the floor more slippery. Even the dancers’ sweat on the floor can cause slick spots. If the air is humid enough to cause condensation, the flooring may have to be dried off between scenes. Changes in temperature affect the floor’s stickiness and hardness. Liquefied rosin can be applied to floors in extreme situations, like outdoor performances on very humid days, when dancers are in danger of slipping.
Special stage effects can complicate matters still further. For example, various productions of “The Nutcracker” use hundreds of pounds of dry ice to create a snowy field or a fog for the journey to the Land of Springtime. Dry ice also creates the illusion of a foggy lake in the final act of “Swan Lake” (see Figure 5). If the air in the theater or outdoor stage is humid, this cold layer on the surface of the stage can cause water condensation, creating a slippery surface under the fog. Other types of chemical fog can leave a residue on the floor. Hazers, used for laser and other lighting effects, disperse a fine cloud of mineral oil or glycol droplets over the stage area (see Figure 6). If too much haze is used, these droplets can fall onto the stage, making it slippery. However, using too little makes the light beams harder to see. Atmospheric conditions, air circulation and the size of the theater all affect the sweet spot between too much haze and too little.
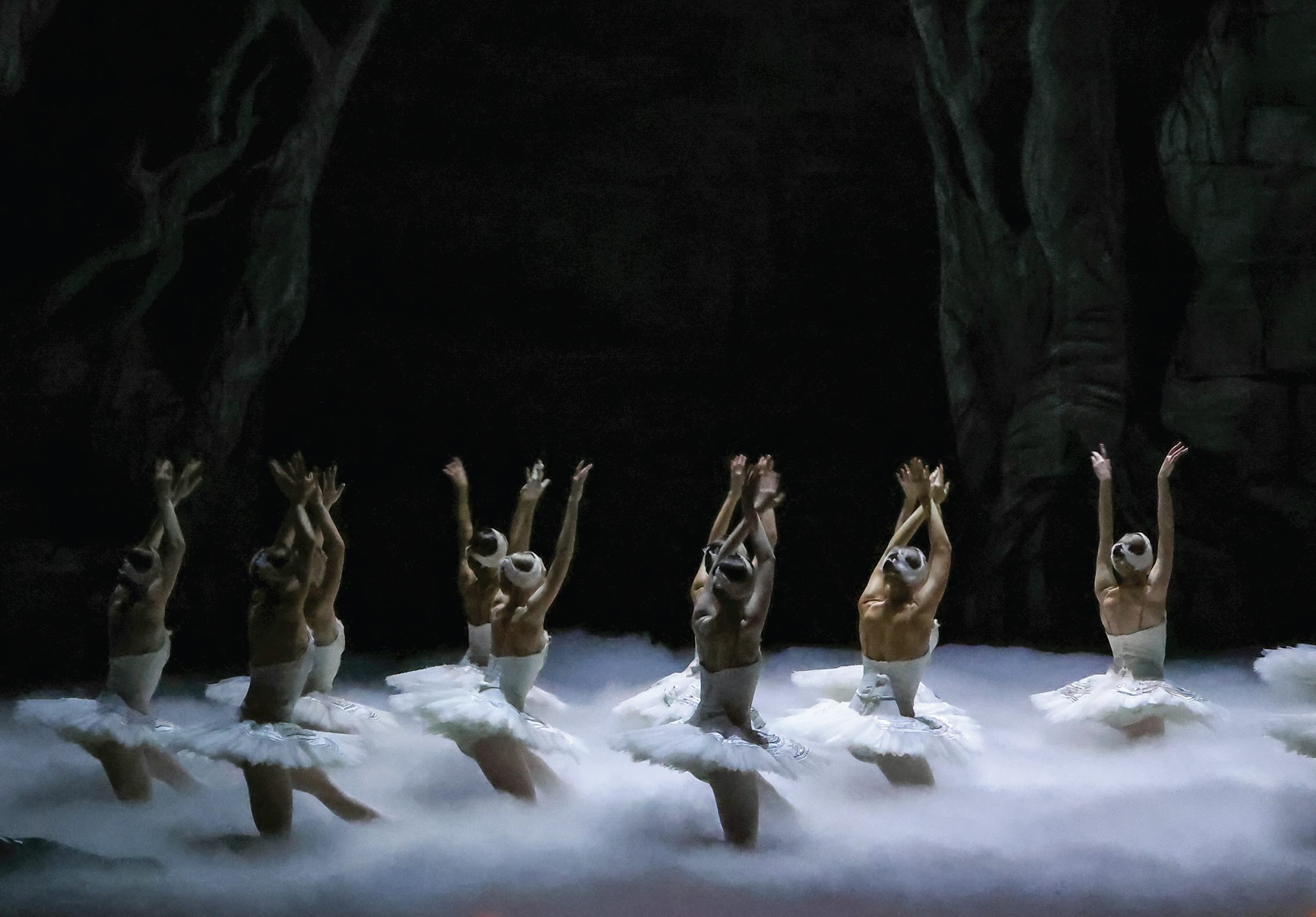
Figure 5. The Washington Ballet performs a foggy scene in “Swan Lake” at the Kennedy Center in Washington D.C. in February 2022. Figure courtesy of The Washington Ballet and xmbphotography.
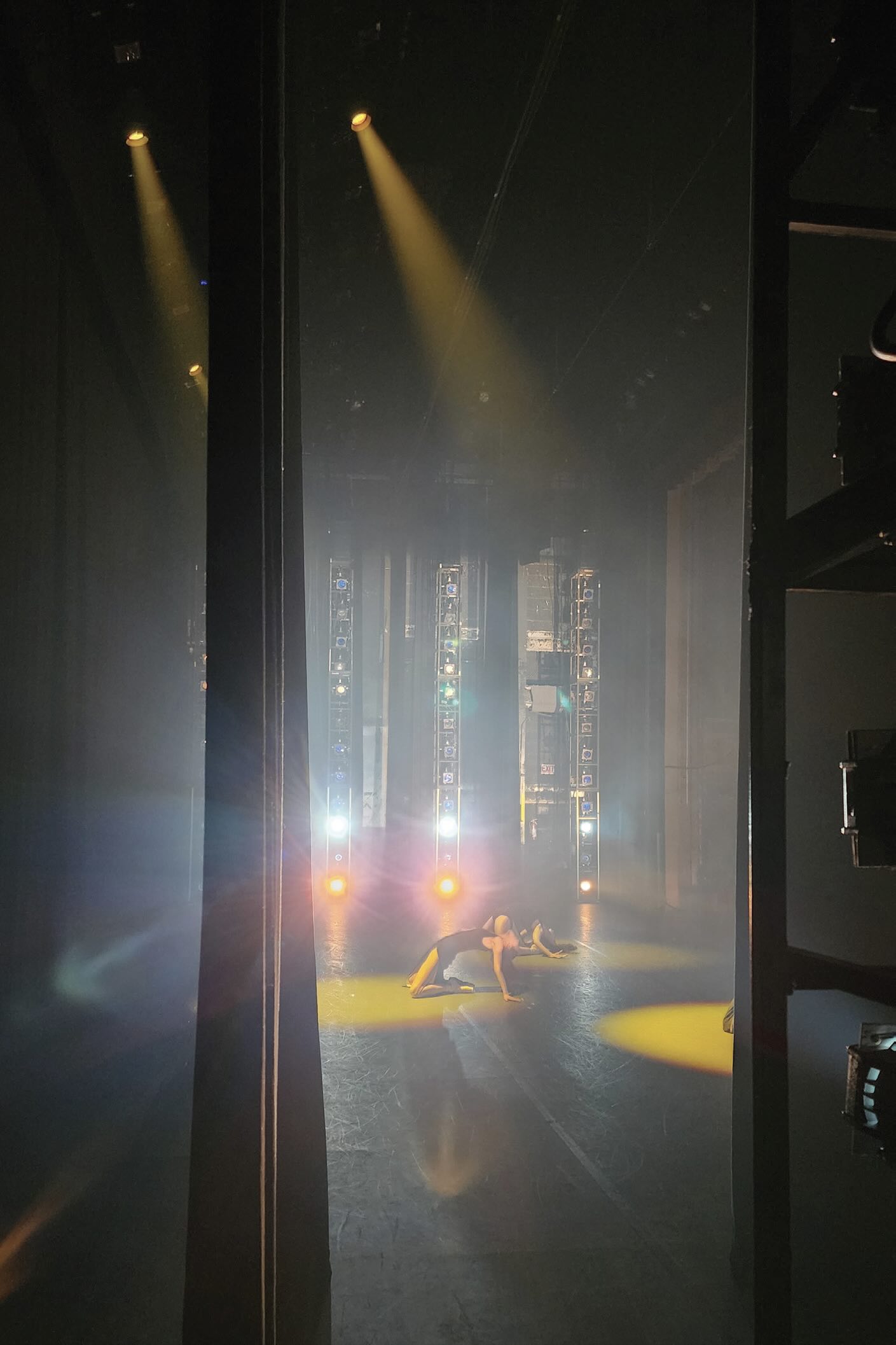
Figure 6. Hazers distribute a fine spray of droplets over the stage to create special lighting effects at the Warner Theatre in Washington, D.C. Figure courtesy of Suzi Kilbourne.
Marley flooring is prone to scratching and scuffing, even during routine use, Kilbourne says, but stage lights and special effects also can leave their marks. Pyrotechnic effects can leave burn marks on the flooring, for example. She recalls one “Nutcracker” performance where she had to stop the show because exploding quartz stage lights rained sharp, hot shards onto the stage. The shards melted tiny “craters” into the Marley floor, Kilbourne says, and stagehands had to pick them out by hand before it was safe for the dancers to continue. Damaged floor areas can make turns, takeoffs and landings unpredictable, putting dancers at risk for injury.
STLE member Christelle Chretien, global lubricant R&D and lab manager, Syensqo (formerly part of Solvay group), works on lubricant development for a living and practices ballet for pleasure. Dance floor manufacturers recommend steady temperatures and low to medium levels of humidity for maintaining consistent characteristics, but that’s not always possible, she says. There is a noticeable difference in the friction of a dance floor between winter and summer, especially during humid East Coast summers, she explains. “It’s not a permanent decomposition of the material of the floor because when the winter comes back, the friction coefficient of the floor comes back as well.” However, temperature and humidity degrade polymer materials, “so this is something to investigate.”
A growing interest in a scientific approach
The tribology testing Chretien does in her lubricant work started her thinking about the turns, slides and other dance moves she performs and how flooring characteristics influence these moves. For example, when she begins a turn, she needs a certain amount of friction to push off (a high static friction coefficient), less friction during the turn (a low dynamic friction coefficient) and more friction again as she finishes the turn. However, when she searched for specific information on the friction characteristics of various flooring materials, she experienced the same difficulty that Clifton did. The flooring manufacturers she spoke with mentioned that they do research on improving their products, but to her knowledge, they aren’t publishing any of this information in the form of patents or articles.
Designing a floor with the optimal friction coefficient depends on the characteristics of the flooring material. It also depends on the force applied, which depends on the size, athleticism and even the gender of the dancers, as well as the type of motion involved. Dancers who perform two turns in a row indoors might substitute a single turn when they perform outdoors on a floor that has become sticky from high humidity to avoid sliding or falling. “They have to apply more force to be able to turn,” Chretien says, adding that a stickier floor might give a dancer more power to begin a jump, but when they come back down, they need small amount of slide to cushion the impact. The dancer’s foot comes down first, and the force is transferred to their ankle and knee. “If your foot is sliding a little bit, everything is sliding together, and you can absorb the energy from the jump and have a smooth landing and prevent an injury.”
“The scientific world is very data oriented, very experiments oriented,” Chretien says. Her lubricant work involves designing experiments to measure friction coefficients of well-characterized interfaces, and then improving and optimizing the lubricants. She was surprised not to find more of this type of research for dance surfaces. Academic research has been done on the biomechanics of jumps and the resilience of the flooring, but not the friction involved, she says. Measuring friction coefficients based on the different steps that dancers perform, she says, would help us to understand how we can improve flooring materials that would help dancers perform safely and well outdoors during a humid summer, for example.
Currently ballet production staffers tend to select flooring for their studios and performance venues based on qualitative terms like “smooth” and “quick,” she says. Tribometric and profilometric benchtop devices are available on the market, with instructions on how to use them to map and monitor wear patterns and rates for flooring samples.11,12 These have been used mainly for general-use floors, however, with an eye toward preventing slips and falls and determining recommended replacement intervals for specific flooring products.
Aside from one book in the Performing Arts Library in New York City, Chretien has found very little information on standardized test methods for dance floors. One of her industry contacts mentioned that his company’s technical center does testing but provided no details. Unlike mechanical systems, it’s very difficult to hold some parameters constant for testing a limited number of variables in isolation. The floors, shoes, dancers, choreography and ambient conditions all vary and interact in complex ways. Testing standards are currently under development, however. One standard builds on DIN 18032, a set of test methods designed for sports flooring that measures such things as shock absorption and vertical and areal deflection. This adapted standard features test criteria specifically designed for dance floors. Another standard adapts tests specified in the EN14904 standard, which is used to evaluate indoor multi-use sports floors.13
A dancer might say, “Why would I even need to know what the coefficient of friction is? I just step on the floor, and I figure out what I need to do.” However, Clifton says, “the dance community now is actually very excited about the science, the sports medicine. It’s just that we’re a little bit behind some of the other areas because of that historical resistance. I talk to young dancers who are great at math and science and are excited about being physical therapists or really incorporating some of this. So, I’d say that resistance is a more historical perspective. And it feels like the dance world is really ready to incorporate some of this different type of quantified insight.”
REFERENCES
1.
Clifton, G. (Fall 2009), “The coefficient of friction of the pointe shoe and implications for current manufacturing processes,” Senior Seminar in Dance, Barnard College. Available
here.
2.
Helen the Hare. (November 20, 2022), “The physics of ballet.” Available
here.
3.
Hackney, J. M., et al. (Feb. 25, 2023), “Reduced stiffness dance flooring increases ankle plantar flexor muscle activation during a ballet jump,” American Physical Therapy Association Combined Sections Meeting. Available
here.
4.
Hopper, L. S., et al. (June 2011), “Dancer perceptions of quantified dance surface mechanical properties,” Proceedings of the Institution of Mechanical Engineers Part P Journal of Sports Engineering and Technology, DOI: 10.1177/1754337111399833.
5.
“The impact of flooring on dance injuries,” The Ballet Blog. Available
here
6.
Swartz, R. (July 18, 2018), “The floor that goes bump in the night.” Dance Teacher.” Available
here.
7.
Dev2023. (April 15, 2022), “How to determine the best floor for the way you dance.” Available
here.
8.
“Da Rookies Nutcracker: Classic meets breakdance,” Harlequin Case Study, 2022. Available
here.
9.
Pope, A. (June 12, 2024), “The physics of breakdancing, a new Olympic sport,” The Conversation. Available
here.
10.
Spivack, E. (July 18, 2024), “How Olympic breakers exploit physics for gold,” Inverse. Available
here.
11.
Liu, F. “Progressive wear mapping of flooring using tribometer with integrated profilometer.” Available
here.
12.
“Floor testing science (tribology).” Available
here.
13.
“Specifying dance floors,” Harlequin white paper summary. Available
here.