Meet the Presenter
This article is based on a webinar presented by STLE Education on April 6, 2023. The Promising Progress of 2D Materials as Solid Lubricants is available at www.stle.org: $39 for STLE members, $59 for all others.
STLE member Dr. Anirudha Sumant leads the Nanofabrication and Devices Group at the Center for Nanoscale Materials, Argonne National Laboratory, where he is a materials scientist. His pioneering research focuses on nanocarbon materials, including chemical vapor deposition (CVD)-diamond, carbon nanotubes, graphene and other 2D materials. Dr. Sumant’s expertise spans the electronic, mechanical and tribological properties of these materials, as well as surface chemistry and micro-nano fabrication.
He has authored and co-authored over 170 peer-reviewed journal articles and proceedings, contributed to two book chapters and holds 39 granted U.S. patents. Notably, his groundbreaking work in demonstrating superlubricity (near-zero friction) at an engineering scale has revolutionized solid lubrication technology.
Dr. Sumant has received numerous prestigious awards, including four R&D 100 Awards, the NASA Tech Brief Magazine Award, three TechConnect National Innovation Awards, the Pinnacle of Education Award at Argonne National Laboratory and the Argonne Excellence in Commercialization Award. He is a member of the Materials Research Society (MRS), STLE and the American Vacuum Society (AVS), and serves on the editorial advisory board for Applied Physics Letters and as the chief editor of the journal Frontiers in Carbon.
You can reach him at sumant@anl.gov.
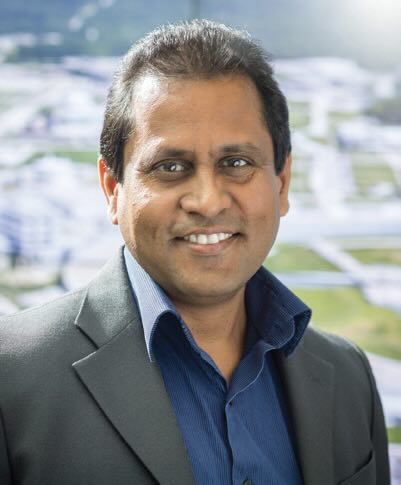
Dr. Anirudha Sumant
KEY CONCEPTS
•
Traditionally thin film-based solid lubricants including oxide films or diamond-like carbon coatings have been in use for conventional mechanical systems; however, recent advances in developing solid lubricants based on two-dimensional (2D) materials such as graphene and MoS
2 and their exceptional tribological performance are getting significant attention due to their unique structural, mechanical and chemical properties.
•
These 2D materials can be combined with other 2D materials to create hybrid lubricants that can enhance their chemical stability and ability to work in harsh environment conditions.
•
These solid lubricants could be deposited using a spray coating process in ambient conditions making them more cost effective and scalable than traditional thin films coatings that are mostly based on either chemical vapor or physical vapor deposition methods, which requires vacuum environment.
•
These solid lubricants could be tailored to work effectively in certain industrially demanding applications such as hot metal stamping in the automotive industry.
While oil and grease-based lubricants are used for standard mechanical systems such as automotive engine parts, gears and bearings, solid lubricants have been reserved for unusual or extreme applications related to areas such as very cold or high temperatures, and vacuum and radiation-prone environments.
However, recently, the objectives of improving energy efficiency of moving mechanical systems and reducing the carbon footprint have opened additional pathways for solid lubricants in conventional mechanical applications such as bearings, gears and camshafts. Since graphene is five times more slick than other dry lubricants, it dramatically minimizes wear and tear on parts—thus extending the lifespan. All of this has the potential to substantially reduce oil consumption and the carbon footprint with an estimated energy savings of 16% in the short term and 35% in the long term.1
This article is based on an STLE webinar presented by STLE member Dr. Anirudha Sumant, who leads the Nanofabrication and Devices Group at the Center for Nanoscale Materials, Argonne National Laboratory, titled The Promising Progress of 2D Materials as Solid Lubricants. See Meet the Presenter for more information.
Why graphene?2
Graphene is a two-dimensional (2D) material with distinctive friction and wear properties that are not typically observed in conventional materials. In addition to its mechanical, optical, thermal and electrical traits, graphene can function as either a solid or colloidal liquid lubricant. The simple shear capacity, extreme strength and chemical inertness are its most sought-after attributes. These properties are due to its densely packed and atomically flawless surface. In addition, because of its ultra-thinness, it can be employed in nanoscale or microscale systems, including microelectromechanical systems (MEMS) and nanoelectromechanical systems (NEMS), with oscillating, rotating and sliding contacts.
Material wear is prevented by the exceptional mechanical resilience of graphene, which is one of the strongest materials ever measured. In addition, it was recently demonstrated that the overall strength of graphene is not influenced by grain boundaries, despite the fact that the mechanical properties of graphene are significantly influenced by the introduction of other types of defects, such as oxidation, which results in a decrease in its strength and rigidity. Tribologically speaking, such extreme mechanical strength is very favorable for wear protection.
Graphene is impermeable to liquids and gases, including water and oxygen. Consequently, the corrosive and oxidative processes that typically cause the most damage to contacting surfaces are slowed down. Additionally, it has been demonstrated that liquid water reduces friction on graphene, thereby potentially mitigating the impact of capillary forces that are characteristic of humid environments. All in all, graphene is highly appealing for demanding tribological applications (see Figure 1) that require low friction and low wear regimens due to the previously mentioned properties.
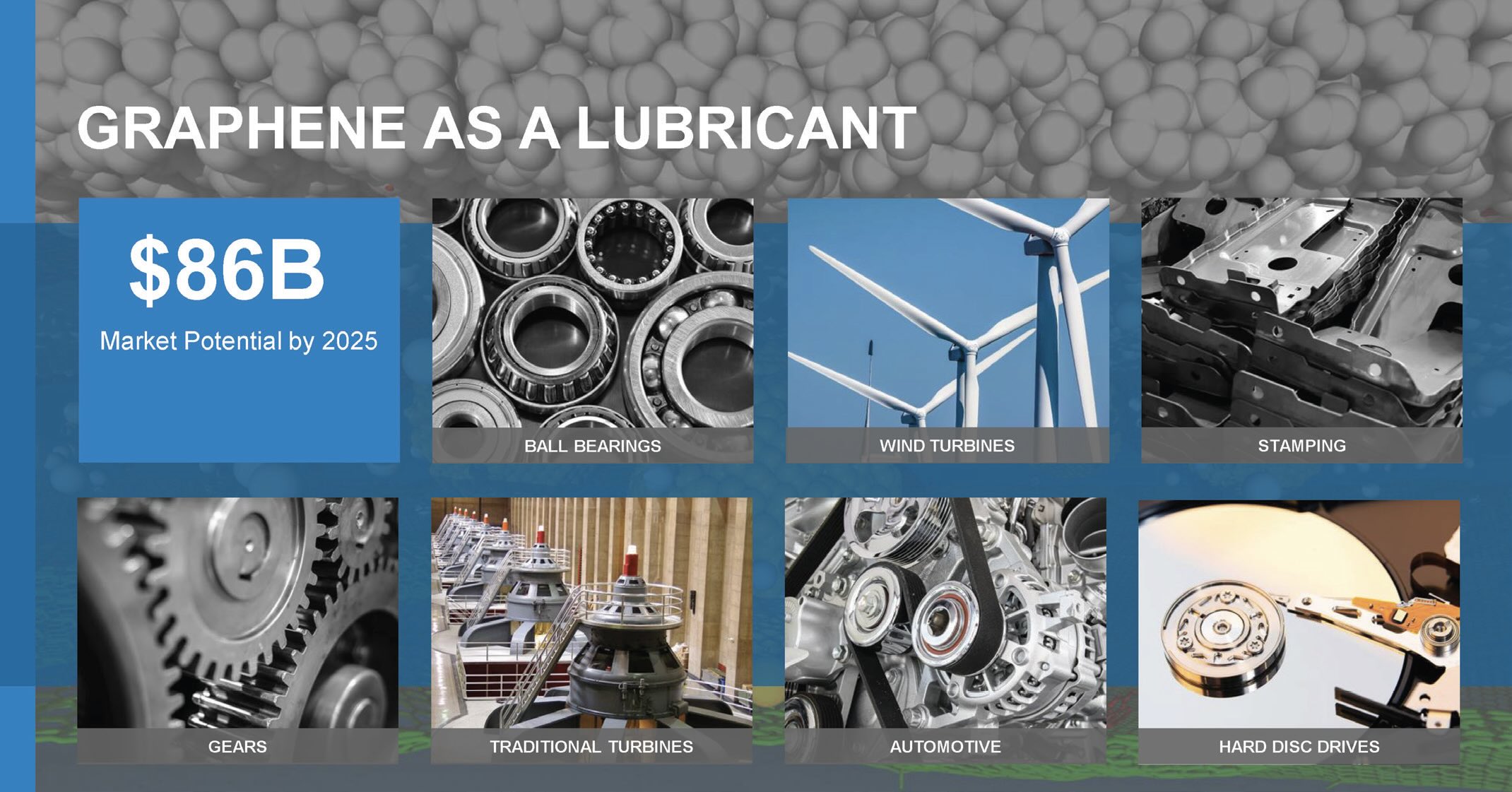
Figure 1. The projected market for graphene.
Properties of graphene as a solid lubricant
Dr. Sumant’s group at Argonne National Laboratory reported one of the first macroscale tribological studies on graphene demonstrating the unusual friction and wear properties of a few graphene layers on steel surfaces.
3 Specifically, a small amount of solution-processed graphene (SPG) was deposited from a low concentration ethanol solution (1 mg/L) with only partial coverage of the steel surface (approximately 25% of the total surface area).
This partial coverage was sufficient to reduce both friction and wear in dry nitrogen and humid air environments. In these environments, the few layers of graphene demonstrated stable low friction (coefficient of friction equal to 0.15 when compared with a value of approximately 1.0 for bare steel) and a four orders of magnitude reduction in wear in comparison to bare steel.
Even in dry nitrogen, the coefficient of friction of the graphene layer derived from the ethanol solution is comparable to that of highly oriented pyrolytic graphite (HOPG) in humid environments. Tests performed in humid air required replenishing the graphene layer in the wear track for a stable low friction and low wear regime. The result clearly demonstrated the wear protection qualities of graphene layers, especially when SPG is periodically fed to the sliding interfaces.
It’s worth mentioning that for both dry nitrogen and humid air, as long as graphene is present at the sliding steel interfaces, the friction is reduced by five to six times and wear by four orders of magnitude for more than 15,000 wear cycles. Graphene not only protects against corrosion and oxidation but also shears readily at the sliding contact interfaces, which can help reduce friction and wear. However, tribotests as a function of increasing load show that the lifetime of the graphene protective layer is shorter under higher loads.
MoS2-GO as a solid lubricant
While graphene offers low friction and wear at moderate contact pressures and sliding velocities, it begins to degrade under high contact pressures (~1 GPa) due to oxidation induced defect propagation. Therefore, it is crucial to enhance its mechanical and chemical properties by integrating it with other 2D materials. Dr. Sumant’s lab has developed a novel process for spray coating a composite material made of molybdenum disulfide (MoS₂) and graphene oxide (GO), forming the MoS₂-GO composite.
4 Molybdenum disulfide, a well-known solid lubricant, possesses a layered structure that enables easy sliding between layers, significantly reducing friction. GO, derived from graphene, enhances the properties of MoS₂ by encapsulating it, thereby protecting it from oxidation. This encapsulation not only enhances the chemical stability of MoS₂ but also provides additional lubrication, mechanical strength and thermal stability. This is particularly promising for harsh environment conditions as it leverages strengths of both materials and offers an excellent alternative as a solid lubricant for advanced industrial applications.
The water-based MoS2-GO lubricant is an innovative, oil-free solution designed for high-temperature applications, offering environmental benefits and eliminating oil-related hazards. It leverages a robust spray coating process that ensures a highly uniform surface finish.
Macroscale tribotesting has shown exceptionally low friction values at both 22°C and 100°C under ambient conditions. It demonstrates superlubricity at elevated temperatures of 200°C, 300°C and 400°C, even under high contact pressures, while maintaining excellent coating integrity (see Figure 2). Additionally, when compared with bare steel-on-steel surfaces, it significantly reduces wear volume loss, making it a superior choice for demanding industrial environments.5
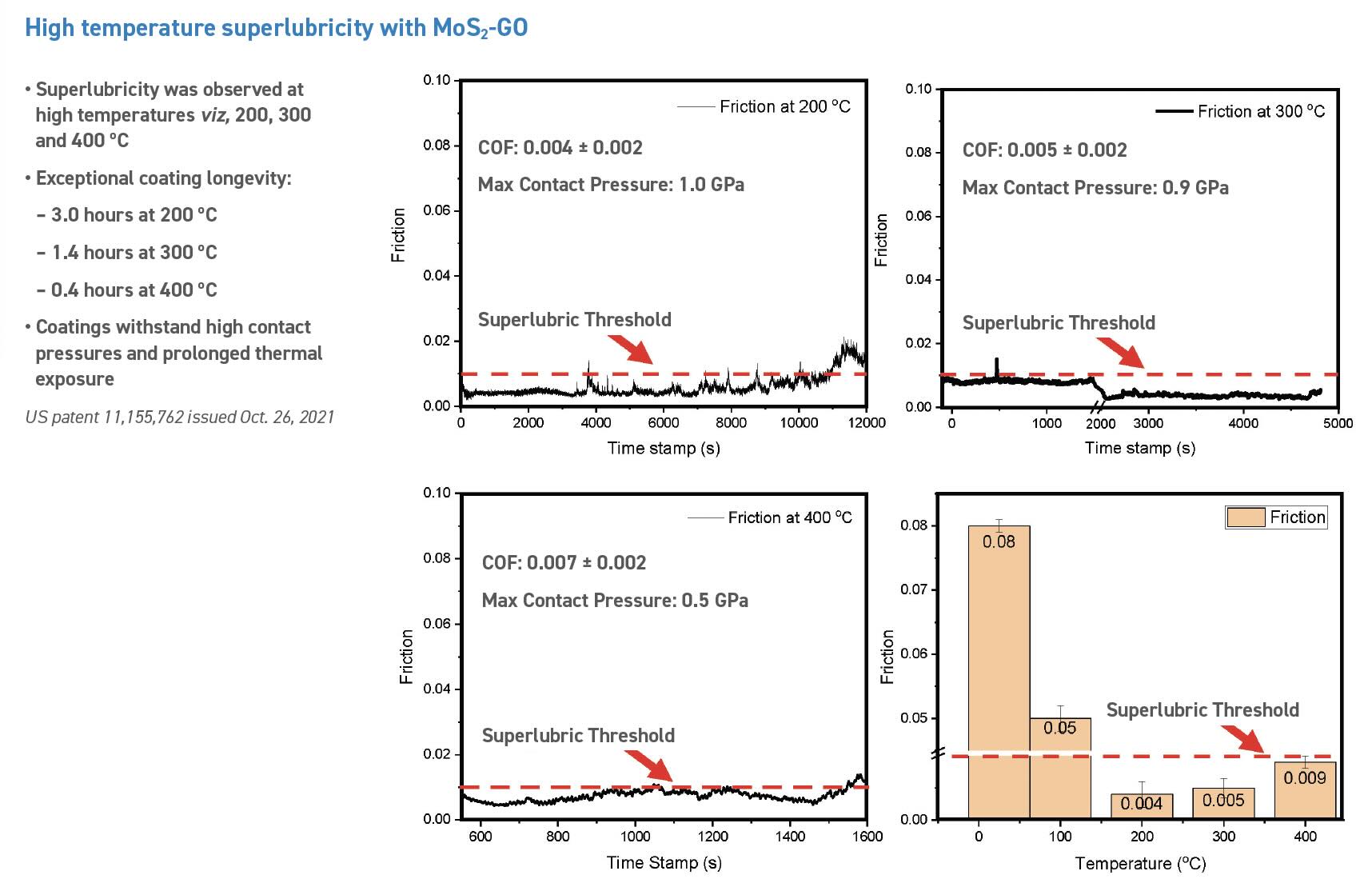
Figure 2. High temperature superlubricity properties of 2D materials-based composite. Figure courtesy of Sumant et al., US patent 11,155,762, issued Oct. 26, 2021.
A summary of the benefits of MoS2-GO on rough steel surfaces includes:
•
It can be easily applied through spray coating, making it a commercially viable technology due to its low cost (~$1/g).
•
It demonstrates superior lubrication performance, achieving 44 km linear sliding without wear on the disc.
•
The lubrication mechanism involving layer-level encapsulation of MoS
2 and GO enhances durability
(see Figure 3).
•
It exhibits lower friction and wear rates across a variety of environments, functioning like a crystalline oil.
Figure 3. Tribolayer formation and wear protection by 2D materials-based composite. Figure courtesy of Sumant et al., US patent 11,155,762, issued Oct. 26, 2021.
Metal stamping applications
Solid lubricants have the potential to be especially valuable for the automotive industry, which can be tailored to accommodate the extremely high temperature range (although for a short time period) required for hot metal stamping applications. Today, more than 44% of automobile parts are hot stamped, accounting for more than 450 million individual pieces per year
(see Figure 4). Stamped components are typically formed at room temperature using water- and oil-based forming lubricants, which reduce the coefficient of friction between the metal blank and the stamping die surface, thereby enhancing formability. These lubricants are effective up to temperatures between 120°C and 250°C.
Figure 4. Graphene-based lubricant applied to hot stamping process.
However, advancements in the metalforming industry have introduced elevated temperature processes, requiring higher use temperatures of 250°C to 500°C for aluminum alloys and up to 900°C for steel hot stamping alloys. While boron nitride lubricants are commonly used in hot stamping operations, they are expensive and incompatible with downstream painting operations, necessitating chemical removal before body shop use.
Because of this, the development of high-temperature lubricants for stamping applications is a pressing necessity. These oil-free solid lubricants also have the benefit of the elimination of post-op cleaning procedures. Dr. Sumant’s group collaborated with a metalforming company, under the Department of Energy Office of Energy Efficiency & Renewable Energy (DOE-EERE) funded Technology Commercialization Grant, to develop advanced graphene-based solid lubricants that solve this problem.
This graphene-based lubricant can be applied to the surface of dies or molds, eliminating the material and processing costs associated with traditional forming lubricants and their removal. Additionally, the graphene lubricant significantly reduces the coefficient of friction and adhesion energy between the die surface and substrate. This reduction in friction enables cost-effective, high-volume production of lightweight, energy-absorbing materials with fewer defects. The enhanced thermal conductivity of graphene also improves heat dissipation, facilitating uniform temperature distribution, minimizing hot spots and ultimately improving the overall yield in the metalforming process.
Key benefits of these lubricants include:
•
State-of-the-art metalforming. These graphene-based lubricants set a new standard in
high-temperature metalforming, offering outstanding performance.
•
Elimination of hazardous processes. These lubricants do not require expensive and dangerous acid-based etching to remove the graphene coating.
•
Effortless cleanup. The lubricants can be easily removed from metal sheets after stamping using a simple pressure water jet, significantly reducing cleanup costs and facilitating downstream coating operations.
•
Proven efficiency. Real-world tests at the metalforming collaborator’s factory showed a 29%-46% improvement in metal thinning and a fourfold improvement in consistency between parts when compared with using no lubricant
(see Real-World Applications). This has the potential for fewer rejected parts, increased productivity and enhanced safety, while also reducing vehicle production costs.
•
Environmental benefits. These lubricants support the cost-effective lightweighting of passenger vehicles and light trucks, leading to better fuel economy and lower emissions with no damage to the environment.
Real-world applications
The applications for 2D materials-based solid lubricants are continuously increasing; potential applications include:
•
Ball bearings
•
Wind turbines
•
Traditional turbines
•
Gears
•
Stamping
•
Hard disc drives
•
Automotive
How 2D lubricants are changing the lubricant industry
SPG and other nanoscale 2D materials show significant potential as solid lubricants in various tribological applications. They have demonstrated super low friction and wear under high contact pressure across diverse environments and over extended periods, indicating their realistic use in various tribosystems.
The work done at Argonne National Laboratory on graphene-based solid lubricants is paving the way for designing oil-free, smart frictionless tribological systems in a range of industrial applications.
REFERENCES
1. Mutyala, K.C., Wu, Y.A., Erdemir, A. and Sumant, A.V. (2019), “Graphene - MoS2 ensembles to reduce friction and wear in DLC-steel contacts,” Carbon, 146, pp. 524-527, ISSN: 0008-6223, https://doi.org/10.1016/j.carbon.2019.02.047.
2. Berman, D., Erdemir, A., Sumant, A.V. (January/February 2014), “Graphene: a new emerging lubricant,” Materials Today, 17 (1), pp. 31-42.
3. Berman, D., Erdemir, A. and Sumant, A. V. (2013), “Few layer graphene to reduce wear and friction on sliding steel surfaces,” Carbon, 54, pp. 454-459.
4. Ayyagari, A.V., Mutyala, K.C., Sumant, A.V. (2020), "Towards developing robust solid lubricant operable in multifarious environments," Scientific Reports, 10 (1), 15390, https://doi.org/10.1038/s41598-020-72666-4.
5. U.S. Patent 11,440,049 B2, Sept. 13, 2022, and U.S. Patent application No. 17/351,817, Aug. 31, 2023.
Jeanna Van Rensselar heads her own communication/public relations firm, Smart PR Communications, in Naperville, Ill. You can reach her at jeanna@smartprcommunications.com.