Perfluoro and polyalkylfluoro substances (PFAS) are one of the top chemicals under scrutiny due to their health and environmental concerns. Regulatory agencies globally, such as ECHA and US EPA, have initiated regulatory programs to limit the use of these substances. The upcoming PFAS regulations may limit the use of fluorosilicone based antifoams causing lubricant formulators to explore alternate chemistries. This has become an important topic for non-aqueous Electric Vehicles (EV) driveline fluids as fluorosilicone based antifoams consistently provide effective foam control under high stress conditions. This paper will review a comprehensive study showing the efficient foam control performance of
FOAM BAN® 204 compared to a fluorosilicone antifoam in EV driveline fluids based on different base oils groups.
Foaming in EV Driveline Fluids
Electric Vehicle (EV) driveline fluids are required to provide multiple properties such as materials compatibility, thermal stability, electrical properties, and high efficiency. Due to these high demands, the industry is shifting towards using group III+, IV, and V synthetic base oils for EV driveline fluids. However, excessive entrained air and foaming have become a crucial issue for new EV driveline fluids which are the results of high rotational speeds and cycle counts in EV motors. Extreme entrained air and foam volumes can increase the volume of driveline fluids which can lead to vent expulsions and contribute to poor lubricity, low heat transfer, lower flash points, and higher rates of oxidation of these driveline fluids.
A fluids optimal performance is dependent on the amount of foam and entrained air present during the end application. For a fluid to perform well, low foam tendency is required, meaning entrained air must rise quickly to the surface and the foam bubbles must then burst instantaneously. Foam destabilization is caused by drainage of the liquid from the foam lamella leading to thinning which then allows the foam bubble to rupture as shown in Figure 1.
Figure 1 - Drainage of Liquid from Foam Lamella
There are certain components present in EV driveline fluids, such as dispersants, detergents, and viscosity modifiers, that can form elastic networks within the foam lamella (Figure 2). These elastic networks tend to increase the viscosity of the liquid in the lamella and reduce liquid drainage resulting in foam stabilization. Also, contamination, such as small amounts of water, metal fines, or soot buildup in the EV driveline fluids can stabilize the foam generation. Another factor of foam stabilization is the Solutocapillary Marangoni Flow as shown in Figure 3. This phenomenon occurs due to evaporation of materials from the fluid surface leading to a higher surface tension in the foam lamella. This causes the lower surface tension fluid in the bulk to flow towards the lamella to minimize the surface tension gradient and thus slowing the ability for the fluid to drain.
Figure 2 - Foam Stabilization - High Molecular Weight Precipitates and Add Packs Components
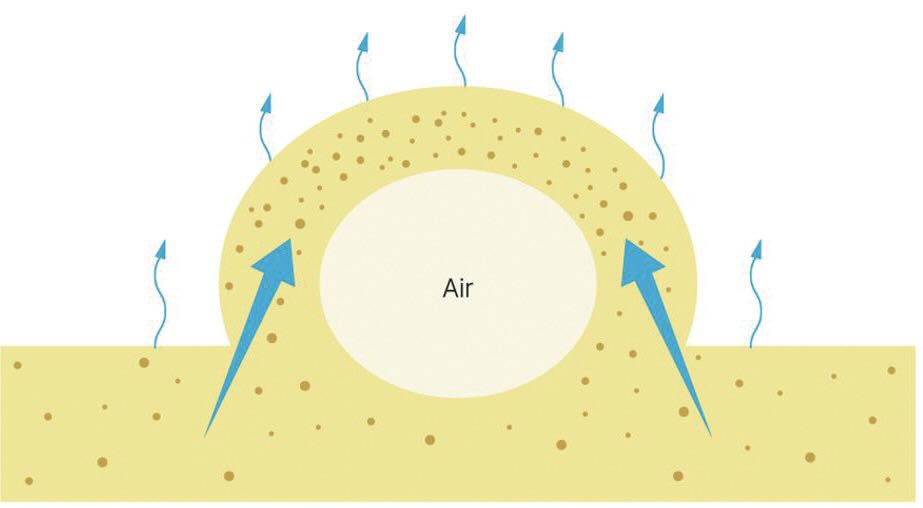
Figure 3 - Foam Stabilization - Marangoni Flow
Antifoams are used to help mitigate the foam in non-aqueous lubricants. The antifoam droplet will enter into the air interface of the lamella and begin to spread in order to maximize the surface area of the antifoam-air interface. This occurs due to the antifoam droplet having a lower surface tension than the fluid, therefore, the antifoam-air interface will have lower interfacial energy than the antifoam-liquid interface. As shown in Figure 4, the antifoam droplet spreads, it will eventually bridge and then rupture the foam bubble.
Figure 4 - Antifoam Mode of Action in Non-Aqueous Fluids
Test Methods for Foam and Air Entrainment
To understand the foam profile of new EV driveline fluids, identifying a test method that can simulate the real-world operating conditions was extremely important. The current test methods available in the industry to evaluate foam and entrained air profile are not effective for EV driveline fluids as these test methods do not show the foam issues that are observed during application.
MÜNZING has developed a new in-house technique known as the “High Shear-Air-Sparge Test” as shown in Figure 5. This test exposes the EV driveline fluid to a combination of high shear and air sparging simultaneously at elevated temperatures. A high-speed benchtop rotor stator is used for shearing. Once the test is stopped, the increase in foam volume and entrained air are recorded. To stress the fluid further, High Stress Cycle testing is conducted, in which the same fluid is tested multiple times to evaluate long term persistence. A schematic of the High Stress Cycle Testing is shown in Figure 6.
Figure 5 - MÜNZING's High Shear - Air Sparge Test
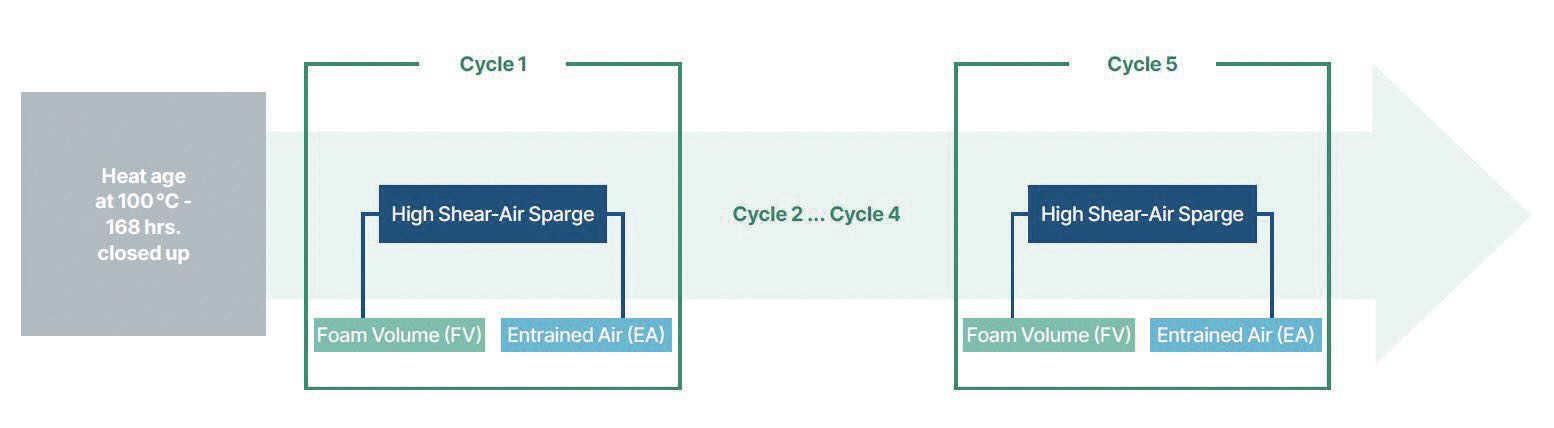
Figure 6 - MÜNZING's High Shear - Air Sparge Test - High Stress Cycle Testing
Fluorosilicone Based Antifoam for EV Driveline Fluids
Upon evaluating different finished driveline fluids using several synthetic base oil groups, it was observed that fluorosilicone chemistry-based antifoams provide improved foam control and entrained air as compared to the traditional silicone-based antifoam chemistry. But as previously discussed, the industry may limit the use of fluorosilicone due to the upcoming PFAS regulations, so a suitable replacement antifoam is of high interest.
Based on decades long experience with non-aqueous lubricants and antifoams, MÜNZING has introduced a new polyacrylate based antifoam,
FOAM BAN® 204, to the EV driveline fluid industry. This antifoam can be used an alternate to fluorosilicone in different types of EV driveline fluids based on different base oils.
Performance Study
MÜNZING evaluated different antifoam chemistries such as silicone, fluorosilicone, organo-modified siloxane, and polyacrylate in multiple EV driveline fluids in a thorough study where fluids were tested using traditional ASTM D892 and ASTM D6082 test methods first and then evaluated in MÜNZING’s new High Shear-Air Sparge test method.
The first fluid evaluated is a low viscosity Group III+ EV transmission fluid. As shown in Figure 7, when the finished fluid is tested in ASTM D892 and ASTM D6082, the blank (no antifoam) does not show significant foam tendency. Fluorosilicone based antifoam causes an increase in foam volume in sequence I and sequence III, whereas
FOAM BAN® 204 provides good foam control in all four sequences as compared to blank (no antifoam) and fluorosilicone based antifoam. This fluid is then tested in MÜNZING’s High Shear-Air Sparge test, and the blank (no antifoam) shows higher foam volume and entrained air as compared to when it is tested in ASTM D892 and ASTM D6082.
FOAM BAN® 204 provides good foam control, lower entrained air, less total volume with higher liquid levels, and faster knockdown times as compared to the fluorosilicone based antifoam.
Figure 7 - Evaluation of Antifoam Performance in Group III+ EV Transmission Fluid
The second fluid that is evaluated is a low viscosity Group IV (PAO) EV gear oil. When this fluid is tested in ASTM D892 and ASTM D6082, no significant foam volume is generated in all four sequences, as shown in Figure 8. Once this fluid is tested in MÜNZING’s High Shear-Air Sparge test, the blank (no antifoam) exhibits higher foam volume, entrained air and lower liquid levels.
FOAM BAN® 204 outperforms the fluorosilicone antifoam by providing lower total volume, foam volume, entrained air and higher liquid levels, indicating better performance.
Figure 8 - Evaluation of Antifoam Performance in Group IV (PAO) EV Gear Oil
The third fluid that is assessed is another low viscosity EV driveline fluid based on a combination of 80% Group IV (PAO) and 20% Group V (Ester) base oil. As shown in Figure 9, when this fluid is tested using ASTM D892 and ASTM D6082, no significant foam volume is generated in all four sequences. However, when it is tested in MÜNZING’s High Shear-Air Sparge test, the blank (no antifoam) sample produces higher foam volume, entrained air and lower liquid levels.
FOAM BAN® 204 performs similar to fluorosilicone based antifoam by exhibiting higher liquid level, less foam volume and entrained air as compared to the blank (no antifoam).
Figure 9 - Evaluation of Antifoam Performance in 80% Group IV (PAO) and 20% Group V (Ester) EV Transmission Fluid
Conclusion
As discussed, due to upcoming PFAS regulations, the need for alternate antifoam chemistries has become more apparent and important. Based on the data collected during evaluations of new low viscosity EV driveline fluids, it is observed that
FOAM BAN® 204 provided similar or improved foam control and entrained air profile when compared to fluorosilicone in ASTM D892, ASTM D6082 and MÜNZING’s High Shear-Air Sparge test. Although fluorosilicone antifoams provide excellent performance in EV driveline fluids, there are alternate antifoam chemistries available in the industry that can potentially replace fluorosilicone based antifoams.