Wire rope
By Dan Holdmeyer, Contributing Editor | TLT Lubrication Fundamentals November 2024
Lubrication is a major component of the cables we use every day.
Wire rope, or cable, of various forms is all around us. Every day we use these cables without much thought. Cables attached to the garage door and springs under tension help lift the door. Cables on multi-speed bicycles enable shifting gears. Wire rope is often hidden as in the parking brake activated by a cable between the foot pedal and the rear brakes. Some elevators are lifted and lowered via wire rope. Guy wires hold cell phone transmitter towers vertical. Suspension bridges are often artistically, besides structurally and strategically, arranged to suspend a roadway over a ravine or river. Even concrete beams may be strengthened via a tension cable in a sheath within the concrete to give it compression and thus more strength. Some of you also may be familiar with those large cables on ski chair lift systems. These are just a few examples of the myriad of wire rope applications requiring unique construction.
Wire rope general classifications identify the number of strands and a nominal number of wires in the strands. Classification provides weight and strength ratings so price comparisons can be made amongst various cables within the classification. However, these general classifications may not reflect the actual construction of the strands.
Wire rope is more complex than a set of wires twisted together to add strength to the cable greater than that of a single strand of wire. Cables have various numbers of strands placed in an orderly manner spiraled around a central core. The core helps to maintain the strand positions of the cable under the stresses of loading and bending. Cores are made of various materials such as fibers (natural or synthetic) and steel. Each strand is a set of two or more wires specifically arranged to form the strand (see Figure 1). Using small diameter wires makes the strand more flexible and larger diameter wires provide greater strength but also offer more resistance to abrasion.
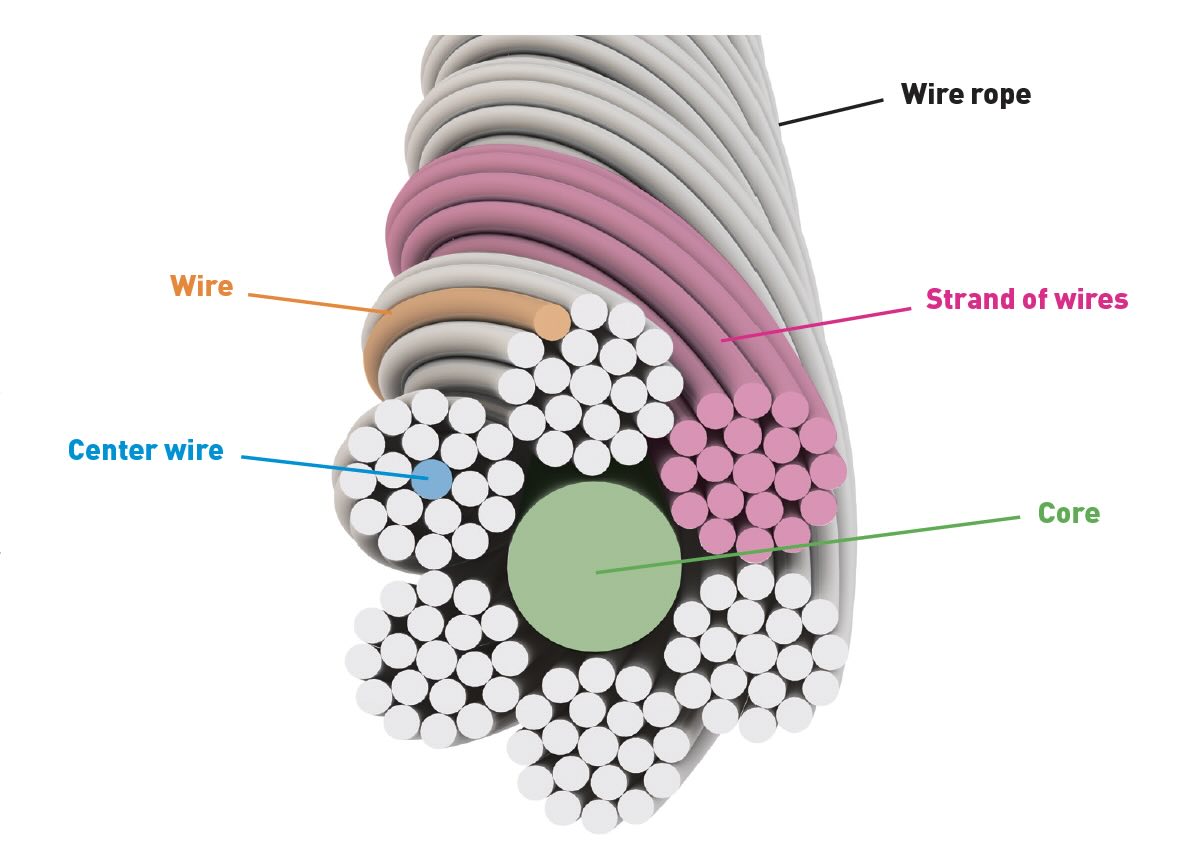
Figure 1. Components of wire rope.
Some cables are made of more than one size wire creating internal clearances to allow movement and lubrication of the strands and wire when the cable is stretched under load or bent around a pulley or drum. Some of the strand patterns are Single Layer, Filler Wire, Seale, Warrington and combinations of these. The Single Layer is the simplest with seven strands, six strands spiraling around a single strand. Other patterns may use smaller diameter strands amongst larger strands to fill in valleys between strands, providing strength and crush resistance. Generally, larger diameter strands are used on the outer layer to provide greater surface contact and fatigue resistance.
The direction the strands are laid around the core also is varied to give unique performance advantages. For example, Figure 2 shows a “Regular Lay” where the lay direction of the wire is opposite of the strand lay. “Lang Lay” wires and strands spiral around the core in the same direction. Lang Lay wire ropes resist fatigue and abrasive wear better than Regular Lay. Regular Lay, however, provides resistance to crushing, and the natural rotation tendencies of Lang Lay ropes. Regular Lay wire ropes spool around a drum better than Lang Lay.
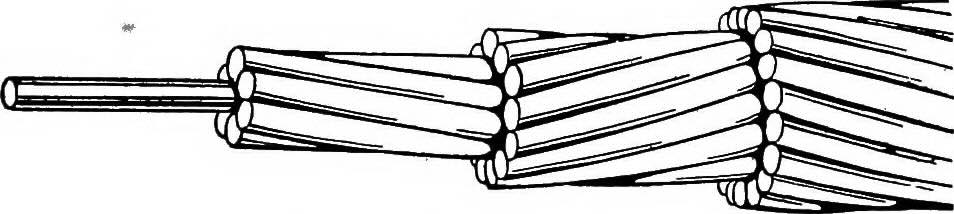
Figure 2. Regular Lay wire rope. Figure courtesy of Internet Archive Book Images, Wright, R. V. (ed.), Little, J. G. (joint ed.) and Augur, R. C. (joint ed.) (1921), Material handling cyclopedia; a reference book covering definitions, descriptions, illustrations and methods of use of material handling machines employed in industry, New York, N.Y., Simmons-Boardman Publishing Co.
Special care must be taken with wire rope spooling and unwinding from drums to lay the cable on the drum in an orderly fashion, so the cable fits for one thing, but it also reduces kinks and abrasive wear of the cable. Figure 3 shows a drum with a guide pulley on a block that traverses back and forth across the drum laying the cable evenly distributed on the drum.
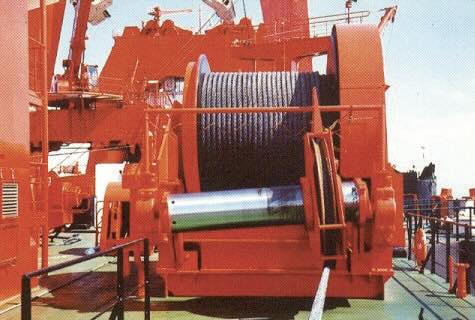
Figure 3. Guided cable winder to drum. Figure courtesy of Alfons Kifmann, CC BY-SA 3.0 DE, via Wikimedia Commons.
The “drum,” sometimes referred to as a “spool” or “windup spool,” can be smooth or grooved. Grooved drums are recommended when more than one layer of cable is wound up on the drum to set the first layer of cable on the drum. Additional hardware used with wire rope are “pulleys” that simply redirect the cable direction and force. A “block” holds the pulley shaft, or “pin,” in bearings and can be stationary or movable. The block may hold more than one pulley. A common set of blocks is the “block and tackle” in Figure 4 with a fiber versus wire rope. Another term used for pulley is “sheave,” sometimes pronounced like “shiv,” versus “sheev,” when working with wire rope depending on the region of the country.
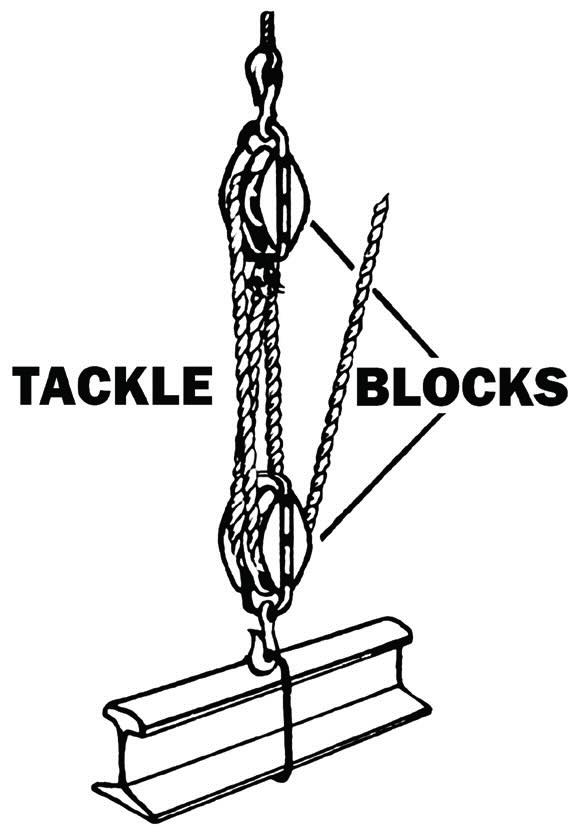
Figure 4. Block and tackle. Figure courtesy of Pearson Scott Foresman, Public Domain.
The bearings of the pulleys are often lubricated for life except in large wire rope systems such as elevators, which may require an NLGI Grade 2 grease with an ISO Viscosity Grade 150, 220 or 320 oil. The drive mechanism for a wire rope system that moves or lifts a load is usually a gearbox driven by an engine or electric motor. Figure 5 shows an electric motor under the gear box driving the wheel to lift the chairs up the ski mountain. The ski chair lift also will have a large tension pulley mounted on a sliding platform heavily weighted to keep the cable taut with and without loaded chairs. The slides on the platform will require lubrication.
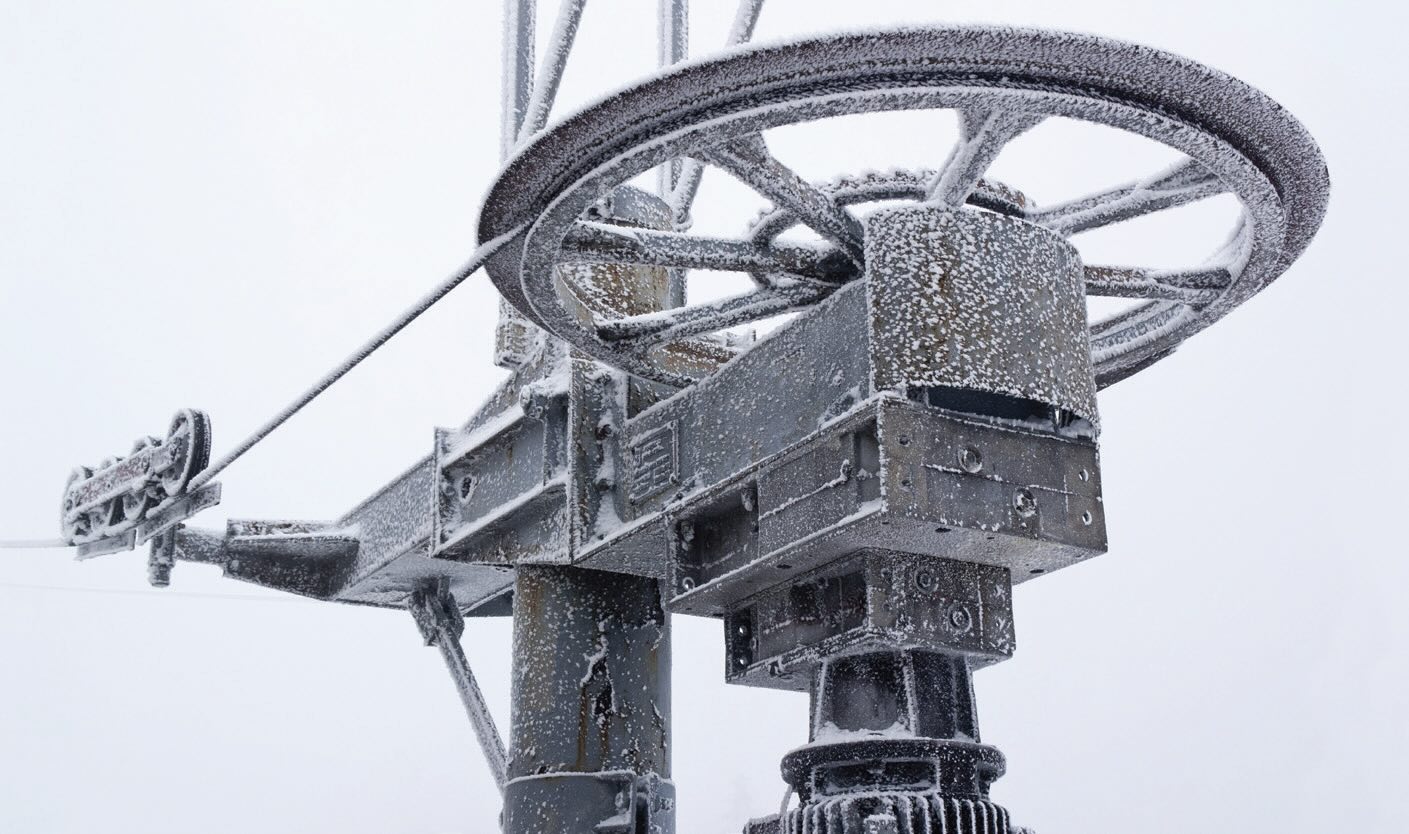
Figure 5. Ski chair lift drive.
The wire rope also needs lubrication. The heavy-duty industrial wire ropes in fact need regular relubrication. Lubricant is the fourth major component of a wire rope. The other three are the core, the wires that make up the strands and the strands.
Even the smallest wire ropes need to be lubricated, and lubricant applied during cable manufacturing may be sufficient for its life. The lubricant may be a solid lubricant, such as a fine coating or a modified metal layer on the surface of each wire. Or it may be a polymer or oily substance.
The lubricant reduces the friction between the wires and the strands as they rub and slide over each other when the wire rope flexes under load or when the cable bends around a sheave or a drum. The surface interactions of these wires and strands are like sliding cam followers on engine cam lobes, except slower. Therefore, the lubricant must provide anti-scuff (extreme pressure) protection, just like it would on engine cam lobes or heavily loaded gear teeth. Even the guy wires holding radio towers vertical flex enough to cause sliding between the wires to require wear and anti-scuff protection.
The lubricant also must provide corrosion protection. The aforementioned radio tower guy wire needs corrosion protection due to rainwater contamination. Marine applications may need better or slightly different corrosion protection because sea water tends to be slightly alkaline, definitely more corrosive. Mining wire rope applications are frequently exposed to acidic fumes, which are even more corrosive to most metals.
A plastic sheath (not a sheave, as mentioned previously) around the wire rope is desired in some applications. The plastic sheath may provide the wire rope some external abrasive wear protection, but it primarily protects the cable from corrosive elements in the environment around the cable. One drawback of plastic sheathing is inspection for frayed or damaged wires of the cable is impossible unless the wires have broken through the plastic coating. However, plastic sheathing is ideal for post-tension concrete because the wire rope is encased in the concrete visual inspections are not conducted, and the plastic sheath keeps the alkaline nature of the concrete away from the cable.
At first glance, a good coating of a grease brushed on the wire rope would seem to protect it against abrasive and adhesive wear from the sliding of the wire rope over itself and against the drums, sheaves and other components of wire rope system. However, grease is tacky and does tend to stay in place, but it also collects dust and dirt, which is abrasive to metal surfaces sliding over each other.
Therefore, a lubricant that forms a tough, non-drying, but non-tacky film is needed for the external wire rope lubrication; petrolatum or asphaltic base stocks are common. The lubricant also needs to penetrate to the core of the wire rope because the internal wires and strands need wear and corrosion protection. So, a not-too-viscous oil with anti-scuff or extreme pressure additives is needed, with anti-corrosion additives, as well. Pumpability at very low temperatures is needed particularly in mining and construction operations. The lubricant film must remain flexible at low temperature to avoid chipping and peeling. It also must remain in place and not drip off during high temperature operation.
Relubrication of large industrial wire ropes is best applied by pressurized cable lubrication systems. These systems clean the cable first, removing dirt, debris and old lubricant from the surface and then apply fresh lubricant under pressure to penetrate deep into the cable. Then, as the wire rope flexes, it helps develop the needed oil wedge between moving surfaces, the wires and strands, to draw the lubricant between them deep inside the wire rope. Other lubricant application methods include brushing, spraying or sliding through a lubricant trough.
One last thought: The parking brake cables in many automobiles are small wire ropes encased from the pedal inside the cab to the brake drum. The encasement protects the cable from road salt and water spray. However, if the brake is never used, the cable sits in one position for years. Without movement to draw the initial cable lubricant between the internal cable wires, the wires lose lubricant protection and corrode until one day when the parking brake is eventually used, the cable snaps. If the parking brake is engaged regularly, the parking brake cable would continue to relubricate itself and last a lot longer.
Dan Holdmeyer is retired from Chevron Lubricants and is based in Washington, Mo. You can reach him at dan.holdmeyer@gmail.com.