BYK
BYK Additives for Industrial Lubricants and Greases
By Dr. Maximilian Böhmer, Head of Global End Use Lubricants and Metal Processing at BYK-Chemie GmbH | TLT CMF Plus November 2024
In the world of industrial lubricants, the effective management of foam, the improvement of grease viscosity and the stabilization of solid particles are key challenges. BYK proves to be a reliable supplier, offering a comprehensive range of additive solutions for the lubricant sector. At the forefront of our offerings are silicone and silicone-free defoamers that have been carefully developed to meet the requirements of all API classes. These defoamers are an indispensable ingredient to reduce foaming and ensure optimal performance in various applications. In parallel, BYK presents organoclays tailored to elevate the viscosity and stability of lubricating greases. Moreover, our dispersing additives stabilize solid particles such as graphite, MoS2, PTFE, and an array of other fillers within lubricating oils. From perfect particle dispersion to anti-sedimentation and maintaining viscosity under high loads, our solutions are precisely tailored to the diverse challenges encountered in the lubricants market.
New defoamers for industrial oil-based lubricants
BYK has introduced three specialized defoamers designed for use in industrial oil-based lubricants: a silicone-free variant (BYK-9731), a silicone-based option (BYK-9732), and a hybrid version (BYK-9730). These defoamers address the challenges posed by the presence of numerous surface-active substances, such as dispersants and detergents, which tend to stabilize foam. By targeting and destabilizing the foam at the interface, these defoamers cause the foam bubbles to burst without negatively impacting the lubricating properties of the oil (Figure 1). Developed for a range of systems, BYK's defoamers are suitable for use in mineral oils (API classes 1 to 3), naphthenic oils, ester oils (API class 5), and poly-alpha-olefins (API class 4).
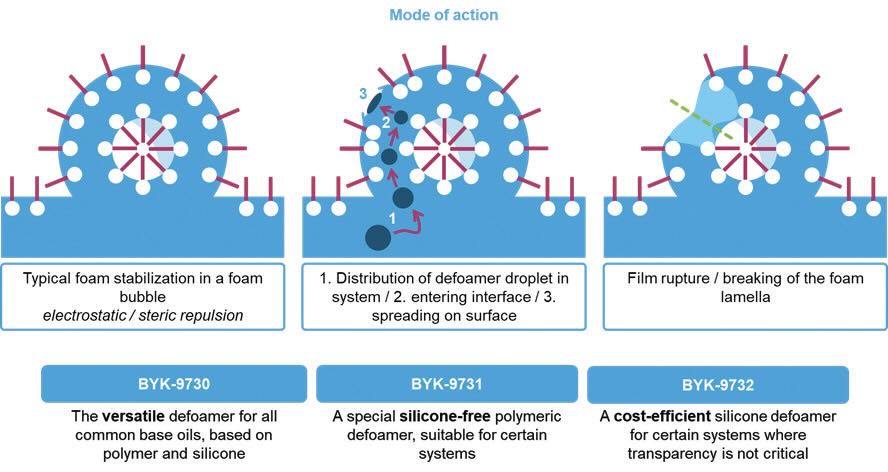
Figure 1: BYK now offers a solution with its first three defoamers specifically for industrial oil-based lubricants.
The recommended dosage is typically between 0.05% and 0.1% of the total formulation. Each defoamer is tailored for specific applications, ensuring optimal performance without compromising the transparency or stability of the lubricant (Table 1). BYK-9731, for instance, has a low silicone content, ensuring no impact on transparency. A key feature of this defoamer is its excellent storage stability, with no precipitation or separation observed, and its particle-free nature, which prevent it from being filtered out over time.
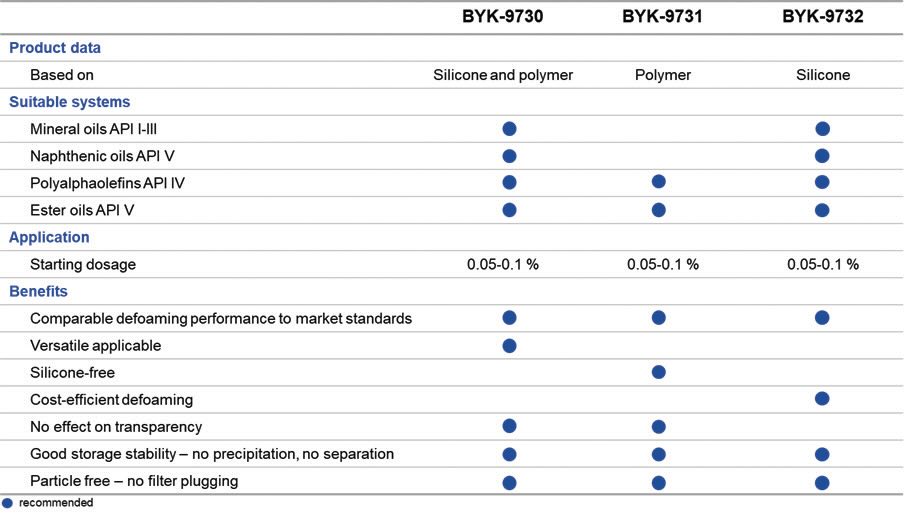
Table 1: Differentiation between BYK-9730, BYK-9731 and BYK-9732.
This was demonstrated in the ASTM D892 test conducted in BYK’s laboratory using the BYK-9730 defoamer in a mineral oil API class 2 (Table 2). The test results showed that, compared to a market benchmark, BYK-9730 exhibited excellent foam control immediately after formulation and significantly better performance after two months of storage.
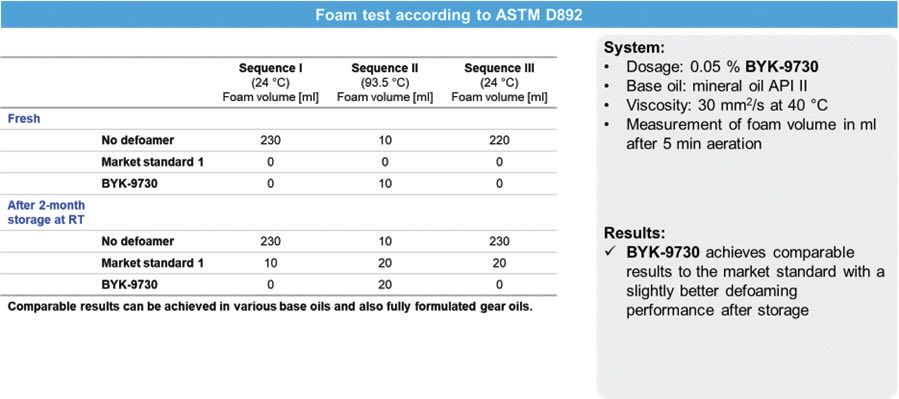
Table 2: Foam test according to ASTM D892 of BYK-9730.
Furthermore, the transparency of lubricants remains unaffected even at higher dosages. This is illustrated by images of mineral oil, naphthenic oil, and polyalphaolefin, all of which retained their clarity after the addition of 0.2% BYK-9730 defoamer. In contrast, purely silicone-based defoamers resulted in slight turbidity, especially at higher dosages (Figure 2). BYK's defoamers represent a significant advancement in maintaining the performance and clarity of industrial lubricants, providing long-term stability and effective foam control without compromising the essential properties of the oils.
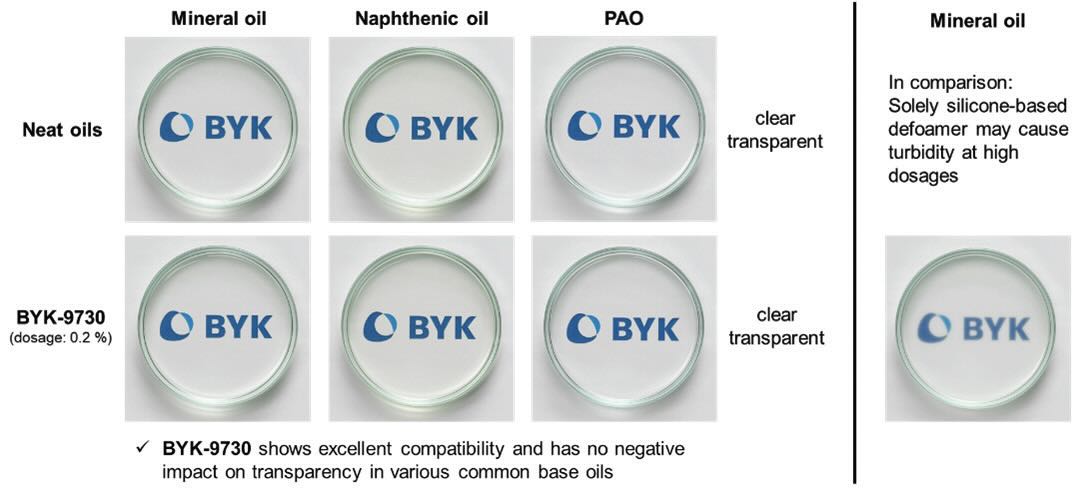
Figure 2: BYK 9730 shows excellent compatibility without negative impact on transparency in various base oils.
Greases thickened by organoclays
Bentonite, particularly montmorillonite, belongs to the smectite group of clays and is widely utilized to thicken lubricating greases. These clays have a layered structure, with each unit layer comprising a silica-alumina arrangement. Crucially, the exchangeable cations on the surface and hydroxyl groups at the edges facilitate hydrophobic modification and hydrogen bonding, essential for gelling lubricating fluids.
In nature, bentonite clays appear in stacks with inorganic cations on both inner and outer surfaces of each layer. When these clays contact water, the hydration energy overcomes the van der Waals forces between the layers, causing them to expand. However, to function as gellants in oil-based systems, the clays must be rendered hydrophobic by replacing the inorganic cations with quaternary ammonium organic cations (Figure 3).
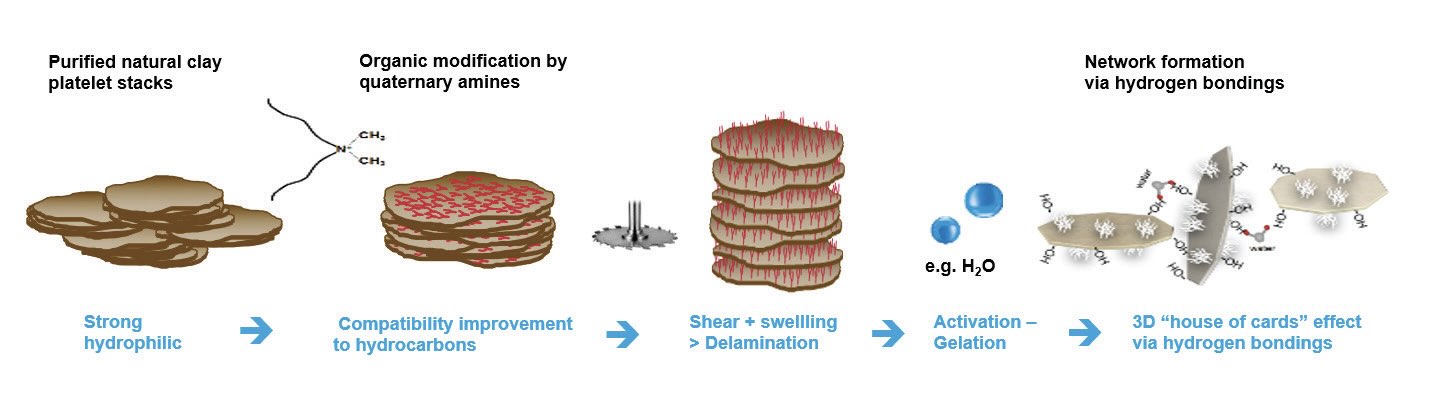
Figure 3: Working mechanism of organically modified clays.
This organically modified clay, available as a dry powder, exhibits desirable gelling properties in oils. The transformation of organoclay into a gel involves three phases:
1. Deagglomeration: Achieved through slow-speed stirring and by recirculating the organoclay-oil mixture through a pump.
2. Dispersion: Requires a chemical polar activator (such as water, alcohols, or carbonates or mixtures thereof) to weaken the van der Waals forces between clay platelets and raise the quaternary organic chains from the platelets, enabling solvation by the oil. Some organoclays are "self-activating" eliminating the need for additional activators.
3. Gel formation: Achieved by applying intense turbulent shear using equipment like a colloid mill or homogenizer. This creates a random network of organoclay platelets held together by hydrogen bonds.
BYK offers various organoclays tailored for specific oils used in grease applications. The most widely used are the CLAYTONE types, which include both self-activating clays and those requiring activators (Table 3). These clays are suitable for all API classes. Notably, CLAYTONE types are also appropriate for food contact applications and suitable for kosher and halal lubricating greases.

Table 3: BYK organoclay product selection—green indicates first recommendation, orange indicates second recommendation.
Activators such as water, propylene carbonate-water (95:5) mixtures, or ethanol-water (95:5) mixtures can be used, with different activators offering varying efficiencies. Typically, a dosage of 10 to 25 percent activator based on clay weight is recommended. Greases manufactured with organoclays demonstrate excellent high-temperature stability, up to 200°C, with very high or no dropping points, making them ideal for applications requiring temperature stability.
Dispersion of solid particles
Dispersing additives stabilize particle dispersions and prevent re-agglomeration of the fillers such as graphite, molybdenum disulfide, PTFE, and boron nitride in lubricant oils. The focus is therefore on the uniform distribution of the fillers in the lubricant oil and the maximization of the surface area by avoiding re-agglomeration. Without dispersing additives, fillers like graphite can significantly thicken oils, making them non-flowable. However, incorporating dispersing additives at concentrations as low as 3-5% can reduce viscosity, can increase the lubrication properties and maintain flowability, as demonstrated in various applications, including forging oils.
A graphite dispersion was prepared with 25% graphite in a mineral oil of API class 2 (Figure 4). The viscosity of the dispersion was measured without any dispersing additive and then with the addition of a dispersing additive, DISPERBYK-2157, at concentrations of 1%, 3%, and 5% based on filler. The results showed a significant reduction in viscosity with the dispersing additive, transforming a highly viscous material into a flowable one. Microscopic images further illustrate the effectiveness of dispersing additives. Without the dispersing additive, large black agglomerates of graphite are visible (Figure 4). With the addition of 3% dispersing additive, the graphite particles are finely dispersed, resulting in a flowable and stable material.
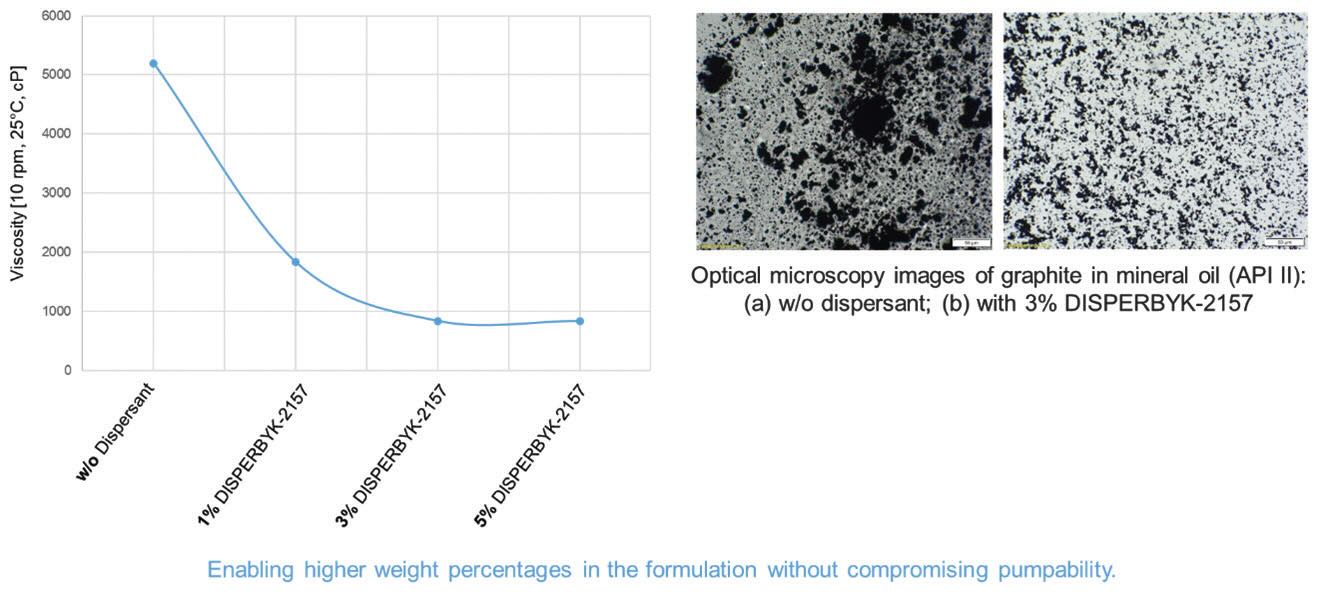
Figure 4: Addition of DISPERBYK-2157 results in a decline in viscosity and better dispersion of graphite particle in the mineral oil. The test system was 25% graphite dispersed in mineral oil (API II).
Summary
BYK offers advanced additives for lubricants including three defoamers (silicone-free BYK-9731, silicone-based BYK-9732 and hybrid BYK-9730) to control foam without compromising lubrication, organoclays, like CLAYTONE and GARAMITE, to thicken greases ensuring high-temperature stability, and dispersing additives to enable the creation of finely dispersed fillers in oil, improving lubricating properties. Moreover, dispersing additives offer substantial advantages for lubricants containing filler and allow for high filler loadings (10-40%), which would be unachievable otherwise. This results in lower viscosity, better handling, and improved pumpability, enhancing the overall performance and efficiency of lubricant formulations.
Overall, BYK’s advanced additives and organoclays significantly enhance lubricant performance, stability, and applicability in various industrial contexts.