HIGHLIGHTS
•
A new aluminum alloy prepared from transition metals (titanium, iron, cobalt and nickel) exhibits greater mechanical strength than traditional alloys when undergoing the additive manufacturing process, selective laser melting.
•
The strength of this aluminum alloy is due to the interactions among three major phases.
•
Micropillar compression testing demonstrated that certain regions of this new aluminum alloy can exhibit strength values in excess of 900 megapascals.
Additive manufacturing, also known as 3D printing, has been gaining in use because it is effective in producing complex metal parts, demonstrates greater sustainability than the commonly used flood application and can provide better production efficiency. This technique does have limitations including difficulties with manufacturing parts using aluminum alloys.
A previous TLT article
1 discussed an approach taken by researchers to produce metal parts from the well-known wrought aluminum alloys, 6061 and 7075. This involved addition of nanoparticle grain refiners to metal powders of these aluminum alloys prior to 3D printing. Hydrogen stabilized zirconium particles were found to be the best fit after the researchers evaluated nearly 5,000 metal powder, nanoparticle combinations. The 3D printed aluminum alloys containing these nanoparticles displayed comparable properties consistent with wrought alloys prepared conventionally.
A common additive manufacturing process technique is selective laser melting. Metal powders are melted in a specific location by a high energy laser beam as a metal part is built layer by layer. When applying selective laser melting to common wrought aluminum alloys, the problem is they are vulnerable to hot cracking.
Anyu Shang, a graduate research assistant at Purdue University in West Lafayette, Ind., says, “Hot cracking typically happens in additive manufacturing during solidification in a similar manner to welding. Aluminum alloys undergo a high thermal expansion during heating followed by a substantial contraction upon cooling, which leads to cracking particularly with other metal elements present. The quenching rate during cooling can be rapid, which accelerates crack generation.”
One approach to reduce the detrimental effects of hot cracking is to add fine and hard particles such as titanium nitride or titanium carbide that can strengthen an aluminum alloy by impeding dislocation movements. Shang comments, “For the past two to three years, researchers have been trying to find the right combination of metal nanoparticles to strengthen aluminum alloys making them suitable for additive manufacturing. The drawback is that special technology is required to uniformly mix metal powders with metal nanoparticles and then process them typically using a technique known as ball milling. Adding to the cost is the labor and tooling required.”
Unfortunately most aluminum alloys produced with metal nanoparticles could only attain mechanical strength in the 300-500 megapascal range, which is far less than the typical strength of steels (500-1,000 megapascal). A new investigation has now led to the production of a high-strength aluminum alloy that can be 3D printed without a loss in hardness.
Intermetallics
The new aluminum alloy was produced by taking advantage of the formation of intermetallics through the interaction of specific transition metals with aluminum. Xinghang Zhang, professor of materials engineering at Purdue University, says, “Intermetallic bonds between transition metals and aluminum yield very stable materials that typically exhibit a high melting point. Examples of transition metal that are particularly effective are cobalt, iron, nickel and titanium.
Shang adds, “Metals such as magnesium form alloys with aluminum that are not stable at high temperatures and in fact can be brittle at room temperature. Transition metals (such as iron) have been found to be particularly stable in aluminum alloys at high temperatures.
The new aluminum alloy was prepared from aluminum (Al), titanium (Ti), iron (Fe), cobalt (Co) and nickel (Ni) and has the following formula: Al92Ti2Fe2Co2Ni2. The alloy was prepared using the 3D printer in Figure 1. Selective laser melting was conducted with a laser power of 200-300 watts.
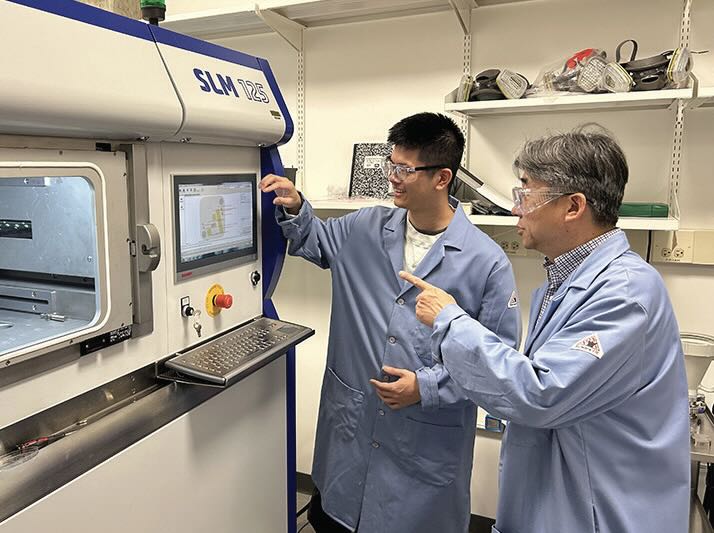
Figure 1. A new aluminum alloy exhibits greater strength than traditional ones when processed using the additive manufacturing technique known as selective laser melting. Figure courtesy of Purdue University.
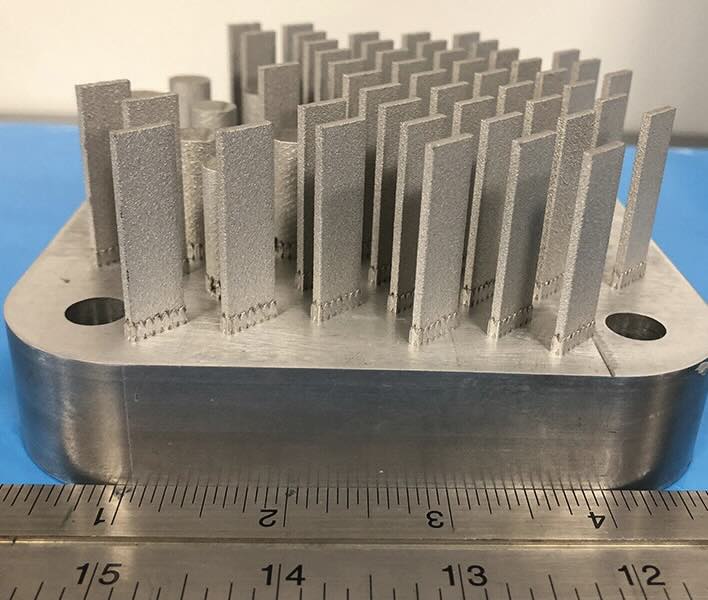
Figure 2. Additive manufacturing on a new aluminum alloy produced the metal parts shown. Figure courtesy of Purdue University.
Zhang says, “We have been studying alloys with combinations of transition metals for some time. Initially, our work was conducted to evaluate sputtered aluminum alloy coatings. In the context of traditional cast/wrought aluminum alloy industries, past studies showed that alloys of aluminum with iron, cobalt and nickel were very brittle. Using selective laser melting, a very fine to ultrafine intermetallic structure that is not as brittle and shows significantly greater mechanical strength is produced.”
Microstructural characterization of the new aluminum alloy identified the existence of three major phases consisting of an aluminum matrix, Al9(Fe, Co, Ni)2 and Al3Ti. The additive manufacturing process conditions lead to the formation of solid precipitates known as intermetallic rosettes in the molten metal matrix. These rosettes are formed due to aggregation of colonies of nanoscale, intermetallic lamellae.
Shang says, “An analogy is that rosettes can be considered to be similar to the presence of fine sand particles in water. Sand is not soluble bur rather is dispersible.”
Micropillar compression testing demonstrated that certain regions of this alloy can exhibit strength values in excess of 900 megapascals. Values in excess of 800 megapascals were found in macroscale compression tests.
Zhang says, “The strength of this new aluminum alloy originates from the interactions among the three phases observed. Back stress is observed in the interphase between hard and soft regions of the alloy. The hard region contains intermetallics while the soft region is aluminum. As an external force is applied, geometrically necessary dislocations form and contribute to the high strength of the alloy.”
Additive manufacturing using this alloy produced parts shown in Figure 2.
Future work will involve gaining a better understanding of the chemistry of and high temperature properties of the new aluminum alloy. Shang says, “Our intention is to better understand the new aluminum alloy’s chemistry to determine how to design other alloys that exhibit advanced mechanical properties. Work done in this study evaluated the new alloy at ambient temperature. The next step is to examine the alloy’s properties at temperatures between 200-300°C to determine if it is suitable in applications such as aerospace.”
Additional information can be found in a recent article
2 or by contacting Zhang at
xzhang98@purdue.edu.
REFERENCES
1.
Canter, N. (2018), “Manufacturing of aluminum alloys by 3D printing,” TLT,
74 (1), pp. 12-13. Available
here.
2.
Shang, A., Stegman, B., Choy, K., Niu, T., Shen, C., Shang, Z., Sheng, X., Lopez, J., Hoppenrath, L., Zhang, B., Wang, H., Bellon, P. and Zhang, X. (2024),”Additive manufacturing of an ultrastrong, deformable Al alloy with nanoscale intermetallics,”
Nature Communications, 15, Article number: 5122.