Oil cleanliness and particle counting
By Dan Holdmeyer, Contributing Editor | TLT Lubrication Fundamentals October 2024
It’s critical to take a relevant and representative sample when measuring particle counts to properly determine the contamination level.
Oil contamination comes in many forms, such as water, air, fuel, chemicals, different oils, particulate and other insoluble materials. Oil cleanliness refers specifically to particulate materials.
Particulate matter causes excessive wear in machinery, leading to unscheduled downtime, increased maintenance costs and shorter equipment life. Particles cause abrasive wear in between lubricated moving surfaces and cause valves to stick and wear. Oil cleanliness is even more critical in systems with close tolerances, such as precision bearings and servo valves. Higher pressure and higher speed in these applications require even cleaner oils to minimize wear.
As these particles cause wear in a lubrication system, they create more particles, raising the level of particulate contamination in the oil. Thus, oil cleanliness is one measure of the system’s oil’s suitability for continued use, or the need for cleaning. It also makes sense that the next charge of oil be cleaner than the oil replaced. OEMs recommend cleanliness levels for fresh oil to their systems and for used oil in the system. They may be different.
One would think that new oil is clean, which it is, relative to used oil. However, new oil easily becomes “dirty” through mishandling. Lubricant storage areas are notoriously not sterile, usually quite dirty. Lubricant storage container lids and caps are often left open or off, allowing airborne dirt to contaminate the lubricant. Oil transfer cans and funnels are exposed to and do collect airborne particles as well. Wiping the funnels and oil cans “clean” may make it look clean, but it is the small particles, too small for the unaided eye to see, that cause the most damage in systems with close tolerances. Even if the lubricant storage area is a first-class operation, the new oil may not meet the demands of today’s high pressure extremely close tolerance systems unless the oil supplier and user collaborate on steps to clean, and maintain the cleanliness of, the oil.
Machining capabilities today make bearing surfaces so smooth that full fluid hydrodynamic films only microns thick can separate the journal from the bearing. Thus, a particle as small as 4 microns in size in the oil can cause damage to the bearing. A micron is one-millionth of a meter, or 1/25,400 of an inch. The unaided human can only see down to about 40 microns. The days of being able to “feel” a clean versus dirty oil by your fingers are long gone, and I’m not sure that ever was a reality.
So, how do we know if the oil is clean enough for these critical systems? How do we measure cleanliness at that level?
One of the earlier methods of determining oil cleanliness was to filter a specific quantity of the oil sample through a fine filter followed by examination via optical microscope. Then, a lab technician counts the number of particles 5 microns and larger, and 15 microns and larger in size. This is a fundamental explanation of the International Organization for Standardization (ISO) 4407. The filter patch typically has a grid imprint to aid in counting, or a comparator book can also be used to aid the analysis. Plus rinsing the patch to remove the non-particle, or “soft,” insoluble material enhances hard particle visibility for easier counting. It is the hard particles that pose the greater risk of abrasive wear. This method is labor intensive and time consuming.
Automated optical particle counters via ISO 11500 are the most widely used counters in use today. The oil sample passes through a capillary tube where a laser or white light is focused on a specific length of the tube. Particles in the tube then cast a shadow on a photocell detector where an internal processor identifies the number of particles and their sizes. The particle count is quickly processed due to the automation. The particle counter does require routine calibration, as do other lab equipment.
A slight variation of ISO 11500 is ASTM D7647-10, which uses the same equipment but adds a sample preparation step. Solvent dilution pre-treatment helps eliminate soft insoluble materials but does add time for in the lab.
Optical particle counters work well with light colored oils such as turbine and hydraulic oils; however, darker and/or higher viscosity oils are better analyzed by ISO 4407, with the filter patch. A more automated version of ISO 4407 is “pore blockage” particle counting used for gear and engine oil applications. Fundamentally speaking, pore blockage counters incorporate two or more screens, which may be rated at 5 and 15 microns to aid in computing National Aerospace Standard (NAS) 1638 results (ISO 4406: 1987), that we’ll discuss later in this article. As the oil sample flows through the screens, the flow degradation is measured as the screen’s “plug” with particles, to determine quantity of the various sized particles.
Ferrography is not so much a method of particle counting but a method of wear analysis used to detect the mechanism and severity of wear in machinery. Ferrous metals are separated from the oil and other metals via a magnetic field in a ferrograph. The ferrous metals’ shapes are examined under a microscope to determine types of wear occurring in the equipment, cutting, severe sliding, spalling, etc.
ASTM D7596, or LaserNet Fines, is a standard for particle counting along with particle shape classification for identifying wear modes. LaserNet Fines, a relatively new test standard, automates ferrography on particles larger than 20 microns as well as particle counting. LaserNet Fines automated ferrography also can identify nonmetallic particles, fibers and even water droplets, which enhances insight to wear and contamination in the lubrication system.
Those are the most common particle count test methods, so let’s talk about how cleanliness is reported. NAS 1638 updated by AS4059 and ISO 4406 are two common standards.
NAS 1638 was developed by the aerospace industry to determine contamination levels and is still in use today. The NAS 1638 breaks the particle counting into five particle micron size ranges: 5-15, 15-25, 50-100 and > 100. The maximum number of particles per 100 ml of oil sample in each size range is then classified into a contamination level from cleanest (00) to dirtiest (12). The results for NAS 1638 are reported by a single NAS class, the maximum value of the various sizes. This report does not provide sufficient information on the cleanliness of the oil. System filters remove certain size particles but not all. The AS4059 standard identifies and reports an NAS class for each of the five particles size ranges, thus providing a much clearer and detailed understanding of what size particles, and how many of them, are in the oil. This then can also easily translate into ISO 4406 Cleanliness Code.
ISO 4406:21 is the most used industry standard for reporting oil cleanliness, also commonly referred to as “particle count.” ISO 4406:21 is the 2021 version of identifying three overlapping size ranges to classify the number of particles in a one milliliter sample of oil. The overlapping ranges are classified in the following order of number of particles, equal to and greater than 4 microns, equal to and greater than 6 microns, and equal to and greater than 14 microns, in size. ISO 4406:87 was coded by 2, 5 and 15 micron size particles, and sometimes only referenced the last two particle sizes of 5 and 15. The two-code report is sometimes used today with ISO 4406:21 and references the 6 and 14 size particles. The report would be in the form of x/y/z, corresponding to the Cleanliness Code for the various size categories; 4/6/14.
If one of the particle counting methods discussed previously identified the following particles by size per milliliter, we can convert that to a much simpler three code report.
Figure 1, the laboratory particle count test chart, shows the number of particles in several different particle size ranges. In Figure 2, the ISO 4406 Cleanliness Code chart, we need to look at the particle count numbers for 4 microns and greater, 6 microns and greater and 14 microns and greater to find the cleanliness codes to report out, respectively. These test results would result in an ISO 4406 Cleanliness Code of 18/15/13. This also may be reported using just two codes as 15/13, or x/15/13.
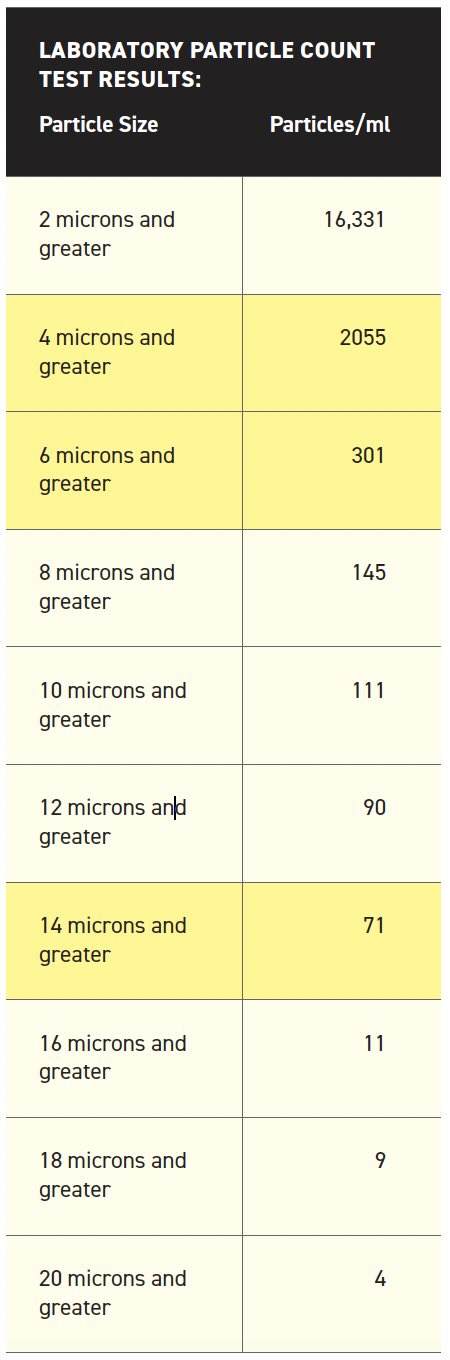
Figure 1. Laboratory particle count test chart.
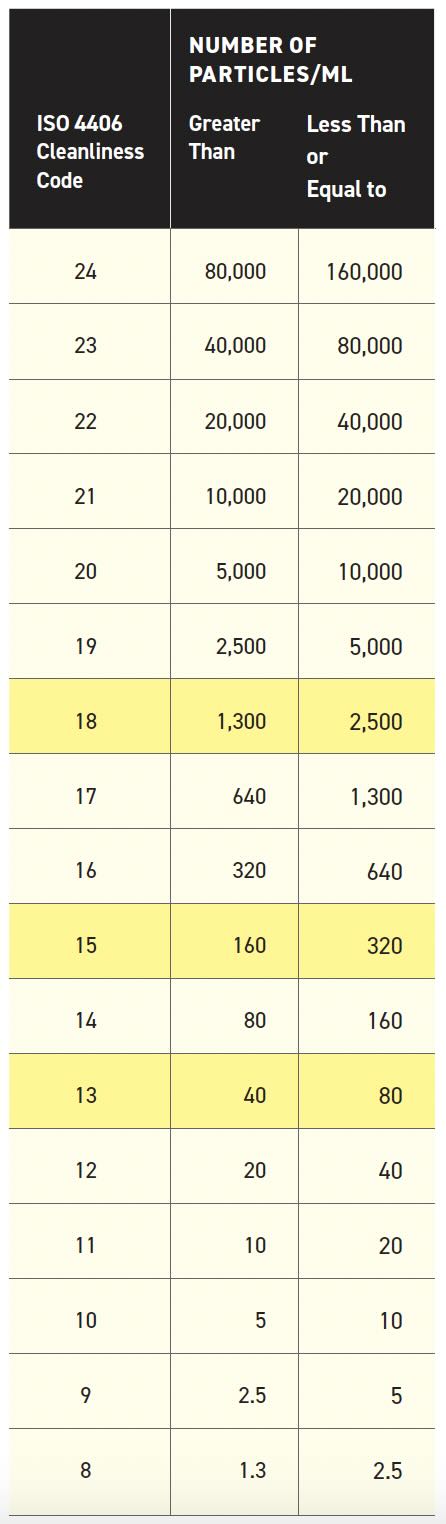
Figure 2. ISO 4406 Cleanliness Code chart.
Note that the number of particles per milliliter in the ISO 4406 Cleanliness Code chart doubles for each succeeding ISO 4406 Cleanliness Code. However, if a particle count in one size range for Sample A was 321 and for Sample B it was 319, they would be reported as ISO Cleanliness Code 16 and 15, respectively, for that particle size range. So it is good to review the actual particle counts in addition to the ISO 4406 Cleanliness Code. Similarly, AS4059 versus NAS 1638 gives clearer insight to the system’s oil cleanliness.
Regardless of the test method and standard used, it’s critical to take a relevant and representative sample when measuring particle counts to properly determine the contamination level. Incorrect sampling can adversely affect the cleanliness level in the sample bottle, which will skew results and lead to incorrect insights. We discussed this in the TLT Lubrication Fundamentals March 2022 article titled “Fluid sampling.”
Lubricant cleanliness is important in all lubrication applications. Turbine and hydraulic applications require the cleanest oil, relative to gear and engine applications. Turbine and hydraulic oils might be around an ISO Cleanliness Code of 17/15/12, whereas gear oils might be around 18/16/14. Specific components and operating conditions will change cleanliness requirements. OEMs will look at the components (valves, bearings, pumps, etc.) of a lubrication system to determine which has the tightest, or the cleanest, oil requirements to set the ISO cleanliness level for a particular machine. The clearance tolerances of the moving parts, system speed and system pressures, both fluid and load, all influence oil cleanliness requirements. The closer the tolerances, the faster the speed, and the higher the pressure all mean cleaner oil required.
Dan Holdmeyer is retired from Chevron Lubricants and is based in Washington, Mo. You can reach him at dan.holdmeyer@gmail.com.