KEY CONCEPTS
•
H2ICE technology is a promising alternative to battery electric vehicles (BEVs) and fuel cell electric vehicles (FCEVs), especially for heavy-duty applications. Because of this, there has been a notable increase in H2ICE technology interest in areas that include OEM and supply chain investment and government funding.
•
H2ICE technology faces several technical challenges such as preignition, hydrogen embrittlement, high water accumulation in engine oil and lower power density in certain air-fuel mixture modes.
•
The development of specialized lubricants to meet the unique needs of H2ICEs is crucial. These lubricants must address issues such as higher combustion temperatures, increased water production and the risk of preignition, while also providing excellent wear protection, anti-corrosion properties and high thermal stability.
Over the last two years, there has been a significant investment increase in the advancement of the technology supply chain for internal combustion engines capable of running on hydrogen fuel (H2ICEs). Depending on how the H
2 is produced, these engines can function as an alternative zero-carbon powertrain solution for both on and off-road applications. A portion of H
2 can be derived from excess generation supplied by renewable sources, such as photovoltaics and wind, and therefore can have very low or even zero-carbon intensity (see How H
2 is Produced).
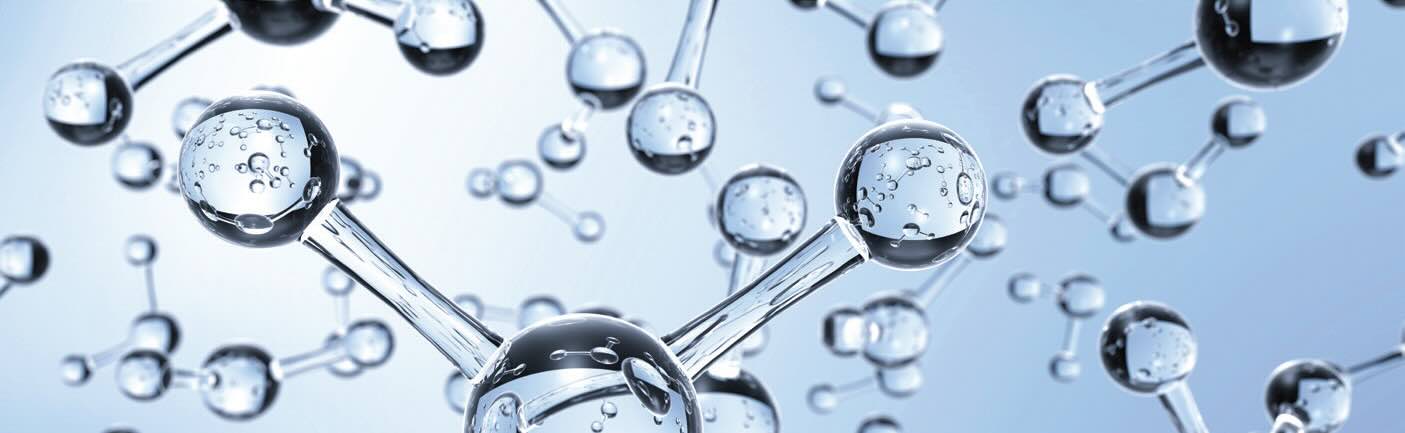
How H2 is producedA
Hydrogen production entails the separation of hydrogen from other elements in molecules that contain hydrogen. Steam-methane reforming and electrolysis are the two most prevalent methods for hydrogen fuel production.
Steam-methane reforming is responsible for the production of virtually all commercially available hydrogen in the U.S. This method is employed by commercial hydrogen producers and petroleum refineries to separate hydrogen atoms from carbon atoms in methane (CH4). In the presence of a catalyst, high-temperature steam (1,300°F-1,800°F) reacts with methane to produce hydrogen, carbon monoxide and a relatively small quantity of carbon dioxide during the process, which occurs under 3 bar-25 bar pressure.
Industrial facilities and petroleum refineries predominantly utilize natural gas as the methane source for hydrogen production through steam-methane reforming, while numerous fuel cell power facilities in the U.S. utilize landfill gas (biogas) as their energy source. Petroleum fuels and biofuels also are potential hydrogen sources.
Electrolysis is a less prevalent method of producing hydrogen fuel. This entails the separation of hydrogen from water through the use of an electric current. Other than hydrogen and oxygen, electrolysis does not generate any byproducts or emissions. Research is currently underway to investigate alternative methods of hydrogen production.
A.
From
here.
STLE member Ke Jian Liang, technology director Asia Pacific, Afton Chemical, observes, “Specifically, the emphasis on OEM investment, regulatory incentives and government investment, supply chain investment and finally in-use demonstration programs is accelerating beyond any previous predictions. Many of the top OEMs have concluded that H2ICEs are more suitable than fuel cells due to lower initial cost, relative simplicity and higher robustness, which is important for many applications. For these reasons, they are motivated to invest considerable sums for the development of this technology.
1,2 They also have begun supplying H2ICE powertrains for certain applications.”
Regulatory authorities also are encouraging the use of H2ICE technology in their jurisdictions. The European Union (EU) is considering classifying H2ICEs as “Zero Emission Vehicles,” while the U.S. government has provided tax credits for H
2 generation and filling stations through the Inflation Reduction Act.
3 This is in addition to funding for development of hydrogen technologies.
4,5
To supply the quantities of hydrogen needed to power H2ICEs and other applications, energy companies are beginning to build generation and transportation infrastructure.
6,7 In-use demonstrations also are underway. Preliminary performance and analysis indicate that H2ICE powertrains are viable for most of the applications.
8,9 A Joint Industry Partnership consortium led by Southwest Research Institute (SwRI) is working to commission an H2ICE on a commercial heavy-duty truck in order to evaluate road performance
(see The Role of Academic/Industry/Government Partnerships).10
The role of academic/industry/government partnerships
According to Shijin Shuai, professor, State Key Lab of Intelligent and Green Vehicle and Mobility, School of Vehicle and Mobility, Tsinghua University, China, a government’s policy for subsidizing H2ICE research is most important. “The H2ICE industry should work together with academic partnerships to develop the key technologies such as preignition and injection bearing mechanisms,” he says.
Dr. Modestino De Feo, senior lubricant technologist, Aramco Overseas, views industry partnerships as essential for overcoming the complex technical barriers associated with hydrogen engines. He emphasizes that expertise from different domains is necessary and that collaboration between lubricant manufacturers, the engine industry and research institutions will accelerate research and product quality.
Bansal concludes, “Industry partnerships are key to solving the challenges in our industry and H2ICEs are no different. These partnerships can allow for easier access to production or commercial grade H
2 engines, promote transparent dialog on key bottlenecks for H2ICE adoption such as supply and distribution of H
2 and most importantly advocate for policy upgrades to recognize H2ICEs as one of the solutions toward a lower carbon future. Industry partnerships will help facilitate joint discovery and problem solving and enable OEMs to improve the overall engine efficiency and reliability.”
Advantages of H2ICE technology
H2ICEs are being developed to address an ever-growing demand for powertrains with a reduced CO
2 footprint. At present, this technology has evolved from being technically feasible to commercially viable.
As hydrogen begins to fill energy supply chain needs, H2ICE technology is beginning to look like a more attractive alternative to battery electric vehicles (BEVs) and fuel cell electric vehicles (FCEVs), specifically for hard to electrify applications. Some of the factors that are being considered in this comparison between H2ICE technology and alternatives include:
•
Charge time
•
Range versus weight/volume
•
Duty cycle (idling, accelerating, cruising and decelerating) requirements
•
Raw material requirements
H2ICE technology is a more attractive solution than electrification for heavy-duty (HD) applications, in particular, for several reasons:
•
H2ICE adoption does not require a redesign of the entire HD powertrain system, and therefore has a lower capital cost. This enables a scalable approach for HD; allowing use of the same cab and truck designs and systems that customers have come to rely on.
•
In commercial HD applications where availability/utilization is critical, refilling H
2 is much quicker than the several hours needed to recharge electric vehicle (EV) batteries. Additionally, H2ICE technology supports the longer ranges that are needed for modern truck and fleet operations.
•
H2ICE vehicles are likely to be less carbon intensive than EVs when considering the full lifecycle assessment. This is due to the high carbon-intensive nature of batteries and EV components, as well as the carbon intensity of the electricity generated in many markets.
Challenges with H2ICE technology
To ensure the performance and durability that customers have come to expect from HD powertrains, and to meet industry regulations, certain engine components had to be modified, while others had to be redesigned for H2ICE. Liang explains, “For example, since hydrogen is a gas, to deliver torque equivalent to a diesel engine requires a lot more volume of H
2 to be injected into the combustion chamber when compared to diesel.”
He cites additional technical challenges such as preignition and hydrogen embrittlement, adding that the industry is currently working hard to develop direct injection fuel injectors for H2ICE technology, and it is possible that designs could evolve over the next decade, as real-world performance and durability are better understood.
Another technical challenge is high water accumulation in engine oil. Liang explains, “Combustion of H
2 produces a lot more water than that of diesel, or even natural gas. At certain operating conditions such as short duration operation, and/or in colder environments, there is an increased risk of water accumulation in the engine oil, which field testing indicates could be an order of magnitude greater than in typical use conditions. Such a high amount of water can lead to corrosion of engine components, formation of emulsions and a loss in engine oil performance and durability. Engine oils have typically not needed to handle such large amounts of water. To this end, prototypes are being developed to handle this increased amount of water.”
Preignition also is a concern. However, Liang points out that preliminary data indicates preignition performance can be improved by the use of a properly formulated engine oil.
Then there is the issue of flammability and leaks. Hydrogen requires only a small amount of energy to ignite, making early/comprehensive leak detection and proper ventilation crucial. However, because hydrogen is colorless and odorless, detecting leaks can be difficult. In the event of a leak, hydrogen disperses quickly due to its low density. This can reduce the risk of a large explosion but may still pose a fire hazard if there is a nearby ignition source.
“To ensure that all these technical challenges are overcome, holistic formulations will be needed to allow optimum operation of H2ICE technology in HD vehicles.” Liang adds, “The solutions are not yet in place and the technology is in the early stages of innovation and development.”
Shijin Shuai, professor, State Key Lab of Intelligent and Green Vehicle and Mobility, School of Vehicle and Mobility, Tsinghua University, China, brings up power density as an issue. “H2ICE has two basic air-fuel mixture modes: port fuel injection (PFI) and direct injection (DI),” he explains. “The PFI mode of H2ICE has a lower power output than gasoline engines (20%-30% lower) due to less air absorption into the cylinder and more hydrogen gas in the intake port. But the DI mode can have a higher power density and efficiency than gasoline engines because of the higher mixture heat value of H
2 directly injected into the cylinder.”
Shuai adds that H2ICE-powered vehicles need a large space for the H
2 fuel tank. “For example, the tank volume of 700 bar H
2 is three times larger than a gasoline tank with the same power output,” he says. “The H
2 fuel storage, fuel delivery and fuel-adding devices also are needed for an H2ICE vehicle application.” A 700 bar (roughly 10,000 psi) tank would have a volume of about 200 liters/52.83 gallons.
Primarily due to established infrastructure and economies of scale, gasoline and diesel are currently more cost-effective on a per-mile basis than hydrogen.
Technical challenges for lubricants
H2ICE technology differs from traditional engine technology in many ways, mainly due to the differences in the combustion characteristics of hydrogen. These characteristics, combined with the need to deliver performance relevant to target applications, lead to unique hardware and operating conditions of the engine, which in turn impact lubricant performance requirements.
Dinesh Bansal, senior R&D scientist, Chevron Oronite LLC, notes, “Broadly speaking, the lubricants for H2ICEs use components similar to diesel and gasoline engine lubricants. The key differences lie in the fine balance of different additives, namely dispersants, detergents, antiwear, antioxidants and other inhibitors required to address H2ICE-specific challenges. The final lubricant formulations for H2ICEs are designed to address the specific challenges posed by H2ICEs. EV lubricants have different performance needs and hence have significantly different composition when compared to the engine crankcase lubricants.”
Bansal points out that currently there are no commercially available H2ICEs, and most independent test labs are offering natural gas engines modified to run hydrogen for lubricant testing. “This is a good first step, but lack of availability of production level H2ICEs precludes lubricant evaluation in a production or near-commercial level engine technology both in test cells and on-road field testing,” he says.
Bansal adds that the second most important challenge is the cost of testing and fuel. “Although it is anticipated that these costs will reduce as the test labs scale up H2ICE testing and the fuel supply improves,” he says.
Dr. Modestino De Feo, senior lubricant technologist, Aramco Overseas, mentions technical challenges for lubricant formulation such as ensuring water emulsification resistance and mitigation of the preignition issue along with other interconnected challenges.
Liang observes, “One of the challenges is the relatively low volumetric energy density of hydrogen air mixtures in the combustion chamber. This leads to relatively low power for traditional displacement engines.”
This can be overcome by using boosting systems such as turbochargers and superchargers, but these systems often have very high surface temperatures and may be susceptible to deposit formation. Given this, engine oil may need to be formulated for these requirements.
Another lubricant formulation consideration Liang points out is the presence of high levels of nitrogen oxide (NOx). “Due to the high adiabatic flame temperature of hydrogen, stoichiometric mixtures are prone to generation of unacceptable levels of NOx,” he says. “Therefore, the air-fuel ratios that production engines operate at are very lean. The presence of excess hydrogen and high combustion chamber pressures leads to significantly higher partial pressure of oxygen in the combustion chamber, which could accelerate oxidation of the oil, particularly at high temperatures. This may need robust antioxidant systems for protection.
In addition, the flame speed of hydrogen air mixtures is higher than that for natural gas engines. Therefore, spark timing can be optimized much more easily for hydrogen engines, which in turn may stress the engine oil much more than other engines, and engine oils may need to be formulated for long oil drain intervals.
As mentioned previously, due to low minimum ignition energy, hydrogen engines also are prone to preignition—much more so than natural gas engines. Since preignition performance is driven by oil composition, particularly the base oil quality and the additive pack, preignition needs to be considered during lubricant formulation.
Liang points out that the risk of preignition also has been identified in the positive crankcase ventilation (PCV) system. Because of this, OEMs are designing systems to flush the crankcase with fresh air in an effort to keep the concentration of H
2 below ignition levels. To ensure acceptable oil loss and durability, this would place requirements, that include volatility, on the lubricant.
As Liang also mentioned previously, there can be a significant concentration of water accumulated in the engine oil. Bansal cautions that it is feasible, under certain operating conditions, that as much as 1%-5% water can accumulate in the oil.
This poses a major challenge for engine oils in terms of preventing deterioration of oil performance, including corrosion and emulsion performance. Engine oils may need improved emulsion handling and corrosion performance to meet these challenges.
A final lubricant challenge Liang mentions stems from the fact that, due to combustion characteristics and lean mixtures, the exhaust from hydrogen engines can be significantly cooler than that from other engines. This could impact performance and durability for the aftertreatment system components. Though these designs are undergoing development, this also could impact oil formulation considerations in areas such as sulfated ash levels.
H2ICE lubricants interact with various materials, including seals and gaskets, in several critical ways. However, De Feo says that, as far as he knows, there has not been extensive research conducted in this area. “I imagine that the lubricants play a crucial role in ensuring compatibility with these materials,” he says. “This would prevent degradation or damage by providing a barrier between the surfaces protecting seals and gaskets from corrosion and chemical reactions that may occur in hydrogen-rich environments.”
He adds, “Specialized additives may be incorporated into oil formulations to enhance this function and extend the sealing function over the engine's lifespan. In my view, while the interaction between lubricants and materials in hydrogen combustion engines is definitely critical for maintaining reliability and efficiency, further research in this area is essential to fully understand and optimize these interactions.”
Bansal concurs that the interaction of hydrogen fuel with various engine components including seals, gaskets and hardware metallurgy is generally unknown and there are no existing standard tests for these evaluations. However, Bansal and colleagues have developed bespoke methods and have modified existing industry tests to evaluate lubricants for any interaction with hardware materials in the engine which include seals, gaskets, copper, steel and other metals.
De Feo cautions, “Many of these problems, such as the embrittlement, may only emerge after prolonged use. This means that, to validate the overall performance of the prototypes and to ensure that the lubricants can meet the demanding conditions of hydrogen-powered engines, extensive endurance testing and real-world trials are essential. Overcoming these challenges requires innovative oil formulations and rigorous testing procedures.”
Given all this, De Feo maintains that the role of the lubricant in engine development is important for enabling reliable running conditions and high-power density for H2ICE technology.
Lubricant requirements
Traditional ICE lubricants focus on managing carbon deposits, oil dilution and combustion residues, while EV lubricants prioritize cooling and electrical insulation properties. The lubricants fine-tuned for H2ICE technology differ significantly from those used in traditional ICEs and even more from EV fluids.
Per De Feo, “Developing lubricants specifically for H2ICE technology presents several key challenges. The unique operating conditions of H2ICE technology, such as higher combustion temperatures, increased water production and the risk of preignition, require the lubricant to provide excellent wear protection and anti-corrosion properties, high thermal stability and enhanced oxidation resistance to protect engine components.”
Another requirement De Feo mentions is ensuring the lubricant's chemical compatibility with hydrogen to prevent degradation and additive depletion. “Hydrogen embrittlement will surely be another important topic to focus on, as it can weaken engine materials and components, which will make the lubricant’s role in mitigating this risk even more important,” he says. “These factors together make the development of lubricants suitable for H2ICE technology both complex and demanding, yet scientifically exciting.”
When it comes to additives, De Feo observes that detergent and dispersant additives may become less critical due to hydrogen’s cleaner combustion. “However, specific additive packages must be meticulously designed to mitigate the risk of preignition due to oil formulation in order to ensure optimal engine performance,” he says. “In this respect, even the selection of the right polymers and right base oils is crucial, as they can significantly influence lubricant behavior in such applications. Moreover, preventing corrosion can become crucial, necessitating careful consideration of additives that manage higher water production and protection of engine surfaces from chemical reactions with hydrogen. This comprehensive approach ensures that lubricants meet the demanding performance requirements of hydrogen engines.”
Bansal concurs, mentioning additives such as dispersants for sludge and high temperature cleanliness; detergents for cleanliness, acid neutralization and wear protection; antioxidants to neutralize oxidative species and maintain viscosity; antiwear additives to provide engine durability; and preignition inhibitors and emulsifiers for improving corrosion protection in the presence of high water content.
Conclusions
According to Shuai, H2ICEs can be easily modified from spark ignition compressed natural gas (CNG) engines or gasoline engines, with the biggest modification being the hydrogen storage injection system. This ease of modification lowers one of the barriers to widespread adoption. However, the durability of the H
2 DI system remains the primary barrier for commercialization. Assuming this is resolved, Shuai expects H2ICE-powered vehicles will be ready for mass production between 2027 and 2030.
REFERENCES
1.
JCB unveils hydrogen engine at Conexpo. Available
here.
2.
Cummins investing more than $1B in U.S. engine manufacturing network. Available
here.
3.
Inflation Reduction Act of 2022. Available
here.
4.
Biden-Harris Administration Announces $750 Million to Advance Clean Hydrogen Technologies. Available
here.
5.
It’s not all lithium all the time: DOE commits millions to hydrogen fuel research. Available
here.
6.
Sinopec to build first “West to East” green hydrogen transmission line in China. Available
here.
7.
Japan to raise hydrogen supply sixfold by 2040 to promote renewables. Available
here.
8.
Fendt trials hydrogen fuel cell tractors. Available
here.
9.
World’s first hydrogen-powered digger set to drive on UK roads. Available
here.
10.
Southwest Research Institute Launches Joint Industry Program to Develop Hydrogen Combustion Vehicle. Available
here.