Meet the Presenter
This article is based on a webinar presented by STLE Education on Feb. 8, 2023. Fundamentals of Surfactants for Metal Cleaning Applications is available at www.stle.org: $39 for STLE members, $59 for all others.
Dr. Thomas Myrdek is a research and development scientist at Kao Chemicals GmbH. Myrdek studied at the Hochschule Niederrhein, in Krefeld, Germany, with his main study topic being surfactant chemistry. He graduated in 2005 with a degree in chemical engineering. He joined Kao Chemicals GmbH in Emmerich am Rhein in 2006 and became a member of the R&D department. He completed his master of science degree in 2010 and in 2020 finished his doctoral study in cooperation with the University Regensburg in the research group of Prof. Kunz. He worked on the synthesis of new types of surfactants, and since 2020, he is project leader for the metal cleaning application at Kao Chemicals GmbH.
You can reach him at thomas.myrdek@kaochemicals.de.
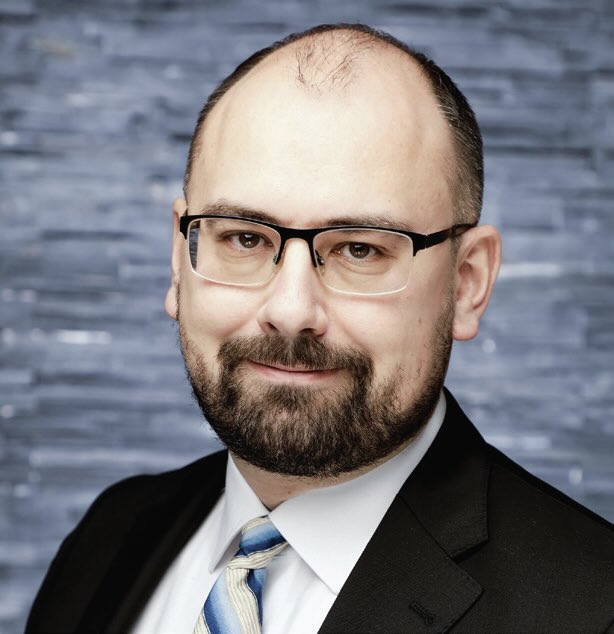
Thomas Myrdek
KEY CONCEPTS
•
Surfactants are amphiphilic organic compounds used in many cleaner formulations. The word surfactant is a blend of letters from the phrase
surface-
active age
nt.
•
Modern surfactants consist of a hydrophilic and a hydrophobic part with the unique structure of the molecule influencing the physico-chemical properties of the molecule, including surface tension, emulsion formation, foaming, wetting properties and the cloud point behavior of the molecule.
•
Metal cleaning formulations are classified based on the pH value of the molecule and employ three main cleaning applications: spray, immersion and ultrasonic.
•
The correct surfactant mixture can improve anti-corrosion behavior, cleaning efficiency and physico-chemical properties in metal cleaning applications.
Many cleaner formulations include surfactants, which are usually amphiphilic organic compounds. That means each molecule has a hydrophilic “waterloving” part (i.e., the head) and a hydrophobic “water-avoiding” part (i.e., the tail). In fact, the word surfactant is a blend of letters from the phrase
surface-
active age
nt.
This article explains the importance of surfactants, the basic function of surfactants in a cleaner solution and how the surfactant molecule’s chemical structure influences how it works. These organic molecules are used to adjust several physico-chemical properties of a metal cleaner. While formulators of cleaners can choose between a huge number of different products, meeting the circumstances and requested characteristics can be challenging. The metal cleaning application in particular involves different challenges discussed here.
This article is based on an STLE Education webinar presented by STLE member Dr. Thomas Myrdek, research and development scientist at Kao Chemicals GmbH, titled Fundamentals of Surfactants for Metal Cleaning Applications. See Meet the Presenter for more information.
Surfactant properties
The molecular structure of surfactants is modular, made up of long carbon-chains, making it relatively easy to change the ends of a particular molecule when constructing the molecule. The middle and end chain parts of the molecule can be modified to adjust what happens when the molecule is mixed in water. Another way to view the hydrophobic part of the surfactant molecule is as an oil-loving part.
There are four types of surfactants based on the head or water-loving part of the molecule: non-ionics, cationics, anionics and amphoteric surfactants
(see Figure 1). Non-ionics do not have a charge and consist of polyether groups and polyethylene ether groups, which provide good water solubility. The hydrophilicity or water solubility of the molecule can be changed by adding more ethylene oxide to the molecule.
Figure 1. The four types of surfactants based on the head or water-loving part of the molecule.
Cationics have a positive charge at the head part of the molecule, potentially from ammonia compounds. Cationic surfactants are not as well-known as the other types and are typically used as hydrotropes to improve the solubility of surfactants in water. Anionics have a negative charge at the head of the molecule, with possible head groups including carboxylic groups and phosphoric groups.
Amphoteric molecules can act as either an acid or a base as they have two charges inside the molecule. This means that at a neutral pH, the anionic part has a negative charge, while the cationic part comes from the positively charged ammonium compounds.
Modern surfactants are mostly hybrid surfactants, which are composed of two modular parts combined. The first modular part is the tail part, which is made by choosing the raw material (i.e., a short chain or long chain fatty alcohol, middle chain fatty acid). The second modular part can be a combination of anionic and non-ionic parts by changing the amount of ethylene oxides, which can impact the water solubility.
Extended hybrid surfactants are created by adding a partial hydrophobic structure between the hydrophilic and hydrophobic ends, which enlarges the C-chain and changes the polarity of the surfactant. Also, a common surfactant for metal cleaning applications is the socalled non-ionic hybrid surfactant. These include a polyethylene oxide group with the polypropylene oxide on the end, which provides a partial hydrophobic part, giving some specific and interesting new properties.
Chemical properties
Basic physico-chemical properties occur when the surfactant is added to water. These properties are important for metal cleaning. Properties discussed include surface tension, emulsification, wetting and cloud point.
Surface tension. The surface of any liquid behaves as though it is covered by a stretched membrane with the net force on a molecule at the surface of the liquid directed into the bulk of the liquid. Surfactants decrease that surface tension.
A micelle is an aggregate of surfactant molecules. Initially, when a surfactant is added to a solution, the surfactant particles line the surface of the solution. The critical micelle concentration (CMC) is the concentration of surfactant in water at which the surfactant begins to form micelles
(see Figure 2). Before reaching the CMC, the surface tension changes strongly with the concentration of the surfactant. After reaching the CMC, the surface tension remains relatively constant or changes only with a lower slope. Above the CMC, the surfactant loses its cleaning properties.
Figure 2. Illustration of a micelle.
The temperature of the system also is important as an increased system temperature results in decreased surface tension. A low surface tension is required for good cleaning properties. Surfactants stabilize the interface between oil or particles and water in suspension
(see Figure 3). This is important for both soil removal and soil stabilization.
Figure 3. Types of emulsions.
Emulsification. The emulsification properties of surfactants are critical to cleaning as surfactants act to stabilize soil and oil in suspension. The forces surrounding a given water molecule are equally distributed unless the molecule is at the surface of the liquid. At the surface of a water sample at room temperature, the force of the surface tension is 0.073 Newton-meter (N-m). When surfactants are added to the room temperature solution, the surface tension is reduced to 0.025 N-m. The emulsification process is important because in water-based systems the soil is usually oil-based and is well distributed by this type of emulsion. Surfactants act to stabilize the interface between oil or particles and water in a dispersion, which is important for removing and stabilizing the oil or particles.
Only a micro-emulsion is a thermodynamically stable system. The particle sizes and distribution in a micro-emulsion are very low, so the solution appears clear. Other emulsions are not stable and soil particles do not remain in solution as they begin to settle out.
Wetting. Wetting is the ability of a liquid to maintain contact with a solid surface, resulting from intermolecular interactions when the liquid and solid are brought together. Good wetting is mandatory for an effective cleaner and happens in the presence of a gaseous phase or another liquid phase not miscible with the first phase. Wetting behavior hinges on surface tension
(see Figure 4). Adding surfactants changes the surface tension, which changes the contact angle between the liquid and the solid surface. A contact angle of 0° shows the liquid spreading across the metal surface with full wetting. A contact angle greater than 90° results in incomplete or no wetting.
Figure 4. Diagram of hydrophobic versus hydrophilic surface drops.
Foam. Liquid foam consists of small gas bubbles separated by liquid walls formed by surfactants and mostly water
(see Figure 5). High foam levels are unwanted for most metal cleaning applications. Over time, wet foam becomes dry as the liquid tends to sink. Dry foam tends to be stable as the surfactants are stabilizing the gas bubbles. Defoamer chemicals may be needed to reduce foaming.
Figure 5. Liquid foam.
The cloud point. The cloud point (CP) is the temperature at which the mixture of non-ionic surfactants starts to phase separate, and the solution becomes cloudy. This behavior is characteristic of non-ionic surfactants containing polyoxyethylene chains, which exhibit reverse solubility. In other words, cloudy solutions show low/no foam behavior. If temperature is increased, the hydrogen bonds break and the result is decreased water solubility, and the mixture becomes cloudy. If the temperature is decreased, the hydrogen bonds reform and the mixture becomes clear. A long C-chain inside the surfactant molecule tends to decrease the CP.
Metal cleaners
There are two main types of metal cleaners: aqueous cleaners or solvent cleaners. This article focuses only on aqueous cleaners, which can be divided into three types: acid cleaners (pH <5), neutral cleaners (pH 5 to 11) or alkaline cleaners (pH >11). The typical ingredients for all three types of cleaners include components for pH regulation (e.g., caustic soda, potassium hydroxide, amines, phosphoric acid), coupling agents (e.g., silicates, phosphates, carbonates, complexing agents) and surfactants (e.g., non-ionics, anionics, cationics).
Sinner’s circle is a visual representation of the four factors involved in cleaning: chemistry, temperature, mechanics and time. Herbert Sinner was a German chemical engineer who identified the four factors in 1959. Each factor takes up part of the circle with the factors interdependent, so changing one impacts the other three. For example, today, people want to use lower temperatures during cleaning to save energy, so the other three factors have to be adjusted to compensate while still achieving the desired end result.
There are three general metal cleaning applications:
•
Spray cleaning involves spraying the cleaner with high pressure onto the metal surface. The impurities are partially dissolved or emulsified by the cleaner and washed away by the high kinetic energy of the spray jet.
•
Immersion cleaning is the method of choice for parts with complex geometries (e.g., blind holes). When the metal piece is immersed in the cleaning bath, the chemical effect of the cleaner loosens the dirt and mechanical forces, like rotation or swiveling, increase the cleaning effect.
•
Ultrasonic cleaning is based on the physical effect of cavitation. Electrical signals are generated at a specific frequency. Due to the high intensity, microscopically small cavities form in the negative pressure phases. In the subsequent overpressure phase, the cavities collapse or implode and generate shock waves. This creates micro-currents in the liquid that “blast” dirt off the metal part.
The primary challenges when using surfactants for cleaning metals involve the type of soil, the type of metal and the type of application.
Under soil types, pure oils typically require non-ionic surfactants. In contrast, a more realistic soil typically involves both oil and particles (e.g., rust, graphene) and can even include burning depending on the process that created the need for cleaning. In the case of these more realistic soils, a mix of non-ionic and anionic surfactants may be required to clean the metal surface.
Depending on the metal type, with the wrong surfactant mixture, corrosion can occur. The wrong surfactant mixture can result in corrosion, while the correct surfactant mixture (e.g., a combination of anionics and amine) yields no corrosion.
The type of application also is very important. For example:
•
Spray cleaning involves cleaning via strong mechanical forces with strong alkaline or mild neutral cleaners. This application usually is fast contact, typically using non-ionics with a low CP. In these applications, foam formation can be a huge challenge and defoamers may be needed.
•
In immersion and ultrasonic cleaning, chemistry is the main “driver.” These processes typically use strong alkaline/mild neutral/acid cleaners with long contact times. Soil degreasing is very important and mixtures of non-ionics and anionics are used.
Conclusions
Surfactants are unique organic molecules that are classified based on the charge on the molecule. Modern surfactants are totally modular, consisting of two major parts— the hydrophilic part and the hydrophobic part. This unique structure influences the physico-chemical properties of the surfactant molecule, which include reducing the surface tension and emulsion formation, foaming and wetting properties and the CP point behavior of the molecule. Metal cleaning formulations are classified based on the pH value of the molecule. There are three main metal cleaning applications: spray, immersion and ultrasonic. Surfactants are critical in metal cleaning with the correct surfactant mixture improving anti-corrosion behavior, cleaning efficiency and physico-chemical properties.
Andrea R. Aikin is a freelance science writer and editor based in the Denver area. You can contact her at pivoaiki@sprynet.com.