KEY CONCEPTS
•
Development of industry standards is a collective process that requires input from industry stakeholders.
•
Laboratory data must be paired with field data for proper assessment of component health.
•
Advances in the industry propel development of new standards, tools and processes.
Crude oils, petroleum products and lubricants are highly complex materials. Enormous efforts have been spent by oil companies throughout the world to characterize their chemical and physical properties with a high degree of precision and accuracy. The explosive growth in the availability of modern analytical instrumentation in the last four to five decades has significantly helped in the task of petroleum products analyses.
1
The foundation of lubricant analytical instrumentation is to enable development of accurate and informative data that can be related to how the machine and/or lubricant may work or fail.
2 Diverse instruments support generation of different data sets, and the data sets could be used in a collective nature to create specific guidelines to analyze specific performance characteristics. There are several organizations that work on the development of various industry standards, which later are used in the field to ensure optimized performance in a specific application.
This article will give insights into the process involved in developing industry standards, field performance requirements, typically used tests and their results to ensure that the standards are maintained throughout the lubricant life.
Developing standards
STLE member Lisa Williams, digital product manager at Ametek Spectro Scientific and chair of ASTM D02 CS96 Subcommittee on In-Service Lubricant Testing and Condition Monitoring Services, recently worked on ASTM STP 1634 development. She shares that the ASTM STP 1634 was designed to highlight current developments and research in the lubricants industry that have not yet been developed into an official ASTM standard (but could be). “Research and development projects are critical to the advancement of in-service lubricant analysis. Changes and advancements in equipment design, environmental conditions and lubricant formulations make it critical for the lubricant testing industry to develop testing methods that correlate with the advancements in modern industry,” Williams says. She shares that the ASTM STP 1634 contains pertinent research and observations on monitoring phosphate esters using Membrane Patch Colorimetry (MPC), improved varnish detection methods and advanced techniques for monitoring greases, and that’s just scratching the surface of its rich content.
Williams adds: “Developing an ASTM standard is a rewarding process that can take some time to develop.” She states: “Anyone with relevant knowledge has the power to participate in creating an ASTM standard. A spirit of perseverance and time to commit to the process also are needed.”
Williams shares insights into standards development: “The ASTM D02 Committee meets twice a year, once in June and once in December, at locations (typically large cities) around the U.S. If you have an idea and supporting research that you would like to submit as a standard, we invite those individuals to present their idea at one of those meetings. From there, the group will provide feedback as to whether or not it is worth pursuing a standard. If the group feels the idea should be made into a new standard or incorporated into an existing standard, the person presenting the research typically becomes the technical contact of the standard and works with a small subset of the subcommittee (called a task group), to develop the standard and officially submit it through the ballot process at ASTM. When a standard is submitted for ballot (also known as an ‘official vote’), the standard goes out to the sponsoring subcommittee for approval. If it passes, it proceeds to the D02 main committee where a wider audience votes on the standard. Once it passes through the main committee, the draft is assigned a standard number, and it is an ASTM standard! After that, every five years the standard must be reviewed and maintained by the sponsoring subcommittee to ensure that the standard as written is still valid.”
Williams continues: “The most common changes or updates that I see during the five-year review period are around precision and bias statements relating to the standard test method as written. If something changes about the test method in the standard, it is best practice to ensure the precision and bias statement are updated according to the test method so the end-user referencing the standard feels confident following the test method.”
In Williams’ opinion the most critical aspects in developing industry standards are: 1.) soft skills and 2.) technical skills. “Regarding soft skills, the technical contact will have a much easier time (and more fun) developing a standard if he/ she develops a core team of diverse individuals that can help develop the standard before officially going to ballot for vote. This helps immensely in getting items passed quickly and any differences in opinion efficiently resolved. The other is obviously technical. He/she must have the technical knowledge and project management skills to champion the standard all the way to the end,” Williams states.
Updating standards
Aside from developing new standards, there is an emerging trend of updating already existing standards. Williams shares: “As a subcommittee chair, I am going to look for ways to incorporate new ideas into existing standards before suggesting a new standard be developed. Within the selected technical paper (STP), I think there are a lot of opportunities to do just that. I certainly will not deter the development of a new standard as the opportunity presents itself, but adding new ideas to existing standards is something that can be done more easily than drafting something from scratch. It’s the most effective way to quickly introduce new ideas (with solid supporting data) to the industry, and I believe that is our main goal at ASTM.”
There are many industry standards and tests that can assist in determining lubricant health. Some of them are more cost-effective, and some have shorter turnaround time. Some tests are used more often and are very accessible, and some tests, although extremely effective, are not so often used or readily available.
3
Test methods
STLE member Elaine Hepley, CEO and founder, Solana Consulting Services LLC, shares her insights on the most used test methods that aid in informing users about the condition of their oil: “The basics are viscosity to check if it’s providing the adequate film protection to prevent wear, particle count to verify the level of cleanliness and contamination
(see Figure 1), metal analysis to check for any wear debris, contamination and check additive levels and water to check for any moisture that is present. For engines, fuel and soot are what I would recommend doing testing on. Overall, these tests will give you a general idea of the condition of the oil and if any further action is needed.”
Figure 1. Automatic rapid particle count and air sample device analysis tester.
There also are specific tests that can tell users if the oil is not performing one of its fundamental functions. In Hepley’s opinion, viscosity is the most important test to check first to verify if the fluid is within the specified range for the viscosity grade in use. “When the viscosity is too high or too low it can indicate the oil is either being diluted with a fluid that is thinner and can thus increase friction resulting in wear or exposure to severe stress. Too high of a viscosity can be an indication of oxidation, contamination or wear. Viscosity alone can indicate an issue that can result in further being investigated to determine the root cause,” she says.
Hepley shares that some of the most underrated lab tests can give critical information to users. These are:
1.
Filter Debris Analysis, ASTM D7919. The filter serves as the kidney to the system which collects data of wear regime and contamination over a certain period. Lots of debris is captured that otherwise isn’t detect via standard analysis. This is very useful for root cause analysis. The debris is flushed from the filter and then studied under a microscope.
2.
Micropatch and Analytical Ferrography, ASTM D7690. It is the study of wear debris, contamination and varnish under a scope; both analyses specialize in the study of cut in wear particles to determine the root cause of wear generation and can even detect contamination not otherwise being detected via standard analysis. Scope analysis also can measure the size of wear in microns and can detect larger particles of wear that usually can’t be detected through elemental analysis due to size limitations.
3.
Varnish Analysis, ASTM D7843 (MPC). This helps detect the potential for varnish formation by using the CIE ΔE as a reported value. A value greater than 30 is considered to be severe. With the significant increase in varnish formation which began in turbines and is now being found in hydraulics, compressors, gears and even diesel fuel, Hepley believes this is one of the most underrated tests that also is the most misunderstood on its interpretation. When proper analysis is performed including both soluble and insoluble varnish potential, correlating with L*a*b* values is crucial to being able to understand the formation of varnish and even the root cause.
4.
FTIR Analysis Full Spectrum, ASTM D7889. When performed and interpreted correctly this test can detect when the oil begins to break down and change its chemistry. As the oil begins to oxidize there are alcohols and carboxylic acids that form and can cause the oil to lose its ability to continue to protect the equipment. It can detect water, oxidation, nitration, phenols, carboxylic acids and antiwear additives to name a few.
Oil analysis
Hepley cautions that oil analysis in the lab alone cannot identify whether a lubricant is failing. It should always be a combination of both lab and field observations/tests. She says: “Oil analysis alone can’t tell you all that is happening with the lubricant. It can be useful in determining the state of the oil; however, field tests and other tools are needed to be able to have data points of various sources to truly know if the lubricant is failing and why. It’s important to determine the root cause and work to implement a solution. Inline sensors, as well as field tests such as vibration analysis, thermography and RULER®, are some of the tests recommended to utilize to determine if the oil is failing. I believe the more data you have about the equipment, the better to help have a good grasp on the state of the oil and the machine.”
According to Hepley there are areas of concern that can easily be identified by users based on oil analysis. She says, “High wear and contamination shouldn’t be ignored. This is where scope analysis would be recommended to verify and study any presence of wear and contamination to determine root cause. Also verifying the sample draw procedure to ensure sampling tools are sterile at the time the sample was taken is essential. If the data looks suspicious don’t hesitate to request a retest from the lab to verify analysis. It is important to check flagging and commenting to ensure that the alarms and comments align with the specific type of equipment. It’s also extremely important to correctly identify the component and lubricant in use to help ensure the correct flagging criteria is being utilized for wear and contamination and check the fluid properties. Having all the correct information identified will ensure the proper analysis will take place with the sample. Lastly, if your operational environment has a unique wear regime or working conditions, check with your lab if they can provide custom flagging limits specific to the type of wear and operational regime of the equipment.”
Early warning signs
Vanda Franco, associate manager – operations (onshore), TEAM Services and Rentals W.L.L. (a Petrotec Co.) - An Al Mahhar Holding Co., based out of Qatar, shares some insights on early warning signs from her work field experience of when a lubricant may be failing: “Qatar being a peninsula in the Persian Gulf is vulnerable to extremely stressful ambient working conditions: high temperature and humidity. Under these stressed conditions both oxidative and thermal degradation can happen simultaneously and consistently in lubricants of turbo machinery/critical rotating equipment, which are the main cause of internal contamination formation, especially during the summer (July to September) when the air and water temperatures are too high. During this period, the cooling ability/capacity is limited.” She adds: “From our experience in Qatar at onshore and offshore fields, we can see that the warning signs when lubricant fails are related with oil contamination (external or internal), oil degradation/oxidation and additive depletion. Regarding the symptoms of the machines, as soon as the bearing temperature and/or vibration profile starts showing one or more spikes also can be a warning sign that the lubricant is failing, even if the oil sample results are within normal/acceptable condition. Another warning sign is when the main lube oil filter is clogging frequently
(see Figures 2 and 3).”
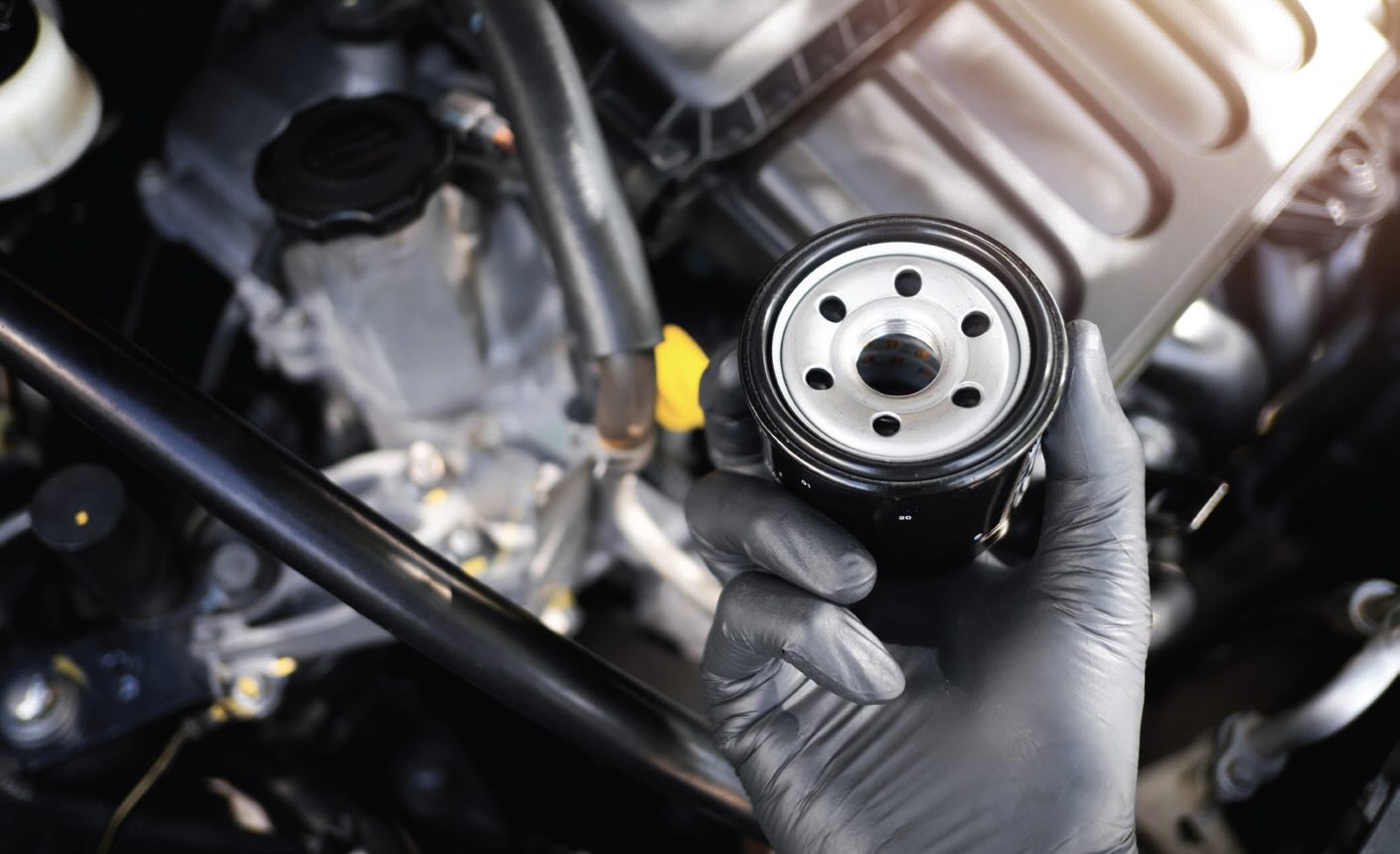
Figure 2. New car oil filter.
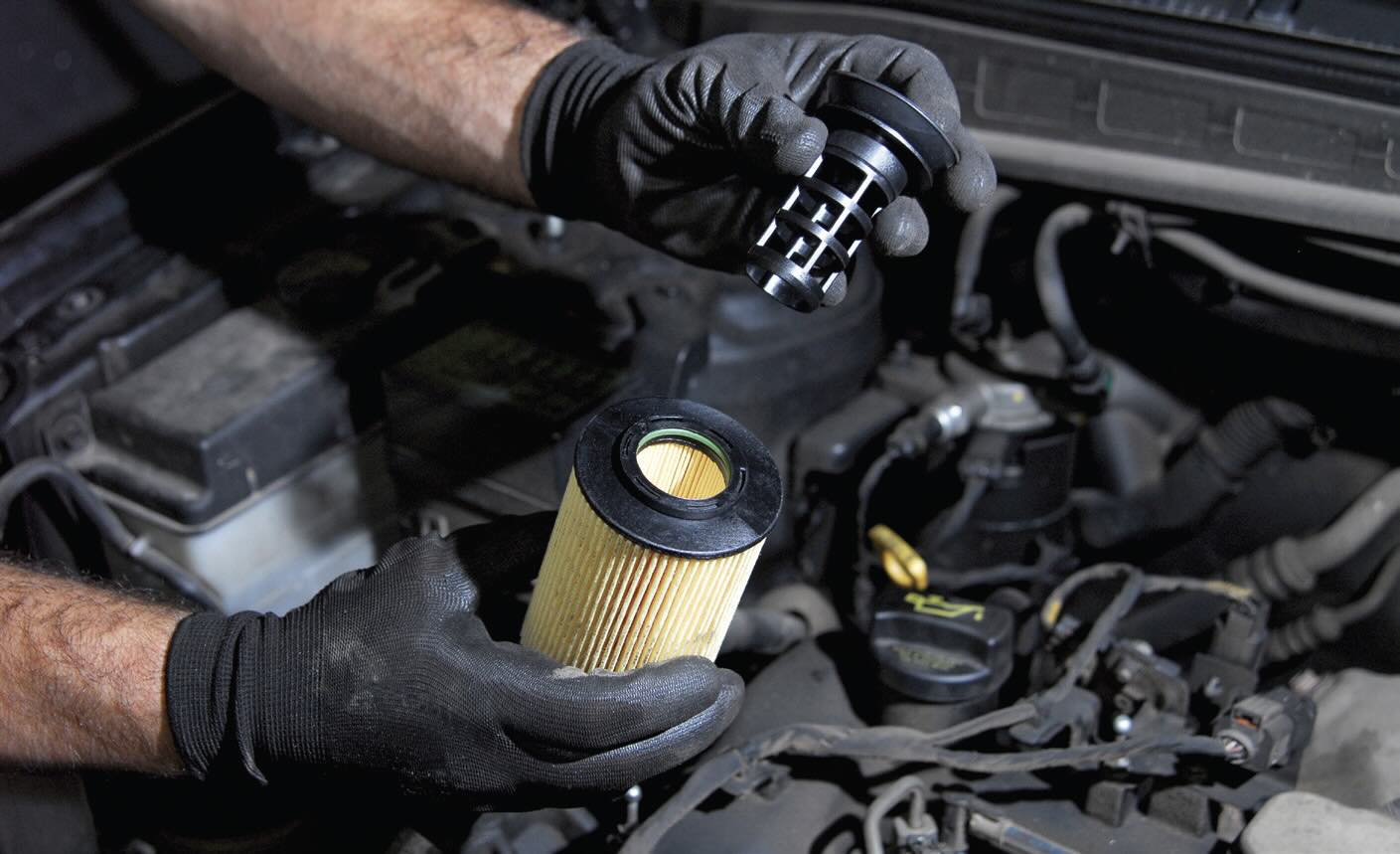
Figure 3. Removing the car oil filter.
Users can couple oil analysis and field experience to determine if a lubricant is not performing as it should. Franco says: “As we know, lubrication practices followed in the plants have a direct impact on plant and equipment reliability and when a lubricant is healthy, with no chemical degradation and with limited contamination within it, the equipment reliability can be kept and improved. Monitoring the contamination in the oil is one of the main actions all plants want to achieve to avoid problems associated with oil degradation.” She adds: “I frequently ask our clients—your lubricant and machine are talking. Are you listening to them?”
Franco says that it is very helpful to have an oil condition monitoring team working alongside a maintenance team, to understand all the maintenance activities which can affect the oil condition. Evaluating the trends of each analyzed parameter in the oil and listening to the symptoms of the machines is a must as preventive action, to avoid unexpected shutdowns. It is important to read every sample report, even with oil condition within acceptable limits, to understand if the trends are stable or if there is an increase/decrease for critical parameters to be aware of possible future failures in the machine. Most of the time, the mechanical team associates the symptoms of the machines with lubricants performance; however they cannot forget that the alignment of all parts of the machine also is important, especially when moving/replacing the bearings.
While sharing her experience, Franco says: “There was a case when the main lube oil filters of a gas turbine were clogging fast, but the oil analyses from routine sampling points were showing all parameters within acceptable levels and trends also were stable for the year prior with the exception of particle count (ISO 4406). By visual observation, the oil sample was clean.” She continues: “An investigation was performed to analyze the filter contamination for three different main lube oil filters, which showed black and large deposits
(see Figure 4). We requested to collect oil samples from the cooler and from the tank, which are not the usual sampling points—a large quantity of particles (ISO 4406) and MPC test (ASTM D7843) levels within an abnormal level have been found. Since the customer had a planned engine change for this system, we recommended to perform the oil change and take photos of all parts of the machine—cooler plates and tank were heavily contaminated with sticky varnish. 258 cooler plates had to be replaced and the tank continued with some varnish after mechanical cleaning.” In conclusion, Franco amplifies that it is important to perform investigations to find the root causes as soon as the machine shows a symptom, or the oil condition is not within acceptable limits for at least one of the parameters.
Figure 4. Filter contamination.
The top five warning signs that users can look out for as it relates to a lubricant failing, per Franco, are:
1.
Oil contamination—internal (machine wear and oil degradation by-products) or external (dust, humidity, salted water [sodium content increase—ASTM D5185])
2.
Oil oxidation—sludge and varnish (ASTM D7843)
3.
Additive depletion—antioxidants level (ASTM D6971)
4.
Spikes in lubricant temperature
5.
Spikes in bearing temperature and/or vibration
There are supplemental technologies which Franco uses, in addition to her standard toolkit, that help detect the onset of a lubricant failure: “I use ASTM D4378, Standard Practice For In-Service Monitoring Of Mineral Turbine Oils For Steam, Gas, And Combined Cycle Turbines, where different technologies are identified. In addition, online oil condition monitoring technologies that have been developed to be used in the field, to complement the analyses performed by each laboratory, are another tool. Ultrasound data collectors are another technology as they detect the vibration in different parts of the machine, if present, which cannot be detected by the usual systems installed,” Franco says.
Summary
Industry advances significantly impact and enable next level development of formal standards for the lubricant industry. These advances also impact lubricant formulation, data analytics, delivery, software and asset management.3 Experts already use computerized software systems such as machine learning and artificial intelligence to take an understanding of lubricant performance to the next level. This paired with innovation in hardware systems such as sensor technologies enables “live” analysis of many lubricants properties. The need for industry standards remains high due the need to continue optimizing effectiveness and utilization of resources, especially with the variety of new applications coming to the industry at a never seen before rate, not to mention sustainability goals, an aspiration the industry is gearing toward.
REFERENCES
1.
Nadkarni, R. K. (2000),
Petroleum Products and Lubricants, ASTM International.
2.
Villalba, M. and Williams, L. (Eds.). (2022),
Standard Guides and Practices that Support the Lubricant Condition Monitoring Industry, ASTM International.
3.
Mathura, S. (2020),
Lubrication Degradation Mechanisms: A Complete Guide, CRC Press.
Dr. Yulia Sosa is a freelance writer based in Peachtree City, Ga. You can contact her at dr.yulia.sosa@gmail.com.