Meet the Presenter
This article is based on a webinar titled In-Situ SEM Tribological Testing of 3D-Printed Micro/Nano-Textured Surfaces. Hosted by the American Society of Mechanical Engineers’ (ASME) Tribology Division and presented by STLE member Dr. Mahyar Afshar-Mohajer on June 28, 2023, the session covered how leading-edge in situ testing steers the development of precisely controlled tribology-friendly surfaces. Courtesy of STLE, this article captures the core insights from this ASME-organized event. For more technical content from the ASME Tribology Division Webinar Series, visit the ASME Tribology Division’s website here.
Afshar-Mohajer is a postdoctoral Fellow at the Department of Mechanical Engineering, University of Arkansas, where he works with STLE Fellow professor Min Zou in the Nanomechanics and Tribology Laboratory (NMTL). His research includes 3D printing of micro/nano-textured surfaces and in situ observation of their friction and deformation inside an SEM for direct observation of their micro/nanoscale building blocks subjected to normal and tangential loading. You can reach him at mafsharm@uark.edu.
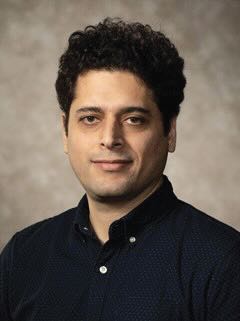
Dr. Mahyar Afshar-Mohajer
KEY CONCEPTS
•
Key technologies such as in situ SEM instrumentation and 3D printing are expanding the field of surface texturing.
•
New 3D printing methods, such as two-photon lithography, enable a level of precision never before available.
•
Coupled with in situ SEM testing and verified through finite element analysis, surfaces with 3D printed micro-structures deliver a level of surface control that is expanding tribological possibilities.
By reducing the actual area of contact between two surfaces, texturing decreases adhesion and friction. Surface functionalities including superhydrophobicity, superhydrophilicity and structural color also can be controlled by surface texturing. A common example of something that is superhydrophobic due to natural texturing is a lotus leaf, which is covered with micro-pillars and nano hairs
(see Figure 1).
Figure 1. Structural elements of a lotus leaf.
Textured surfaces suffer from inherent issues due to the increased pressure resulting from surface area reduction. In the past, this has limited their application. So, a better understanding of textured surface tribology is needed. This can be achieved by better control over manufacturing and testing of micro/nano-textured surfaces down to their micro/nanoscale building blocks.
Three of the most common among many texture fabrication methods are:
•
Soft-lithography
•
Laser ablation
•
Photolithography-based
Generally, the problem with photolithography (and laser ablation) is that there is little control over their 3D structure. A new method that holds much promise is two-photon lithography.
This article is based on a webinar presented by STLE member Dr. Mahyar Afshar- Mohajer, postdoctoral Fellow at the Department of Mechanical Engineering, University of Arkansas, and the Tribology Division of the American Society of Mechanical Engineers (ASME) titled In-Situ SEM Tribological Testing of 3D-Printed Micro/Nano-Textured Surfaces. See Meet the Presenter for more information.
Two-photon lithography
With two-photon lithography, there is no limit to what can be designed and printed. It is essentially high-resolution 3D printing. The high resolution is achieved through two-photon absorption, which restricts the exposed photoresist to a very small volume. To speed up the process, soft lithography was used to replicate copies of the master surface fabricated via two-photon lithography
(see Figure 2). Two-photon lithography can be used to create exacting micro/nano-hierarchical textures that confirm finite element modeling of the structures. The result is a better fundamental understanding of the relevant underlying mechanisms.
Figure 2. Two-photon lithography fabrication method, complemented with soft lithography.
Using a digital optical microscope can be especially useful for macroscale monitoring of tribological tests, for example when using a universal mechanical tester. It yields accurate data on the movement of the counterface. However, it would be better to also see the interface to shed light on what happens to the smallest structures during tribological testing. This is especially true now that 3D printing enables micro-nanostructures and can be achieved through in situ scanning electron microscopy (SEM) testing of such structures.
Three sample studies
Following are three representative studies of
in situ SEM tribological testing of 3D printed micro/nano-textured surfaces.
Study 1: Multi-scale in situ tribological studies of surfaces with 3D textures fabricated via two-photon lithography and replica molding
The purpose of the first study was to look at the effect of the three dimensionality of the structures’ shape on tribological behavior of the textures made up of those structures; the surfaces were printed using two-photon lithography and then their tribology was examined. The data comes from both macroscale and microscale tribological testing.
By implementing a micro/nanoscale additive manufacturing technique known as two-photon polymerization, it became feasible to create textures with exact control over their shape, dimensions and position. This facilitated a methodical examination of the consequences of texture three-dimensionality through the comparison of 2.5D textures (rods and cylinders) with 3D textures cones)
(see Figure 3).
Figure 3. Surface morphology of various textured surfaces.1
Researchers wanted to directly observe what was happening to the individual structures, which is where carrying the tests inside SEM was key. In terms of friction values, the macroscale and microscale generally followed the same trend. Micro-cone textures showed the lowest friction because the area at the top of the cones was able to be reduced. Tall and thin structures (rods) ended up having the highest friction because at some point they failed and came very close to being flat.
The study showed that the ability to fabricate textured surfaces with high resolution and accurately control the textured 3D shape are the keys to designing and engineering optimal textured surfaces without compromising their performance and durability. Textures made up of actual 3D structures, such as micro-cones, not only reduced the friction by reducing the real area of contact at their tip but also had the strength and deformation resistance provided by a large base to support loads. Furthermore, the friction reduction resulted in a smooth movement of the surfaces in contact.
In contrast, surfaces with higher friction values (2.5D textures) experienced significant irregularities during their movement—which is one of the factors contributing to their inferior durability. This multiscale study provided a thorough understanding of the underlying mechanisms. The use of
in situ SEM lateral force measurement on textured surfaces provided unprecedented insight into the relationship between the deformation and friction of the textures that could lead to engineering and optimization of such textures in the future.
Key learnings include the following:
•
3D texturing
-
With a reduced area of contact at the tip, there is reduced adhesion and friction.
-
With reduced friction, there is a smoother counterface movement.
-
Smooth sliding and a larger base lead to greater durability.
•
Microscale
in situ tests provided significant insight into the counterface-texture interaction at very small scales, i.e., the relationship between deformation of textures and friction
(see Figure 4).
Figure 4. Bending of long hairs during sliding.2
Study 2: Understanding the friction and deformation behavior of micro/ nano-hierarchical textures through in-situ SEM observation and mechanics modeling
The second study used two-photon lithography to create the structure, which was inspired by hierarchical structures in nature, such as a lotus leaf, that have micro pillars and are covered by nano hairs. The width of the nano hairs are about 300 nanometers (nm). The short hairs are 400 nm long and the longer hairs are about 1 micron long. The long hair contributes to the surfaces becoming superhydrophobic. Adding the long hairs on top of the micropillar significantly increased the water repellency and reduced contact angle hysteresis. With laser scanning confocal microscopy, researchers were able to observe that the reason for this was that the long hairs produced an extra level of air cushion on the top of micro/nano-hierarchical structures.
Friction values from these tests showed how the contact area and hence the friction at the top of the structures was a function of the length of the nano hairs. The highest friction occurred where there were no hairs. The lowest friction occurred where the hairs were shorter. The long hair, because it tends to fall, creates a surface that is close to flat and has a friction value between surfaces with no hair and short hair.
The fabrication accuracy was matched with the accuracy of the small-scale tribological testing of the textures inside a SEM, which not only enabled precise targeting of individual hierarchical structures, but also provided direct observation of their deformation. This resulted in the observation of unique phenomena due to the hierarchy, such as the coupling effect of the first-level structure (nano hair) deformation to the bending of the second-level structure (micro-pillar base) before or after sliding was initiated.
Specifically, different nano hair heights affected the contact area, and hence the lateral force and the degree of micro-pillar bending. Moreover, the buckling of the long hairs caused a lateral force to bend the micro-pillar. Another interesting phenomenon observed was that the bending and buckling of the long-hair structures resulted in assistive forces for sliding and hence negative lateral force. This could happen even before the start of programmed sliding in the case of buckling of long-hair structures. This level of control and accuracy over fabrication and testing, which cannot be accomplished by bulk testing methods, promises excellent insight for studying hierarchical textures. It enables a fundamental understanding of the surfaces at their individual building block level.
Researchers collaborated with the University of Colorado Boulder to replicate the results using finite element analysis (FEA), which provided additional insight.
Key learnings include the following:
•
The effect of increasing the nano hair length on the formation of multiscale air-pockets resulting in their superhydrophobicity was directly observed.
•
Variations in nano hair length determined the deformation of the supporting micropillar under shear and normal loading.
•
The effect of nano hair bending on the changes in friction during sliding via providing assistive and resistive forces was observed.
•
Development of friction forces before sliding, caused by buckling of nano hairs under normal loading, was observed.
Study 3: 3D printing of micro/nano-hierarchical structures with various structural stiffness for controlling friction and deformation
The third study included micropillars with three different base dimensions to modify their stiffness (small-base, medium-base and large-base micropillars) in addition to the three different hair lengths (no-hair structures, which was made up of only micropillars, short-hair structures that had 400 nm long nano hairs and long-hair structures with 1 micron long nano hairs), resulting in micro/nano-hierarchical structures with nine different effective stiffness values to see how that affects their deformation, friction and water repellency
(see Figure 5). In all the three different micro-pillar base dimension cases, there was a steady state region of friction, but the sliding point varied. Structures with a smaller base took longer to slide than those with a larger base.
Figure 5. Severe deformation of small-base structure.3
Putting the data from this and the previous study together, researchers were able to see that the stiffness and friction can be controlled by hair length and the width of the micro-pillar base, along with other variables.
The versatility and resolution of two-photon lithography enabled control over the 3D shape and dimensions of fabricated micro/nano-hierarchical structures. This control resulted in the ability to increase the stiffness and thus decrease the deformation of the structures. Additionally, the 3D variations in the shape of the structures affected the onset of sliding motion, friction, friction-normal load relationship, water contact angle (WCA) and the interplay between the micro-nanoscales’ structures. Stiffer structures showed reduced lateral and normal deformation, earlier onset of relative sliding motion and a more linear relationship between the friction force and the applied normal load.
The addition of nano hairs reduced the effective stiffness and contact area of the structures. Noteworthy interplays across the micro-nanoscale structures were observed. The small-base micropillars with long nano hairs on top experienced complete bending under the smallest applied normal load while no-hair and short-hair structures did not, showing how the nano hair affected the behavior of the micropillar. Moreover, it was discovered that as the micropillar base dimension increased, it took a larger applied normal load for the long nano hair to buckle. This, together with the fact that larger micropillar base dimensions did not reduce the WCA, provides a solution for addressing the inherent challenges of developing surfaces with high WCA and mechanical stability. The combination of small-scale 3D printing (two-photon lithography), in situ SEM monitoring of friction tests and FEA modeling resulted in discoveries that can be used to guide the design of surfaces with precise properties. Using faster fabrication methods, for example replication of 3D printed structures and surfaces using soft lithography, can speed up the fabrication process while maintaining the accuracy, resolution and versatility of 3D printing.
As with the previous study, researchers collaborated with the University of Colorado Boulder to replicate the results with FEA.
Key learnings include the following:
•
Increasing the stiffness resulted in:
-
Reduced deformation
-
Earlier onset of the sliding motion
-
A more linear relationship between the friction force and the applied normal load.
•
Interplay across micro-nanoscale structures resulted in increased micropillar stiffness delaying the buckling of the long nano hair on top.
•
Wettability, stiffness and friction can be controlled for the desired application. The ability to fabricate structures with optimal control, using methods like two-photon lithography, opens up a world of surface texture fabricating possibilities. Thanks to the latest instrumentation, the behavior of these surface structures can be observed in detail. All of this is leading to the design of a better set of structures for the next generation of surfaces.
REFERENCES
1.
Afshar‐Mohajer, M. and Zou, M. (2020), “Multiscale in situ tribological studies of surfaces with 3D textures fabricated via two‐photon lithography and replica molding,” Advanced Materials Interfaces, 7 (13), 2000299.
2.
Afshar‐Mohajer, M., Yang, X., Long, R. and Zou, M. (2022), “Understanding the friction and deformation behavior of micro/nano-hierarchical textures through in-situ SEM observation and mechanics modeling,” Tribology International, 165, 107271.
3.
Afshar‐Mohajer, M., Yang, X., Long, R. and Zou, M. (2023), “3D printing of micro/nano-hierarchical structures with various structural stiffness for controlling friction and deformation,” Additive Manufacturing, 62, 103368.
Jeanna Van Rensselar heads her own communication/public relations firm, Smart PR Communications, in Naperville, Ill. You can reach her at jeanna@smartprcommunications.com.