Application-specific lubricant tests
By Dan Holdmeyer, Contributing Editor | TLT Lubrication Fundamentals June 2024
Industry organizations have developed standardized tests for lubricant characteristics and performance.
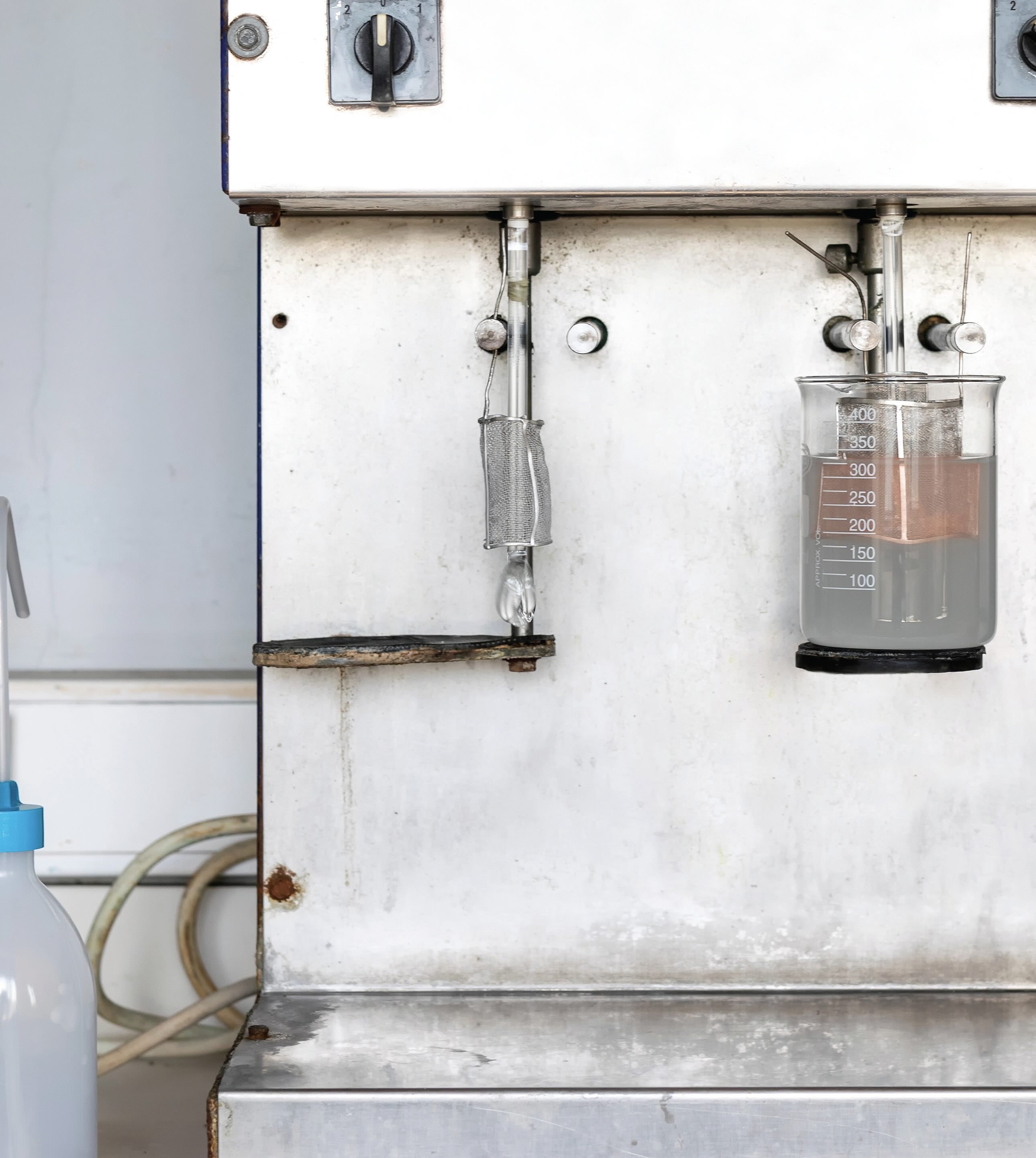
Many OEMs and end-users rely on lubrication industry common tests and specifications to help identify what lubricant can be used in certain applications, such as turbine, hydraulic and industrial gear applications. Each of these applications has unique challenges and requires certain additives as we discussed in the TLT Lubrication Fundamentals articles titled “How additives finish the lubricant” and “More on how additives finish the lubricant,” in September and October 2022, respectively.
Not all additives perform the same. Lubricant performance also varies greatly depending on the amount of additive used, but more additive does not always improve performance. Sometimes more of an additive may give the opposite effect expected from the additive or one additive may interfere with the performance of another additive in the finished lubricant. Interestingly, some additives may act together to give higher performance than expected from simply adding together each additive’s performance level. This is called a synergistic effect. Furthermore, many additives perform differently depending on the base oil used in the finished lubricant.
Fortunately, out of necessity, industry organizations such as ASTM, DIN and ISO have collaborated to develop standardized tests to also differentiate lubricant performance levels in desired characteristics. These tests are beyond the physical and chemical tests such as viscosity, viscosity index, flash point, pour point and acid number. Some of the common performance tests used in most applications include rust prevention, copper strip corrosion and foaming characteristics as we discussed last month in the TLT Lubrication Fundamentals article titled “Testing and specifications.”
Here are some of the additional common lubricant performance tests used for turbine applications.
Turbine Oil Oxidation Stability Test, ASTM D943, is frequently referred to by its acronym TOST (long o sound). It was developed to indicate the oxidation life of oxidation inhibited turbine oils. A tube with a specified quantity of the tested oil is exposed to catalyst steel and copper coils, water and elevated temperature while oxygen is bubbled through the sample. At designated intervals, samples of the oil are taken, and the acid number (AN), ASTM D974, is measured, and the test is terminated when the tested oil AN reaches 2.0 mg of KOH per gram. The result is reported in hours, as in the number of hours the test ran to reach an AN of 2.0. ASTM D974 was designed to end at 10,000 hours when the periodic sampling required depletes the sample volume for testing. If the sample has not reached an AN of 2.0 by the end of the test a value of >10,000 hours is reported. The test is indicative of an oil’s oxidation resistance. It does not mean the oil will last in an actual turbine 10,000 hours, or whatever is the test result. There are many variables that affect oil life in the application.
Some have, somewhat controversially, given results with actual numbers >10,000 hours by running parallel tubes of the sample, pulling samples from the second tube once the first tube is depleted of oil sample.
TOST is sometimes, also controversially, used to indicate quality and life of hydraulic oils. The concern is that TOST is designed for turbine oils, and the test is terminated when the AN reaches 2.0. AN is used to indicate oil oxidation but AN also can be affected by additive content. Not all hydraulic oils have the same starting AN. Some hydraulic oils’ AN range from 0.17 to 0.6, depending on the type and level of additive, whereas turbine oils typically range from 0.05 to 0.1.
Rotating Pressure Vessel Oxidation Test, ASTM D2272, is commonly called RPVOT. Previously, this test was called the RBOT for Rotating Bomb Oxidation Test. Supposedly, the name was changed because the Transportation Security Administration (TSA) would confiscate RBOT equipment being shipped via plane because of the term “bomb” in the name.
The RPVOT is a relatively rapid oxidation life test, used for comparing oxidation life of new oils with similar additive levels and base oils. It can be used to compare oxidation life of turbine, hydraulic, gear and transformer oils. Because the RPVOT measures oxidation life in minutes versus hours with TOST, it also is used to determine remaining life of in-service oils.
The RPVOT procedure involves putting the oil sample in a glass vessel with water and a copper wire catalyst. The vessel is pressurized and rotated in a preheated chamber. The pressure is monitored until it reaches a specific level, and the test is terminated when the oil oxidation absorbs the oxygen in the vessel, and then the pressure drops 25 psi from its high plateau level. High quality turbine oils report an RPVOT in the 1,000-minute range. Used oil results are compared to the new oil RPVOT to determine when the used oil has reached the end of its useful life.
Air Release, ASTM D3427, is a different metric than foaming, which forms on the surface of the oil level. Air entrainment is in the oil. It reduces lubricant film protection and causes “sponginess” in turbine and hydraulic systems. Air is bubbled through the oil at a specific pressure for seven minutes. The oil density is then measured until the sample oil density reaches 99.8% of the oil’s initial density, and the time to get there is recorded. The test is terminated after 30 minutes, whether or not the oil’s density has returned to the initial density. An ISO Viscosity Grade 46 turbine oil would typically have an air release time of seven minutes.
Water Separability, ASTM D1401, is particularly important in steam turbine and hydro-turbine applications due to the potential for water contamination. The water needs to separate from the oil so it can be decanted from the system reservoir. Oxidation resistance and air release are important lubricant performance characteristics in all turbine applications.
Water separability is measured in a graduated cylinder with 40 ml of oil and 40 ml of water mixed for five minutes. The volume of oil, water and emulsion is measured until 3 ml of emulsion remains and the time to get to 3 ml of emulsion is recorded. The results are reported in milliliters of oil/ water/emulsion at how many minutes to get to 3 ml, or 0 ml, of emulsion. A good quality turbine oil might report 40/40/0 at less than 20 minutes.
Four Square Gear, ASTM D1947, also referenced as “FZG,” DIN 51354, is rarely required for U.S.-based turbines (see Figure 1); however, European turbines are connected via a gearbox to their generators and thus need to demonstrate gear wear protection. Mild extreme pressure (EP) or anti-scuffing performance is measured by ASTM D1947 and typical geared turbine applications require a failure load stage 6-8. A different ASTM or DIN test protocol is used for industrial gear oils, and they typically require a failure load stage 12 or higher.
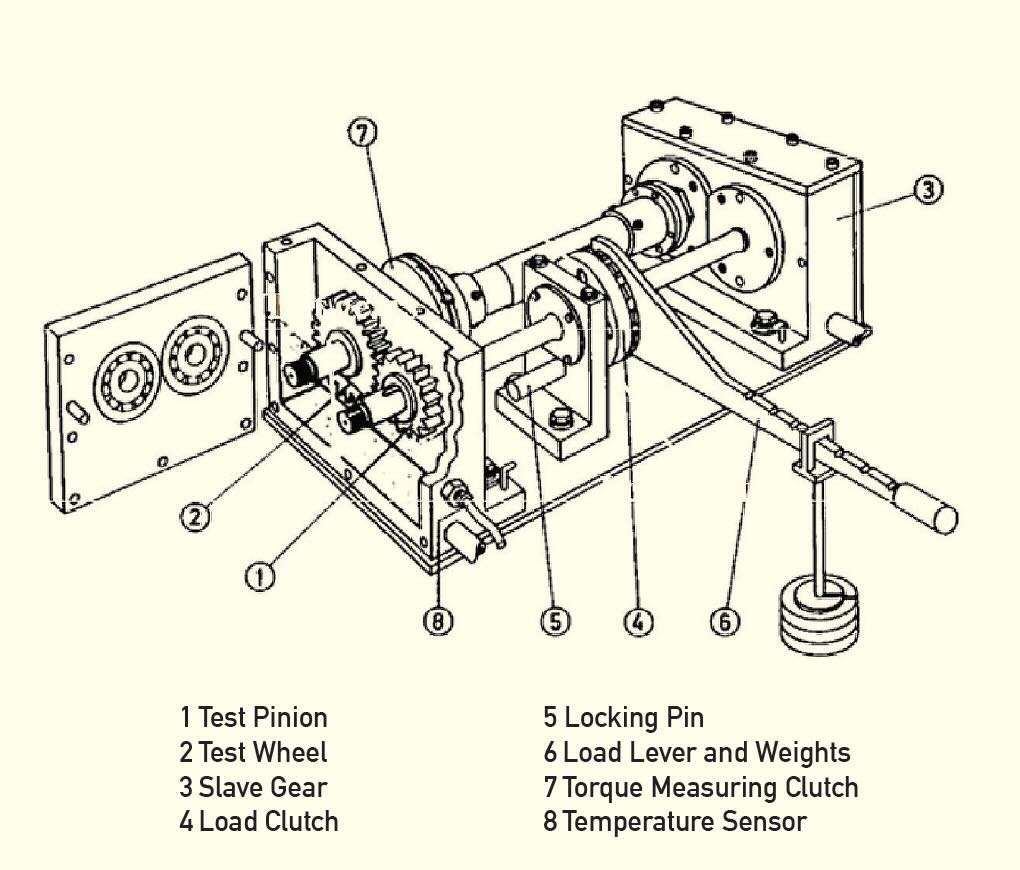
Figure 1. FZG or four square gear test rig. Figure courtesy of Faruck, A. A. M., Hsu, C.-J., Doerr, N., Weigand, M. and Gachot, C. (2020), “How lubricant formulations and properties influence the performance of rotorcraft transmissions under loss of lubrication conditions,” Tribology International, 151, 106390, https://doi.org/10.1016/j.triboint.2020.106390.
The FZG test is a gear set, with mismatched gear teeth profiles to enhance the discrimination or severity of the test. The test gear set is run for 15-minute intervals at a set speed, immersed in the test oil at a specific temperature. The gear teeth are examined and weighed after each interval, or load stage. Failure at a load stage is when 20% of the pinion gear flank-area exhibits scuffing or the pinion gear has 10 mg of weight loss. There are a maximum of 14 stages in the test.
Lubricant cleanliness is important in all lubrication applications. Turbine and hydraulic applications require the cleanest oil, relative to gear and engine applications. Cleanliness levels are reported via ISO Cleanliness Code ISO 4406. Turbine and hydraulic oils might be around an ISO Cleanliness Code of 17/15/12, whereas gear oils might be around 18/16/14. Specific components and operating conditions will change cleanliness requirements. Oil cleanliness is a whole topic of discussion of its own, too complex for a succinct discussion here to give a clearer understanding of it.
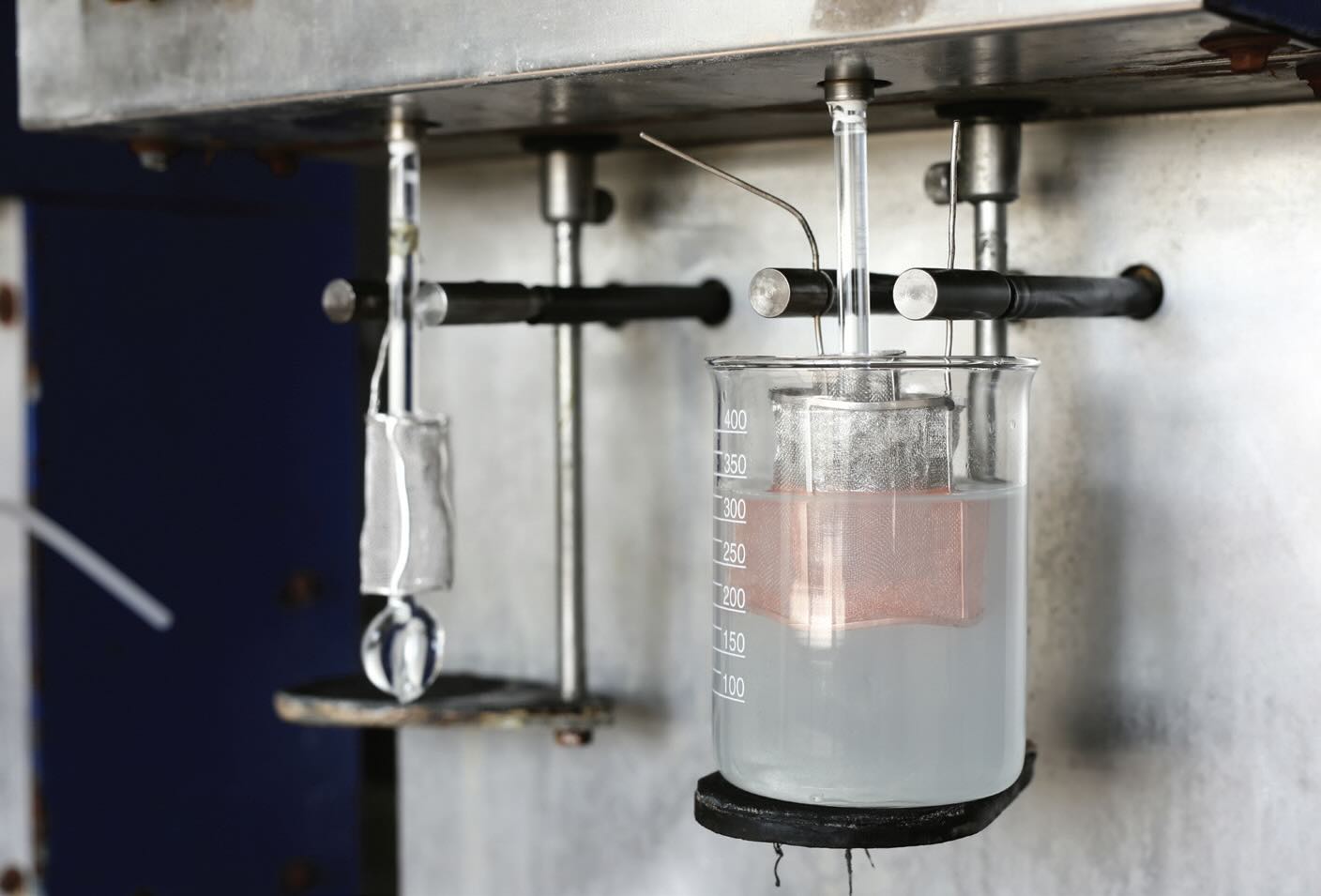
Common lubricant performance tests used for hydraulic application in addition to those used for turbine applications are primarily wear tests supported by the hydrolytic stability test to determine how stable the antiwear additives are in the presence of water contamination. Unstable additives in the presence of water decompose into salts that drop out of solution leading to clogging of valve orifices and filters.
Hydrolytic Stability, ASTM D2619, uses a six-ounce beverage bottle. I’ve typically seen an old fashioned 6-oz Coca- Cola® bottle used with a 3:1 mixture of oil: water, and a copper strip inside. The capped bottle is inserted into a heated oven and rotated for 48 hours. At the end of the test, the following measurements are made—the oil viscosity change, the AN of the water and the copper strip weight loss. Water ANs less than 4.0 mg of KOH and less than 0.2 mg/cm3 copper strip weight loss is a pass.
The Accelerated Hydraulic Pump Test, ASTM D2882, originally the Vickers 104C pump test, measures the wear protection performance of hydraulic fluids in vane pumps under server operating conditions. Vickers was an early leading hydraulic vane pump OEM, and the Vickers 104C pump test was so ubiquitous that ASTM established it as an industry standard test for the world to be able to run the test.
The test’s vane pump ring, vanes and bushings are weighed prior to assembling and testing. The pump is initially operated at 1,000 psi until the operating temperature reaches 150 ºF, when the operating pressure is adjusted to 1,900 psi for the 100-hour test. The vane pump cartridge is then removed, and the ring, vanes and bushings are re-weighed. The difference in the total weight of the parts is reported in milligrams. A quality hydraulic fluid will not have more than 30 mg of wear.
A second antiwear performance test is also from Vickers. The Vickers 35 VQ- 25 tests fluid performance in vane pumps at 3,000 psi versus 1,000 psi in the ASTM D2882, and uses three separate vane pump cartridges operating at specific temperatures, flow rates and rpm. At the end of the test the vanes cannot have more than 15 mg of weight loss and the ring is allowed up to 75 mg of weight loss for a successful fluid pass. The Vickers 35 VQ pump test is not an ASTM test but is widely used in the industry (see Figure 2).
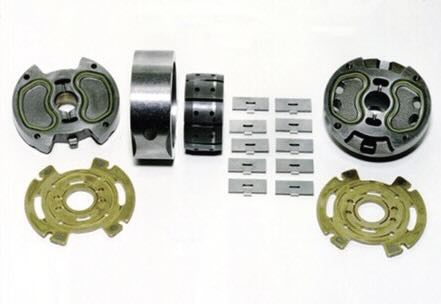
Figure 2. Vickers 35 VQ pump test. Figure courtesy of the Basic Lubrication Course, STLE Annual Meeting.
The Bosch Rexroth RA and RE 90220 and the Parker Hannifin (Denison) HF-0, HF-1, HF-2 and T6H20C are a few of the other commonly used OEM specifications to identify high quality hydraulic fluids.
DIN 51524 Part 1 Type HL, Part 2 Type HLP or Part 3 Type HVLP are often used in the industry and set the minimums and maximums for the common tests discussed previously. DIN 51524-1 Type HL does not require antiwear protection testing, whereas DIN 51524-2 Type HLP includes an FZG of Stage 10 and the Vickers 35 VQ pump test. DIN 51 524-3 HVLP adds a minimum viscosity index (VI) of 140 for ISO VGs 15 through 68 and a VI of 120 for ISO VG 100.
Next month we will discuss the unique tests for industrial and automotive gear applications. Spoiler alert: it is more than just adding EP or anti-scuff additives to handle the extreme loads.
Dan Holdmeyer is retired from Chevron Lubricants and is based in Washington, Mo. You can reach him at dan.holdmeyer@gmail.com.