Meet the Presenter
This article is based on a Webinar presented by STLE Education on March 8, 2023. Eliminating Varnish-Related Failures Through Lubricant Chemistry Management is available at www.stle.org: $39 for STLE members, $59 for all others.
Dr. Matthew G. Hobbs is the manager of research, development and technical services at EPT Clean Oil. EPT is a global leader in the field of lubricant management, working with users to provide sustainable lubricant contamination solutions in critical industrial applications. Dr. Hobbs is an active contributor to the turbine oil-related committees within STLE, ASTM and ICML. Before joining EPT, he obtained his doctorate degree in synthetic chemistry from the University of Calgary and was the general manager of a national oil analysis laboratory. You can reach him at mhobbs@cleanoil.com.
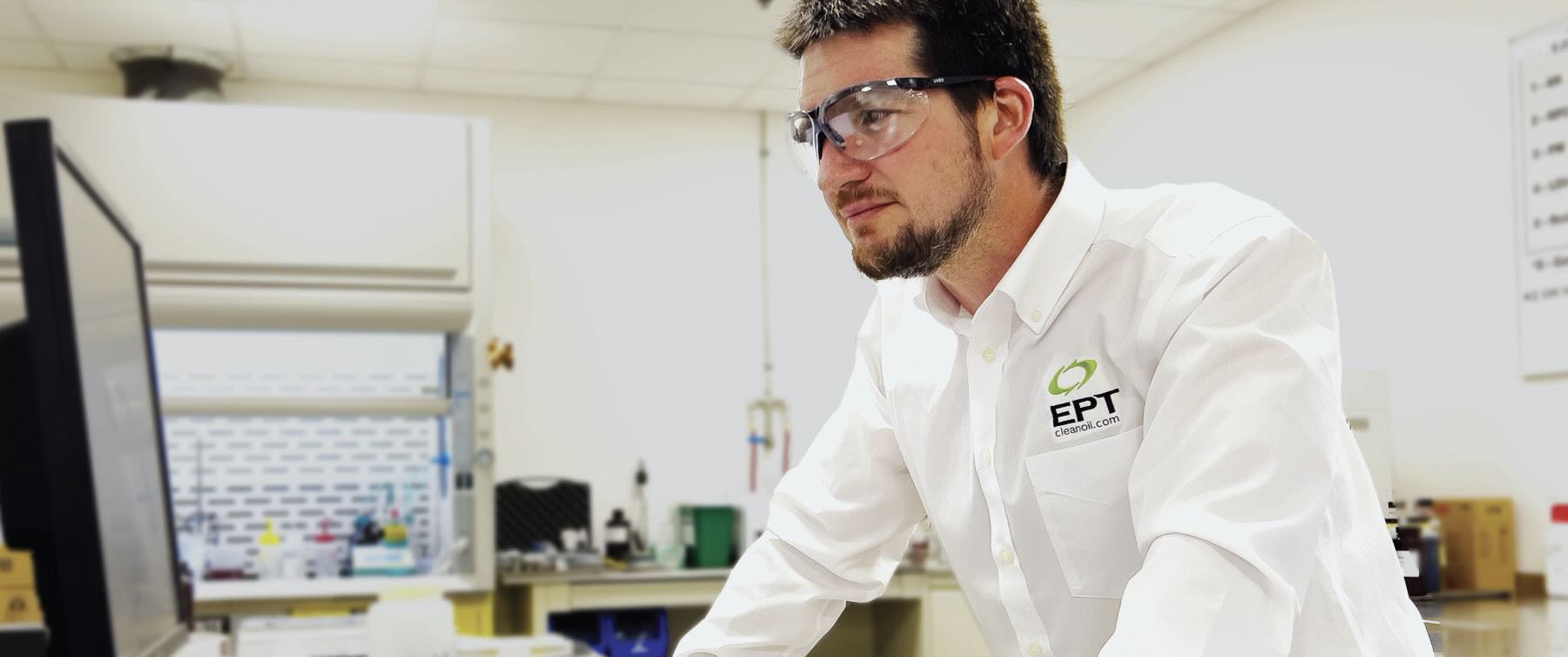
Matthew G. Hobbs
KEY CONCEPTS
•
Treating lubricants like assets instead of treating them like consumables provides a better, more cost-effective, more sustainable approach to lubricant maintenance and management.
•
Lubricant chemistry management uses ion-exchange resin to better manage and maintain lubricants by removing breakdown products so that the lubricants do not need to be replaced.
•
Removing the breakdown products and varnish from lubricants reduces both maintenance costs and environmental waste.
•
The cost of a lifetime of ion-exchange filtration is typically less than the cost of a single oil-related equipment failure.
While turbine oil maintenance is recognized as being essential, many programs lack the basic information and tools to maintain their lubricants within specification. Existing lubricant maintenance is typically reactive, uses outdated filtration technology and does not target the root cause of most lubricant and mechanical failures: oil breakdown and subsequent varnish formation.
This article introduces lubricant chemistry management, which is a modern, sustainable approach to turbine oil maintenance that eliminates the possibility of varnish-related equipment failures. Lubricant chemistry management offers users technical, cost and environmental advantages relative to alternative strategies, which may be competitive or complimentary. Unlike traditional approaches that result in varnish accumulation and deteriorating oil quality over time, this approach maintains lubricant quality in ideal condition from day 1, improving performance and eliminating common issues. By doing so, lubricant chemistry management maximizes equipment performance, increases return on investment, improves maintenance predictability and reduces the impact of power generation, allowing for more sustainable turbine operation.
This article is based on an STLE Education webinar presented by STLE member Dr. Matthew G. Hobbs, manager of research, development and technical services at EPT Clean Oil, titled Eliminating Varnish-Related Failures Through Lubricant Chemistry Management. See Meet the Presenter for more information.
Hobbs shares a case study where a pipeline operator implemented fleetwide lubricant chemistry management. The company had 80 turbo-compressors spread across North America and decided to improve their fluid filtration systems using ion charge bonding (ICB) ion-exchange resins. This improved maintenance program saved the company $97 million in maintenance and fluid replacement costs over the 37 years this approach has been followed.
1 In addition, it prevented 14.7 million kg of carbon dioxide equivalents (CO
2e) from being released into the atmosphere.
1
Current maintenance practices
The current outdated approach to lubricant maintenance focuses almost entirely on particle filtration and water removal. While it is important to keep oils clean and dry, particle and water levels are not the basis for condemning lubricants. Instead, a lubricant is typically condemned when it chemically breaks down.
Hobbs observes that oil analysis is key to understanding the chemical condition the fluid is in, but current oil analysis programs often miss key tests that would allow the oil’s remaining lifecycle to be better managed. Current approaches to oil maintenance also make few considerations for sustainability. Instead, the oil is treated like a consumable, where it is used until it degrades and is not usable, and then is simply discarded. However, treating turbine oils in this manner is not a sustainable behavior and is a reactive approach to maintenance.
Hobbs shares a case study, illustrating the current “business-as-usual” approach to turbine oil maintenance. This case study examined a Frame 9 gas turbine at an oil and gas facility where the oil is treated as a consumable and replaced on a typical two to five-year lifetime. While the site kept the lubricant clean and dry, they did not manage their lubricant’s chemistry. Oil breakdown products accumulated over time, leaving the in-service fluid in sub-optimal condition, and increasing the risk of oil-related failures. In fact, it was normal for this facility to experience 24 hours of unplanned downtime per year as a result of these oil-related issues. This translated into $368,640 in annual loss. Over the 25-year turbine lifetime, this is predicted to result in $9,216,000 of total losses. Clearly, this reactive approach to oil maintenance is a costly way to do business.
Lubricant chemistry management
Business as usual obviously isn’t good enough, but Hobbs notes that this does present an opportunity. Lubricant chemistry management is a way to operate more reliably, profitably and sustainably. Hobbs presents a two-pillar approach to lubricant chemistry management. The first pillar is oil analysis, which involves running the right tests in the right way and acting on the results. This oil analysis is a window into the lubricant’s chemistry, so that problems can be identified and then proactively fixed. The second pillar is applying maintenance budgets toward the actual cause of oil failures and preventing them, rather than paying to address these failures reactively. Sadly most lubricant programs are not effectively managing their lubricant chemistry.
As described in the first pillar, oil analysis is a key part of maintenance programs; however, many facilities rely on third-party labs to establish their test packages, test their samples and interpret their results. The value of these programs depends on whether the right tests are being run in the right way and the end-user understanding and acting on results.
To get value from an oil analysis program, the end-user needs to understand the program. To reach understanding, Hobbs identifies key questions to guide their oil analysis interpretation:
•
Will this oil do its job? In this regard, the oil’s physical properties are the most important, especially its viscosity. If the fluid becomes too thick or too thin, problems arise.
•
Could the equipment fail imminently? Are there contaminants present that could cause imminent equipment failure? This includes looking at particles, water and metals present in the oil.
•
Is the oil’s chemistry failing? Varnish forms as oil breaks down and is the primary cause of oil-related failures. Unfortunately many laboratories don’t routinely test for this harmful varnish and its precursors.
Routine third-party lab reports typically address the first and second questions, but most fail to adequately address the third question.
Varnish management
Hobbs notes that varnish, the result of unmanaged oil breakdown, is the reason oils are condemned. Varnish is the most common cause of unplanned gas turbine downtime. Varnish can lead to a number of different problems in lubricated systems, including valve sticking, filter plugging, high-temperature operation, equipment wear, poor heater/cooler performance and costly unit trips. As noted previously, many labs don’t routinely test for varnish, making it difficult for oil users to manage their fluid’s varnish levels. Hobbs observes that by managing lubricant chemistry to prevent varnish formation, varnish-related losses can be eliminated.
This means testing for varnish regularly, so that the end-user isn’t blind to this extremely important aspect of their oil’s chemistry. Varnish testing costs a little more and, as a result, many do not perform it frequently enough. The right test for varnish is the membrane patch colorimetry (MPC) test (ASTM D7843).2 During this test, the varnish present in the fluid is captured on a 0.45 µm lab patch and is then evaluated by its color intensity (∆E). The MPC ∆E measurement is representative of the fluid’s potential for forming varnish. A high ∆E means a high varnish potential, as shown on the right side of Figure 1.
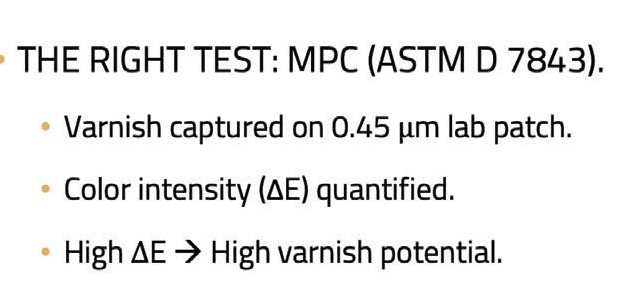
Figure 1. A high ΔE means a high varnish potential. Figure courtesy of EPT Clean Oil.
While using the right test is important, the test also must be performed in the right way. There are several key sample prep steps in ASTM D7843 that some labs fail to follow. The sample must be heated to about 60 °C for 24 hours and then incubated in the dark at room temperature for 72 hours. The heating step allows insoluble varnish that has precipitated in the time between sample collection and sample analysis to be re-dissolved within the lubricant. The incubating step then allows this soluble varnish to precipitate back out, making it more readily detectable. The 72-hour hold time is key as it provides each and every sample tested with a consistent amount of time for soluble varnish to precipitate and become detectable on an MPC patch. The hold time must, therefore, be consistent between different samples and different labs to make MPC results comparable. Labs are required to report this hold time alongside the ∆E result so that oil users know the test was run the right way. When the test is run as outlined in ASTM D7843, it provides a measure of both soluble and insoluble varnish levels.
The importance of the MPC hold time demonstrates how varnish is a “shapeshifter” that can exist in soluble (dissolved) and insoluble forms. The relative amount of varnish in each of these two forms is dependent upon oil saturation, which is a measure of how much soluble varnish a lubricant can hold before it begins to precipitate as insoluble varnish. As oils cool, varnish that is soluble at a higher temperature becomes insoluble, meaning that an oil’s varnish-saturation point is temperature-dependent. While equipment issues and failures are often associated with insoluble varnish, soluble varnish is the root cause of all of these problems. Varnish, therefore, needs to be detected and managed in both its forms.
Varnish management strategies have the goal of mitigating the risk of varnishing. Hobbs identifies three possible strategies:
1.
Cleaners and solubilizers. Unfortunately, these do not remove varnish. Instead, they solubilize it, which is not a long-term solution since soluble varnish persists and can still cause problems.
2.
Particle removal systems. These only remove insoluble varnish, leaving the soluble varnish that is the root cause of all varnish problems behind.
3.
Ion-exchange resins. These address the soluble root cause of varnish problems, making them the best way to manage lubricant chemistry.
To manage varnish levels, ion-exchange resins can be engineered to allow them to chemically filter out the oil breakdown products that are varnish precursors. Varnish that has already formed but is still dissolved is also chemically attracted to the ion-exchange resin and preferentially attaches to it instead of to metal equipment surfaces. This process interrupts varnish formation at its earliest stages and prevents the formation of insoluble varnish.
Unlike particle removal systems, an ion-exchange resin also is capable of removing both soluble and insoluble varnish. After the removal of soluble varnish, the oil is no longer saturated, meaning that it has capacity to accommodate more varnish in a dissolved state. Insoluble varnish can, therefore, redissolve off the equipment and into the fluid, where it is then removed (again) by ion-exchange filtration. This creates a positive feedback cycle that allows the ion-exchange-filtered oil to continuously clean the system.
Sustainability
Since it dramatically extends oil lifetimes, lubricant chemistry management provides a better, sustainable way to manage critical industrial oils. Hobbs notes that sustainability must be an operational tenet and goes on to define it as follows:
“Sustainability (noun): the ability to be maintained at a steady level without exhausting natural resources or causing severe ecological damage.”3
This definition shows that sustainability and maintenance are intimately linked. To operate sustainably, best practices for oil maintenance, therefore, need to be followed.
As we all know, current carbon dioxide (CO
2) emissions are not sustainable, which is why there has been a worldwide push to reduce emissions. The energy sector accounts for 76% of global greenhouse gas (GHG) emissions, with power generation responsible for about one third of those emissions, or about 25% of global GHG emissions.
4, 5 Because power generation is responsible for so much of these GHG emissions, seemingly small changes, when implemented on a large scale, can have major impacts.
The Three Rs
When it comes to positive environmental practices, most are familiar with the Three Rs (i.e., reduce, reuse, recycle). However, for fun, Hobbs identifies the Three Rs of lubricant chemistry management: rethink, remove, restore.
Rethink offers the most advantages of the three. By rethinking how the industry looks at assets to include the oil as well as the equipment, significant changes can be realized. It is not just about the machines. Oils also are assets (even though they are not currently maintained as such). Poor oil maintenance leads to waste, equipment damage, lost production and reduced efficiency; none of which embody sustainability.
Like other assets, oils are both economically and environmentally costly. Indeed, lubricant manufacturing is the most energy-intensive process in a crude oil refinery.
6 As a result, the cost and carbon footprint associated with lubricants are significant. From cradle-to-grave, every liter of lubricating oil results in 3.5 kg of CO
2e being released into the atmosphere.
7 In 2020, 37 billion kg of lubricant were produced globally, which corresponds to approximately 152 billion kg of CO
2e released into the atmosphere.
8
Oil waste, therefore, needs to be rethought. For example, the average lifespan of a gas turbine oil is two to five years. Over the gas turbine’s typical 25-year lifespan, that translates to
at least five oil fills. By practicing better maintenance through lubricant chemistry management, oil lifespan is extended, and the environmental and economic impacts of oil use are reduced concomitantly.
Hobbs shares a case study where the end-user’s maintenance went beyond particle and water removal and involved ICB ion-exchange resin from day one of their operations. This meant that oil breakdown products (varnish precursors) were removed from the lubricant as they formed. Over the course of its 13 years of service to-date, this power turbine (PT) compressor driver had no oil related failures, and oil analysis showed that its lubricant remained in like-new condition. Indeed, the oil’s current projected lifetime is longer than the projected lifetime of the PT compressor driver that it is used in!
This result (and others like it) are cause to rethink oil management, especially when the costs associated with poor maintenance are identified. Table 1 shows the possible impacts for a Frame 7 turbine with a 22,800-liter lubricant reservoir, both with and without lubricant chemistry management. Managing the lubricant’s chemistry can translate into a fill-for-life scenario. In this scenario, both the economic and environmental costs associated with the oil are reduced by 80% thanks to lubricant chemistry management.
Removing oil breakdown products is a key part of lubricant chemistry management, which as we’ve seen, significantly extends the lifetime of lubricants. Recall: oils are not condemned for particle or water accumulation—they are condemned due to chemical breakdown, which leads to the accumulation of varnish, acids, etc. By managing lubricant chemistry with ion-exchange filtration, varnish is removed with concomitant oil life extension.
This is a cost-effective way to treat an asset.
Hobbs goes on to provide a case study showing that it is never too late to remove varnish. A power turbine experienced a failure due to valve sticking. To prevent a recurrence, the turbine’s operators installed an ion-exchange filtration system, which improved their oil’s MPC varnish potential by 94% over only six months. The power turbine has operated reliably ever since. Instead of disposing of their oil, this end-user salvaged the oil charge, resulting in dollars and CO
2e saved.
The last of Hobbs’ Three Rs is
restore, and Hobbs proceeds to list the things that lubricant chemistry management can
restore, including reliability, efficiency and profitability. Hobbs notes that, based on an informal online poll of gas turbine users, in the last year, 20% of gas turbines lost production due to oil problems. By managing oil chemistry, these production losses can be eliminated, and turbine reliability can be restored. For a Frame 7 turbine, 24 hours of downtime translates to a loss of about $164,160. That one annual loss costs more than the 25-year lifetime cost of an ion-exchange filtration system. In addition, whenever a turbine fails, it needs to be re-started. Since a turbine’s startup emissions are greater than its baseload emissions, the most efficient emissions per output profile can be achieved by keeping that turbine up and running.
Hobbs observes that gas turbines also can run hot due to varnish crashing out in their coolers. In one case study,
9 the cooler did not perform well, leading to a high-temperature alarm. By derating the turbine by 40%, the system engineers silenced this high-temperature alarm; however, the turbine’s output reduction (from 5.5 megawatts [MW] to 3.3 MW) led to an estimated annual loss of $350,000 in the year that followed. Moreover, derating the turbine created a 12% operating efficiency loss, meaning that more fuel was burned for less power produced. Eventually, operators had enough of this “Band-aid” solution and installed ICB ion-exchange resin to manage their turbine oil’s chemistry. After installing ICB, the oil’s MPC varnish potential improved by 97%, allowing the fluid to clean the varnish deposits that had accumulated in the cooler. As the cooler was restored, it became easier to maintain appropriate oil temperatures, and the turbine was
restored to its full design capacity. This also resulted in savings as the turbine oil charge was salvaged instead of replaced. Indeed, profitability is among the most enticing things that lubricant chemistry management reliably restores.
As a final note, when it comes to profitability and sustainability
(see Tables 2 and 3, respectively), the larger the turbine, the greater the impact that lubricant chemistry management has. Nevertheless, systems of all shapes and sizes can benefit from this improved, more proactive oil maintenance approach.
Conclusions
Current oil maintenance tends to be reactive and focuses mainly on particle and water removal; however, oils are condemned due to their chemical breakdown, not their particle counts or moisture levels. The reason that oils are condemned on this basis is that varnish forms and equipment failures occur when the oil’s breakdown is unmanaged. Since oil breakdown is a chemistry problem, a chemistry solution is required. That solution is lubricant chemistry management.
Lubricant chemistry management is a better way to maintain critical oils. It requires complete and reliable oil analysis data so that oil chemistry can be “seen” because you can’t manage what you’re blind to. Then, it involves proactive oil chemistry management with ICB ion-exchange resin filters. These filters remove soluble varnish and its precursors, eliminating the root cause of oil-related failures and extending fluid lifetimes. By actively managing oil chemistry, the end-users of critical industrial equipment can operate more reliably, profitably
and sustainably.
REFERENCES
1.
ASTM STP 1573
2.
www.astm.org/d7843-21.html
3.
www.collinsdictionary.com/us/
4.
WRI.org
5.
EPA.gov
6.
American Carbon Registry
7.
Grice, L.N., Nobel, C.E., Longshore, L., Huntley, R. and DeVierno, A.L. (2014), “Life cycle carbon footprint of re-refined versus base oil that is not re-refined,”
ACS Sustainable Chemistry and Engineering, 2, pp. 158-164.
8.
Statista.com
9.
Hobbs, M.G. and Dufresne, P. (2022), “The Three Rs: A sustainable approach to turbine lubricant management,” STLE Annual Meeting & Exhibition.
Andrea R. Aikin is a freelance science writer and editor based in the Denver area. You can contact her at pivoaiki@sprynet.com.