Testing and specifications
By Dan Holdmeyer, Contributing Editor | TLT Lubrication Fundamentals May 2024
National and international organizations coordinate lubricant specifications and tests.
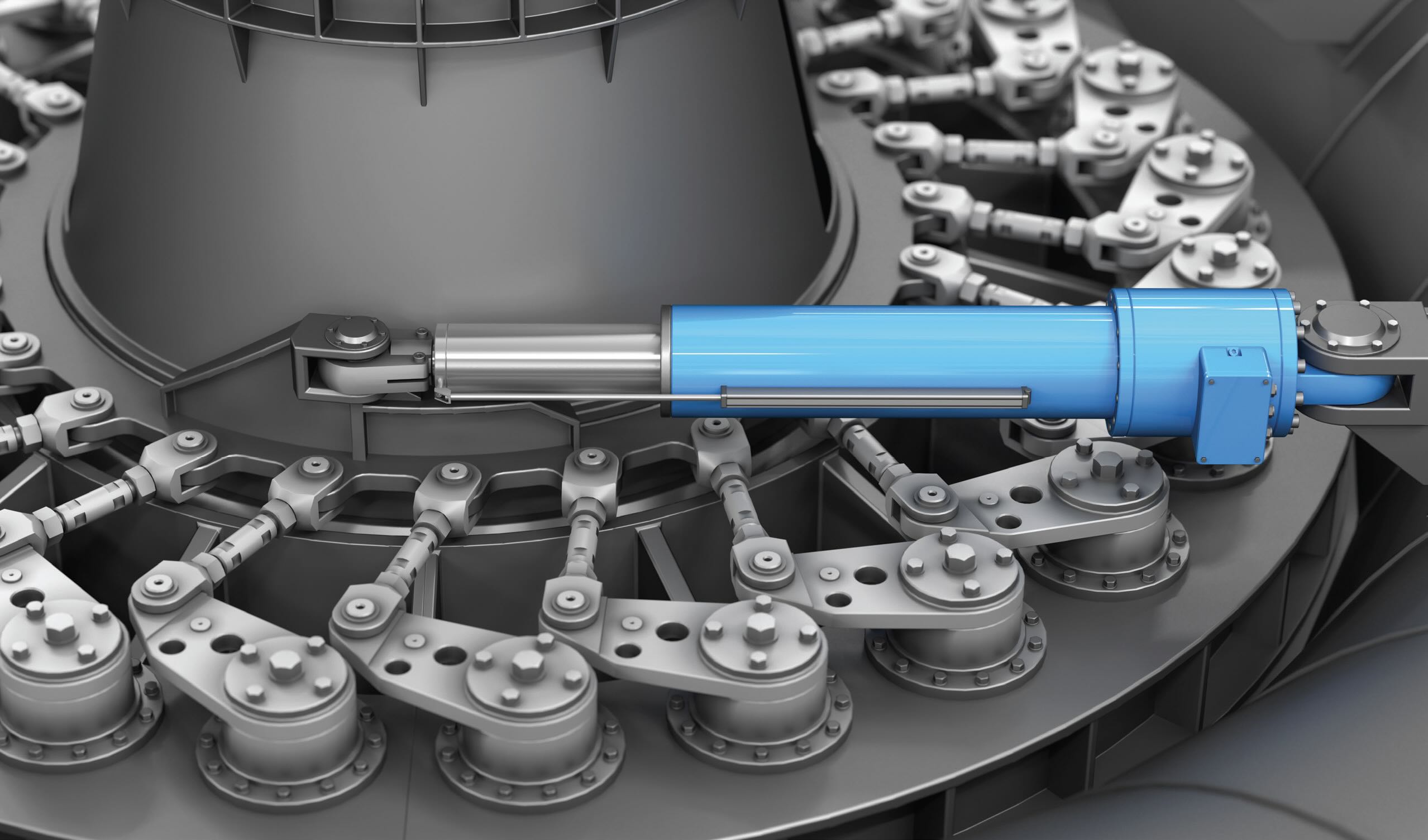
Last month we talked about various transmissions requiring specific lubricant frictional performance characteristics. A lubricant for most modern automotive transmissions needs to pass identified OEM tests and meet OEM specifications to be approved for use in the specific OEM, and model, transmission. Any formulation change in the lubricant needs to requalify in most cases.
Some engine OEMs also have unique specifications for lubricants to be used in their engines. These OEM specifications are often in addition to the most recent industry organization specifications, such as American Petroleum Institute (API) SP for gasoline engines and API CK-4 for diesel engines, that are intended to meet many of the marketplace requirements.
Even some industrial, or non-mobile, equipment OEMs have specific performance requirements for their equipment that also may involve field trials, or OEM equipment tests conducted in laboratory conditions.
Yet there are many OEMs that rely on lubrication industry common tests and specifications to help identify what lubricant can be used in certain applications.
So, let’s first talk about those common chemistry and physical lubricant tests before we delve into various industry and OEM specifications. These tests need to be standardized to afford reliability and repeatability in the results. Standardized testing also provides assurance similar results can be reproduced by different personnel, at another location on the globe.
Two of the predominant institutions regulating the equipment and methodology of these standards are Deutsches Institut für Normung (DIN), translated to “German Institute for Standardization,” and ASTM International, formerly known as American Society for Testing and Materials. Both organizations have written standards for not only lubrication but for a myriad of industries.
In 1917, “DIN 1” became the first published German standard regarding “taper pins” by the Normenausschuß der deutschen Industrie (NADI). NADI later changed its name to Deutsches Institut für Normung (DIN). Although DIN started in Germany and became the German Institute for Standardization, DIN also is a member of International Organization for Standardization (ISO) expanding its use globally.
ASTM started a little earlier, writing standards for American industries in 1898. Like DIN, ASTM’s first standard was not for the lubricant industry, but for the railroads. In 2023, ASTM celebrated 125 years as a leading world standards organization, not just in America. ASTM also is part of ISO and changed its name to ASTM International in 2001.
The ASTM and DIN standards are written by the committees in open and transparent methods. The committees consist of professionals of industries for which the standards are being developed.
ISO works to establish global consensus on new, and updates to established, standards of materials from the experts of the various relevant national organizations, along with ASTM and DIN.
The use of these standards is voluntary but does enable fair comparison of different lubricants. By citing the standard and the results, a lubricant’s performance level is indicated in that category, such as wear protection, oxidation resistance, water separability, etc. The standards may become mandatory, no longer voluntary, if they are referenced in contract, regulation or specification (OEM or industry).
Viscosity is the most important property of a lubricant and thus is always, or at least should be, quantified when citing a lubricant’s performance characteristics. ASTM D445 is the common standard used in America to determine a lubricant’s viscosity in centistokes (cSt). (See the February 2023 TLT Lubrication Fundamentals article titled “What about viscosity?” and March 2023 TLT Lubrication Fundamentals article titled “Viscosity index and classifications.”) DIN 51 562-1 is likely the standard used in Europe, also giving results in cSt. ASTM D2161 may still be used in North America but is becoming less popular giving viscosity in Saybolt Universal Seconds (SUS). Other standards, such as Redwood number and Degrees Engler, have become even more rare.
ISO established its Viscosity Grade (ISO VG) system which is primarily used for industrial lubricant applications around the world (see Table 1). The ISO VG is the mid-point viscosity at 40 ºC, from ASTM D445, with a range of plus or minus 10% of that viscosity grade. For example, ISO VG 100 has a range of 90-110 cSt so any oil with a viscosity at 40 ºC of 90 to 110 cSt is an ISO VG 100 oil.
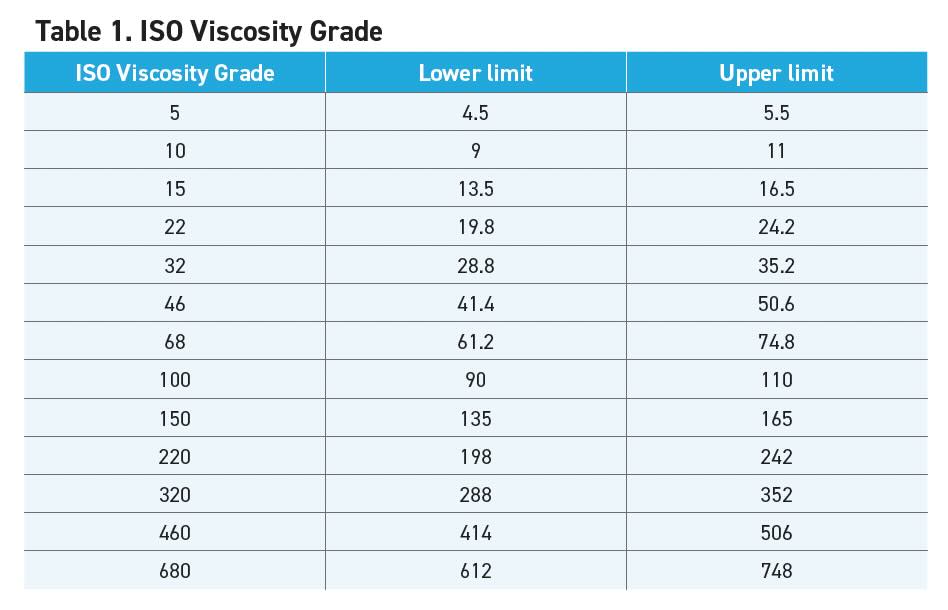
SAE International, formerly the Society of Automotive Engineers, established its SAE J300 classification for engine oil viscosities, a more complex system of classification. SAE J300 classifies viscosity grades using several different ASTM viscosity test methods. The oil viscosity at 100 ºC, determined by ASTM D445, is bracketed into SAE 8, 12, 16, 20, 30, 40, 50 or 60 to assure a satisfactory lubricant film in the engine at operating temperature. For SAE 0W, 5W, 10W, 15W, 20W and 25W (Winter grades), two ASTM test methods are used to measure the maximum low temperature oil viscosity that will allow cranking of the engine to start the engine and allow lubricant flow quickly enough to protect the engine once started. Cold cranking simulation viscosity is determined by ASTM D5293 to bracket the SAE xxW (Winter grades) by a maximum viscosity at bracket specific temperatures. Another ASTM test method is then used to measure the borderline pumping temperature (ASTM D4684).
Viscosity index (VI) per ASTM D2270 is a calculation from the viscosities measured at 40 ºC and 100 ºC. This unitless number is important for lubricants subject to a wide operating temperature range. A straightgrade engine oil, or a normal VI industrial oil, will have a VI of around 95-105. Synthetics, multigrade engine oils or high VI industrial oils will have a VI of 130-160.
Flash point, measured via ASTM D92 or ISO 2592, is a measure of the temperature at which a fire will flash but not remain burning with a source of ignition, such as a spark or flame. Fire point, on the other hand, is the temperature at which a fire is maintained after being ignited by a flame. Auto-ignition point is when the oil begins to burn without a source of ignition, like what happens in the cylinder of a diesel engine when the diesel fuel reaches a high enough temperature to ignite.
Pour point, measured via ASTM D97 or ISO 3016, is determined by cooling the oil sample and testing at 3-degree Celsius increments to see if no surface movement of the sample is detected within 5 seconds of tipping the oil sample. The pour point is then recorded at the previous temperature. Pour point is well below the recommended temperature for equipment start-up, particularly hydraulic and circulating oils. Engine oils have the SAE J300 classification to help determine the right oil viscosity for start-up temperatures. Industrial gear oils in bath type systems need to “slump” back into the path of the gear teeth to start lubricating, so long as the gearset bearings are lubricated by other than the gearbox oil. It is always a good idea to not put equipment under load when starting at the recommended lower temperature ranges. In mineral oils cloud point will be several degrees higher than pour point. Cloud point is the temperature at which the wax in the oil begins to crystalize and may look like a cloud in the oil. This is critical for filtering oil, and for filtering diesel fuel, as the crystal “cloud” will likely clog the filter.
Acid number, ASTM D974 or DIN 51 558-1, indicates acidity, normally caused by additives in fresh oil. New turbine oils are typically around 0.05 to 0.1 mg of potassium hydroxide (KOH), hydraulic oils approximately 0.4 and gear oils roughly 0.8. Acid number increase in used oils may indicate oil oxidation but also may be due to contamination.
Rust prevention, measured via ASTM D665 A/B or DIN 51 585, indicates the oil’s ability to protect steel parts from rusting. ASTM D655A is conducted with distilled water, whereas D655B uses sea water. ASTM D655 is an excellent predictor of rust inhibition properties of the oil.
Copper strip corrosion, ASTM D130 (see Figure 1) or ISO 2160, measures the oil’s corrosivity to copper and copper alloys (“yellow metals”). Certain additives, especially sulfur, are corrosive to yellow metals. After the copper strip has been exposed to the oil at the required temperature and time duration, it is compared to a chart that visually shows the color variations of the copper as it corrodes. Most lubricants today are expected to rate a “1a” or “1b.” Some metalworking fluids will rate a “2a” or higher.
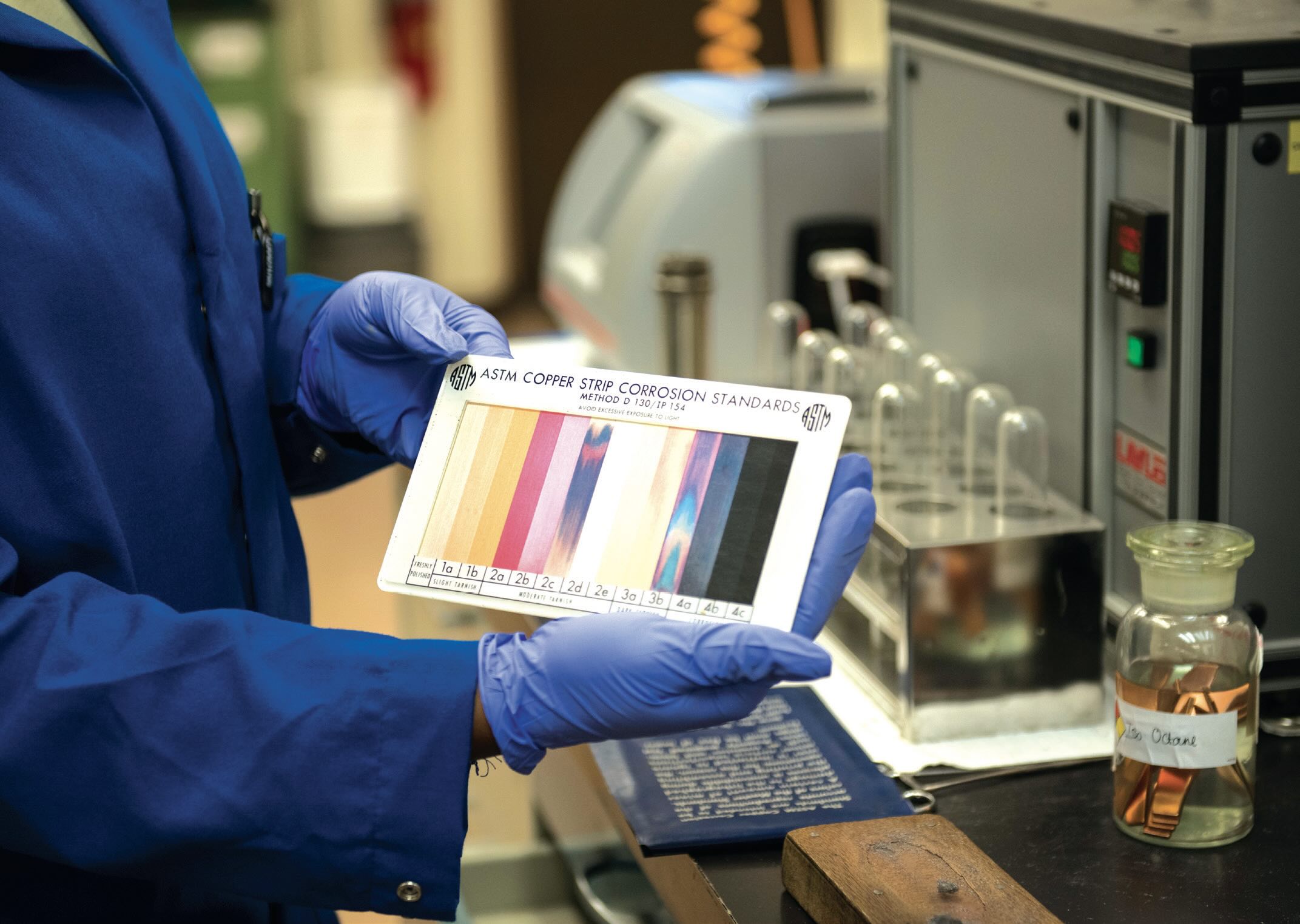
Figure 1. Color chart for ASTM D130 copper corrosion test. Figure courtesy of Airman 1st Class Greg Erwin, U.S. Air Force.
Foaming Sequence I/II/III, ASTM D892 or ISO 6247, is an indicator of foaming tendencies and stability of foam in lubricating oils. Air is blown into a predetermined amount of oil in a graduated cylinder for five minutes. The amount of foam is measured right after the air flow is stopped and then again after 10 minutes. This indicates the foam tendency and foam stability in the oil. Sequence II is used most often for expediency and because it is run at 200 ºF, which more closely represents typical operating temperatures. Sequence I and III are run at 75 ºF. All three sequences may be required for critical applications where foaming is likely to be an issue.
Those are the most common tests run on all lubricating oils. Next month we’ll discuss some of the common industry lubricant performance tests required by some industrial applications, such as turbines, hydraulics and gears.
Note: This article has been edited and updated from its originally published form.
Dan Holdmeyer is retired from Chevron Lubricants and is based in Washington, Mo. You can reach him at dan.holdmeyer@gmail.com.