KEY CONCEPTS
•
Journal bearings, in particular, benefit greatly from surface texturing to enhance their tribological performance.
•
Surface texturing contributes to reduced friction and wear by increasing hydrodynamic pressure, acting as a reservoir to trap debris away from the contact zone and controlling lubricant distribution.
•
The choice of texturing technique, such as laser surface texturing and laser shock peening, plays a crucial role in achieving desired surface features.
Over the past two decades, surface texturing has become an accepted method for precisely customizing tribo-friendly features. Textures on various scales have been created using a variety of techniques, including lithographic procedures, laser surface patterning and embossing/ micro-coining. The corresponding frictional properties and contact conditions of the associated system and its materials determine which technique is best.
While the concept of surface texturing is a widely researched topic in tribology, an expanding number of applications for surface texturing as a means for friction and wear control have been under study in recent years.
Studies show that, through surface texturing, precisely defined surface features can reduce friction and wear in many ways. Microtextures, for instance, can produce hydrodynamic pressure in addition to acting as debris or oil reservoirs.
Surface texturing has drawn attention for machine elements more recently due to its ability to have a major impact on tribological performance under various lubrication conditions.
In mechanical systems, bearings are among the components that are the greatest contributors to frictional losses. Journal bearings, in particular, are utilized in a wide range of machinery that relies on start-stop cycles during operation
(see Journal Bearings). Because of this, journal bearings experience especially high wear and friction. To exacerbate the issue, bearings found in heavy-duty machinery often operate with mixed or even borderline lubrication, making them more susceptible to wear and/or increased friction. As such, much of the research into surface texturing has focused on journal bearings.
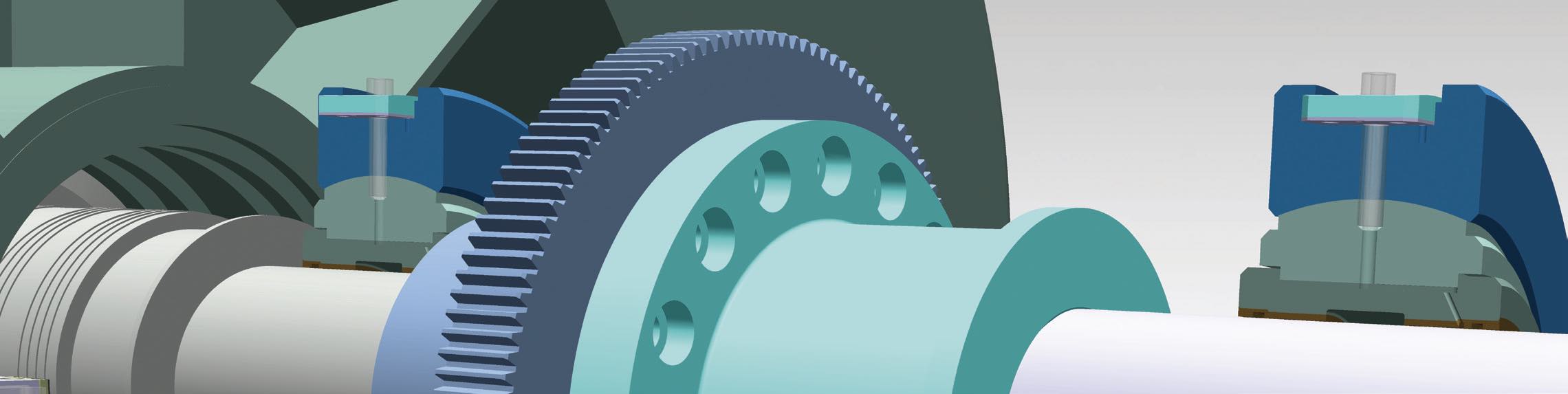
Journal bearingsA
Journal bearings, also referred to as “plain” bearings, are composed of a journal, or shaft, that spins freely within a supporting metal shell or sleeve. The journal is the portion of the shaft that fits into these bearings. There are not any rolling components. The mechanics of these bearings can be intricate, despite their seemingly straightforward design and construction. These bearings can withstand a sizable amount of weight despite lacking rollers to support radial loads.
In the case of journal bearings, lubrication not only forms a barrier between the rolling contact and sliding surface and promotes heat transfer, but it also is crucial for shielding surfaces from corrosion and contamination.
Journal bearings function in the boundary lubrication phase during the bearing’s startup and shutdown, as well as in the hydrodynamic lubrication regime. A textured surface is very important because, at the beginning of bearing operation, there is metal-to-metal contact that leads to boundary contact and little to no lubrication. It operates at the hydrodynamic lubrication regime once the engine is started because oil is provided at the junction that creates pressure and hydrostatic lift. The hydrodynamic fluid film rotates at high speeds and aids in supporting heavier loads.
Hiroo Taura, associate professor, Faculty of Science and Engineering, Kindai University, Higashiosaka, Japan, adds that for the same minimum clearance, a textured surface will increase the average clearance more than a smooth surface; partially textured surfaces increase the average clearance only in the textured area, thus changing the overall clearance distribution of the journal bearing. When the textured area is set on the load side, the increased clearance causes a decrease in load capacity and an increase in attitude angle. The effect of the texture on the static characteristics is small when it is placed on the anti-load side.
A.
From Tribonet entry Journal Bearing by Manoj Rajankunte Mahadeshwara. Available at
www.tribonet.org/wiki/journal-bearing/.
Another reason for the focus on journal bearings is the continuing campaign for improving the energy efficiency of vehicles; friction accounts for about 20% of energy loss during vehicle operation. Piston pin joints, balancer shafts and crankshafts all rely on journal bearings.
Regarding surface texturing for electrical applications (including electric vehicles), Hiroo Taura, associate professor, Faculty of Science and Engineering, Kindai University, Higashiosaka, Japan, explains, “For electrical contacts, it is desirable to reduce friction while maintaining solid contact for electrical continuity. To achieve these contradictory requirements, surface textures are used. If a circular groove texture is provided on the moving side of the electrical contact, increasing the radius of the circular groove will decrease the load capacity, even if the rider’s lifting capacity remains the same. This means that the pressing force required to maintain solid contact can be reduced. For friction characteristics, the coefficient of friction decreases with increasing groove radius.”
Single and multi-scale surface patterns fabricated from laser patterning and microcoining have resulted in the fastest lubricant spreading behavior and enhanced frictional performance of journal bearings. Studies show that both single and multiscale surface-patterned journal bearings are able to shift from mixed to hydrodynamic lubrication at reduced rotational speeds. Also, the positions of texture regions in partially textured bearings have a significant effect on static and dynamic characteristics, and surface texturing mitigates friction in low-speed reciprocating sliding contacts.
So, at this point, the question is not whether surface texturing is beneficial from a tribological perspective, but how surface texturing can be improved to meet the increasing demands of new and critical machine elements.
One idea is biomimetics—the application of nature’s adaptations to inanimate challenges—in this case, journal bearing surface textures inspired by the micro-spike structure of the dragonfly yield improvement in bearing performance characteristics.
Journal bearing surface textures inspired by the biomimetic micro-spike structure on the dragonfly yield improvement in bearing performance characteristics.
STLE member T V V L N Rao, professor and dean, Faculty of Engineering, Assam Down Town University, Guwahati, Assam, India, says, “The performance of textured bearings is invariant across a number of textures. Although texturing has been around for a long time, partial texturing at the inlet of near parallel bearing surfaces has gained prominence. It is a feasible method for performance enhancement of lubricated bearing contacts in terms of load capacity, friction and wear.”
He adds, “Bearings (journal or slider) with nominally parallel surfaces benefit most from partial texturing. The potential partial texturing benefits include performance improvement in load-carrying capacity and reduction in coefficient of friction. The texture patterns impart nearly the same benefits on the performance improvement in load-carrying capacity and reduction in coefficient of friction.”
Surface texturing and tribological benefits
Surface texturing can significantly affect the friction and wear response of a surface regardless of the acting lubrication regime and under different lubrication conditions. Dr. Philipp Grützmacher, Tribology Research Division at TU Wien University, Vienna, Austria, explains, “This can be attributed to several aspects. Surface textures can increase the hydrodynamic pressure and, thus, the load-carrying capacity. Additionally, they can draw additional lubricant into the contact, reduce the real area of contact, act as a secondary oil supply by storing lubricant and remove wear particles from the contact by trapping them.
“Surface texturing has been shown to greatly improve tribological performance for sliding components, such as mechanical seals or journal bearings. For rolling contacts, which are mostly non-conformal and rely on elastohydrodynamic lubrication, surface texturing also can induce beneficial effects, but the situation is more complicated.”
Grützmacher clarifies that if the textures are not ideal, they can easily induce adverse effects that lead to greater friction and wear. Using rolling contacts (which undergo high pressure over a small contact area) as an example, the texture for these types of bearings needs to be small and shallow, i.e., dimples.
“These variations in texture are particularly applicable to machine elements, which do not operate under a single set of tribological conditions but often across different lubrication regimes (e.g., due to start-stop cycles) where different textures give optimum performance,” Grützmacher says. “Therefore, combining different textures with different sizes might significantly broaden the range of operation conditions where these surface textures work effectively.”
Although, according to Rao, tribological improvements in terms of increased load capacity and friction reduction under different lubrication regimes offered by surface texturing vary with respect to texture shape, geometry, pattern and the type of sliding contact, the tribological performance of textured lubricated bearing is substantially improved when compared with untextured lubricated bearings of the same type. “Textures in the inlet zone ensure less resistance to flow and hence improve the tribological performance. The presence of texture also increases local film thickness,” Rao says.
The impact of surface texturing on journal bearings
While journal bearings are critical components across many types of machinery, they do have the downside of requiring more intensive maintenance than most other types of bearings. This is particularly true regarding lubrication, making journal bearings prime candidates for texturing.
“Journal bearings are a classic machine element, which can greatly benefit from the application of surface textures,” Grützmacher points out. “Particularly the onset of hydrodynamic lubrication and, therefore, wear-free operation can be pushed to lower sliding speeds or higher loads by the use of surface textures. We have shown that friction can be greatly reduced (up to an 80% reduction in coefficient of friction [COF]) across several operation regimes by applying both single- and multi-scale surface textures to the shafts.”
A 2018 study
1 examined the effects on journal bearing frictional performance of particular single- and multi-scale surface patterns created by roller-coining and/or direct laser interference patterning. Surface designs that demonstrated positive results in initial laboratory testing were chosen and manufactured onto a stainless steel (AISI 304) journal bearing shaft.
The observed reduction in friction agreed with earlier laboratory testing. Study conclusions were as follows:
•
In spite of the surface curvature of the shaft, single- and multi-scale surface patterns are consistently produced with excellent accuracy and reproducibility.
•
With a high COF of 0.23 at the lowest velocities and a progressive drop in COF at higher rotational speeds, the burnished reference shows Stribeckcomparable behavior.
•
Over the whole rotational speed range, all patterned samples exhibit a lower COF when compared to the burnished reference. Furthermore, for every design sample, the changeover from mixed to hydrodynamic lubrication shifted to smaller rotational speeds. The patterned samples showed a 20%- 30% reduction in friction at the lowest rotating speed of 25 rpm.
•
For all patterned samples, a sharp decline in COF is seen with increasing rotational speed, while the burnished reference’s COF reduces very marginally. All patterned samples exhibited a fairly steady and low COF at rotating speeds greater than 150 rpm.
•
When combining deeper micro-coined dimples with a cross-like surface pattern, the multi-scale sample exhibits the largest friction reduction (4.6) when compared to the burnished reference.
•
The friction reduction found under hydrodynamic lubrication (up to a factor of 4.6) and mixed lubrication (approximately a factor of 2-3) closely corresponds with findings from earlier laboratory testing.
The study authors conclude that the results justify the application of findings from this streamlined ball-on-disk test apparatus to journal bearings operating in more real-world settings.
Biomimetics
In the multidisciplinary field of biomimetics, materials, artificial systems and machines with functionalities similar to biological processes are created using concepts from biology, chemistry and engineering.
Journal bearing surface textures inspired by the biomimetic micro-spike structure on the dragonfly yield improvement in bearing performance characteristics. Researchers conclude that the optimum design of the spike structure on journal bearings affects the oil film distribution—reducing friction and increasing stability.
Dr. Masayki Ochiai, a professor of the Department of Mechanical System Engineering, Tokai University, Hiratsuka City, Japan, and head of the Research Group at the Research Institute of Science and Technology, researched the fine protrusion structure on dragonfly wing veins: Dragonflies use this structure to reduce drag or friction on their wings. “Our experiments have confirmed that when applied to journal bearings, friction torque is reduced at high-speed rotation,” he reports.
Grützmacher explains, “If we look at natural surfaces, we can observe that almost all of these surfaces are multi-scale in their structure. These multi-scale surface structures or textures give rise to exceptional properties, such as the non-wetting properties of the lotus leaf or the low drag resistance of shark skin, among many examples. Therefore, we can take inspiration from these natural surfaces and create even more efficient surface textures by making them multi-scale.”
A 2020 study
2 applied biomimetics to journal bearings in order to enhance their properties. To achieve this, researchers modeled the journal bearing’s texture after those tiny spikes found on a dragonfly wing. They then measured the impact of this texture by determining the shaft center locus and friction torque. By using X-ray computed tomography to take pictures of the lubricant film distribution, the impact of the spike structure on film creation was further verified. The outcome demonstrated how the spikes’ microbubbles widened the gas-phase zone and decreased spinning and friction. The study concluded the following:
•
In the presence of spikes, the friction torque significantly increases at low rotational speeds. However, during high-speed rotation, the friction torque decreases, and whirling is suppressed.
•
Microbubbles expand the gas-phase region, thereby reducing the sliding area and friction torque. The microbubbles form a gas-phase region in the inverse wedge, which suppresses circulation flow and whirling.
•
Spikes effectively reduce friction under shear flow, because microbubbles are less likely to form as the pressure in the clearance increases.
•
The squeeze effect caused by the shaved and conformed spikes probably resulted in an increased oil film thickness and a damping effect.
The primary conclusion is that the optimum design of spike structure on journal bearings affects the oil film distribution, reducing friction and increasing stability.
Ochiai adds, “Regarding the direction of my research, I believe that it is important to propose new design methods and learn from the natural world.”
The disbursement of lubricants across surface patterns
While it is well-known that surface textures can greatly affect the wetting properties of surfaces, Grützmacher points out that this naturally also affects how a lubricant is wetting a textured surface
(see The Effect of Temperature on Disbursement).
The effect of temperature on disbursement
Dr. Philipp Grützmacher, Tribology Research Division at TU Wien University, Vienna, Austria, explains that lubricants migrate over surfaces, for example due to centrifugal forces or temperature gradients. Temperature gradients can be induced due to frictional heating. The migration of a lubricant out of the frictional contact zone can lead to lubricant starvation and, therefore, drastically increase friction and wear. Surface textures can prevent lubricant from migrating out of the frictional contact zone, where it is needed, by pinning the lubricant or even guiding the lubricant into the contact. Multi-scale surface textures are particularly effective in doing so because they have a stronger effect on the wetting properties of surfaces.
“By controlling the wettability of a lubricant on a surface, we have another tool to influence its tribological properties,” he says. “Furthermore, by creating suitable surface textures, such as channel-like textures, a lubricant can be deliberately guided over a surface to locations where lubrication is needed. Surface textures can be used as barriers to pin the lubricant in certain directions and as channels to guide the lubricant into other directions by making use of capillary forces inside these channels.”
A 2021 study
3 on the impact of a textured surface on the lubricating properties between the piston ring and the cylinder liner in internal combustion engines concentrated on power loss, minimum oil film thickness and various dynamic force types. In addition, the impact of the lubrication conditions—starved and fully flooded— was investigated.
The textured surface of the cylinder liner was found to minimize the maximum magnitude of the asperity contact force and the total friction force by 9.43% and 5.29%, respectively. This was due to the decreased contact area between the piston ring profile and the cylinder liner. Furthermore, the rough surface made it possible to achieve a thicker lubricating coating, which slowed down the wear process. Generally speaking, it was found that the textured surface enabled a 4% rise in minimum oil film thickness (MOFT), which demonstrated that it is feasible to lessen power loss in this manner.
The study’s data analysis indicated that adding a textured surface to the ring profile can result in a 5% increase in MOFT. This suggested a decrease in power loss of as much as 11%. But since an insufficient surface texture in the ring might result in a 7% drop in MOFT and a 9% increase in power loss, a thorough investigation is required to determine the properties of the ideal textured surface.
Because poor lubrication was taken into account, the numerical model that has been implemented will help develop more sophisticated studies that analyze tribological characteristics under the influence of textured surfaces.
Texturing techniques
Patterns on various scales have been created using a variety of techniques, including lithographic procedures, laser surface patterning and embossing/micro-coining. Laser-based texturing techniques are frequently utilized because they can build texture geometries with accuracy and flexibility and work with a number of materials, including metals, ceramics and plastics. Laser surface texturing (LST) is widely used because it simplifies the manipulation of texture parameters including the width, depth and density of dimples as well as their relative placements. Surface microfeatures, like dimples, are created during the LST process by interacting with surface materials through ultrashort laser pulses that cause an ablation effect. Although LST can provide the precision required for complex textures, adopting it for production-scale use at a reasonable cost remains unresolved.
Laser shock peening (LSP) can be used to engineer surfaces for improved wear resistance. This method is an efficient surface strengthening technique. When compared to other surface strengthening techniques, such as shot peening and ultrasonic impact peening, LSP stands out due to its remarkable controllability, good flexibility and improved process efficiency. LSP shock surface patterning (LSSP) is another laser- related surface texturing technique that has been effectively used to increase wear resistance. It uses indirect laser (indirect- LSSP) to create anti-skew surfaces with a variety of micro-indentations. The technique controls friction values and improves wear resistance.
4
Fluid film bearingsB
Fluid film bearings are designed to deliver low friction between solid surfaces and create load support for mechanical components. Well-designed and operated fluid film bearings will support both dynamic and static loads. This makes them a key component of rotating machinery. Hydrodynamic, hydrostatic and hybrid are the basic types of fluid film bearings.
•
Hydrodynamic fluid film bearings exhibit relative motion between two surfaces. The lubricant is pulled into the film where hydrodynamic pressure is generated and able to support the external load.
•
Hydrostatic fluid film bearings are pressurized externally. This pressurized fluid forces the lubricant between surfaces. This creates a separation and the capability of supporting a load with no surface contact.
B.
Introduction to Fluid Film Bearings and Seals, Texas A&M University. Available at
https://rotorlab.tamu.edu/me626/Notes_pdf/Notes00%20Introduction.pdf.
Hydrodynamic and sliding contacts
Hydrodynamic fluid film bearings
5 (see Fluid Film Bearings)—which include journal bearings—have major advantages, such as enhanced dynamic behavior, over other types of bearings, especially under transient or impact loads. The reduction of friction also contributes to a faster transient response. Fluid film textured thrust bearings provide reliable operation with high load capacity and low friction
(see Research on Thrust Bearings). Thermal deformation is an important consideration in their design, which needs to maintain minimum friction losses while keeping sufficient thrust load capacity.
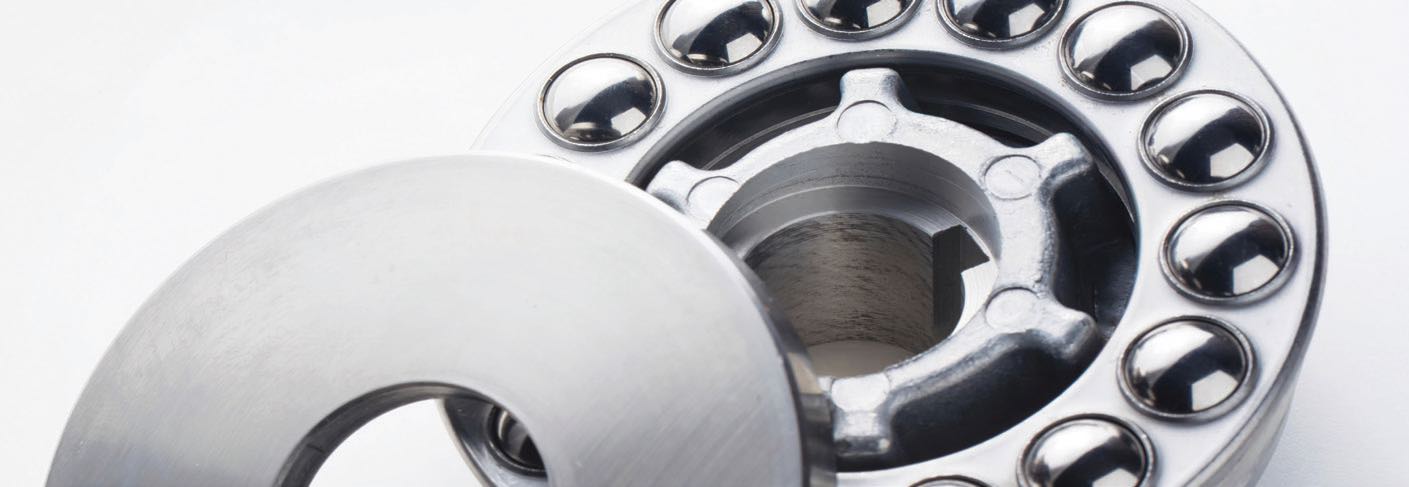
Research on thrust bearings
Dr. Masayki Ochiai, a professor of the Department of Mechanical System Engineering, Tokai University, Hiratsuka City, Japan, and head of the Research Group at the Research Institute of Science and Technology, has been particularly interested in texturing the surfaces of thrust gas foil bearings. Thrust bearings are rotary bearings designed to support a primarily axial load.
Ochiai and his colleagues measured and evaluated friction torque using their laboratory’s own high-speed thrust bearing testing equipment. “This is a simple method that uses a load cell to measure the rotational force on the floating non-rotating side part and calculate it into torque,” he explains. They then proposed a new texture called “F-groove,” added dimples and compared it with a non-textured version.
For spiral groove bearings, they replaced the curve with a third spline function in order to increase design flexibility. They applied this method to bearings for small motors used in hard disks. They also performed optimization to minimize variations in bearing characteristics caused by processing errors.
While spiral groove thrust bearings have outstanding load capacity, in some cases, the load floats excessively, reducing stiffness and damping performance. So Ochiai and colleagues proposed a new method for optimizing the shape and found the unique shape of grooves. “An interesting point is that when the proposed optimal design is carried out with the aim of maximizing the flying force, almost the same curves are obtained for spiral groove bearings,” Ochiai adds. “Optimal design can be expected to improve bearing characteristics, and there is a possibility of discovering shapes that people could not imagine before.”
Dr. Nicholas Morris, senior lecturer, Loughborough University, Loughborough, England, explains, “When textures are required to reduce friction via micro hydrodynamics and increase load-carrying capacity, the position and design of these textures in the contact area become crucial. Most hydrodynamic junctions are intentionally designed with a convergent-divergent geometry. Well-placed textures amplify the pressure generated by entrainment within this geometry, while poorly positioned textures can adversely affect hydrodynamic pressure. Partial surface texturing is a well-known approach to only texture the appropriate region of the contact. Textures have been shown to reduce friction in partial pad design bearings. An interesting aspect of the research was the benefit the textures have to enhance lubricant supply throughout a contact when out of roundness is significant in comparison to the film thickness.”
Morris adds, “For textures to generate net load-carrying capacity within a contact, the spacing of textures relative to each other is of critical importance. Increasing the number of textures has been shown to be favorable in reducing friction in the hydrodynamic regime of lubrication.
6 In mixed regime lubrication, consideration also must be given to the reduced apparent contact area between the surfaces and the implication this has on the real asperity contact area and boundary friction under any particular operating condition. Additionally, on occasion, we have found that texturing contacts has enabled the surfaces we were investigating to achieve a preferential surface form during run-in compared to their untextured counterparts, which is a very interesting phenomenon.”
Regarding the frictional performance of lubricated untextured and partially textured sliding contacts, Morris explains, “When textures are applied to contacts lacking a convergent surface design as part of the surface’s macro geometry, significant benefits can be obtained from surface texturing. In these contacts, surface texture microhydrodynamic action becomes the primary means through which hydrodynamics can provide load-carrying capacity.”
Conclusions
Numerous studies have examined various elements of surface texturing, including the impact of texturing geometry, as well as the physical mechanisms lowering friction and wear. Despite recent advancements, a comprehensive understanding of how textures work is incomplete.
Grützmacher concludes, “Often it is forgotten that basically all texturing techniques, not only those that create geometrical textures but also those that modify the microstructure of the textured parts or their chemistry (laser processing, for example), often lead to oxidation. Both alter the parts’ mechanical properties on the surface. When investigating and discussing the effect of surface textures it is, therefore, imperative to not only take the geometrical effect of the surface textures into consideration but also the modification in microstructure, chemical state of the surfaces and mechanical properties induced by the texturing technique.”
REFERENCES
1.
Grützmacher, P.G., Rosenkranz, A., Szurdak, A., König, F., Jacobs, G., Hirt, G. and Mücklich, F. (2018), “From lab to application-improved frictional performance of journal bearings induced by single-and multi-scale surface patterns,”
Tribology International, 127, pp. 500-508.
2.
Kairi Furukawa, K., Ochiai, M., Hashimoto, H. and Kotani, S. (2020), “Bearing characteristic of journal bearing applied biomimetics,”
Tribology International, 150, 106345.
3.
Garcia, C. P., Rojas, J. P. and Abril, S. O. (2021), “Analysis of the influence of textured surfaces and lubrication conditions on the tribological performance between the compression ring and cylinder liner,”
Advances in Tribology and LCA Applied to Thermal Machines, 9 (5), p. 51.
4.
Andrew, J.M. (2019), “Controlling surface topography,” TLT
75 (10), pp. 28-38. Available
here.
5.
Usually a low-clearance arrangement, a hydrodynamic bearing depends on an oil (and sometimes air) layer that creates room as the spindle rotates. The load is transmitted (floated) by the bearings on a self-renewing lubricating coating. The journal bearing is the most fundamental type of hydrodynamic bearing.
6.
Ronen, A., Etsion, I. and Kligerman, Y. (2001), “Friction-reducing surface-texturing in reciprocating automotive components,”
Tribology Transactions, 44 (3), pp. 359-366.