Lubrication of hybrid electric vehicles
By R. David Whitby, Contributing Editor | TLT Worldwide March 2024
The fluid properties and performance required to lubricate are very different from those required to cool.
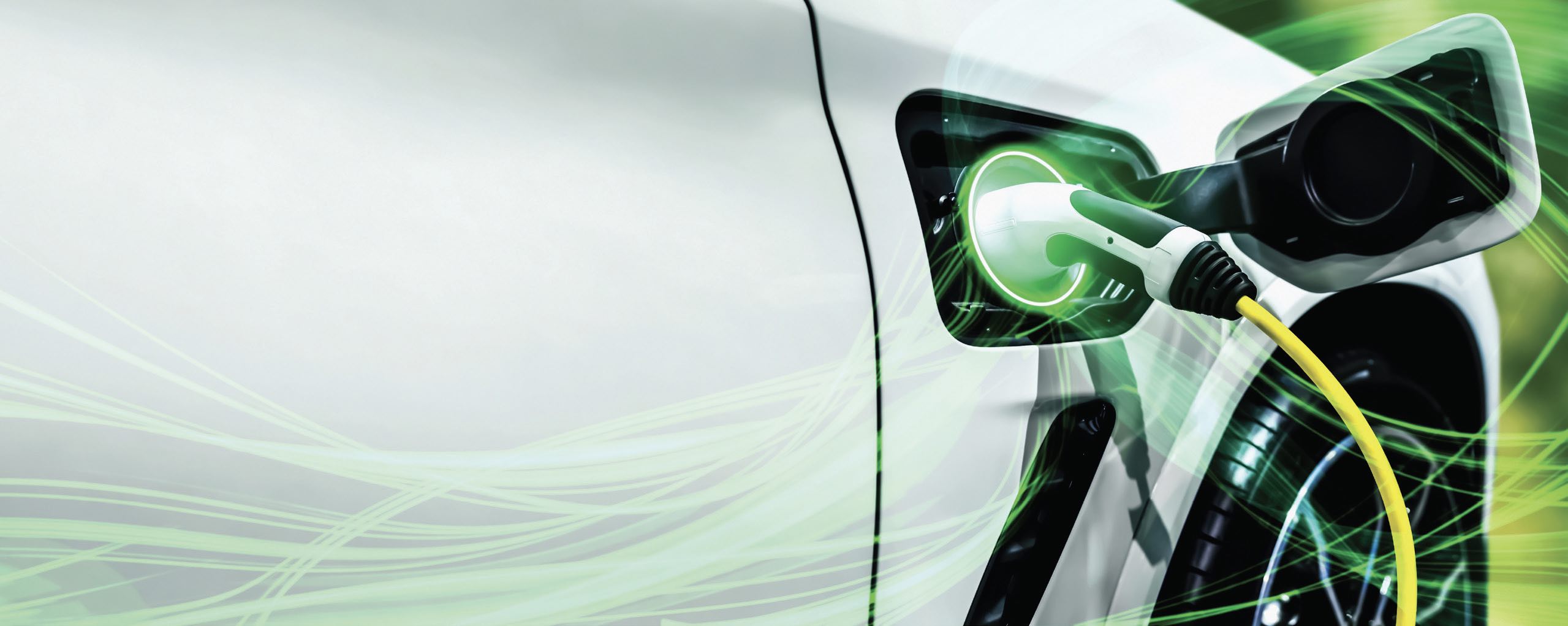
Unlike internal combustion engine vehicles, powered by either gasoline or diesel fuel, in which the essential mechanics are very similar, hybrid electric vehicles have one of three different mechanical arrangements. These are described as:
•
Series, in which an electric motor powers the wheels, receiving electricity from a battery pack which is linked to a generator run by an internal combustion engine
•
Parallel, in which an electric motor and an internal combustion engine work together to generate power to the wheels
•
Series-parallel, in which an electric motor and an internal combustion engine can independently generate power to the wheels.
Each of these arrangements requires a drivetrain (powertrain), consisting of a transmission, a drive shaft and bearings, to transfer the power to the wheels. Many transmissions are of the dual-clutch type, often integrated with the electric motor. Electric motors generate maximum torque at zero rotational speed, so the transmission system must be able to cope with high stresses as the vehicle begins to move.
Many systems include a regenerative braking system. This recharges the battery pack by capturing the kinetic energy of the vehicle while it is slowing down or stopping. In addition, stop-start systems shut down the combustion engine when the vehicle is stationary, helping to reduce energy before the vehicle needs to move again.
The combustion engines in hybrid electric cars tend to use gasoline as the fuel, while the engines in some hybrid electric trucks and buses use diesel fuel. Biofuels and hydrogen also are being tried in some vehicles.
With the series-parallel (also known as power-split) design, the battery pack can provide all the power at low speeds, such as during around town driving, and the gasoline engine can provide all the power at higher speeds. In this way, the series-parallel’s versatile design can use less fuel and provide optimum energy efficiency.
In the series design, only the electric motor drives the drivetrain, and the combustion engine can be run continuously at a constant speed just to generate electricity to the motor and the battery pack. The engine does not need to provide power at high torque (unlike a conventional internal combustion engine-powered vehicle) when the vehicle accelerates from rest. In this case, the electric motor provides all the required torque.
With the parallel design, the electric motor and the engine are both connected to the transmission and can simultaneously transmit power to drive the wheels. In many parallel hybrid vehicles, the engine also can act as a generator for supplemental charging of the battery pack. Parallel hybrids are more energy efficient than comparable non-hybrid vehicles, particularly during urban stop-start conditions.
Series hybrids tend to be more efficient at lower speeds, and parallel hybrids tend to be more efficient at higher speeds, which is why series-parallel hybrids are more efficient overall.
All these mechanical arrangements require both lubrication and cooling. In particular, the electric motor and battery require cooling, while the engine, drivetrain, bearings and regenerative braking system require lubrication. The fluid properties and performance required to lubricate, by reducing friction and wear, are very different from those required to cool, by transferring heat.
Because the engine in a series hybrid is often smaller than one in either a parallel hybrid or a series-parallel hybrid and can be run at a constant speed, its lubrication requirements are much less demanding. In the series-parallel arrangement, when intown driving changes to highway driving, the engine may need to kick in very quickly, stressing the engine oil. In some designs, the lubricant for the transmission also lubricates the electric motor, so it must be compatible with the copper coils in the motor. Some vehicle manufacturers are developing combined lubricant-coolant fluids, because this requires a less complex fluid system.
At present, there does not seem to be much consensus among system designers, fluid suppliers, additive manufacturers and vehicle manufacturers about which hybrid electric arrangement is optimum. This is unlike conventional combustion engines, whose design has been optimized over the last 120 years.
All of this means that a large number of lubricants and coolants could be required to meet the demands of the three different mechanical arrangements. This could pose a real dilemma for manufacturers, marketers and distributors of the fluids required for hybrid electric vehicles.
David Whitby is chief executive of Pathmaster Marketing Ltd. In Surrey, England. You can reach him at pathmaster.marketing@yahoo.co.uk.