Meet the Presenter
Dive into the world of lubrication fundamentals with this article, based on the webinar titled Electrical Contact and Lubrication. Hosted by the American Society of Mechanical Engineers’ (ASME) Tribology Division and presented by Dr. Robert Jackson on Jan. 25, 2023, the session explored some of the fundamental theories of electrical contacts and examined current issues in electric vehicles and possible solutions. Courtesy of STLE, this article captures the core insights from this ASME-organized event. For more technical content from the ASME Tribology Division Webinar Series, visit the ASME Tribology Division’s website at www.asme.org/get-involved/groups-sections-and-technical-divisions/technical-divisions/technical-divisions-community-pages/tribology-division.
STLE Fellow Dr. Robert Jackson is the Albert Smith Junior Professor in the Department of Mechanical Engineering at Auburn University in Auburn, Ala. He obtained his bachelor of science degree, master of science degree and doctorate degree from the Georgia Institute of Technology. He has published widely in a variety of respected technical journals, and his research contributions have been recognized by awards from both the ASME and STLE. In 2012 he initiated one of the first undergraduate minors in the field of tribology, for which he received the 2014 STLE recognition for Commitment to the Advancement of the Science of Tribology. You can reach him at jacksr7@auburn.edu or (334) 844-3340.
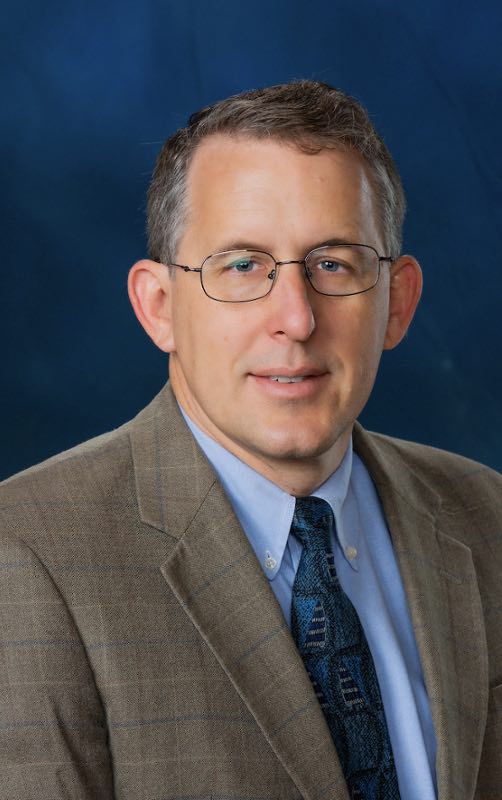
Dr. Robert Jackson
KEY CONCEPTS
•
The increase in the number of electric vehicles and other electric devices raises the importance of the study of electrical contact and lubrication where electrical current can be desired or not across a metal contact in a mechanical device (e.g., desired in cell phones, but not in bearings or gears
•
Based on a mixed lubrication model, rougher surfaces, higher forces and lower viscosities were found to lower the contact resistance by allowing the metal surfaces to cross the non-conductive lubricant film thickness.
•
Silver nanoparticle lubricants and ZDDP enhanced dodecane lubricant both reduced friction and wear between surfaces; however, ZDDP caused electrical contact resistance to increase significantly.
•
In contrast, a silver nanoparticle lubricant had a lower friction coefficient and a lower change in electrical resistance than the ZDDP enhanced dodecane lubricant—and may prevent arcing damage to the surfaces.
Electrical contact and lubrication of those contacts are growing topics because of the increase in electric vehicles and other electric devices. Jackson notes that generally there are two kinds of electrical contact:
1.
connectors or switches where electrical current is desired (e.g., charging cell phones, electric vehicles, electronics) and
2.
mechanical contact where electrical current is not desired (e.g., bearings, gears).
The motivation might be different, but the physics behind the two types of electrical contact are essentially the same.
A typical connector operates by having a pin with a spring that loads a metal contact against the pin. There are always gaps in these contacts that can be filled by a lubricant but more often are filled by air
(see Figure 1). It is almost impossible to apply enough pressure between the pin and the metal to not have gaps. Where the metals connect are called asperity contacts. When current is applied, it goes across the metal contacts or peaks (i.e., asperity contacts) shown in Figure 1. These asperity contacts bottleneck the electrical current and cause spreading resistance. Heat can grow at these contacts, which can oxidize, degrade or wear, leading to additional contact resistance over time.
Figure 1. Electrical connectors. Bottom half of figure courtesy of Angadi, S., Wilson, W. E., Jackson, R. L., Flowers, G. T. and Rickett, B. I. (October 27-29, 2008), “A multi-physics finite element model of an electrical connector considering rough surface contact,” The 54th IEEE Holm Conference on Electrical Contacts, Orlando, Fla. Available at https://ieeexplore.ieee.org/document/4694941.
Even though these contacts are supposed to be stable, they can get moved around, especially when in electric vehicles. Those vibrations can cause the contacts to change with time, and that change is called fretting wear.
1, 2, 3 Fretting is due to small amounts of sliding without the contact areas ever completely separating. It is usually reciprocating.
In a spherical type of contact, in the middle is a stick zone, while on the edges, a sliding zone develops. When the sliding zone is small, particles are not moved away from the surface, which can result in more abrasion. This also can combine with corrosion.
Corrosion is a different mechanism. Fretting is just small amplitude wear, while corrosion is chemical degradation on the surface (e.g., oxides forming on the surface). The oxide is usually less conductive and can cause problems in contact resistance. Corrosion often combines and overlaps with fretting and other forms of wear to accelerate the degradation process.
Wear occurs in automobile connectors where fretting and corrosion are found in the contacts. This is a very practical example as this type of wear is one of the leading problems in vehicles.
4 Corrosion results in a chemical reaction that leaves a changed surface composition. A lubricant can alleviate both of these issues. To identify if corrosion is present, a scanning electron microscope (SEM) analysis of the surface can be performed to see if there is an oxide present, and also to identify the type of wear.
5
The mechanical components of wind turbines, with high amounts of electric power being generated in the turbine, can have stray currents going across them. This also happens with electric vehicles.
6 There are many tribological components in electric vehicles even without having an internal combustion engine
(see Figure 2).
Figure 2. Electric vehicles and energy.
Current leakage in electric vehicles has several sources, but often is from the invertor that transforms electrical energy from the battery so it can be used by the motor. Electric motor bearings and wheel bearings can have this current leakage traveling across the lubricant film. Grounding and other solutions are available, but they may not be permanent or may add significant cost. When a contact is electrified, added surface damage can be seen, including pitting, frosting, fluting, spark tracks and welding, while the lubricant can show damage through lubricant degradation, microbubble effects and electrowetting.
7
Typical tribology contact modeling shows a rough surface with asperity contacts and possibly a lubricant in between
(see Figure 3). With an electrical contact, electrical flow occurs mostly where the metals touch. If the lubricant film thickness gets large enough, the metals come out of contact and do not allow current to be conduct- ed easily. Looking at the Stribeck curve
(see Figure 4), roughness can be ignored in the full-film lubrication regime but must be considered in mixed and boundary lubrication.
Figure 3. Typical region of mixed lubrication. Figure courtesy of Jackson, R. L. (2004), “The wear and thermo-elastohydrodynamic behavior of thrust washer bearings under non-axisymmetric loads.” PhD Dissertation, Georgia Institute of Technology.
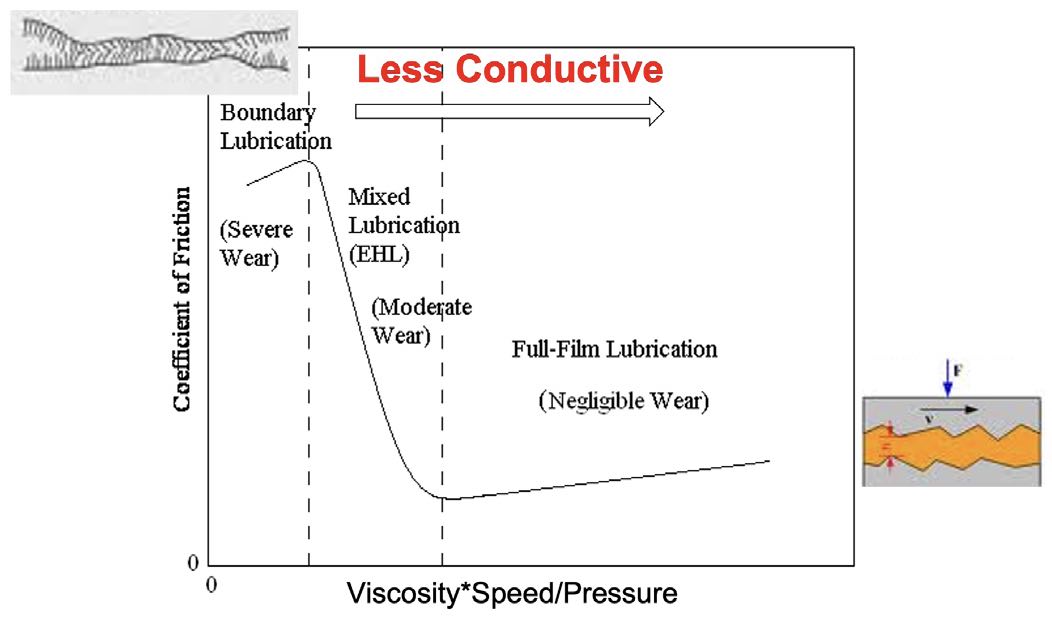
Figure 4. The Stribeck curve.
Modeling asperity contacts
A simple model was developed using the following assumptions:
•
Materials are homogeneous and continuous.
•
Wear and corrosion of the surfaces are not included.
•
The effects of lubricant chemistry at the interfaces, such as tribofilm formation, are not directly considered.
•
The quasi-static model neglects time dependent effects such as vibrations and squeeze film effects.
•
Thermal effects, such as heat generation due to Joule heating and friction, are ignored, along with temperature dependent properties.
Figure 5. Model assumptions. Figure courtesy of Jackson, R. L. and Angadi, S. V. (2022), “Modelling of lubricated electrical contacts,” Lubricants, 10 (3), 32. Available at https://doi.org/10.3390/lubricants10030032.
A very simple model is shown in Figure 5 based on those model assumptions.
8 In this model, when considering the lubrication part, the modified Reynolds equation is employed to consider hydrodynamic lubrication and the effect of roughness. This model considers how, when the film gets very thin, the roughness obstructs the flow of the lubricant. The differential equation was solved using the center finite difference method. For the solid model, statistical mathematics were used to try to mimic a real rough surface with multiple asperities. In other words, the model considers how those asperities distribute over different heights
(see Figure 6).
Figure 6. Statistical rough surface contact model.
The equation in Figure 6 can be used to make a prediction for electrical contact resistance based on the solid asperity contact.
9 The equations are solved iteratively until the forces balance. Some solutions are shown on Figure 7. As velocity increases, as shown with the Stribeck curve, a film is generated between the contacts and the friction drops. However, with more roughness, the film is broken and friction increases. Increased velocity yields increased contact resistance. More roughness breaks the lubricating film and improves contact resistance by maintaining electrical contact. Any given situation can have competing concerns, depending on what is being designed for.
Figure 7. Effect of roughness. Figure courtesy of Jackson, R. L. and Angadi, S. V. (2022), “Modelling of lubricated electrical contacts,” Lubricants, 10 (3), 32. Available at https://doi.org/10.3390/lubricants10030032.
Experimental results
Nanoparticles are cutting edge lubricant additives. They have gained some traction in industry but are not yet widely used. A colloid is formed when small particles are suspended in a fluid. Common examples are milk or toothpaste. The trick is to make stable colloids where the particles don’t fall out as sediment. Chemists usually use surfactants on the surface of the particles to keep them in solution. This is critical for a colloidal nanoparticle lubricant to be stable and have a practical shelf-life.
In this research, Jackson’s team has studied silver colloids the most, with the guidance of Prof. German Mills from the Auburn University Department of Chemistry and Biochemistry. The team has developed a silver nanoparticle additive made up of concentrated silver colloids that are 1.3 by weight percent or about 6 nanometers in diameter. These mixtures are usually made with dodecane, a hydrocarbon oil.
Zinc dialkyldithiophosphate (ZDDP) is the most common friction and wear additive. It was originally developed as an antioxidant and reduces wear. There was a movement to phase it out as it might damage catalytic converters. ZDDP and other extreme pressure additives are added to the lubricant or oil where the asperities in contact under high pressures or high temperatures can generate chemical reactions. These reactions generate a tribofilm on the surface that is good for reducing wear but not for conducting electricity.
10
The team used a reciprocating test setup to allow for an improved electrical signal path
(see Figure 8).11 Figure 9 shows friction results with pure dodecane, silver and ZDDP. The silver and ZDDP produce a large change in resistance.
Figure 8. Example reciprocating test.
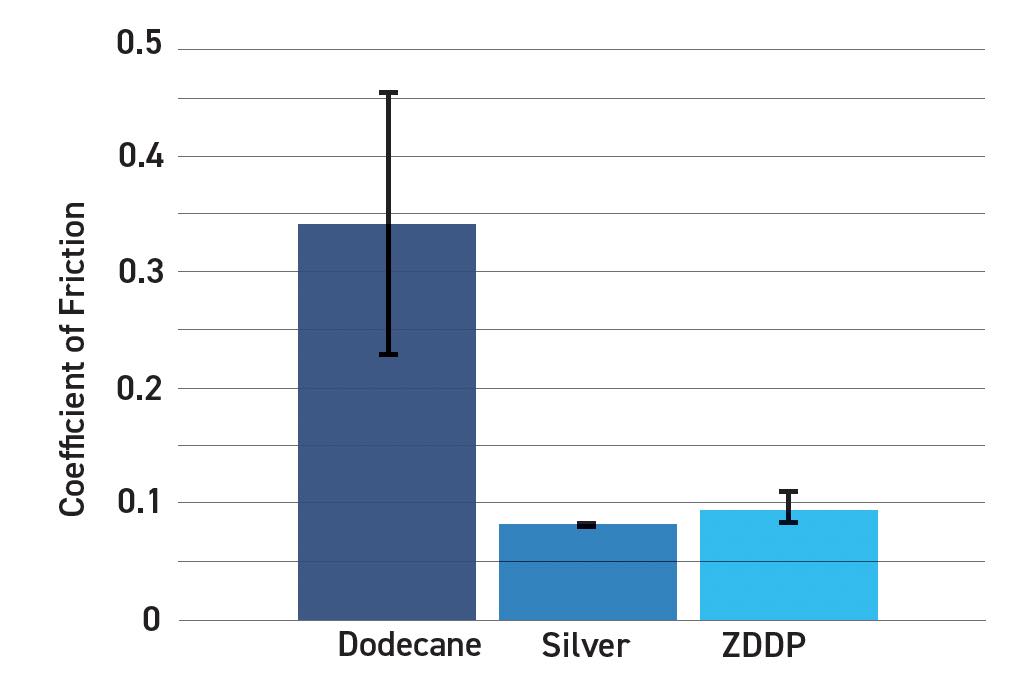
Figure 9. Reciprocating test friction. Adapted from Ref. 11.
Testing greases
In an electrified lubricated contact, the asperity contact can be relatively conductive. If a film develops, it may electrically insulate the surfaces. However, if a leakage current is present, it could build up charge between the surfaces. Eventually an arc can occur and cause damage.
The team tested electrically conductive nanoparticle additives with greases used in electric vehicles.
12 As the film thickens it changes the relationship between the current and the amps. The team tested four different polyurea grease samples: mineral grease (MG), synthetic grease (SG), fully formulated MG (FF MG) and fully formulated SG (FF SG). These were combined into three different formulations: base grease, dodecane (Do) and dodecane with nanoparticles (NP), resulting in 12 different grease samples.
These are fully formulated NLGI 2 greases with no extreme pressure additives present. The greases were ISO 100 (i.e., 90 to 10 kinematic viscosity in centistokes [cSt]) with antioxidant and anticorrosion protection for the finished grease. All of the 12 formulations were tested in triplicate.
When voltage was applied, the wear appeared as small pits forming under the current. The SEM imaging confirmed this was electrical pitting. Before applying motion, resistance was low; when motion was applied, resistance increased. The resulting data display a lot of features and noise, which may be related to arcing, but the team is continuing to study the data. When looking at profilometry, as voltage was applied, pits began forming in the surfaces. Wear scars showed interesting features. Most of the pits accumulated at the ends of the scars, which is perhaps where the arcing occurs. This suggests that most of the scarring occurs when the electric vehicle stops and starts or changes speed.
Figure 10. SEM surface damage comparison.12
Figure 10 shows the percent of surface damage with the different lubricants. Nanoparticle greases showed lower surface damage than the other lubricants. The additives and dodecane may change the electrical conductivity of the grease.
Conclusions
This research and modeling resulted in the following conclusions:
•
Based on a mixed lubrication model, rougher surfaces, higher forces and lower viscosities are found to lower contact resistance by allowing the metal surfaces to cross the nonconductive lubricant film thickness.
•
Both the lubricant with silver nanoparticles and with ZDDP drastically reduced the friction and wear between the metal surfaces.
•
However, the ZDDP created a non-conductive tribofilm on the surface that caused the electrical contact resistance to increase significantly.
•
The silver nanoparticle lubricant had a lower friction coefficient and change in electrical resistance than the ZDDP enhanced dodecane—and may prevent arcing damage.
•
Electrical current increased the wear on the contacts measurably compared to conventional rolling. Pitting with carbon and oxygen suggested micro-scale arcing.
•
Greases with silver nanoparticles decreased the surface pitting damage compared to all other lubricants tested
REFERENCES
1.
Xie, F., Flowers, G. T., Chen, C., Bozack, M. J., Suhling, J. C., Rickett, B. I., Malucci, R.D. and Manlapaz, C. (2009), “Analysis and prediction of vibration-induced fretting motion in a blade/receptacle connector pair,”
IEEE Transactions on Components and Packaging Technologies, 32 (3), pp. 585-592.
2.
Fu, R., Choe, S. Y., Jackson, R. L., Flowers, G. T., Bozack, M. J., Zhong, L. and Kim, D. (2012), “Vibration-induced changes in the contact resistance of high power electrical connectors for hybrid vehicles,”
Components, Packaging and Manufacturing Technology, IEEE Trans., 2 (2), pp.185-193.
3.
Kubiak, K. J., Mathia, T. G. and Fouvry, S. (2010), “Interface roughness effect on friction map under fretting contact conditions,”
Tribology International, 43 (8), pp. 1500-1507.
4.
Hilmert, D., Yuan, H. and Song, J. (2022), “The analysis of failure mechanisms of electrical connectors in long-term use field vehicles,”
2022 IEEE 67th Holm Conference on Electrical Contacts (HLM), Tampa, Fla., pp. 1-8, doi: 10.1109/HLM54538.2022.9969820.
5.
Flowers, G. T., Xie, F., Bozack, M. J. and Malucci, R. D. (2004), “Vibration thresholds for fretting corrosion in electrical connectors,” in
IEEE Transactions on Components and Packaging Technologies, 27 (1), pp. 65-71, doi: 10.1109/TCAPT.2004.825791.
6.
Farfan-Cabrera, L.I. (2019), “Tribology of electric vehicles: A review of critical components, current state and future improvement trends,”
Tribology International, 138, pp. 473-486.
7.
Prasad, S. and Krishnanunni, S. (2020), “Review on analysis of failures modes in the electric vehicles due to electric bearings,”
International Research Journal of Engineering and Technology (IRJET), 7 (12), pp. 1722-1725.
8.
Jackson, R. L. and Angadi, S. V. (2022), “A model of contact in lubricated sliding rough electrical contacts,”
Lubricants, 10 (3), p. 32. Available at
https://doi.org/10.3390/lubricants10030032.
9.
Greenwood, J. A. and Williamson, J. P. (1966), “Contact of nominally flat surfaces,”
Proceedings of the royal society of London. Series A. Mathematical and physical sciences, 295 (1442), pp. 300-319.
10.
Mourhatch, R. and Aswath, P. B. (2011), “Tribological behavior and nature of tribofilms generated from fluorinated ZDDP in comparison to ZDDP under extreme pressure conditions—Part II: Morphology and nanoscale properties of tribofilms,”
Tribology International, 44 (3), pp. 201-210. Available at
http://dx.doi.org/10.1016/j.triboint.2010.10.035.
11.
Jackson, R. L., Coker, A. B., Tucker, Z., Hossain, M. S. and Mills, G. (2019), “An investigation of silver nanoparticle laden lubricants for electrical contacts,”
IEEE Trans. on Components, Packaging, and Manufacturing Tech, 9 (2), pp.193-200, doi: 10.1109/TCPMT.2018.2887402.
12.
Bond, S., Jackson, R. L. and Mills, G. (2024), “The influence of various grease compositions and silver nanoparticle additives on electrically induced rolling-element bearing damage,”
Friction. Available at
https://doi.org/10.1007/s40544-023-0837-4.
Andrea R. Aikin is a freelance science writer and editor based in the Denver area. You can contact her at pivoaiki@sprynet.com.