HIGHLIGHTS
•
A new strategy for 3D printing stainless steel involves controlling the thermal stability of the metal alloy’s microstructure by using the laser as a “microscopic hammer.”
•
Two laser powder bed fusion strategies known as “H” and “L” were developed, which produce metal alloys with high and low thermal stability.
•
Using this technique, 316 stainless steel underwent substantial yet controlled microstructure changes compared to the same alloy processed in a conventional manner.
Research is ongoing to improve the efficiency and reduce the production cost of additive manufacturing, which also is known as 3D printing. Metal alloys have been particularly difficult to process using one of a number of 3D printing techniques. For example, the 3D printing technique known as laser powder bed fusion has caused the formation of pores that can shorten fatigue life because fatigue cracks are generated in the metal during the process.
A previous TLT article
1 discussed work conducted to circumvent the need for high temperatures and expensive equipment in additive manufacturing. Copper metal was stabilized in an aqueous environment through the use of a liquid metal (eutectic gallium indium). A solid-liquid-liquid gel was produced that can be used as a 3D printing ink by extrusion through a nozzle at room temperature. The key to the process is the liquid metal forms small bridges between copper particles to stabilize the gel in water. Highly conductive parts can be prepared and stressed through additional processing to change its shape.
Dr. Matteo Seita, Granta Design assistant professor in the Engineering Department at the University of Cambridge in Cambridge, UK, says, “Processing of metal has been conducted using the ‘heat and beat’ approach since the Bronze Age when a blacksmith would fabricate metal objects through the use of hot and cold forging followed by quenching using oil and water. In this manner, heat is used to soften and beating is done to harden the metal workpiece. The result is that metal can be transformed into a specific shape while retaining desired properties such as flexibility and strength. Controlling internal structure of metal is why this approach continues to be used.”
Additive manufacturing utilizes a layer- by-layer material consolidation process to produce metal parts that can have very complex geometries. Seita says, “Unfortunately, the problem with additive manufacturing is that once a part is manufactured, it is very difficult to control the internal structure in a similar manner to the ‘heat and beat’ approach. As a result, post-processing steps such as heat treatment are needed to adjust the internal structure of the metal. This leads to added cost and inefficiency.”
Seita and his colleagues have now developed a new approach using laser powder bed fusion to manipulate a metal alloy’s microstructure while circumventing the ‘heat and beat’ approach.
Microscopic hammer
The researchers determined that irradiating the material with special laser “strategies” can lead to a controlled reconfiguration of the metal alloy’s microstructure once the part is placed in a furnace at relatively low temperature. Seita says, “The key is to control the thermal stability of the metal alloy’s microstructure by using the laser as a ‘microscopic hammer’ to engineer a certain defect density—called dislocations—and by melting the metal a second time to relax the structure, which forms upon solidification from the melt.”
To achieve this objective, the researchers developed two laser powder bed fusion strategies, which are designated as “H” and “L.” Seita says, “These two methods produce metal alloys with high and low thermal stability, respectively. They differ in how close the metal tracks are to one another in a single metal layer and in how often the same layer is scanned by the laser.”
In conducting this study, the researchers worked with 316 stainless steel. Seita says, “This metal alloy is easy to work with in laser powder bed fusion, and we have a lot of experience in working with it.”
The researchers evaluated 316 stainless steel using the “H” and “L” methods. Seita says, “The metal alloy produced using the “H” method exhibits a more heterogeneous but less defective solidification structure, while that produced using the “L” method is more relaxed and uniform but contains many more dislocation.”
The low thermal stability of 316 stainless steel produced by the “L” method leads to complete recrystallization, while the material produced using the “H” method does not. Seita says, “The result was the production of a metal alloy that underwent substantial, yet controlled microstructure changes compared to 316 stainless steel 3D printed in a conventional manner.”
By controlling the thermal stability of 316 stainless steel, the researchers can tailor the microstructure of the metal alloy. This approach produces metal alloys with alternating regions of strong and tough material that exhibit properties comparable to processing done through the traditional “heat and beat” technique. Seita says, “Besides having control over the metal alloy’s microstructure, we think this method could help reduce the costs of metal 3D printing, which could, in turn, improve the sustainability of the metal manufacturing industry.”
An example of a 3D printed metal part using this new approach is shown in Figure 3.
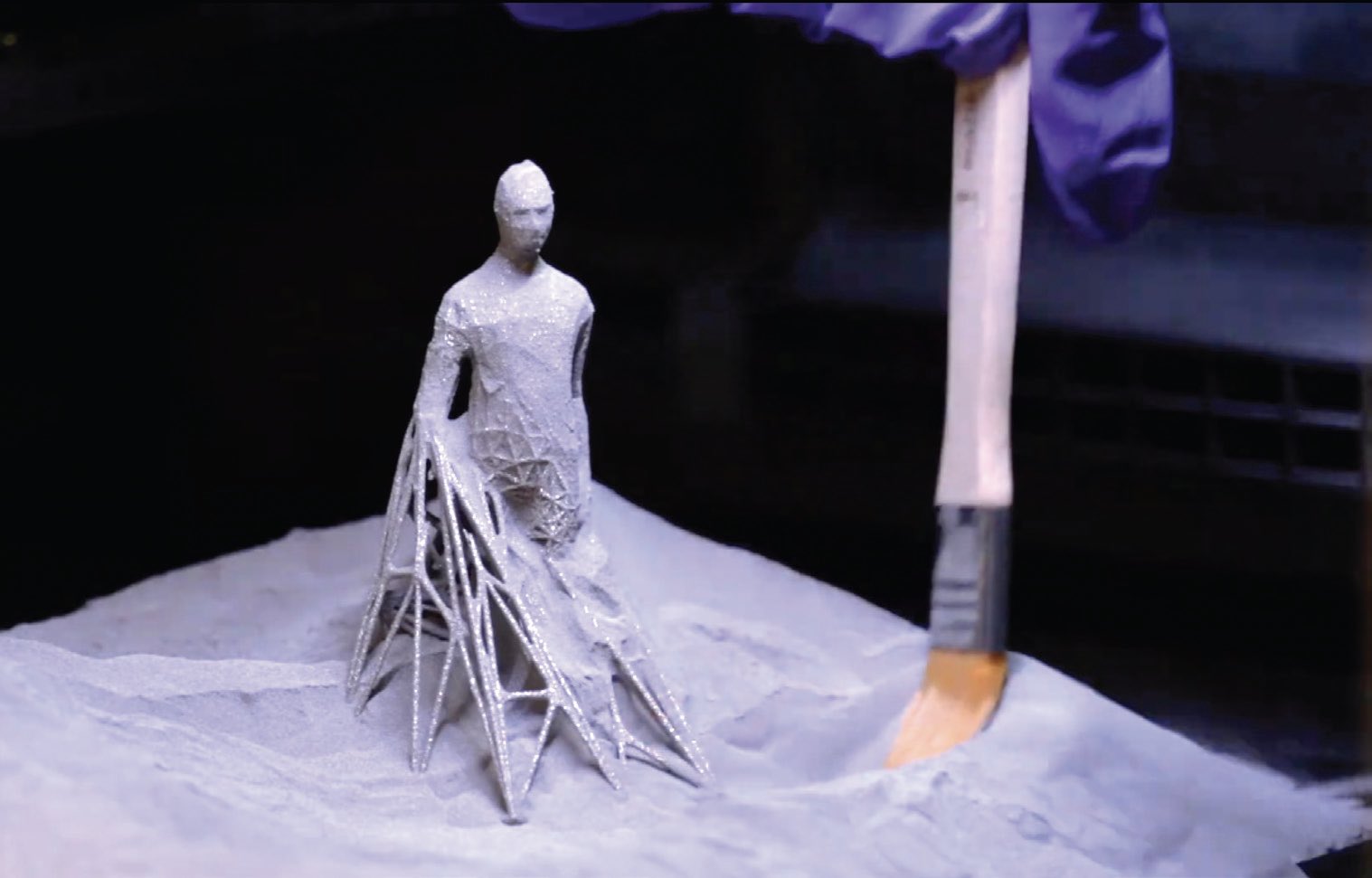
Figure 3. The figure shown in this image was 3D printed using a new technique that combines the ability to engineer the structure and properties of metals using traditional machining methods with the ability of additive manufacturing to prepare complex shapes. Figure courtesy of the University of Cambridge.
Future work will involve close examination of the microstructure of 316 stainless steel at the local level. Seita says, “We also intend to evaluate other metals such as nickel base superalloys using this modified laser powder bed fusion approach.”
Additional information can be found in a recent article
2 or by contacting Seita at
ms2932@eng.cam.ac.uk.
REFERENCE
1.
Canter, N. (2023), “Additive manufacturing using metallic gels,” TLT,
79 (11), pp. 12-13. Available
here.
2.
Gao, S., Li, Z., Petegem, S., Ge, J., Goel, S., Vas, J., Luzin, V., Hu, Z., Seet, H., Sanchez, D., Swygenhoven, H., Gao, H. and Seita, M. (2023), “Additive manufacturing of alloys with programmable microstructure and properties,”
Nature Communications, 14, Article Number: 6752.