KEY CONCEPTS
•
Synthetic esters may be the most promising base oils for electric vehicle applications—especially in terms of electrical conductivity, thermal control and even the prevention of varnish formation.
•
Because of the natural polarity of synthetic esters, they have applications that extend beyond base oil.
•
Chemist expertise backed by data technology can produce an almost unlimited number of synthetic ester iterations.
Synthetic esters have diverse molecular structures designed and controlled by a common organic reaction—the esterification of various natural or synthetic acids and alcohols. Major properties can be tailored and predictable. Also due to the inherent polarity of synthetic esters, they are functional beyond base oils.
The polar nature and various structures give ester lubricants many benefits such as high viscosity index, high lubricity, robust tribo-film strength, excellent low temperature properties, low volatility and high flash/fire points.
Easy access to biogenic raw materials, such as natural fatty acids and alcohols, facilitates the application of esters to many biodegradable/food-grade and environmentally acceptable lubricants.
The major downsides of esters include high cost, hydrolytic stability and seal compatibility. These could be controllable through optimization of structure-property-performance relationships.
Since most electric cars run on high-energy-density compact batteries under high-speed, high-load and high-temperature environments, electric vehicle (EV) lubricants require new functional fluids with electrical properties such as low traction, better stability and better thermal control.
To date, synthetic esters (Group V) and polyalphaolefin (PAO) (Group IV) have been the most promising base oil candidates for meeting those requirements. However, in some electromagnetic stress circumstances, esters are well-fitted for achieving a proper/subtle balance between dielectricity and conductivity.
There are some useful structure- property-performance relationships of ester base oils in terms of structure control and effects of chemical, physical, viscometrical, electrical and thermal properties for EV-related products.
The objective is to develop the robust structure-property-performance relationships of synthetic esters with a focus on electrical/thermal properties and the application to high performance EV lubricants.
Key advantages
According to STLE member Dr. Alexei Kurchan, applications manager, Cargill Bioindustrial, the main difference between traditional base stock and synthetic esters is the defined molecular structure of the esters in contrast to the broad distribution of Group I, II, III and—to a lesser degree—Group IV base stock. He adds that synthetic esters are highly tailorable by combining different acids and alcohols to achieve properties required for EV applications.
STLE member Gene Zehler, technical support manager, BASF Corp., summarizes the advantages of synthetic ester base stock in the following list. They can:
•
Improve oxidative and thermal stability and cleanliness at high temperatures—extending service life
•
Optimize material compatibility, additive solubility, low temperature fluidity and cleanliness in blends with PAO and Groups II, III and III+ base stocks
•
Reduce flammability or volatility
•
Improve frictional performance and energy efficiency
•
Increase biodegradability or renewability
•
Optimize thermal and electrical conductivity.
Due to the long service life of EV fluids, varnish formation is possible in systems with direct cooling of electrical components such a motors, batteries and inverters; this points to another advantage of synthetic esters. “At the present time, it is unknown if varnish formation can have a negative effect on the properties of electric components, such as heat conductivity and dielectric properties of the insulating materials,” Kurchan says. “Esters are known to help prevent varnish formation due to higher polarity and better solvency.”
Performance requirements
Given the existing applications for synthetic esters, Zehler notes the following performance requirements: they need to withstand high and low service temperature extremes; exhibit frictional efficiency; have a long service life; protect the machinery; and, in some applications, they need to be biodegradable, renewable or have approval for indirect food contact
(see Existing Applications for Synthetic Esters).

Existing applications for synthetic estersA
Major application areas of synthetic esters in lubricants include:
•
Gas turbines—aviation and power generation
•
Hydraulic fluids
•
Compressors for air and refrigerants
•
High temperature chains and bearings
•
Engine crankcases
•
Gearboxes—industrial, marine, transportation
•
E-driveline fluids and coolants
•
Electrical and transformer fluids
•
Metalworking fluids
•
Heat transfer fluids/coolants
•
Textile lubricants
•
Greases
•
Two stroke oils
•
Biodegradable lubricants
•
Biobased/renewable lubricants.
A. Per Gene Zehler, technical support manager, BASF Corp.
STLE member Hoon Kim, application technology manager, Zschimmer & Schwarz Inc., observes that, although many components of internal combustion engines (ICEs) and EVs are the same, the primary difference is how the power source and powertrain system initiate and transform mechanical motions during operation.
“For example, ICEs are powered by fuel combustion creating thermal energy, and the thermal energy is sequentially converted into mechanical energy by the engine,” he explains. “Instead, EVs utilize electrical energy stored in the battery as the power source and utilize the e-motor for energy transformation from electrical energy to mechanical energy. Those differences require many system accommodations for EVs including the drivetrain system, operating environment, component materials, operation speed, load and temperature. Consequently, the EV system differences require new performance criteria for EV lubricants.”
These changes are summarized in Table 1.
Table 1. System changes and performance requirements
Kim continues, “For example, high cooling capacity lubricants are essential for minimizing heat generation from the e-motor, e-battery and single-speed transmission. High voltage or high electric current environments require proper electrical properties to tackle potential hazards and energy loss. An increase in copper components and a highly charged electric field accelerate the corrosion process. Thus, better anti-corrosion performance is one of the key elements for EV lubricants.”
In addition, new material compatibility is required due to polymeric insulation systems. Relatively high-speed, high-load and high-temperature operating conditions require enhanced antiwear performance and fuel efficiency.
The design of the molecular structure
As Kurchan notes, one of the hallmarks of synthetic esters is the defined molecular structure. STLE member Jared Nelson, laboratory manager, product and application development, Emery Oleochemicals, LLC, also points out the endless design potential of expert chemists backed by leading-edge technology.
“With a near-infinite number of possibilities when designing synthetic esters, a massive proportion of the development cycle depends on the historical understanding and expertise of chemists in the field,” he says. “However, increasingly, the use of statistical tools (design of experiments, DOE) and machine learning are guiding our molecular structure optimization.”
He continues, “But since each permutation introduces multiple variables (chain length, branching and other molecular features) into a given structure, we are finding it more and more critical to capture and organize data in meaningful ways that allow us to extract the information that is relevant, and identify which data are coincidental or inconsequential. While new possibilities arise from statistical and IT tools, the experience and knowledge of R&D personnel about the structure-property relationship of ester molecules is still the starting point for the majority of new product and component developments.”
Fundamentally, the process of esterification is extremely basic—involving a chemical reaction between a carboxylic acid and an alcohol. “The customization primarily happens on the frontend, by choosing the appropriate alcohol(s) and acid(s) to achieve the desired properties,” Nelson explains. It is often iterative in nature—one combination may achieve some of the desired properties but will usually necessitate additional changes that lead to a compromise in properties or push the limits of what can be achieved even further. We are often preparing multiple samples at a time—altering one parameter at a time—to explore a given space, and submitting those for relevant testing, after which we review the data to find what can/should/must be improved.”
Development challenges with synthetic esters for EVs
Per Nelson’s experience, there are four main challenges with developing new EV lubricants:
•
Performance. As requirements for fluid properties, composition and safety change, the development of products that meet these requirements becomes increasingly challenging. Although developers can often lean on what has been learned from other industries or efforts in the past, many of the problems they are facing today involve additional requirements (higher flash point, lower viscosity, better overall tribology) without sacrificing the other properties that have allowed those applications to advance to their current state—all while balancing cost versus performance. Product development is inherently fraught with trade-offs; optimizing one parameter affects other properties. Occasionally they are synchronized, but incremental advances in lubricant performance are built out of multi-variate optimization which, to overcome, involves significantly greater resources.
•
Testing. In addition to the technical challenges of developing innovative lubricants and thermal management fluids, testing requirements have become more stringent and sometimes prohibitive when it comes to achieving an EV manufacturer’s requirements. This can lead to additional processing steps and/or higher purity feedstocks which drive up costs.
•
Targets. Since the EV lubricants industry is still developing, there is very little guidance in the form of OEM specifications. Manufacturers are struggling to better understand what is going to be important in five to 10 years regarding lifecycle assessments. New EV fluids will need to meet some existing specifications, but new items and properties are being added as those trends emerge. Therefore, new test methods are still in development (or a standardization phase) making the evaluation and rating of innovations challenging.
•
Regulatory. Across the landscape of growing listing and regulatory systems, the chemical industry faces increasing restrictions and regulation that temper innovative forces. But a global presence and compliance is required now more than ever to ensure customers have flexibility in an international market and a consistent supply chain.
Thermal control benefits for EVs
STLE member Pedro Cawich, tribology specialist at Idemitsu Lubricants America Corp., points out that the key aspects of an EV coolant system can vary widely. “Now, if we strictly look at the properties of a fluid for an e-axle, which consists of an inverter, reduction gear and motor, then there are two main properties required for the fluid—motor efficiency and gear performance,” he says. “To improve motor efficiency, we need to improve motor cooling performance, hence thermal management is a key requirement of the fluid. If we need to improve gear performance, then we need to improve durability by improving component protection from the fluid.”
Cawich continues, “If we look at Newton’s law of cooling, we see that the heat transfer amount is related to the heat transfer coefficient of the fluid.
1 Thus, improvement of heat transfer coefficient is important. Now, if we look at the equation for the heat transfer coefficient, we can see that kinematic viscosity and thermal conductivity are directly related to the heat transfer coefficient. Therefore, oils with lower kinematic viscosity and higher thermal conductivity improve the heat transfer of a fluid.”
Cawich recounts a study his company conducted that showed a lower viscosity base oil had a much higher temperature drop compared to a higher viscosity base oil. In some modeling, they saw that fluids with higher thermal conductivity show higher heat transfer when compared with other properties such as specific heat or density.
The study also demonstrated that synthetic base oils typically have higher thermal conductivity than mineral base oils provided kinematic viscosity is the same for both. “Group V > Group IV > Group III base oil is the general order for thermal conductivity that we observed,” Cawich says. “With a higher thermal conductivity there will be a higher heat transfer (at least theoretically). Additionally, in a recent study that we conducted on how to improve motor efficiency, we observed that synthetic base oils can help to improve efficiency due to their lower traction coefficient.”
How thermal, electrical and other properties contribute to EV energy efficiency
Permittivity, loss of power factor, resistivity and breakdown voltage could be important electrical properties for EV lubricants, Kim says.
2 “Generally speaking, low permittivity, low loss factor, high power factor and high resistivity are desirable for maximizing energy efficiency and minimizing electric energy loss,” he says. “Breakdown voltage is determined by the initiation point of the breakdown using an oil breakdown voltage tester. Typically, a high value indicates high dielectric strength. The design versatility of synthetic esters is ideally suited to achieve desired polarity of the molecules and consequently to optimize the balance of electrical properties. Synthetic esters inherently have a low risk of static shock as well.”
All of this points to the energy efficiency advantage of synthetic ester fluids.
“Per our latest investigation, good correlations exist between viscometrical properties and electrical properties that are directly associated with energy loss of EV systems,” Kim adds. “For example, viscosity (VIS) at 40 °C and 100 °C of synthetic esters indicated a good correlation with dielectric constant (DC), loss factor (LF) and resistivity (R)
(see Figure 1a and b).”
Figure 1. Correlations between viscometrical properties and electrical properties directly associated with EV system energy loss. Figure courtesy of Zschimmer & Schwarz Inc.
Kurchan notes that the well-defined molecular structure of the esters allows creation of base oils with inherently lower traction coefficients, which, in elastohydrodynamic and mixed regimes, reduced parasitic losses due to friction.
Driveline fluids for EVs
Per Zehler, driveline fluid for EVs is a relatively new and rapidly evolving application area that is an exciting opportunity for formulators, OEMs and component suppliers to work together to develop innovative next generation fluids.
“Fluids for e-vehicle driveline service require new base oil concepts to meet the evolving targets for low viscosity, frictional efficiency, thermal conductivity, oxidative stability and electrical conductivity,” Zehler says. “Ester base stocks are uniquely capable in these areas and are an excellent and synergistic choice as co-base stocks for use with Group III or PAO stocks. For instance, to compare the level of improvement in frictional efficiency that different esters can provide, Figure 2 shows the improvement in traction coefficient that the addition of 20% of various esters can provide to a 3 cSt Group III base stock. Ester base stocks can help to improve the frictional efficiency of the next generation EV driveline systems that will operate at very high speeds.”
Figure 2. Frictional efficiency of Group III base stock with 20% ester at 80 ⁰C. Figure courtesy of BASF Corp.
Zehler explains that the next generation drive and motor systems for EVs will operate at higher temperatures than conventional driveline applications. This means the ability of the new fluids to act as a coolant and heat transfer fluid is even more important. Thermal conductivity and heat capacity measurement show how well the new fluids can transfer heat away from sensitive components. Selected esters offer advantages in these areas
(see Figures 3 and 4).
Figure 3. Thermal conductivity of 3 cST base stocks. Figure courtesy of BASF Corp.
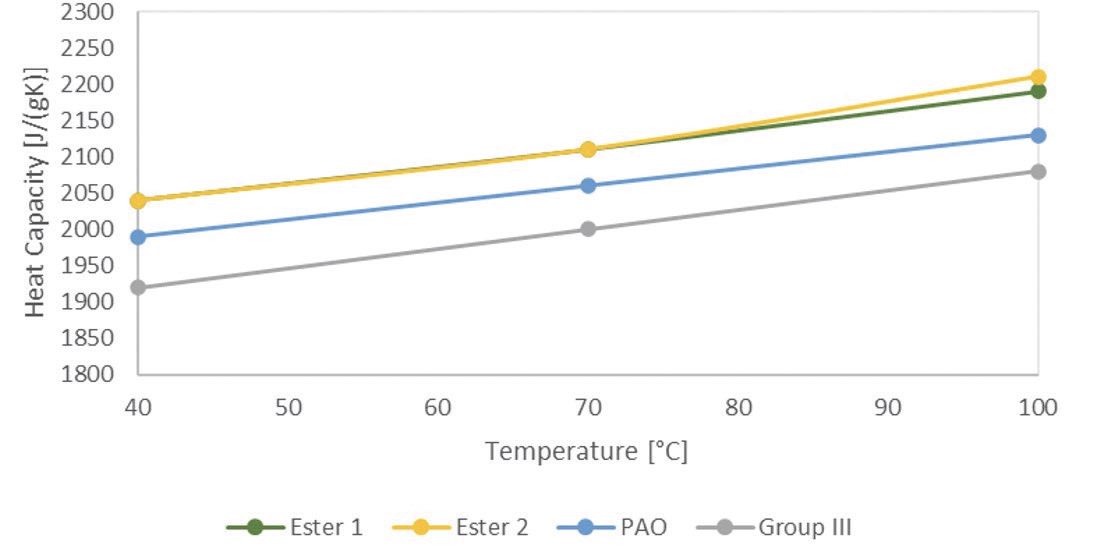
Figure 4. Heat capacity 3 cST base stocks. Figure courtesy of BASF Corp.
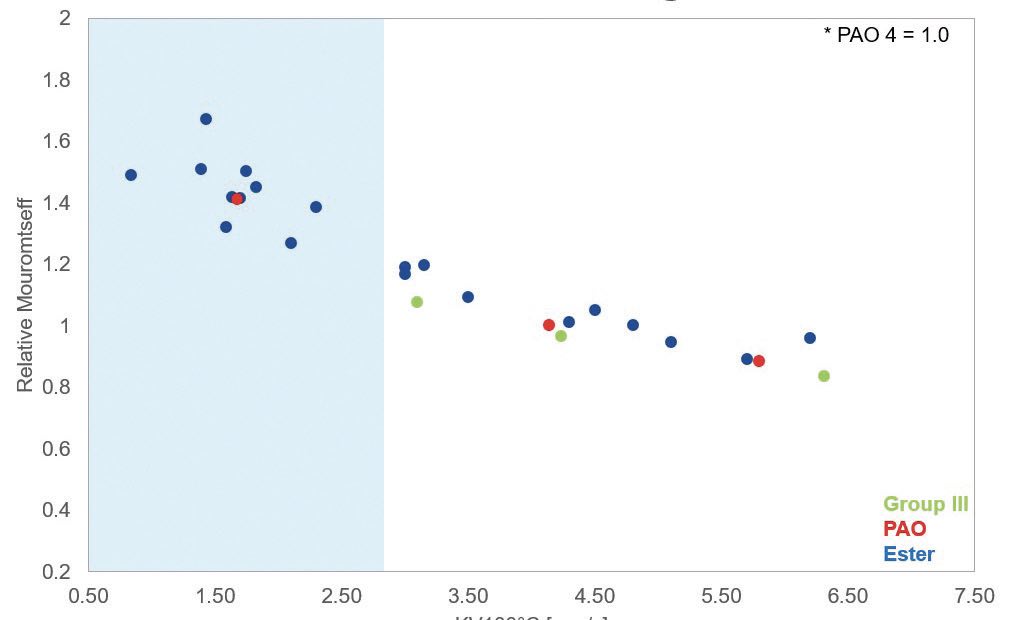
Figure 5. Relative Mouromtseff number at 100 ⁰C. Figure courtesy of BASF Corp.
Per Zehler, Figure 5 compares many base stocks where the Mouromtseff number for PAO 4 has been normalized to a relative value of 1.0. Ester base stocks with lower viscosities are now frequently being considered for use in next generation fluids. The Mouromtseff number is a calculated indicator of fluid heat transfer efficiency using dynamic viscosity, density, thermal conductivity and heat capacity.
Comparisons of the Mouromtseff number provide more detail into the ability of a fluid to transfer heat. There is a beneficial influence of using both lower viscosity formulations and esters in the next generation fluids.
“Since the new fluids will have direct contact with motors and electrical connections, they will need to have good dielectric function as well,” Zehler says. “Breakdown voltage measures the ability of a dielectric fluid to withstand severe electrical stress without a catastrophic failure, such as an arc or flashover between electrodes or contacts. For a dielectric fluid, a higher kV result is considered better. Esters typically have much higher breakdown voltage than hydrocarbon fluids like Group III or PAO base stocks. The use of ester as a co-base stock with a hydrocarbon fluid will increase the breakdown voltage result of the finished formulation
(see Table 2).”
Table 2. Breakdown voltage comparison of base stocks
Conclusions
Cawich would like to see OEMs start to optimize machinery for new EV-friendly fluids. “While many lubricant producers already understand new concepts relating to synthetic esters, most EV OEMs are skeptical about adopting these new technologies,” he says. “Until OEMs start to develop new machinery in conjunction with a fluid, we will not be able to see the full potential of these new fluids using synthetic base oils,” he says.
He adds, “Current e-axle units have already been optimized to use ‘old’ automatic transmission fluids (ATF) technologies. For instance, current units use pumps that have been designed for maximum operation based on higher viscosity. Thus, lower viscosity oils will not show their full potential in these systems. In order to get the better efficiency, which these new fluids can provide, the equipment needs to be optimized for it. If we are to achieve higher efficiency and cooling performance, then OEMs need to work along with lubricant producers to get there.”
Nelson summarizes, “Esters present an exciting opportunity for lubricants to address the high performance needs of EV fluid applications, without compromising on sustainability (long-term performance, cost-performance rating) and environment (renewable, biobased feedstocks, non-toxic) goals. Through greater understanding of the features which drive a physical performance characteristic, we can engineer the right components for finished fluids, which bring better solutions to today’s and tomorrow’s problems.”
REFERENCES
1.
Newton’s law of cooling is roughly the following: The rate of heat loss of an object is directly proportional to the difference in the temperatures of the object and its environment.
2.
Permittivity, loss of power factor and resistivity all can be measured by an oil tan delta and resistivity tester.