Tribology leads innovation for efficient machines
By Dr. Hong Liang, STLE President | TLT President's Report December 2023
STLE members lead the way for machinery research and development efforts.
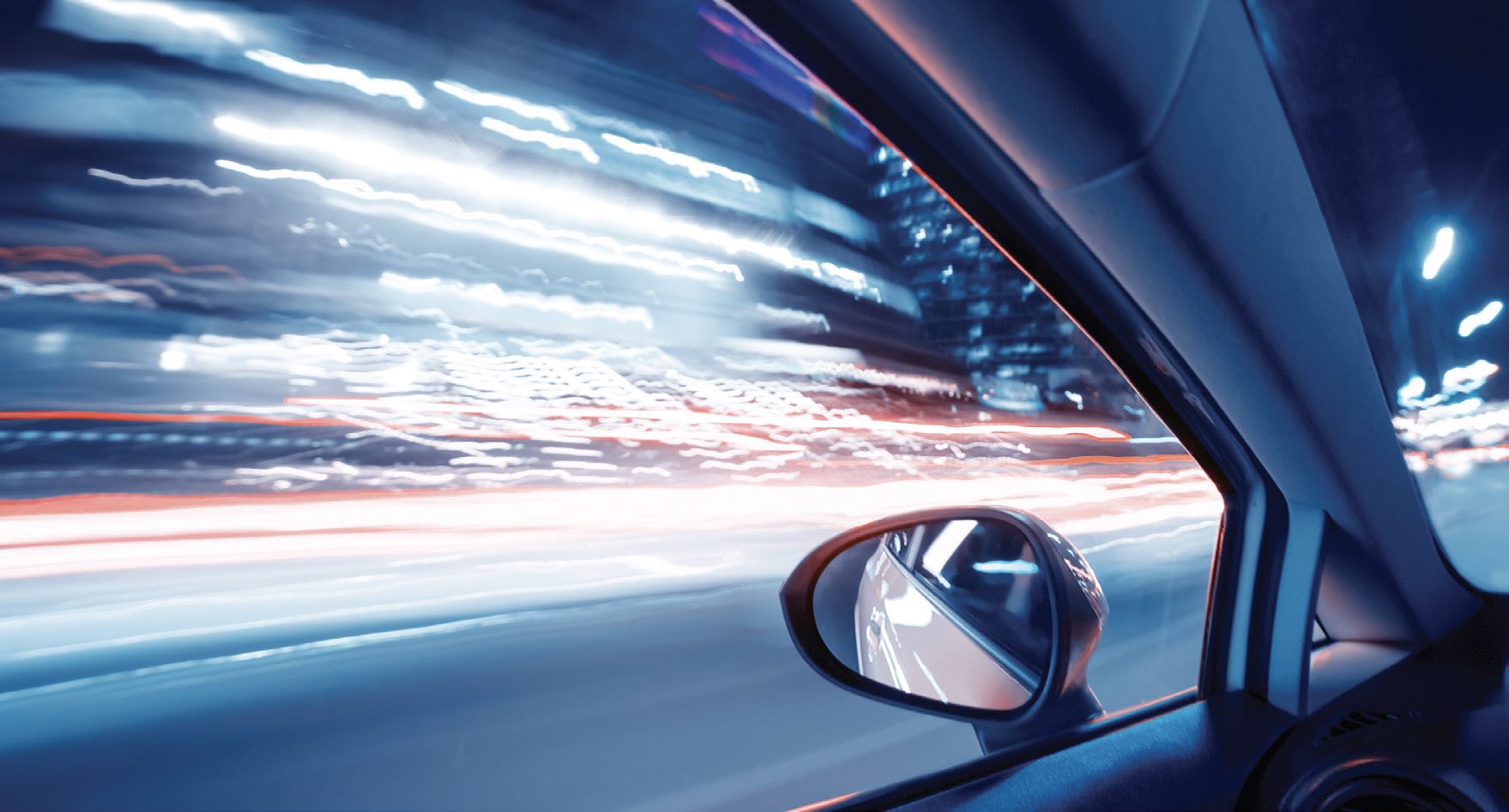
Before the new year arrives, let’s take a look at our leading field of tribology in OEMs. We all know that the establishment of our society was driven by the innovation in transportation, automobiles and aircrafts. The development of manufacturing and equipment promoted the growth of our technical fields. Eighty years later, lubricants, metalworking fluids, materials and coatings have all become marvels for mechanical systems and components to run efficiently with reduced impacts on environments and health. All these are possible because of better understanding in friction, wear and lubrication, such that we are able to better control and perfect motion, minimize toxic emission and improve the performance and lifespan of manufacturing processes, equipment and devices. Now we ask, how does our field lead innovations in OEMs?
To put things in numbers, in January and February of this year, the total patents filed in this two-month period on automobiles was 94,050 worldwide. Those related to tribology were 18,756, making up about 20% of new patents. For electric vehicles (EVs), there were 35,508 patents filed in two months, with 6,623 in tribology, making up 19%. Among all automobile patents filled, 38% are about electric vehicles. These numbers tell us that tribology plays an important role in innovation for automobiles and electric vehicles. Without tribology, without controllable motion nor durable components, we would be living in dangerous conditions and hazard- ous environments.
Tribology plays a crucial role in the design of equipment, mechanical systems and components as well as their manufacturing, materials selection, lubrication systems, tribotesting and validation, performance, maintenance, environment and health and innovation and optimization. Understanding and applying tribological principles can lead to more efficient and durable equipment with a sustainable future, ultimately benefiting both equipment manufacturers and their customers.
Within STLE, we have many members who are leading research and development efforts benefiting OEMs. My colleagues STLE members Dr. Luis San Andres, Dr. Adolfo Delgado and Dr. Alan Palazzolo have been conducting research on experimentally verified computational film flow models for the prediction of the static and dynamic force response of various thin film bearings, energy dissipation and dynamics. Their understanding in thin-film lubrication guides the design, modeling and improvement of rotating machinery systems and components. One application example involves our members from Tesla. STLE member Dr. Wenyang Zhang and his Tesla team drive the development of fluids and lubricants for current and future electric vehicles. Zhang said that the current push for lower fluid viscosity with cost-effective raw materials to achieve cooling and energy efficiency is not necessarily the best approach as desired. What they have been doing is using a system design approach to solve the complexity of EVs and lubrication systems. They focus on fluid design including formulation, viscosity turning, durability, lifetime performance, maintenance, overall energy consumption and vehicle scale cost reduction. What should a tribologist do for EVs? Zhang suggested the following: understanding the interfacial wear mechanisms of the bearing creep through bearing and fluid design, modeling of electrically induced-bear damage and developing next generation grease suitable for EVs.
We are at an exciting time to discover and innovate for a sustainable future. Efficient and safely running machines need our solutions to ensure no waste.
Dr. Hong Liang is Oscar S. Wyatt Jr. Professor of the J. Mike Walker ’66 Department of Mechanical Engineering at Texas A&M University in College Station, Texas. You can reach her at hliang@tamu.edu.