Gear lubricants
By Dan Holdmeyer, Contributing Editor | TLT Lubrication Fundamentals December 2023
The type of lubricant to use for gears depends on the configuration inside the gearbox.
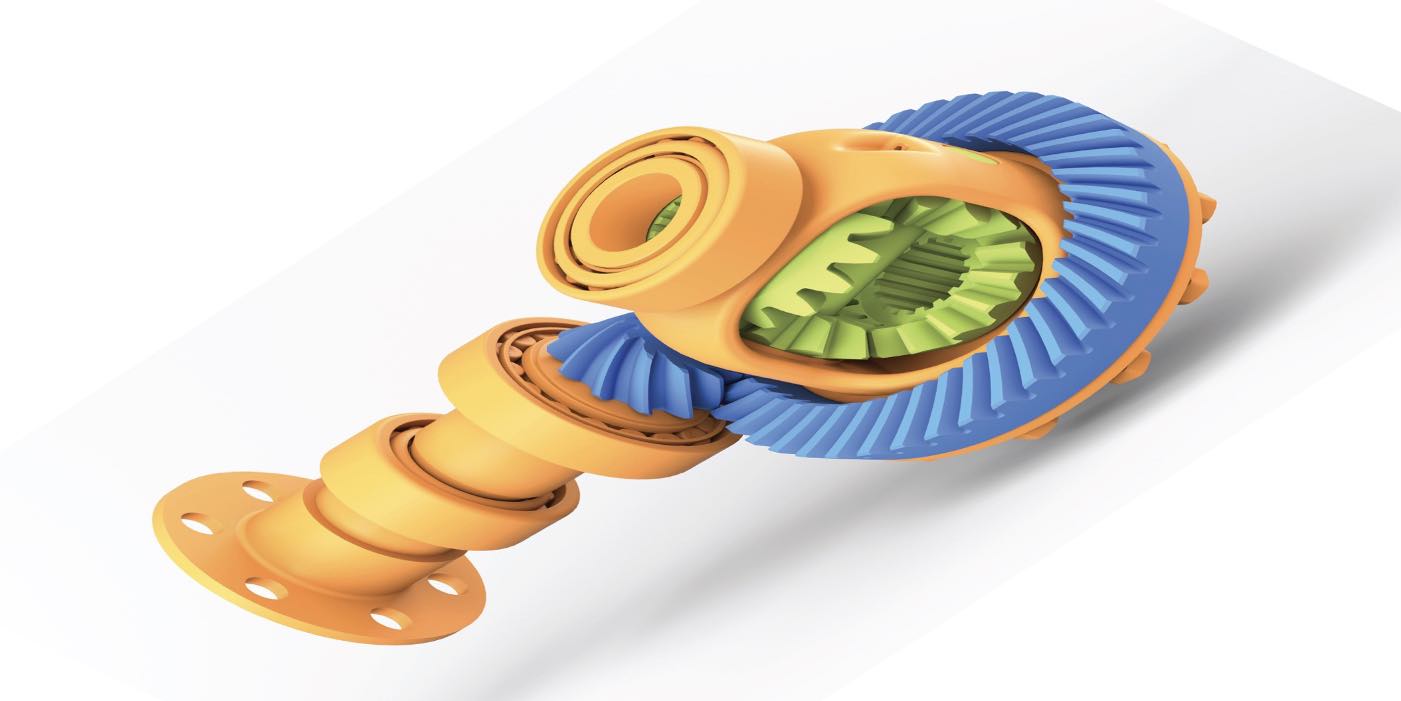
Last month we talked about the various gear configurations to better understand the application we need to lubricate. Knowing the configuration gives clues to what type of lubricant is required. The challenge is to know what configuration is inside the gearbox even though the gears inside cannot be seen from the outside without opening the box.
Figure 1 is of a “parallel shaft” gearbox, as the input shaft is parallel to its output shaft. It also has an intermediary shaft to enable a “double reduction” within the gearbox. The input shaft small gear is engaged with the large gear on the intermediary shaft. The small gear on the intermediary shaft then drives the large gear on the output shaft. Thus, there are two small gears driving two large gears to get two speed reductions through the gearbox, a double reduction gearbox. Further reductions can be achieved by adding more shafts and gears, which require different gear cases to house the additional gears and shafts. Of course, industrial gearboxes are also designed to be speed increasers.
As we discussed in last month’s TLT Lubrication Fundamentals article on gears, a reduction in speed results in an increase in torque. Note that we call the gearbox in Figure 1 a double reduction gearbox in deference to the reduction in speed. We don’t reference the change in torque specification in the nomenclature. Similarly, in a transmission we refer to the first gear as “low gear” referencing the low-speed output versus a fourth gear as a “high gear” because of the higher output speed. The speed reduction and torque increase of the gearbox in Figure 1 is static and cannot be changed by shifting gears as in a transmission.
The gearbox in Figure 1 shows spur gears but also could have helical or double-helical gear teeth. If the input shaft came in from the right side of the gear case in line with, and perpendicular to, the intermediary shaft, a set of bevel or spiral bevel gears is required to transfer the power from the input shaft to the intermediary shaft. The speed reduction ratio of the gearbox could remain the same with properly sized bevel gears, but this configuration allows for the driving motor, or engine, to be oriented differently to accommodate space constraints in the equipment design.
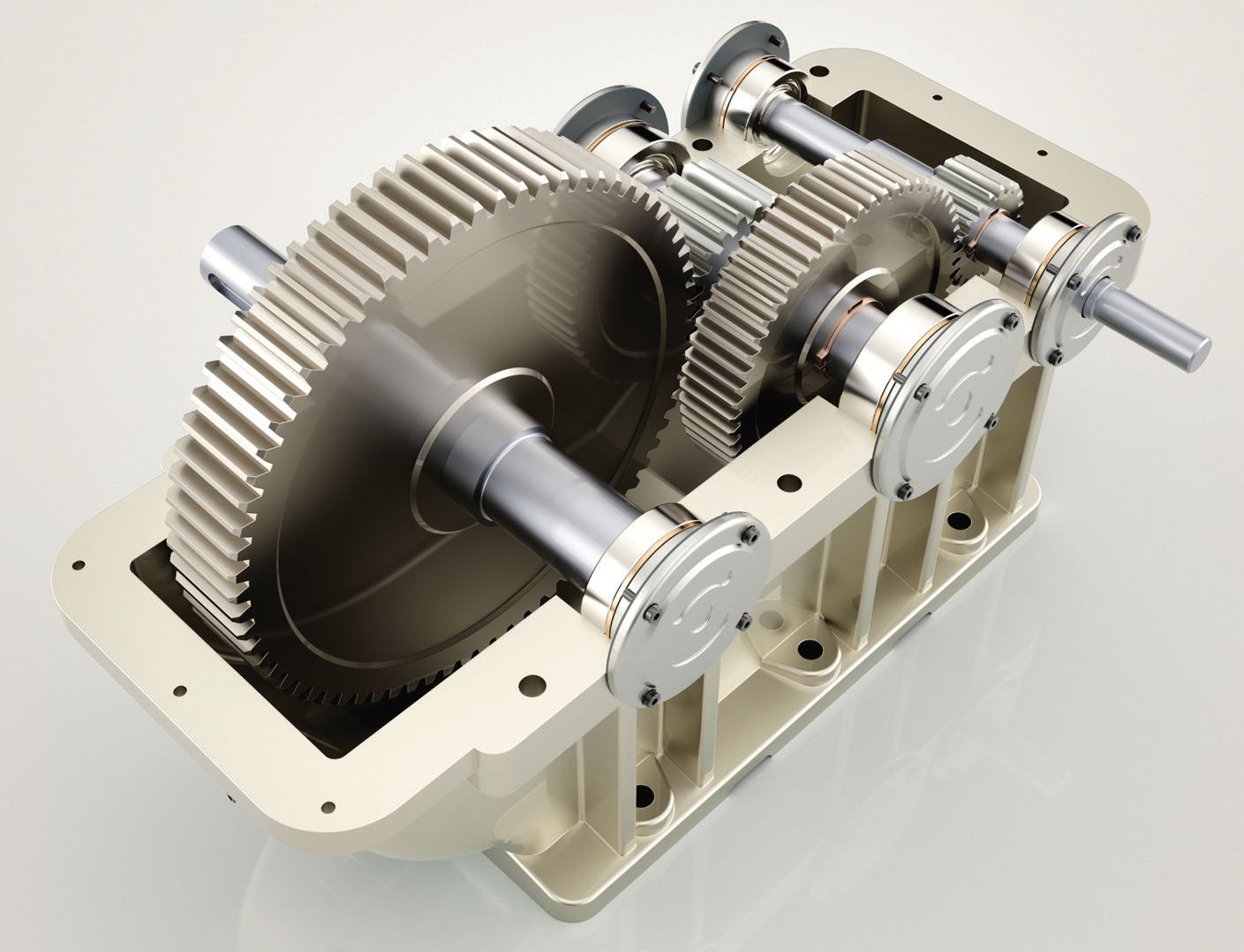
Figure 1. Parallel shaft, double reduction gearbox. Figure courtesy of Craig Paup.
The gearbox in Figure 1 and the variations we mentioned previously, along with the myriad of size variations, are typical of many industrial gearboxes. This leads to a variety of recommended lubricants. However, the list can be broken down into a few categories. Generally, anti-scuff, or commonly known as extreme pressure (EP), gear oils are recommended for most industrial gearboxes. Proof of anti-scuff performance is documented via any combination of tests, such as the Timken OK Load (ASTM D2782), Four-Ball Weld (ASTM D2783) and FZG Scuffing (ASTM D5182). Additional wear, foam and water separation performance specifications as well as oxidation, rust and corrosion protection are common as well. Some lightly loaded gearboxes, without shock loads, may not require anti-scuff oils to protect them from excessive wear. Rust and oxidation (R&O) inhibited oils, maybe with some antiwear (AW) additive, provide enough protection given the right viscosity. (More detailed discussions on R&O, AW and anti-scuff oils can be found in the TLT September 2022 and October 2022 Lubrication Fundamentals articles “How additives finish the lubricant” and “More on how additives finish the lubricant.”)
An additional variation in recommended gear lubricants is synthetic versus mineral base oils. Synthetic-based gear lubricants provide several benefits over mineral oil-based gear lubricants. Synthetics provide a wider operating range due to their inherently higher viscosity index. Viscosity index improvers (VII) can be added to the mineral oils; however, shear stability of the VII is critical in gear applications because gear meshing produces severe shearing, much more than engine applications. Synthetic base oils also help extend the gear lubricant life and improve the gearbox efficiency.
Finally, and most importantly, the oil viscosity needs to be matched to the gear set, operating speed and temperature. Ideally, the machine manual is available, or the name plate is visible, with lubrication requirements. The recommended viscosity grades are commonly assigned to specific operating temperature ranges. Most parallel shaft and bevel industrial gearboxes that I have found use ISO viscosity grades 150, 220 or 320, depending on the speed and temperature. Design engineers look at the slowest speed gear mesh to determine what viscosity grade to recommend for the gearbox since it is the hardest to lubricate due to the slower speed and higher torque.
Figure 2 is of a worm gearbox. The input shaft is in the midline of the electric motor attached to the gearbox and is well above the output. In Figure 2, the output is not a shaft but is a keyed ring where a shaft can be inserted. The output ring gear inside the gearbox meshes with the input shafts worm gear at the top of the gearbox. Friction modifiers, older formulations using fat, are required to reduce wear, due to the excessive sliding action between the worm gear teeth and the ring gear teeth. Sulfur and phosphorous anti-scuffing additives are not recommended in worm gear applications because the ring gear is usually made of a copper alloy. The sulfur additives are prone to chemically attacking copper and copper alloys. The most common lubricant viscosity grades are ISO viscosity grades 460 and 680, with ISO VG 680 used in heavily loaded, large worm gearboxes, especially when the worm and ring gears mesh at the top of the gearbox as opposed to the bottom or side.
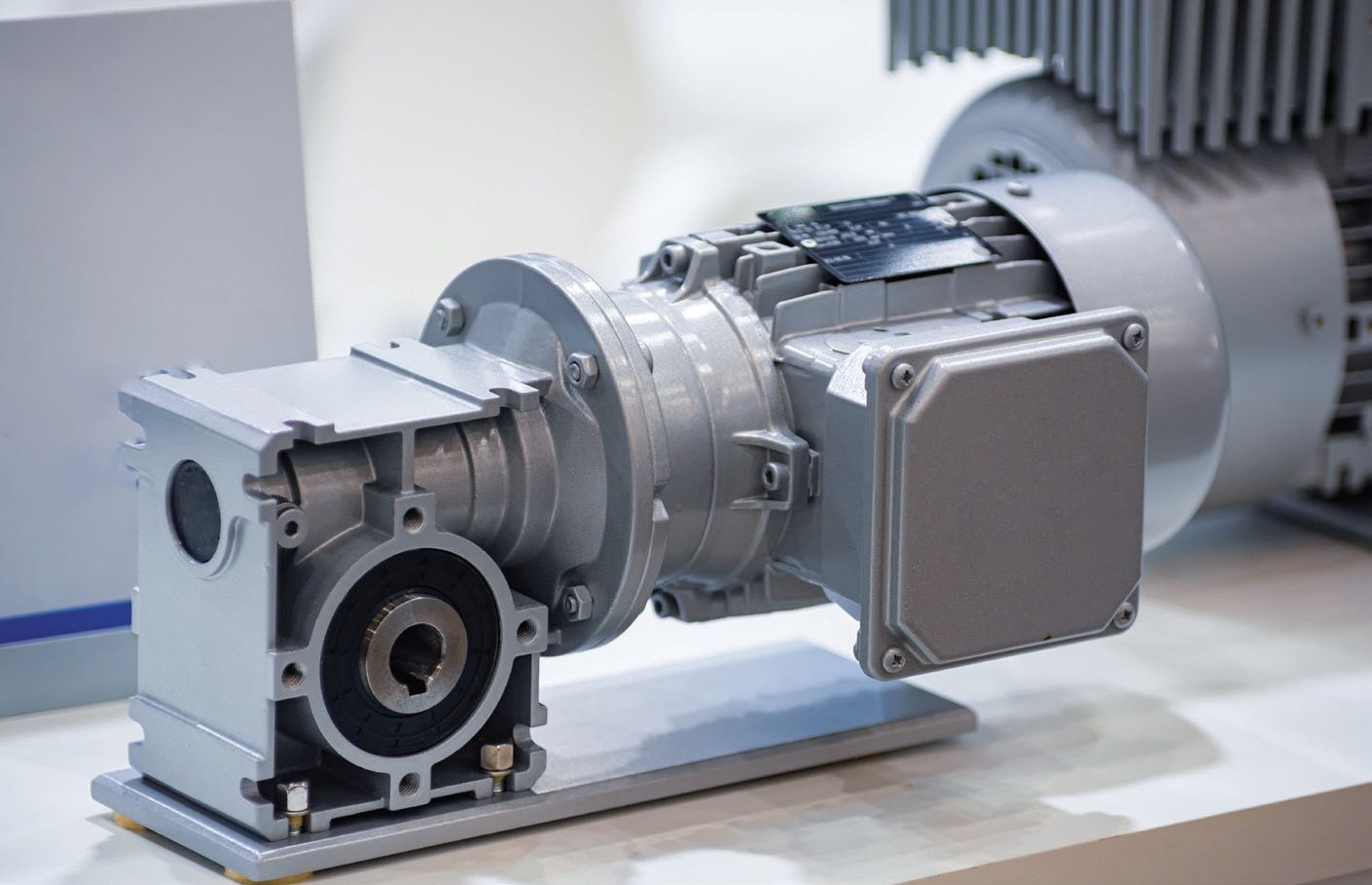
Figure 2. Worm gearbox.
Some gearboxes have circulation systems to help keep the gearbox cool and free of contaminants. The oil pump can be driven by the gearbox or an external mechanical drive source. The oil is pumped to the gearbox bearings and sprayed on the gear teeth as they enter mesh. Typical circulating system maintenance is required to assure proper lubrication, such as changing out filters, maintaining proper oil levels, repairing leaks, removing water if necessary and keeping the system clean.
Other gearboxes rely on splash lubrication of the gears and bearings. The oil level is very critical in these systems. If the oil level is too high, excess air can be driven into the lubricant causing foaming, poor lubricant film formation, poor heat dissipation and possibly oil foam overflow onto the floor creating a fall risk. If the oil level is too low, the oil may not be picked up by the largest gears to “splash” to the rest of the gearbox for lubricating the bearings and the rest of the gears. Oil levels are monitored via dipsticks or sight gauges. Sight gauges are helpful in detecting excess foaming and water contamination. Either way, it is important to know if monitoring is to be done while operating or idle since the direction of gear rotation can either raise or lower the oil level in one side of the gearbox and because oil splashed throughout the gearbox will result in a lower oil level in the bottom of the gearbox.
Gearbox bearings can be open to the inside of the gearbox and lubricated by the lubricant in the gearbox, or they may be external to the gearbox and greased. Gearboxes in extremely dirty environments may have added external shaft seals that require greasing to help keep out contaminants.
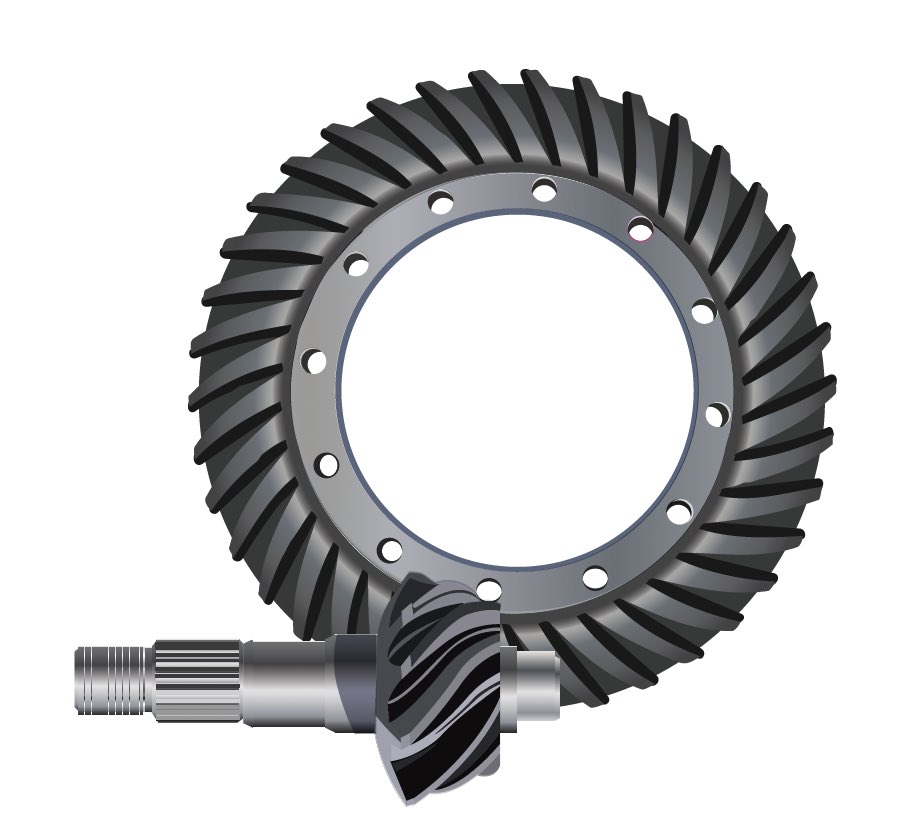
Open gear applications offer opportunities for more lubricant categories. Open gear configurations include parallel shaft and rack and pinion designs. Open gear lubrication is a large topic, but here are some of the common lubricant categories. Semi-fluid tacky grease with solid lubricant additives such as graphite or molybdenum disulfide can be brushed or sprayed on the open gear teeth. Grease offers good protection in applications operated infrequently. High viscosity asphaltic-based oils and high viscosity synthetic-based oils in semi-closed systems where one of the gears picks up the oil from an open pan before meshing with other gears are a couple of other types of open gear lubricant. A unique lubricant category of open gear lubricants is a high viscosity oil with a volatile diluent to enable spraying of the lubricant onto the open gear. The diluent containing lubricant is sprayed on the ring gear of a kiln, or similar equipment, just as the gear comes out of mesh with the driving gear so that the diluent evaporates before going back into mesh and the lubricant is viscous enough to provide wear protection.
Hypoid gears are found in the differentials of rear wheel drive vehicles. They are heavily loaded with a lot of sliding friction between the gear teeth requiring specific lubrication properties. The American Petroleum Institute (API) Category GL-5 was the standard for axle lubricants for years. API GL-5 performance requirements include low-speed high-torque and high-speed shock load tests along with other corrosion, foaming and oxidation tests. The Society of Automotive Engineers (SAE) issued SAE J2360 around 1998, although its origin dates back much further in military history. SAE felt the need for SAE J2360 to provide gears, seals and bearings better protection and improve efficiency. Some of the additional tests required by SAE J2360 are seal compatibility, oxidation/deposit control and storage stability. Furthermore, light- and heavy-duty equipment field trials are required, and the results reviewed by an independent panel of experts. If approved, then the lubricant can be listed on the Qualified Products List (QPL) for SAE J2360 for automotive differential applications.
Those are some of the fundamentals of gear lubrication.
Dan Holdmeyer is retired from Chevron Lubricants and is based in Washington, Mo. You can reach him at dan.holdmeyer@gmail.com.