KEY CONCEPTS
•
Gears are superior to alternatives, such as chains and belts, for drive and torque transmission. Reasons include nearly unlimited torque, being able to transmit drive or power in a limited space, ability to change rotation direction, etc.
•
Factors that can affect gear lubrication include operating temperature and humidity of the gear drive assembly, transmitted load and power, operating pressure in the lubrication system and operating decibels of the gear drives.
•
Because equipment is getting increasingly compact, efficient gear design and performance is more crucial than ever. In this high-demand, compact environment, gear lubricants must deliver relatively more boundary protection between interlocking cogs.
Since the first known existence of gears in the 27th Century B.C., various designs have emerged to accommodate the required speed, load and stress tolerance. Consequently, the antifriction materials required for proper operation have emerged and evolved as well
(see Early Gear Applications).
Early gear applications1
Early gear applications include the following.
• In the 2nd Century B.C., the Antikythera machine, the world’s first analog computer, was constructed. It could resolve various astronomical issues and make long-term predictions about the motion and positions of the sun, moon and planets.
• Between 200 and 265 A.D., Ma Jun employed gears as a component of a south-pointing chariot.
• About the 6th Century A.D., a geared calendrical instrument displaying the Moon’s phase, the day of the month and the Zodiac was created in the Byzantine empire.
• About the year 725 A.D. the first geared mechanical clocks were created in China.
• About the year 1221 A.D., in Isfahan, which is now Iran, a geared astrolabe was developed that displays the moon’s position in the zodiac, its phase and the number of days since the new moon.
• Between 1348 and 1364, Giovanni Dondi dell’Orologio created a sophisticated as¬tronomical clock known as the Astrarium. The Astrarium, which had seven faces and 107 movable components, displayed the positions of the sun, moon and five then-known planets as well as holy days at the time.
• In 1386 A.D., the oldest still-running geared mechanical clock in the world was created. It is located at Salisbury Cathedral in Salisbury, England.
• Around the 13th or 14th Century, in the Indian subcontinent, the worm gear was first created for a roller cotton gin.
1. From Gear/History Wikipedia. Available at https://en.wikipedia.org/wiki/Gear.
To enhance the near perfect rotation of the gears and to reduce sliding friction, proper alignment of the shafts is critical. Also, the right type of gear oil (fully synthetic, semisynthetic or mineral-based) along with the grade needs to be selected so that it aligns with the application.
As plants and machineries have become more compact, designs and functionalities also have become more central to expected outputs and gear performance. This means gear lubricants must deliver relatively more boundary protection between interlocking cogs.
Ultimately, the goal is to develop gears that adequately enable and accommodate the evolution and design of machinery, along with compatible high-performing, cost-effective lubricant.
A final consideration is how to decommission gear-integrated machinery and associated fluids at the end of their lifecycle in an environmentally responsible way.
The impact of gear design on mechanical engineering
In one sense, gears are basic—causing motion by means of interlocked teeth that create a specific rotational speed and initiate a chain of mechanical movements. In a much broader sense, they are highly complex, having evolved over the centuries into precision components that are the lifeblood of most machinery.
Maxwell Doe Kofi Sappor, mechanical engineer, Cocoa Processing Co. PLC, Tema, Ghana, explains, “Gear design has had a significant impact on the mechanical industrial sector by revolutionizing machinery, improving efficiency, enabling new technologies and enhancing various applications. The development of new gear design techniques has led to a wide range of new and improved applications for gears.”
He cites the development of high-efficiency gears that has made it possible to design more fuel-efficient vehicles and the development of lightweight gears that has made it possible to design aircraft and spacecraft that are more fuel-efficient and easier to maneuver.
Harry A. Sackey Jr., technical sales director, Dates Limited, Accra, Ghana, points out that improvements in gear design have made mechanical engineering ubiquitous in virtually all fields of engineering where power transmission, change of motion direction, timing, oscillation of moving parts, etc., is required in equipment design and function. “It is therefore hard to imagine how mechanical engineering could have advanced beyond primitive early machines without the invention of gears,” he says.
Theophilus Ayertei, technical instructor (automobile), Accra Technical Training Centre, Accra, Ghana, says that although there are other means of drive and torque transmission, such as belts and chains, gear drives have proven superior for the following reasons:
1.
Provide positive transmission of motion or power—no slippage.
2.
Can transmit drive or power in limited space.
3.
Are very compact and strong when compared to belt and chain drives.
4.
Can increase the torque being transmitted.
5.
Can change the direction of rotation (clockwise to counterclockwise).
6.
Split the drive being transmitted at 90 degrees (for example, back axles of vehicles).
7.
Can be used to change direction of motion (as in moving vehicles changing to reverse).
8.
Can be used as pumps (as in engine oil pumps) in hydraulics and other sectors.
9.
Can transmit unlimited torque providing the structural supports can withstand the load being transmitted.
“Gears are therefore indispensable within mechanical engineering, assuming there is precise engineering as well as good alignment and professional maintenance,” Ayertei adds. “All of this leads to efficient operation and long service life.”
Sliding friction and improvements in gear design
Sliding (kinetic) friction has driven significant improvements in gear design by influencing the way gears interact, transmit power and function within various mechanical systems. “These improvements have led to enhanced efficiency, durability and overall performance of gears in a wide range of applications,” Sappor observes. “They also have helped in the development of new materials that have lower coefficients of friction. This means that they generate less friction when they are in contact with other surfaces, which can lead to longer gear life.”
Sliding friction involves resistance, which results in heating of the sliding surfaces. This may eventually lead to galling and seizure between the surfaces. “If this should happen in a machine, power transmission will fail with catastrophic consequences,” Sackey says. “In order to avoid the consequences of sliding friction, gear design profiles have been significantly improved to convert sliding friction to tangential contact rolling friction, thereby greatly reducing power loses in transmission.”
Friction is essential for nearly all machines to work efficiently as they were intended. “In fact, there would be no lathes or milling machines to manufacture these gears if friction did not exist,” Ayertei says. However, friction has to be reduced to the bare minimum to achieve good mechanical efficiency from mechanical components that are rotating, sliding or reciprocating. To reduce sliding friction, in order to reduce or prevent gear tooth damage, excessive wear, excessive heat generation or any other operational defects, the following are some important considerations
(see Major Gear Teeth Wear and Failures Modes):
•
Gear materials that are fit-for-purpose
•
Precisely engineered gear teeth (tooth design and configuration)
•
Gear alignment
•
Type of lubrication system used (film, injection, full flow, etc.)
•
Type of lubricants used (grease or gear oil)
•
The gear shaft support mountings (bearings and rubber supports)
•
Rolling resistance between the mating gears.
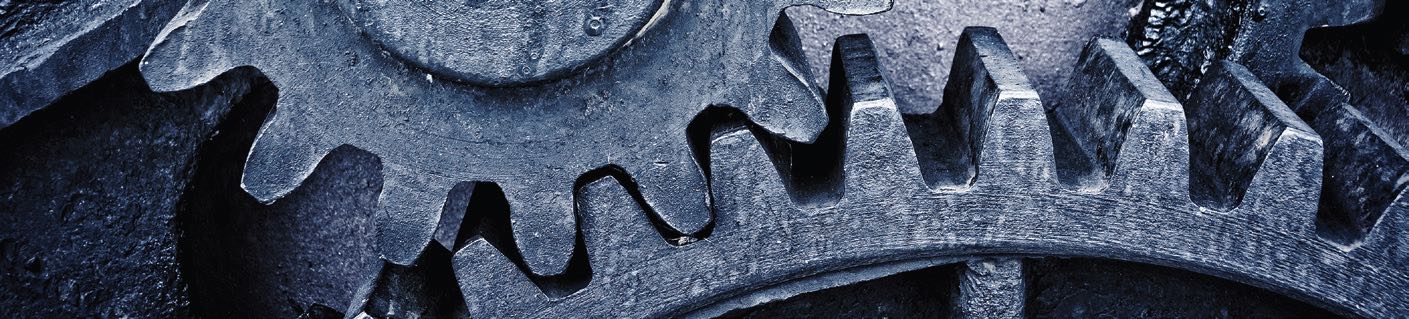
Major gear teeth wear and failures modes
Theophilus Ayertei, technical instructor (automobile), Accra Technical Training Cen¬tre, Accra, Ghana, explains, “Lack of lubrication and other factors increase gear wear and failure. The cause can always be found by examining the damaged parts.” Some major gear teeth wear and failure modes he cites are:
•
Normal wear appears as a polished surface, which should extend the full length of the tooth from near the root (bottom) to the tip of the tooth. Gears properly manu¬factured and installed, well lubricated and not overloaded will exhibit this condition after long use.
•
Abrasive wear appears as surface injury from line abrasive particles carried in the lubricant or imbedded in tooth surfaces. Common causes are metal particles from worn gears and abrasive materials.
•
Scratching is often found on heavily loaded gears operated at slow speeds. It is caused by metal particles (larger than abrasive particles) that flake off gears. It generally indicates a wrong gear design for the load.
•
Overload wear is a depression along the length of the teeth caused when metal is removed by sliding pressure. Teeth are worn but smooth. Continued wear results in excessive backlash.
•
Rolling leaves a burr on the tooth edge caused by overloading and sliding of the teeth.
•
Peening results from excessive backlash and hammering of one tooth against another with tremendous impact.
•
Rippling leaves a wavy surface or fish scales on the teeth at right angles to the direc¬tion of slide. It may be caused by the surface yielding due to heavy loads, vibration or friction from lack of lubrication.
• Scoring is caused by temperature rise and thinning or rupture of the lubricant from overloading. Pressure and sliding action heat the gear and permit metal transfer from one tooth to the face of another.
• Pitting is sometimes associated with thin oil film, possibly due to high oil temperatures.
• Spalling starts with surface cracks and eventually results in larger flakes or chips leaving the tooth surface. Improperly hardened teeth are most subject to spalling.
• Corrosion is when the gear tooth deteriorates as a result of chemical or electro¬chemical interactions. The tooth appears stained or rusty. The presence of moisture or foreign elements in the lubricant, the presence of active substances in the lubri¬cant like sulfur and extreme-pressure additives added to the lubricant that react with the gear teeth are all common causes of corrosive wear.
• Burning is usually caused by complete lubricant failure or lack of lubrication. Burned teeth are quite brittle and easily broken.
• Interference wear can be caused by misaligned gears, which place heavy contact on small areas. It also can be caused by mating gears with different tooth designs. Different wear patterns may appear at the root and tip of the gear teeth.
• Ridging causes scratches near one end of a tooth, especially on a hypoid pinion gear. This can be caused by overloading, lack of lubricant or improper heat treatment.
• Breakage is caused by high impact forces or defective manufacture. Fresh metal around the break indicates damage caused by impact overload.
• Cracking is normally caused by improper machining and faulty heat treatment during manufacture. Most heat treat cracks are extremely fine and do not show up until the gear has been used for some time.
Ayertei advises that new gear teeth usually have slight imperfections, but they normally disappear during break-in as the teeth are oiled and polished. After that, with proper lubrication, operation and adjustment, the teeth or gear assembly should have a long service life.
The effect of shaft alignment on gears and rotation
Sackey explains that shaft alignment is factored into the design of the gear tooth profile and is a field for engineering specialists. If shaft alignments are not achieved within the design specifications, one or more of the following failures could occur:
•
Gear failures
•
Shaft failures
•
Shortened service life of seals and bearings
•
Overheating of lubricating oil
•
Fouling of lubricants resulting from chaffing and pitting of gear teeth surfaces
•
Crack failures in the gear housing
•
Rotation of gears that results in excessive noise due to rough meshing
•
Shaft misalignment that inherently imposes imbalance thrust forces on components of the assembly.
Sappor adds, “Shaft alignment plays a critical role in the proper operation and longevity of gears and rotational machinery. The alignment of shafts directly affects the meshing of gears, transmission efficiency, vibration levels and overall performance. A misaligned shaft can affect the gear in that it can increase friction between the gears, increase vibration and noise, lead to premature wear and tear on the gears, lead to bearing damage and, in some cases, even lead to catastrophic gear failure. Ensuring that the shafts are properly aligned helps extend the life of the gears and prevent costly repairs.”
Key gear lubrication issues
Sackey says there are a number of factors that affect gear lubrication and that would effectively influence their efficiency and reliability as well as their overall service life. Some of these factors include:
•
Operating temperature and humidity of the gear drive assembly
•
Transmitted load and power
•
Oil viscosity and lubricity
•
Gear types and operating speed
•
Material compatibility
•
Corrosion and oxidation inhibition
•
Operating pressure in the lubrication system
•
Oil properties like exfoliation and adhesion to surfaces
•
Operating decibels of the gear drives.
Sappor points to several key issues that can arise in gear lubrication, impacting gear performance, durability and overall system efficiency.
•
Lubricant starvation. In some operating conditions, such as high-speed or intermittent operation, gears may experience lubricant starvation. This can result in insufficient lubrication between gear teeth, leading to wear and potential failure.
•
Improper lubricant application. Incorrect lubricant application methods, such as uneven distribution or improper lubricant type, can lead to uneven lubrication and subsequent gear tooth wear.
•
Temperature extremes. Operating outside the recommended temperature range of the lubricant can affect its viscosity and lubricating properties. Extreme temperatures can lead to poor lubrication and accelerated gear wear.
•
Insufficient lubrication. Inadequate lubrication can lead to increased friction and wear between gear teeth. This results in accelerated gear tooth wear, increased heat generation and potential catastrophic failure.
•
Over lubrication. Excessive lubrication can lead to churning losses and overheating due to the increased internal resistance caused by excessive oil volume.
Decommissioning gears and gear lubricants
After successfully lubricating the gear assembly, eventually when the lubricant becomes dirty and loses its properties, it will need to be changed. If the gear assembly will exhaust its lifespan and malfunction, both the gear assembly and lubricant need to be disposed of and replaced in an ecofriendly way.
Ayertei notes that gear assemblies can be repurposed or smelted, and used lubricants can be responsibly handled by collecting them into drums and either rerefining them or using them as is for niche industries such as vulcanizers that employ used lubricants to provide airtight sealing between tire beads and tire rims.
When decommissioning gears and gear lubricants, the lubrication system should be flushed and the equipment subsequently run to its normal operation temperature. This will suspend all grime and sediment. Sackey says, “After this procedure, the gear oil should be completely drained. Used lubricant samples can be sent for oil analysis, and the remaining lubricant can be repurposed or recycled. The gears, bearings and shafts should be effectively degreased, washed and sent to foundries.”
Sappor also recommends recycling gear assemblies and reusing or recycling lubricants.
Conclusions
Ayertei points out that gearing has given birth to splines, sprockets and toothed wheels, which are essential in almost all engineering-related sectors. Although there are other methods by which drive can be transmitted, that of gear systems is superior, since they exhibit positive drive engagement, less transmission loss, less noise in operation (provided the correct lubricant is applied) and longer service life than the alternatives.