Super-slippery cellulose surfaces
By Drs. Wilfred T. Tysoe & Nicholas D. Spencer, Contributing Editors | TLT Cutting Edge December 2023
Cellulose nanofibers are normally thought of as reinforcements, but molded into solid pieces and in the right lubricant they show great promise as bearing materials.
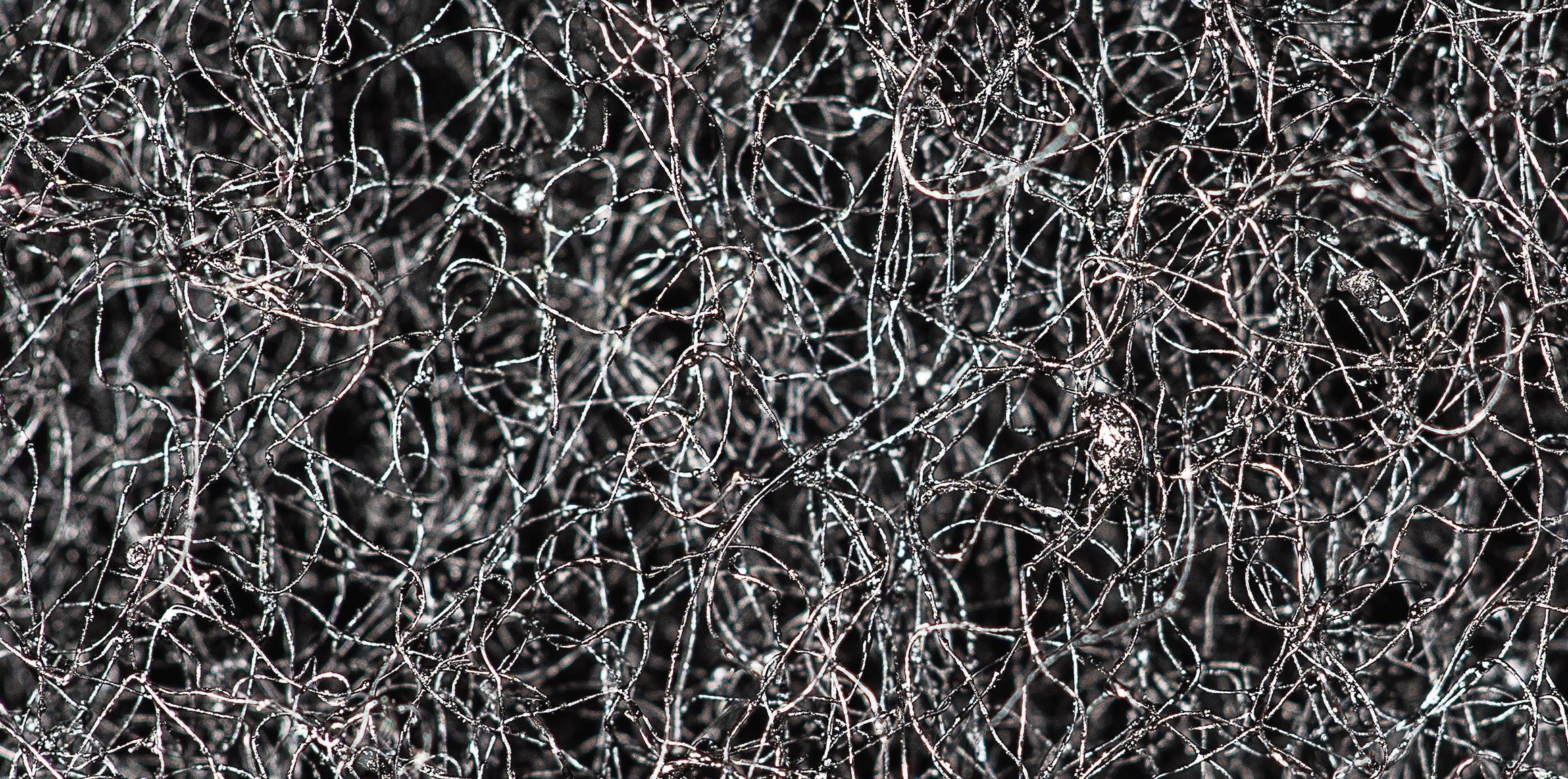
Energy savings and lower carbon footprint in transportation systems are key goals in this era of rapid global warming. Reducing the weight of vehicles is certainly a valid approach to achieving these goals, although increased use of lightweight engineering plastics comes with its own environmental challenges. A radical alternative is to use cellulose nanofibers (CNF), which are very attractive for their mechanical properties (5x the strength of steel), their biological origin, their low coefficient of thermal expansion and their low density (5x less than steel). Moreover, their surface chemistry, which features high concentrations of hydroxyl groups, lends itself to functionalization.
Until now, CNFs have been largely used as reinforcements for engineering plastics, and therefore their environmental advantages have not been fully realized. Thanks to developments in compression-molding technology, CNFs can now be formed into solid pieces, with a density only about 40% greater than water, and an indentation hardness in the hundreds of GPa range. These materials can therefore be considered for applications as machine elements. Super-slippery cellulose surfaces Cellulose nanofibers are normally thought of as reinforcements, but molded into solid pieces and in the right lubricant they show great promise as bearing materials.
Tribological applications also require low friction, and a recent article
1 by Hikaru Okubo and Ken Nakano of Yokohama National University, Hiromi Hashiba and Toru Inamochi of Chuetsu Pulp and Paper Co., Kaisei Sato and Shinya Sasaki from Tokyo University of Science and Kazushi Yamada of Kyoto Institute of Technology, demonstrates that great strides have been made in imparting low friction to CNF moldings in an oil environment.
Key to this development is the use of glycerol monololeate (GMO) as a lubricant additive to the base oil—in this case a poly(alphaolefin) (PAO). In pin-on-disk tests, comparisons were made between CNF-steel (AISI52100) and steel-steel pairings, lubricated by PAO alone or PAO + 1 wt% GMO. The results
(see Figure 1) show that while GMO already reduces friction between steel partners (as is well known), it reduces friction between CNF and steel by an additional order of magnitude—under conditions corresponding to boundary or mixed lubrication.
Figure 1. Frictional behavior (10 N load, 50 C, 10 mm/s sliding speed) of CNF/steel and steel/steel tribopairs lubricated with PAO or PAO+GMO. Figure from Ref. 1 with kind permission.
Furthermore, while the CNF molding surface showed a brown discoloration after lubrication by only PAO against steel (presumably from iron oxide formation), the presence of GMO seemed to eliminate this effect, suggesting that the CNF surface had been chemically modified. The steel-steel pair showed no difference in the wear scars upon GMO addition to the PAO.
In an effort to understand these results, the researchers performed a battery of tests to analyze the CNF before and after tribological testing. Raman spectroscopy was used to measure the cellulose crystallinity, and showed that while CNF lubricated with PAO alone had some loss of crystallinity due to sliding (presumably due to thermal and friction-induced effects), the addition of GMO to the lubricant appeared to lead to a greater crystallinity loss in the CNF, despite its lower friction—again suggesting that the effect had a chemical origin. Attenuated total reflectance infrared spectroscopy was used to understand the chemical effects; only after sliding in PAO-GMO did the CNF-molding surface show a greatly increased carbonyl signal, presumably due to binding of the GMO to the OH-rich cellulose surface. This might explain why the brown stains on iron were eliminated, since the aggressive OH groups were now prevented from reacting with the steel countersurface by the GMO.
A key piece of information was gained by high-resolution, frequency-modulation atomic force microscopy (HR-FM-AFM), which provided a z-x (depth-dependent) molecular-density visualization analysis of the tribologically tested CNF surfaces while still submerged in lubricant
(see Figure 2a). HR-FM-AFM shows clear differences between CNF moldings that had been lubricated with and without GMO, suggesting that the outer surface of the nanocellulose molding had become expanded by GMO over a depth of some 50 nm. A forcedistance curve
(see Figure 2b) showed a greatly reduced modulus (0.01-1.0 kPa) in the outer 10 nm.
Figure 2. a) High-resolution, frequency-modulation atomic force microscopy (HR-FM-AFM) Z-X frequency-shift mapping images of the solid-liquid interface of the CNF moldings following sliding against steel under PAO and PAO+GMO, b) HR-FM-AFM force-displacement curve on the CNF molding surface for PAO+GMO. Figure from Ref. 1 with kind permission.
Putting all of this together, it appears that GMO acts to swell the outer surface of CNF moldings to produce a soft, highly lubricious layer, tens of nm in thickness. This explains the loss in cellulose crystallinity and is consistent with the significant increase in infrared carbonyl signal from the CNF molding following tribological testing in PAO+GMO. Such a structure is reminiscent of the “brushy” structures at the outer edge of cartilage
(see Figure 3), although the precise nature and mechanism of the chemical functionalization of the cellulose by GMO has yet to be determined. Nevertheless, it is clear that this strong, biological material has shown impressive tribological behavior in an oil environment under conditions that are relevant to transportation systems.
Figure 3. Superlow-frictional model for a combined system of CNF molding and a GMO-containing oil. Figure from Ref. 1 with kind permission.
REFERENCE
1.
Okubo, H., Hashiba, H., Inamochi, T., Sato, K., Sasaki, S., Yamada, K. and Nakano, K. (2023), “Novel environmentally superior tribomaterial with superlow friction: 100% cellulose nanofiber molding,”
Tribology Letters, 71 (83).
Eddy Tysoe is a distinguished professor of physical chemistry at the University of Wisconsin-Milwaukee. You can reach him at wtt@uwm.edu.
Nic Spencer is emeritus professor of surface science and technology at the ETH Zurich, Switzerland, and editor-in-chief of the STLE-affiliated Tribology Letters journal. You can reach him at nspencer@ethz.ch.