Meet the Presenter
This article is based on a webinar presented by STLE Education on Feb. 16, 2022. Test Methods for Evaluation of Electric Vehicles is available at www.stle.org: $39 to STLE members, $59 for all others. This article contains information that has been updated from the webinar to reflect changes in this rapidly evolving field.
STLE member Rebecca Warden is a senior research engineer at Chevron Oronite, functioning as a test engineer and OEM liaison for driveline and hydraulics, with a focus on lubricant additive development for next-generation electric vehicles. Prior to joining Chevron Oronite, Warden was the manager of advanced drivetrain lubricants at Southwest Research Institute (SwRI), focusing on lubricant evaluations for electrified vehicles, automatic transmissions, axles, tractor hydraulic systems and gear/hydraulic systems in industrial applications. Warden has been active for nearly 14 years in the lubricants industry with over a decade of experience in driveline testing.
You can reach her at Rebecca.Warden@chevron.com.
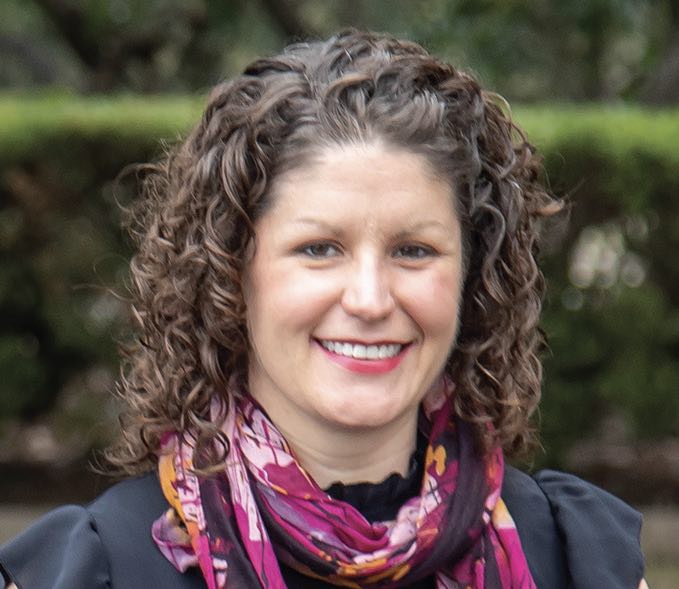
Rebecca Warden
KEY CONCEPTS
•
Electric vehicle drive units run under different conditions than their internal combustion counterparts, and tests must be created and adapted accordingly.
•
Electric vehicle fluid formulations are as varied as vehicle designs, and both are evolving rapidly.
•
As electric vehicles continue to mature, the industry needs repeatable test methods that can differentiate lubricants while maintaining strong ties to field performance to ensure that those methods are relevant to the application.
Today’s electric vehicles (EVs) encompass a wide variety of architectures and designs. Discussions of lubricants for EVs can include fully electric vehicles, as well as conventional hybrids, plug-in hybrids and fuel cell vehicles. Each design places unique demands on its lubricants. For the near future, at least, there is no one-sizefits- all lubricant solution. Often, a change to improve performance in one area can reduce performance in another area, so a delicate balance is required for the lubricant to meet a specific application. Even though EV lubricants are highly customized, producing useful and meaningful test results requires repeatable test methods for comparing formulations and evaluating their performance.
This article is based on an STLE webinar titled Test Methods for Evaluation of Electric Vehicles, presented by STLE member Rebecca Warden, senior research engineer for Chevron Oronite. See Meet the Presenter for more information.
Lubricant formulation for conventional applications is a relatively mature field. A variety of standardized tests and established acceptable ranges for test results help yield good field performance. In contrast, there are few standardized tests specific for EV fluids. Some tests developed for conventional vehicle applications or for other mechanical systems may be tangentially applicable, but there is little consensus about how relevant those tests are to EV applications and how they correlate to long-term field performance. What EV drivetrain fluid properties require testing, and what is the current state of the art?
Electrical properties
A lubricant’s base oil and additive package determine its electrical properties and how it interacts with an electric field, which, in turn, can affect the fluid’s performance. These interactions change as the fluid shears, oxidizes or is contaminated with wear particles or water. Testing a fluid’s electrical properties in a way that is relevant to the end application requires considering operational conditions like voltage level and frequency, test temperature and levels of contamination.
Electrical conductivity is a key property of EV fluids. An EV fluid with conductivity that is too high can transmit stray currents, which in extreme cases can pose a safety hazard. On the other hand, if the fluid’s conductivity is too low, static charges may build up and then discharge suddenly, damaging bearings and other components. The optimal range between “too high” and “too low” has yet to be established.
Several methods exist for testing the electrical conductivity (or its inverse, resistivity) of transformer oils, which also are insulating fluids. For this reason, ASTM D1169 is a good place to start when evaluating EV fluid conductivity
(see Electrical Properties). In this test, the lubricant sample provides the only interface between two concentric electrodes, one grounded and another with an applied voltage. The amount of induced current traveling between electrodes indicates the fluid’s conductivity
(see Figure 1). This method is applicable to DC currents (it does not address AC frequency), and it covers a limited range of temperatures. A new method in development, DIN 51 111, will evaluate a fluid for conductivity, relative permittivity and dissipation factor with an AC current. Benefits of this new method over ASTM D1169 are the low fluid volume required for testing, the expanded temperature evaluation range and the use of AC instead of DC voltage.
Electrical properties
ASTM D1169 Standard Test Method for Specific Resistance (Resistivity) of Electrical Insulating Liquids (
www.astm.org/d1169-11.html)
DIN 51 111 (draft status) Electrical properties of fresh and used oils from electric drives in vehicles (
www.din.de/en/getting-involved/standards-committees/nmp/drafts/wdc-beuth:din21:364582829)
ASTM D1816 Standard Test Method for Dielectric Breakdown Voltage of Insulating Liquids Using VDE Electrodes (
www.astm.org/d1816-12r19.html)
ASTM D924 Standard Test Method for Dissipation Factor (or Power Factor) and Relative Permittivity (Dielectric Constant) of Electrical Insulating Liquids (
www.astm.org/d0924-15.html)
Figure 1. Setup for ASTM standard tests D1169 (resistivity) and D924 (dissipation and relative permittivity). Left side of the figure courtesy of ASTM D1169.
Some EV designs place high demands on insulating fluids. For example, it can be important to evaluate a formulation’s ability to resist dielectric breakdown under high voltages. Dielectric breakdown testing evaluates a lubricant’s ability to withstand applied electrical stress by increasing the voltage between two electrodes until an electrical arc passes through the insulating fluid in between. ASTM D1816 uses a button-style electrode
(see Figure 2), while other methods use the same principles with different electrode shapes and styles. Existing tests are limited to AC currents in the 45- to 60-Hertz range and ambient temperature; however, typical EVs operate at much higher switching frequencies and temperatures.
Figure 2. Dielectric breakdown testing apparatus with button electrodes. Figure courtesy of Chevron Oronite.
The power factor, related to the dissipation factor, is an indication of the fluid’s dielectric losses in an AC electric field. This can be correlated to an increase in lubricant temperature due to lost power. The power factor is expressed as the ratio between the true power (the power available to do useful work) and the apparent power (the power that would be available if there were no dielectric losses).
For electrically insulating fluids, including EV fluids, ASTM D924 is the standard test method for dissipation factor (or power factor) and relative permittivity (dielectric constant). This method applies to AC frequencies from 45 to 65 hertz, much lower than a typical EV’s operating range. The test cell design for D924 is the same as for method D1169, with a fixed electrode spacing and a limited temperature range. The temperature limitations of existing standardized tests are especially relevant because some EV fluids serve as coolants as well as lubricants. Power loss often manifests itself in the form of heat generation, and keeping power losses as low as possible is highly desirable.
High-speed EV gears and bearings are prone to wear and unique failure mechanisms. For example, stray electrical currents from the motor can ground through a bearing, which causes a rippling effect called fluting. This decreases the bearing’s life and causes noise and vibration problems. OEMs are working to reduce the chance of fluting by ensuring that electrical grounding paths do not go through bearings. Ceramic bearing components are an effective, but expensive, solution. Grounding rings, another solution, can wear out and become ineffective over time. Each of these mechanical design solutions adds to the cost of designing and manufacturing an EV.
Using more conductive lubricants could be a solution, but EV-relevant lubricant tests need to be developed. A new method, currently under development to evaluate a lubricant’s ability to prevent this type of damage, uses a rotating motor to induce currents that are grounded through a test bearing. This method operates at speeds up to 4,000 rpm, loads as high as 2.4 kN, under peak-to-peak voltages as high as 60 V, while controlling lubricant temperature between 20 C and 100 C.
Heat transfer
Heat transfer is another important property of EV fluids, especially those used for EV motor cooling applications. Thermal conductivity, diffusivity (the rate of heat transfer from a material’s hot end to its cold end) and specific heat capacity (the quantity of heat absorbed per unit mass per unit temperature rise) are all used to define a material’s ability to store and transfer heat. These three properties can be measured using ASTM D7896
(see Heat Transfer and Materials Compatibility). This method, originally developed for engine coolants, uses a thin platinum wire immersed in the sample. A pulse of current passes through the wire, which heats the wire and the fluid sample, and the resistance of the wire is measured as it cools. The profile of fluid temperature versus time is an indicator of the fluid’s thermal properties. The standard method is applicable in the temperature range between -20 C and 100 C.
Heat transfer and materials compatibility
ASTM D7896 Standard Test Method for Thermal Conductivity, Thermal Diffusivity, and Volumetric Heat Capacity of Engine Coolants and Related Fluids by Transient Hot Wire Liquid Thermal Conductivity Method (
www.astm.org/d7896-19.html)
ASTM D130 Standard Test Method for Corrosiveness to Copper from Petroleum Products by Copper Strip Test (
www.astm.org/standards/d130)
ASTM D638 Standard Test Method for Tensile Properties of Plastics (
www.astm.org/d0638-14.html)
Convective heat transfer encompasses all of the lubricant properties of a fluid that can affect the ability of that fluid to transfer heat away from the electric motor. It can be measured directly using a forced convection calorimeter. Oil is circulated through the calorimeter at a specified flow rate, as well as specified wall and fluid temperatures. Heat is applied to the test section to maintain a consistent wall temperature, and the fluid temperature increase is measured across the test section.
Materials compatibility
EV fluids must be able to avoid damaging or being significantly degraded by the metals, polymers or other materials with which they are in contact. Copper corrosion, both immersed and in the vapor space, is one major concern of fluid developers. Copper corrosion not only removes copper from the wiring, but it also forms conductive deposits on various components of the system, both of which can cause catastrophic damage.
A new wire corrosion test has been proposed to ASTM for consideration as a standard method. This 70-hour test uses 400-ml fluid samples heated to between 80 C and 150 C. A small current passes through 1 meter of 64-micrometer diameter wire that is either immersed in the fluid or suspended in the vapor space above the hot lubricant. As copper corrodes away from the wire, the rate of electrical resistance increases, and this can be correlated to the wire’s diameter changes.
Additionally, work has been done to develop EV-specific adaptations to the copper corrosion test method ASTM D130
(see Heat Transfer and Materials Compatibility). In this test, a polished copper strip is immersed in the sample and/or exposed to the vapor space and heated for a specified amount of time. Then, the copper strip is removed, washed and rated by comparing it to a set of standard degraded copper strips. The test is typically run for three hours at 150 C for conventional automatic transmission fluid applications
(see Figure 3). Adapting this method to EV fluids requires extended test durations, including vapor phase exposure and analyzing the copper content of the oil in which the test sample has been submerged.
Figure 3. Extended-duration adaptation of ASTM D130 copper corrosion test. Blue bars show final concentrations of copper in the oil sample (parts per million). Figure courtesy of Chevron Oronite.
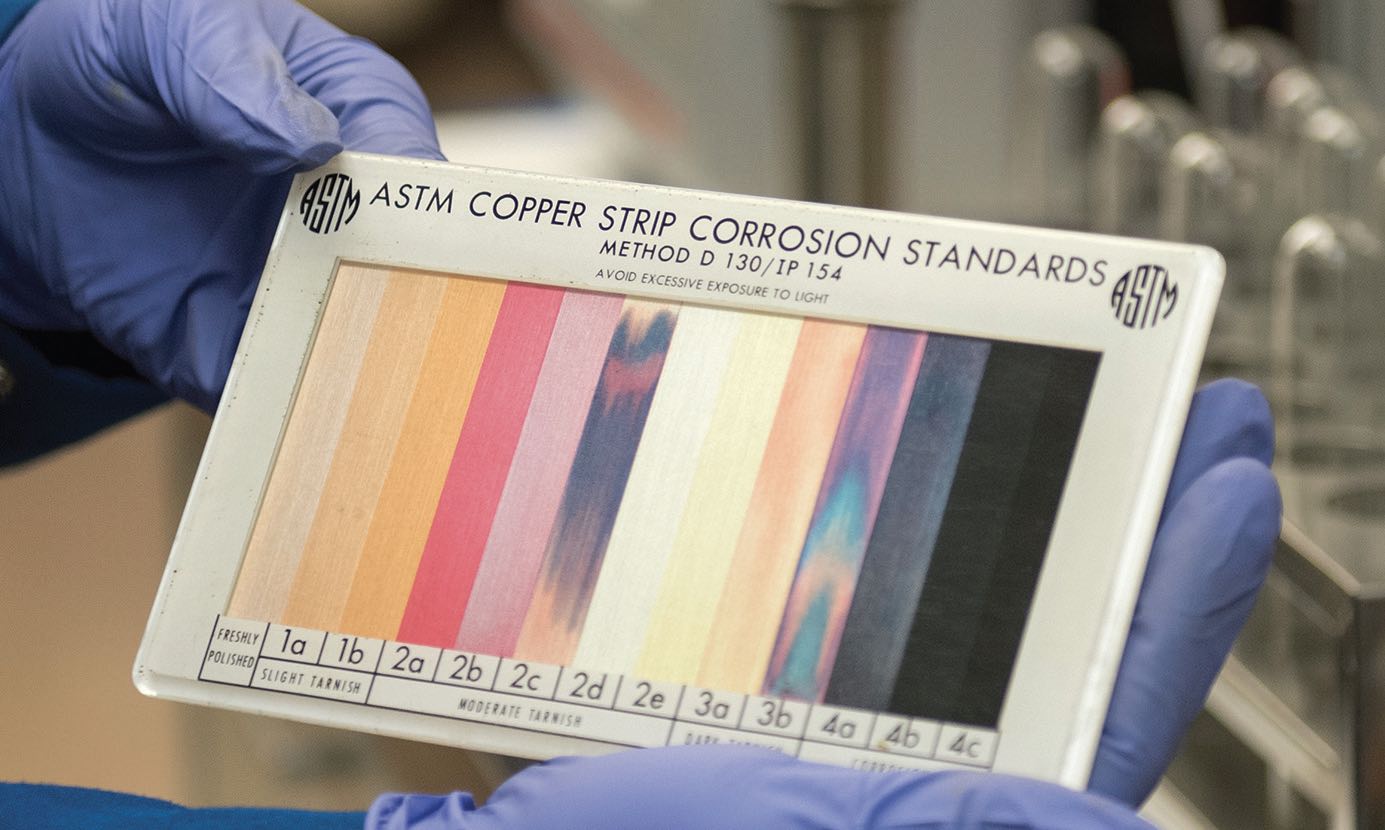
Color chart for ASTM D130 copper corrosion test. Figure courtesy of Airman 1st Class Greg Erwin, U.S. Air Force.
Conductive deposit tests use stacked circuit boards that are exposed to the oil and vapor phases during testing. Conductive deposits form, causing electrical shorts between the boards. The change in electrical resistance over time indicates the formation of conductive deposits shorting the electrical path. Currently, tests can last as long as 1,000 hours.
Polymer products are another area of concern for compatibility. These include structural plastics, wire insulation materials and new plastics that are not commonly used in other applications. Exposure to lubricants can affect polymer swelling, hardness and tensile strength. ASTM D638 is a tensile test method that can be applied after a structural plastic is exposed to a lubricant
(see Figure 4). To ensure this test is relevant, the EV OEM must determine how long to expose plastics and polymers to the test lubricant, what test temperatures best correlate to actual field conditions and what materials are most representative of those in their EVs.
Figure 4. “Dog-bone” polymer sample (left) for ASTM D638 and two types of tensile failure (right). Figure courtesy of Southwest Research Institute.
Motor winding coatings are another area where standardized testing is being investigated, and these tests are still very new. These coatings, typically polymer materials, insulate the motor windings, preventing short circuits and motor failures. Corrosion of the polymer coatings can be evaluated by looking at the breakthrough voltage: the voltage level required to break through the coating to the bare copper below. In one test, coated copper wire “hairpin” samples (a u-shape with the center submerged in the fluid and the ends protruding above the fluid) are aged in a test fluid at a defined temperature (static or dynamic) for a defined duration. At the end of the test, the coatings are evaluated for breakthrough voltage.
Oxidation and aeration
Oxidation performance tests are a given for any type of vehicle fluid, but the oxidation mechanisms in EVs are likely different than the mechanisms evaluated using today’s standard test methods. Lubricants are often sprayed or dripped onto hot EV motor windings or circulated through the motor itself. The temperatures at the fluid– hardware interfaces are relatively high compared to the sump temperature of the fluid. Sump volumes are relatively low, making oxidation control critical.
Although ASTM has no applicable standard methods for this EV-specific situation, several other commonly used tests can provide useful information. These include the ABOT (BJ 110-04), DKA (CEC L-48), L-60-1 (ASTM D5704) and ISOT (JIS K 2514), among others
(see Oxidation and Aeration). However, each of these methods uses very high bulk fluid temperatures instead of the high interface temperatures typically seen in EV applications.
Oxidation and aeration
ABOT (BJ110-04), Aluminum beaker oxidation test (e.g.,
http://doi.org/10.4271/2001-01-1991)
CEC L-48 (http://cectests.org/assets/presentations_publications/cec14_3255_3.pdf), DKA modification (e.g.,
http://doi.org/10.4271/2014-01-2801)
ASTM D5704 (L-60-1) Standard Test Method for Evaluation of the Thermal and Oxidative Stability of Lubricating Oils Used for Manual Transmissions and Final Drive Axles (
www.astm.org/d5704-22.html)
ISOT (JIS K 2514), Indiana stirring oxidation test. Lubricating oils-Determination of oxidation stability - Part 1: Oxidation stability of internal combustion engine oils (
http://infostore.saiglobal.com/en-us/standards/jis-k-2514-1-2013-633384_saig_jsa_jsa_1452587/)
ISO 12152 Lubricants, industrial oils and related products—Determination of the foaming and air release properties of industrial gear oils using a spur gear test rig—Flender foam test procedure (
http://webstore.ansi.org/standards/iso/iso121522012)
ASTM D3427 Standard Test Method for Air Release Properties of Hydrocarbon Based Oils (
www.astm.org/d3427-19.html)
ASTM D892 foam test Standard Test Method for Foaming Characteristics of Lubricating Oils (
www.astm.org/d0892-18e01.html)
The ABOT (aluminum beaker oxidation test, BJ 110-04), developed for automatic transmission fluids, uses lead, aluminum and copper test coupons
(see Figure 5). The test results include viscosity change, pentane insolubles, acid number change, infrared (IR) change, elemental analysis, copper coupon rating, lead coupon weight loss, aluminum strip rating and sludge rating. The DKA method, also commonly used for automatic transmission fluids, tracks changes in viscosity, acid number, IR spectrum and sludge rating. Reported results also include end-of-test flask photos to characterize any deposits generated in the glassware and a blotter evaluation to characterize fluid cleanliness.
Figure 5. Setup for aluminum beaker oxidation test (ABOT). Figure courtesy of Southwest Research Institute.
The ASTM D5704 (L60-1) method was developed for automotive gear lubricant evaluations. This method looks at changes in viscosity, pentane and toluene insolubles and the formation of sludge and carbon varnish deposits. The Indiana stirring oxidation test (ISOT), developed for internal combustion engines, uses steel, a copper catalyst and a glass varnish stick immersed in fluid to evaluate varnish deposits. This test tracks changes in acid number and viscosity, as well as a glass varnish stick rating.
Fluid aeration can facilitate oxidation, and it also can affect heat transfer and gear protection as well as increase churning losses. Several test methods assess foaming performance, including ISO 12152 and ASTM methods D3427 and D892, along with proprietary and in-house test methods. Foaming can be different from aeration (air entrained within the fluid), but it is just as important to EV performance.
The most current aeration test methods in driveline applications aerate the lubricant very differently than what is seen in EV applications. EV motors run at very high speeds, which increases aeration—in one EV motor fluid aeration test operating at up to 17,500 rpm, the aeration level reached almost 25% (75% fluid, 25% air). One example of a high-speed aeration evaluation involves pumping a lubricant from the sump of an electric drive unit through a gas content monitor to evaluate the degree of aeration under a specified set of operating conditions
(see Figure 6).
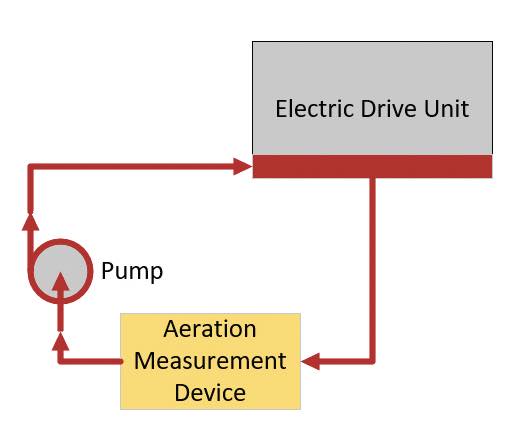
Figure 6. Gas content monitoring of fluid aeration under high-speed operating conditions.
Wear and failure
Today’s EVs have motors operating at 18,000 to 20,000 rpm, and manufacturers are considering taking this significantly higher—possibly up to 50,000 rpm. Today’s standardized gear and bearing tests were not designed with these extreme speed requirements in mind. Historically, the industry has relied heavily on FZG gear testing methods to evaluate different forms of gear wear.
For example, the FZG a10/16.6R/90 step load method can be used to assess extreme scuffing prevention
(see Wear and Failure). Scuffing is the instantaneous welding and release that happens when there is direct metal-to-metal contact. This type of damage occurs when the lubricant is unable to prevent metal-to-metal contact between gear teeth. The test method increases the load on the gears until scuffing occurs. Additional FZG test methods can be used to assess pitting, micropitting and wear.
Wear and failure
DIN-ISO-14635-2 | Part 2: FZG Step Load Test a10/16, 6R/120 for Relative Scuffing Load-Carrying Capacity (
www.document-center.com/standards/show/DIN-ISO-14635-2)
DIN 51 819-3 (D-7.5/80-80), Testing of lubricants: mechanical-dynamic testing in the roller bearing test apparatus
(
http://infostore.saiglobal.com/en-us/standards/din-51819-3-2016-12-421785_saig_din_din_953757/)
Just as important as protecting the gears, the lubricant also must properly protect the bearings from damage and wear. To date, there are no standardized high-speed bearing tests, but historical tests can be used to assess a lubricant’s ability to appropriately protect the bearings. The DIN 51 819-3 (D-7.5/80-80) test evaluates the lubricant’s ability to prevent wear on the bearing rollers.
Battery coolants
There is significant potential for improvements in the area of direct liquid battery coolants. In a typical EV battery configuration, the cells sit on top of a cold plate, with a water-glycol solution passing underneath. However, in direct liquid battery cooled systems, the coolant passes directly between the battery cells, creating an interface between the fluid and the cells
(see Figure 7). The result is more effective heat transfer, which improves charging and discharging performance, potentially preventing fire propagation in the event of a battery cell failure. However, coolants must be compatible with batteries and their packaging materials.
Figure 7. EV battery cooling using a cold plate system (top) and direct cooling of the cells (bottom). Figure courtesy of Moghaddam, H. and Mazyar, S. (2018), “Designing battery thermal management systems (BTMS) for cylindrical Lithium-ion battery modules using CFD,” KTH, School of Industrial Engineering and Management (ITM), Energy Technology, Independent Thesis, Advanced level. Available at https://urn.kb.se/resolve?urn=urn:nbn:se:kth:diva-244459.
Factors to consider in fluid formulations include the fluid’s ability to remove heat from the battery cells while resisting combustion. Can the fluid mitigate or reduce thermal propagation and thermal runaway? Does the fluid keep the battery cooler? Does it increase the number of charge and discharge cycles? Can the battery be charged or discharged more rapidly? A fluid’s fire resistance is a major concern: if one battery cell fails and goes into thermal runaway, it may catch fire. If the fire spreads to adjacent cells, the entire battery pack may ignite.
Nail penetration tests simulate battery failure. For this type of testing, battery cells are fully charged at ambient conditions. Thermocouples are attached to each cell, and the battery is immersed in a circulating fluid maintained at a temperature typical of vehicle operating conditions. A nail is driven through one cell to see if it starts a fire and whether the fire spreads to nearby cells. Heat-induced failure testing involves a similar setup to the nail penetration test, but it uses a heater wire placed amongst the cells in a battery module. After the battery cells are fully charged under ambient conditions, the heater wire is energized and the ability of the coolant fluid to prevent and contain thermal runaway is assessed.
Battery life and performance testing involves placing a battery module and a container with the direct liquid battery coolant into a test chamber plumbed to a circulation system. The battery pack is wired to a battery cycling device in order to create an accelerated aging profile
(see Figure 8). This method can be used for comparing various batteries and fluids to see how they perform.
Figure 8. Battery performance and life testing charge/discharge profile (top) and test setup (bottom). Figure courtesy of Southwest Research Institute.
Life testing involves repeatedly running a fast charge/discharge profile to accelerate aging under high stress. Every five days, the test module is compared to a baseline performance test to assess the battery state of health and determine the effect of the direct liquid battery cooling to extend the life of the battery.
Performance testing targets a temperature rise on the fast charge profile, which helps to set limits on how fast a vehicle can be charged safely. The ability of the coolant to maintain the battery’s temperature within acceptable limits during faster charging is measured. If the charging speed is increased and the temperature rises above an acceptable limit, the chances of battery degradation and failure are increased. Cooling performance during battery discharging also is important, especially for large vehicles and heavy-duty applications.
A work in progress
Although EV designs are currently robust enough for EVs to be sold as consumer products across all sectors (passenger cars, commercial applications and offroad applications), the field is still in its infancy. At present, the number of EVs in operation is still very small compared with the number of internal combustion engine vehicles on the road.
Because EV drive unit design is not a mature field, future EVs may look much different than today’s models, so test methods for EV fluids must be developed to be forward looking. Several standardized test methods are under development, and some are now under ASTM and DIN evaluation. The degree and urgency of industry demand for standardization will play a significant role in the types of methods that are developed and how quickly this effort moves ahead.
The key for any standardized test method is to ensure that it is not only repeatable and able to differentiate between different lubricants, but also that it strongly correlates to field performance. Lubricant formulators need good tools to enable them to determine if a formulation change is providing the desired benefit in that performance attribute as well as not affecting the formulation negatively in other performance requirements. We expect to see significant developments in new EV-specific lubricant tests in the coming years that will help enable the development of superior lubricants, which, in turn, will help further the implementation of EVs.
Nancy McGuire is a freelance writer based in Albuquerque, N.M. You can contact her at nmcguire@wordchemist.com.