Lithium iron phosphate EV batteries
By Don Smolenski, Contributing Editor | TLT Machinery August 2023
This developing technology offers a promising alternative to nickel and cobalt.
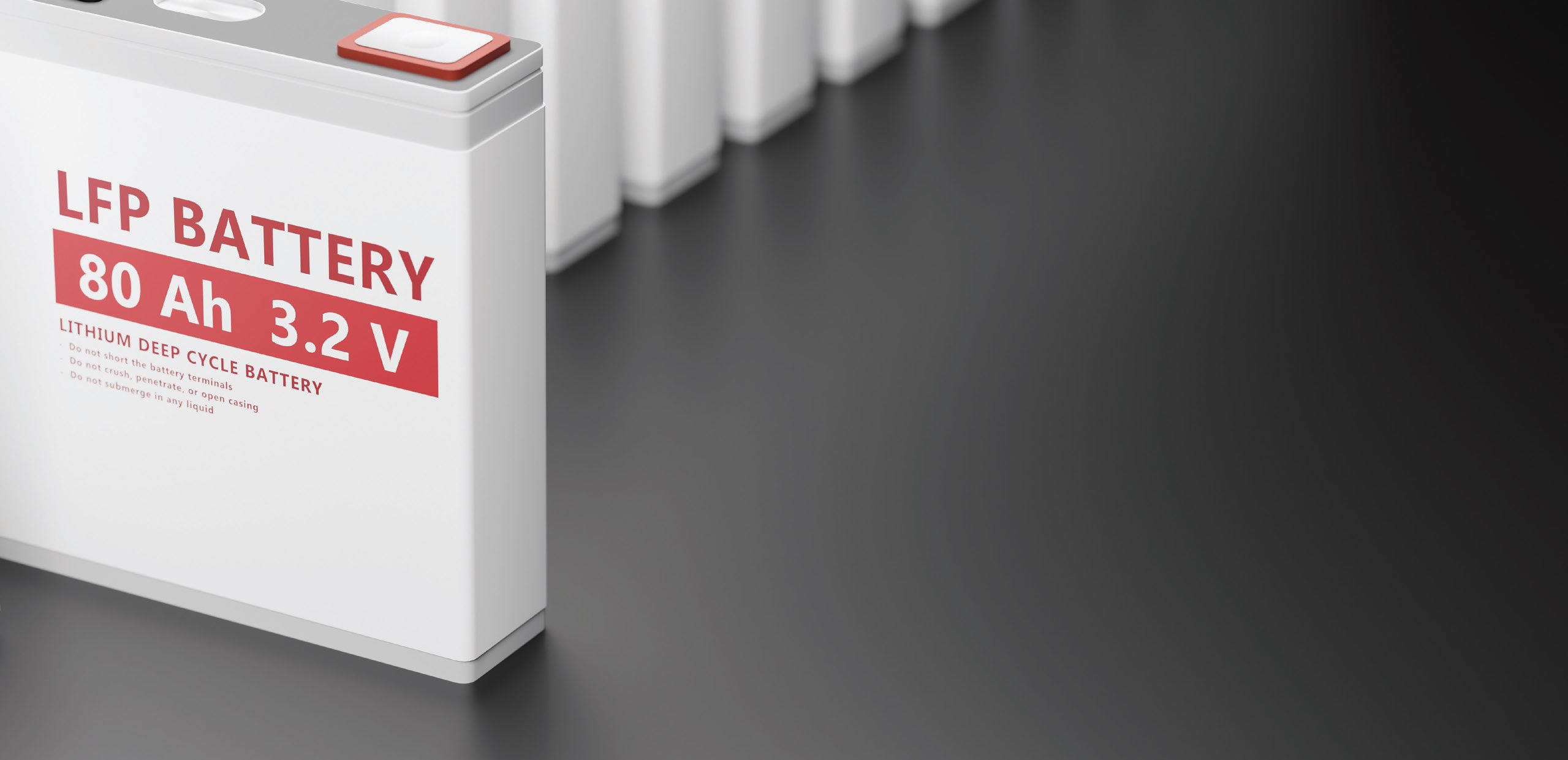
In a previous TLT column,1 I discussed the shortage of key electric vehicle (EV) battery raw materials. Electric car companies are looking for alternatives to nickel and cobalt because of their high costs. Lithium iron phosphate (LFP) is a new, promising alternative, except for the fact that most LFP required raw materials still come from China,
2 and many EV companies are trying to increase the robustness of their supply chain by reducing their dependence on China.
LFP has actually been around for a while for making cathodes, but nickel-cobalt cathodes provide better energy density and higher range. Nickel-based batteries, however, can’t be recharged as many times as LFP batteries, and also are reportedly more prone to fires. Several OEMs are planning to use LFP batteries, expecting that they will bring significant cost savings. A marine propulsion company strongly supports their use in a small but growing marine market.
3 They claim improved charge and discharge efficiency and deep cycle capability. They also are much lighter compared to lead acid batteries, which are often used in marine applications, and they claim a life of up to 5,000 cycles without any significant loss of performance. They also note that LFP batteries reportedly do not experience thermal runaway.
LFP batteries can operate at full charge capacity from -20 C to 70 C. Initially, they suffered from conductivity problems, but these were largely solved by coating the LFD cathodes with carbon. Even though LFP batteries were first invented and developed in the U.S.,2 China significantly improved them. Most Chinese companies react iron sulfate with phosphoric acid to produce iron phosphate, which is mixed with lithium carbonate, and then heated to over 700 C to “sinter” the material. They installed LFP batteries in buses before the 2008 Beijing Olympics, and now LFP batteries are used in 40% of EVs in China.
2 China’s capacity to make LFP cells has increased 100-fold in the last decade. One company, for instance, increased its LFP capacity from 500 to 265,000 tons. China has cost advantages because iron sulfate is a byproduct of another process, and also because environmental regulations are generally looser there.
Nonetheless, many Chinese LFP producers are expanding overseas. In 2022, a major battery supplier planned a plant in Europe. Shortly thereafter, an economic development agency awarded one of their subsidiaries grants and incentives to build a huge plant in Michigan, which will produce 150,000 tons/year of materials for LFP cathodes. Many western firms are jumping into the fray, either using established technologies with partners, or using new technologies. In the U.S., SUVs and pickup trucks will require larger batteries because of their size and often more strenuous duty cycle (Americans like their road trips!).
I always advise young engineers on a project to make it work first—and then make it better and cheaper. It looks like the lithium iron phosphate battery basically “works.” With so many good companies and people working to develop LFP batteries, I’m confident that they will be better and less expensive over time.
REFERENCES
1.
Smolenski, D. (2023), Recycling of electric vehicle batteries,” TLT,
79 (4), p. 88. Available
here.
2.
Blois, M. (Jan. 29, 2023), “Lithium iron phosphate comes to America,”
Chemical and Engineering News. Available
here.
3.
ePropulsion (July 15, 2022), “What are the benefits of lithium iron phosphate batteries (LiFePO4)?” Available
here.
Don Smolenski is president of his own consultancy, Strategic Management of Oil, LLC, in St. Clair Shores, Mich. You can reach him at donald.smolenski@gmail.com.