Meet the Presenter
This article is based on a Webinar presented by STLE Education on June 8, 2022. The Tribology of Piston Rings and Why It Matters in an EV World is available at www.stle.org: $39 to STLE members, $59 for all others.
STLE member Lake Speed, Jr. is the vice president of sales and marketing for Total Seal Piston Rings in Phoenix, Az. He runs Hidden Horsepower podcasts with Joe Castello. He is the son of former NASCAR driver and team owner Lake Speed, Sr. As a kid, Speed grew up at racetracks across the country and started racing go-karts when he was eight years old, though by the time he was a teenager, he realized a driving career was not for him. Speed’s father raced in NASCAR from 1980 until 1998. For many of those years, his father operated his own independent race team in Charlotte, N.C., so he spent several summers working on his dad’s team. By the time he went to college, he was traveling with the team.
Speed graduated from the University of Tennessee with a bachelor’s degree in communications. After graduation, he moved to Charlotte and went to work for a local advertising agency. He learned quickly that working on race cars was a lot more fun, so he went to work for Melling Racing, which fielded the #9 NASCAR team that Bill Elliott made famous back in the late 1980s. Melling Racing also was one of the original Dodge teams when Dodge got back into NASCAR in 2001. During his time with Melling, they developed an engineering department and began testing programs with the aim to improve performance. After working for Melling Racing, he joined Joe Gibbs Racing in 2004.
At Joe Gibbs Racing, Speed began studying lubrication fundamentals and chemistry. Over the years, he helped lead Joe Gibbs Racing to win over 100 races and five championships. In 2019, he joined Total Seal to advance the tribology of piston rings. Speed also is a member of SAE, and his background in tribology provides a unique perspective on engine performance and durability. You can reach him at lspeedjr@me.com or (704) 239-4401.
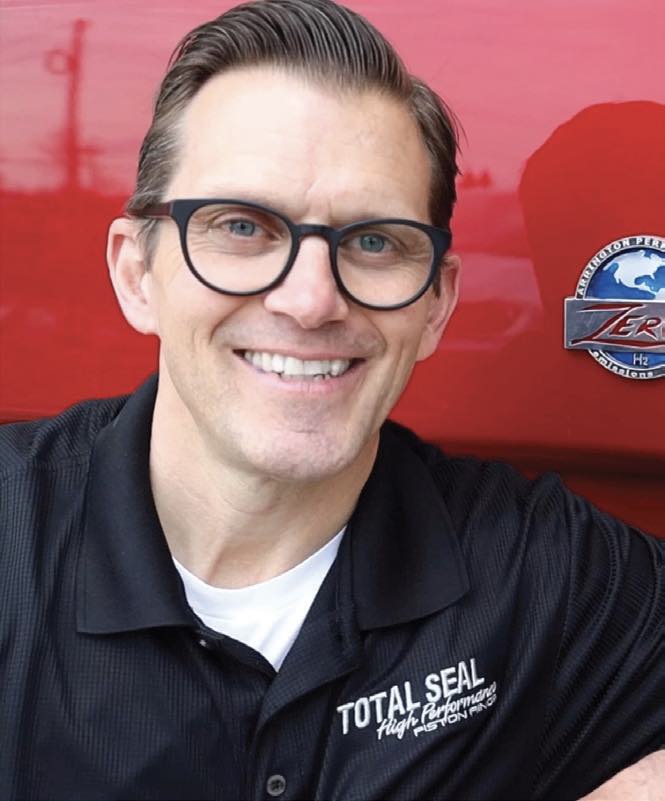
Lake Speed, Jr.
KEY CONCEPTS
•
Industries are still going to be building internal combustion engines for at least another decade if not longer.
•
The interaction between the piston ring and the cylinder bore is the No. 1 source of friction in an internal combustion engine.
•
The lessons learned from studying piston rings in terms of surface finish, friction modifiers and different coatings and materials can all be applied to electric drive motors to overcome some of the challenges they face.
STLE member Lake Speed, Jr., vice president of sales and marketing for Total Seal Piston Rings in Phoenix, Az., notes that today’s racing shows an image of teams of engineers working to extract more efficiency from parts and engines. In addition, the focus from racing can translate to the real world and help address problems faced when creating a more sustainable future. Racing can get things done rapidly while testing in extreme environments, which makes the racing world a great resource for the world of tribology.
This article is based on an STLE Webinar presented by Speed. See Meet the Presenter for more information.
Speed states that research indicates more than 35% of all engine friction comes from the interface of the piston ring against the cylinder wall. Piston rings experience all three stages of lubrication (i.e., boundary, mixed and hydrodynamic) in each engine cycle. This means that the tribology of the piston ring and cylinder wall interface provides a way to improve internal combustion engine (ICE) efficiency.
People may ask whether this matters in a world with a commitment to move to fully electric vehicles (EVs). Will ICEs still have a role in the future? Will piston rings still have a role? Can applying tribology to the piston ring and cylinder wall contact result in a more sustainable future? Can the tribology of piston rings apply to other pieces of equipment? This article answers those questions with a strong “yes.”
Efficiency
Speed says that the way to improve efficiency is not going to be a magic bullet or a magic additive that makes everything better. The way to increase efficiency is through synergies between materials, finishes, additives and base oils all combined to unlock that potential. Meeting the challenge of increasing efficiency will require embracing the full science of tribology.
Industries are still going to be building ICEs (e.g., turbocharged, direct injection, variable compression, etc.) for at least another decade, if not longer. When looking at battery electrics, fuel cells and plug-in hybrids, Speed predicts a mixture of these options going forward.
Racing has shown the way to massive improvements in the efficiency of ICEs. A current Formula One engine is a turbocharged direct injected hybrid engine with greater than 50% thermal efficiency. Speed notes that improvements that are expensive today won’t be as costly in the future once they are adopted and put to scale. That’s why this article doesn’t look at cost as a controlling factor. As the racing world allows proof of concept testing, techniques can move into the mass production world and achieve greater efficiency across the entire field, which is really the goal of this work.
This means that scientists need to continue to study the interaction between the piston ring and the cylinder bore because it is the No. 1 source of friction in an ICE. Additionally, the lessons learned in terms of surface finish, friction modifiers, different coatings and different materials can all be applied to electric drive motors to overcome some of the challenges they face.
The role of the piston ring
Piston rings operate in boundary, mixed and hydrodynamic lubrication every engine cycle. In addition, piston ring performance greatly depends on cylinder bore surface finish, and the knowledge resulting from improving that performance also can be applied to both electric motors and the gearbox.
As previously noted, cost is not considered as a limiting factor for this research. Examples that otherwise might have been cost limited are diamond-like carbon (DLC) coatings and hydrogen combustion. Once new techniques and technologies make their way into production, economies of scale reduce costs.
The ICE used to be the only power source for the vehicle, but the idea of the series hybrid changes the ICE into a generator. This means the engine speed and compression ratio can be idealized to unlock even more efficiency by making the engine smaller with fewer components. As engines become generators, they will be smaller, which means that more money can be spent on the components. While this isn’t necessarily the cheapest solution in terms of engine cost per cylinder, it can be the best solution when users are willing to pay for efficiency. This means there is opportunity to apply knowledge of piston rings and the development of the ICE even within the EV world.
Thermal efficiency
Speed explains that fuel energy goes into the engine with 35% of it going out the exhaust, 30% going to cooling and 35% going to horsepower. This makes the engine about 35% thermal efficient. To achieve 50% in Formula One, a direct injection engine coupled with hybrid turbocharging is used so the exhaust gas isn’t just creating boost pressure. The exhaust gas also is used to recover energy, which can then be separately used to create boost pressure independent of the engine speed. While an expensive achievement, by hybridizing the turbocharger and using very advanced lubricants, cylinder finishes, ring materials, cylinder walls and coatings to reduce friction, efficiency issues are improved.
One report is finding that a lot of the engine friction occurs in the cylinder where coatings can be used to reduce cylinder friction. Even though battery operated vehicles are predicted for the future, izing engine performance is still important, as those same coatings could increase the efficiency of EV gearboxes.
People know that motor oil is a lubricant but tend to forget it also is a coolant. Piston oilers are not a new technology. Motor oil sprayed on the piston can act as a coolant, meaning that the piston rings alone are not responsible for transferring heat out of the piston. When a base oil with a higher specific heat capacity is used, more heat can be pulled out of the piston without increasing the oil temperature, or possibly with only a small increase in oil temperature. This enables the use of thinner rings, which increases engine efficiency. This is an example of using a systems approach to engine efficiency rather than looking for a magic bullet solution.
Sealing to avoid power losses
The power output of an engine is what is left over after all the “losses,” so the easiest way to make more power is by “saving” the power already made. In other words, power output can be increased by cutting losses. Small details can add up to big power gains through the piston ring seal, ring friction (i.e., if the system is not sealed, combustion energy is being wasted), surface roughness and oil formulation (i.e., chemistry must adapt to the application). The rougher the surfaces are throughout the engine, the higher the viscosity of the oil has to be, and the more friction is present.
The piston rings in an engine are going from boundary to mixed to full film during every cycle
(see Figure 1). This means that the surface finish influences those transitions, and surface coatings can impact the coefficient of friction in the boundary and mixed film regimes. Lowering the oil viscosity can mean lower friction, especially at higher surface speeds. Blow-by is the enemy of oil.
Figure 1. Stribeck curve: The piston rings in an engine are going from boundary to mixed to full film during every cycle.
Blow-by also is the enemy of efficiency, especially when the goal is to make sure every ounce of combustion energy is used to drive the piston. The piston ring makes this possible by keeping combustion gases and unburnt fuel out of the crankcase. The leak path is how blow-by gets past the piston ring and that path needs to be eliminated. Speed identifies three potential leak paths
(see Figure 2):
1.
At the ring end gap—there is a time and place for gapless ring designs. A little bit of blow-by can be a benefit if it is used correctly.
2.
Around the ring in grooves—the piston ring seals against the ring groove of the piston. The rougher the ring groove surface, the more likely leaks can occur. Therefore, these surfaces need to be as smooth and flat as possible.
3.
Between the face and the cylinder wall.
Figure 2. Three potential leak paths in a piston ring seal.
Piston rings are not 100% round in the free state before being installed in the engine. There is a slight coil in the design to create tension and hold it against the cylinder wall. A small vertical clearance around the piston ring in the piston groove allows combustion pressure to get behind the ring and push the piston ring against the cylinder wall to seal it dynamically.
Oil also functions as a gasket. Simply put, the oil film between the piston ring and the cylinder bore acts as a sealant
(see Figure 3). The cylinder bore surface finish can be designed to retain the proper amount of oil. If the cylinder bore surface is too rough, it will add abrasion; if the surface is too smooth, it will add adhesion. This becomes a “Goldilocks and the Three Bears” situation where the desired surface is gently undulating with a smooth top surface and valleys below to hold the oil and the surface is “just right.” Retaining the proper amount of oil, especially with the more fuel run through the engine, is the challenge.
Figure 3. Piston ring lubrication; oil is the gasket and lubricant.
Piston ring friction is defined as the coefficient of friction (CoF)
(see Table 1) times load. Previously cast iron was used as it was cheap and could wear for a long time, but it was relatively soft. Plasma moly is a newer material with a low coefficient of friction. Harder surface coatings like DLC offer even lower friction, but correspondingly need more valley in the finish to make it function correctly.
Table 1. Coefficient of friction
When the friction force is reduced, for example with a DLC coated ring, the ring itself can be thinner with lower ring tension. The friction force can be further reduced by that reduction in load. To make the ring thinner, the material the ring is made from must change. For example, cast iron has poor durability as a brittle soft material that wears quickly, so other materials must be used. Also, when rings are cast, material must be subtracted to obtain the desired shape. In contrast, making the ring from wire allows for less waste. Stainless steel has great corrosion resistance and can be formed from wire. Tool steel is very strong and an excellent high temperature material.
These coatings and ring materials solve the challenges with using a ductile iron ring with a molybdenum face coating—the material itself and the channel in the ring face for the molybdenum limits axial thinness.
There is another synergy between the cylinder bore and the cylinder surface finish that can be achieved through thermal spray coating, which creates deep valleys or pores to hold the oil. Spraying in an iron liner and creating a mirror finish can lower the overall friction of the cylinder.
DLC coatings have been used for more than 20 years in professional motor sports; however, DLC is sensitive to the type of friction modifiers used, so the friction modifier has to work well with DLC to make sure the coating is durable.
As previously mentioned, gas pressure behind the ring helps it to seal. It is possible to drill holes in the piston to allow the gas pressure to move the ring outward more easily
(see Figure 4); however, the carbon in fuel can clog those holes, resulting in wear of the cylinder wall. For longer oil life, reducing blow-by by adding gas ports in the piston ring instead results in less blow-by overall. Less blow-by also means cooler temperatures.
Figure 4. Gas porting.
Thinner rings also reduce overall heat generated by friction as there is less contact area. Thinner rings also mean that engines last longer with greater efficiency. The engine may cost more to build initially, but if it lasts longer, the math may work out. All of these technologies are currently being used to win races and championships at the highest levels of motor sports.
Hydrogen combustion
Hydrogen combustion may be one approach that can bridge the fossil fuel transition, but we lack the experience yet to know if it is a truly viable option. The technology has a need for advanced materials and coatings.
Companies in Japan and the U.S. are already building and running hydrogen combustion engines, which are still combustion engines with different challenges. For example, water generated through hydrogen combustion will be a challenge to manage as it can lead to corrosion of parts. One company is trying to increase corrosion resistance using stainless steel sprayed on liners in response to the amount of water in the engine. That same approach may apply to hydrogen combustion engines where stainless-steel rings or a stainless-steel bore with a ring coating may be needed so the engine isn’t running stainless steel against stainless steel.
Hydrogen has a higher flame speed, which enables larger bore engines or higher speed engines. Something to consider could be a hydrogen combustion generator with an electric drive but with high levels of current flow to turn the generator extremely fast. This could possibly result in a zero emissions generator through combining technologies.
Conclusions
In summary:
•
Thinner piston rings can increase the efficiency of ICEs, both traditional use and series hybrid.
•
Piston rings greatly depend on cylinder bore surface finish, so piston ring development taps into the full spectrum of tribology.
•
Advanced materials and coatings will enable researchers to handle the challenges of hydrogen combustion engines.
Speed observed that racing engineering is at a great point where people can come up with crazy ideas and throw them against the wall to see what sticks. That’s the racing mentality. Researchers can’t be afraid to fail. They have to be willing to try a lot of different things and see what actually works. That approach will lead to reducing friction across the full range of lubrication regimes.
Andrea R. Aikin is a freelance science writer and editor based in the Denver area. You can contact her at pivoaiki@sprynet.com.