More on recycling of electric vehicle batteries
By Don Smolenski, Contributing Editor | TLT Machinery June 2023
Factors such as energy consumption, economic considerations and environmental impact are taken into account when choosing a recycling process.
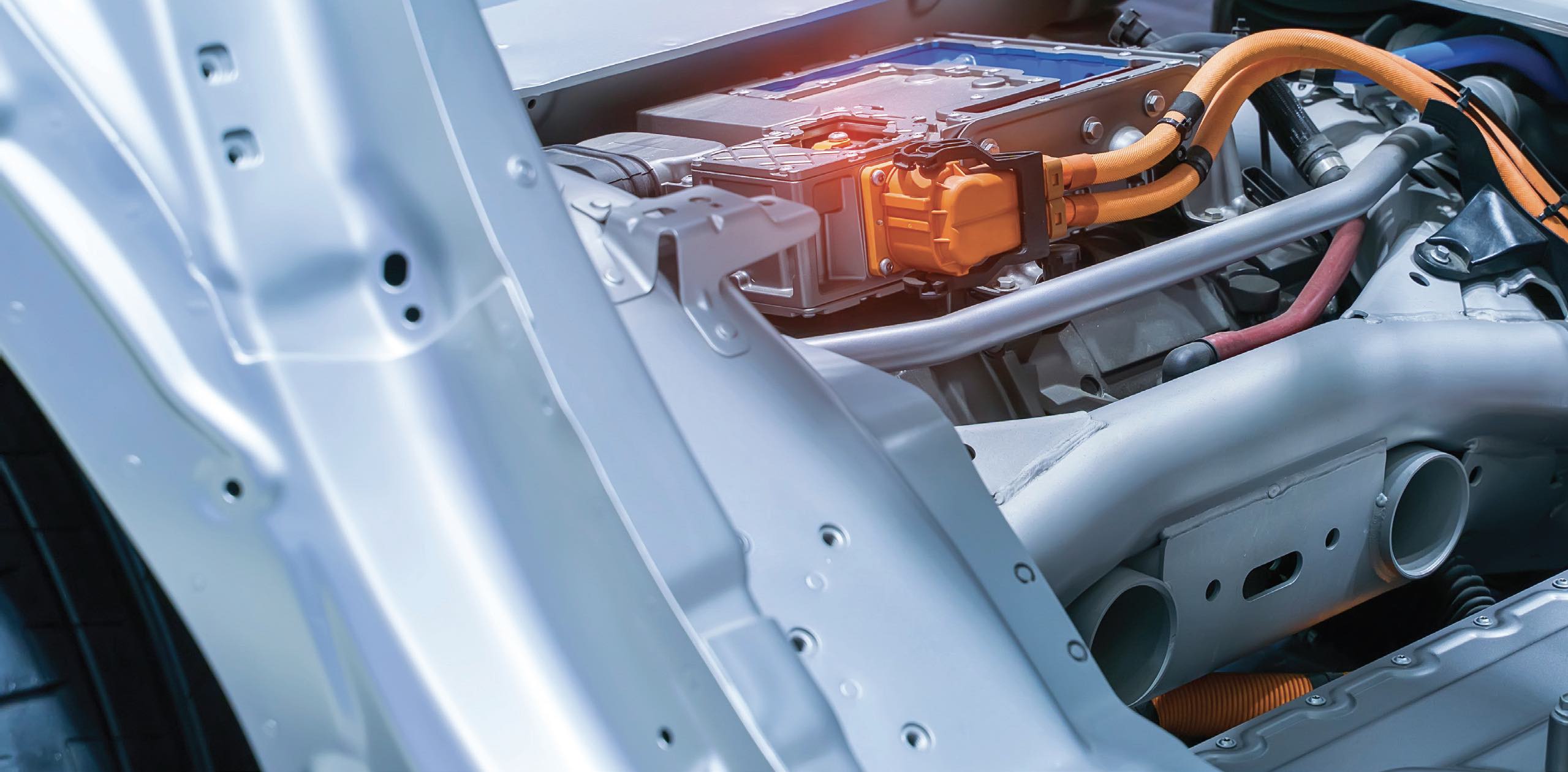
In a previous column,1 I discussed the need for recycling of electric vehicle (EV) batteries, both because of the need for responsibly dealing with the batteries at the end of their life and because of the shortage of key battery raw materials. There was a brief discussion on repurposing of the spent batteries, which entails using the batteries in new and different functions, as opposed to recovering the various raw materials in the batteries. I presented data on the volumes of required raw materials to show the expected demand for various recovered metals. It is worth noting that the average lithium (Li) content of recycled batteries is considerably higher than the Li content in many natural ores. This column will dive more deeply into the battery recycling processes.
Recycling consists of several steps, incorporating physical and chemical processes. Physical processes include discharging the battery, disassembly, electrolyte recovery, cathode recovery and carbon black and battery shredding to recover polyvinylidene fluoride (PVDF). These processes may employ mechanical screening or magnetic separation and washing. Chemical processes can include pyrometallurgical and/or hydrometallurgical processes.
As an example, one company based in Canada that recycles EV batteries
2 shreds the batteries, recovering aluminum, copper and plastic that can be sold to other companies for further recycling. Hydrometallurgy is then used to produce a “black mass,” which contains key metals. This process consists of metal dissolution, concentration, separation/purification and recovery. The company estimates that 15 million tons of batteries will reach life’s end by 2030.
2
At present, hydrometallurgy is one chemical treatment typically used to recover Li after pretreatment, depending on the physical properties of the materials in the spent batteries, including morphology, density, magnetism, etc.
3 The treated battery cases, electrodes and membranes containing electrolytes will be treated separately to improve the safety and recovery rate of hydrometallurgical processes, and to reduce energy consumption. Hydrometallurgy generally involves leaching using inorganic acids, such as hydrochloric, sulfuric or nitric acid, and subsequent reduction with hydrogen peroxide, for example, followed by precipitation. Recovery rates of key metals of over 90% are not uncommon.
In the pyrometallurgical process, batteries are reduced by sequentially preheating, pyrolysis and smelting. The batteries are first preheated to not above 300 C to remove any remaining solvent, and then heated to above 700 C to remove any remaining plastic. In the reduction zone, the material is smelted into metal alloys. Pyrometallurgy is widely used for the commercial recovery of cobalt (Co).
3 The commonly used treatment of spent Li batteries is similar to ore smelting. Before the smelting process, the batteries are first disassembled into separate cells and then fed into a furnace where they are “smelted.”
The process of choice is partly influenced by the maturity of each process (e.g., a very similar process is currently widely used for other products) and partly dependent on the economics of the metals produced. Environmental and energy consumption considerations also are factored in.
REFERENCES
1.
Smolenski, D. (2023), “Recycling of electric vehicle batteries,” TLT,
79 (4), p. 88. Available
here.
2.
SAE International (October 2022), “Closing the loop on EV battery recycling,” Automotive Engineering, pp. 18-25. Available
here.
3.
Zhou, L., Yang, D., Du, T., Gong, H. and Luo, W. (2020), “The current process for the recycling of spent lithium ion batteries,”
Front. Chem., 8, https://doi.org/10.3389/fchem.2020.578044.
Don Smolenski is president of his own consultancy, Strategic Management of Oil, LLC, in St. Clair Shores, Mich. You can reach him at donald.smolenski@gmail.com.