TLT: What attracted you to sealing technology, and how did you get involved in tribology?
Sato: You can find seals everywhere in daily life as gaskets or packings. Their function is to prevent the leakage of fluids and any contaminants coming into the inside. Consequently, all machinery requires seals for safe operation throughout its life—especially radial lips seals, which are widely used for dynamic sealing. They have to provide zero leakage as well as less friction and less wear, while they make sliding contact against the counterface for more than 100,000 miles. This looks like magic in terms of tribology, because eliminating the fluid film would achieve less leakage while, on the other hand, forming certain film would provide better lubrication and less wear. That was my starting point to exploring tribology.
TLT: Tell us any recent exciting experiences in your research and development.
Sato: As I mentioned, radial lip seals provide perfect sealing with little wear throughout their lives. Indeed, most previous research regarding the lubrication of radial lip seals had concluded that hydrodynamic lubrication was dominant. This was acceptable, but we could find few experimental studies on the formation of hydrodynamic film between the sealing surfaces. This was in contrast to the extensive studies on lubrication films in bearings with a number of methods, including optical methods. So, I started visualization of the fluid film formations and finally succeeded by using the laser-induced fluorescence (LIF) technique. The 3D film profiles I got under the sealing condition were exciting; they clearly showed that micro-asperities on the rubber lip form hydrodynamic fluid film. Furthermore, film thickness gradually decreased toward the air side, which suggested that lubrication around the air side was more starved rather than fully flooded
(see Figure 1).
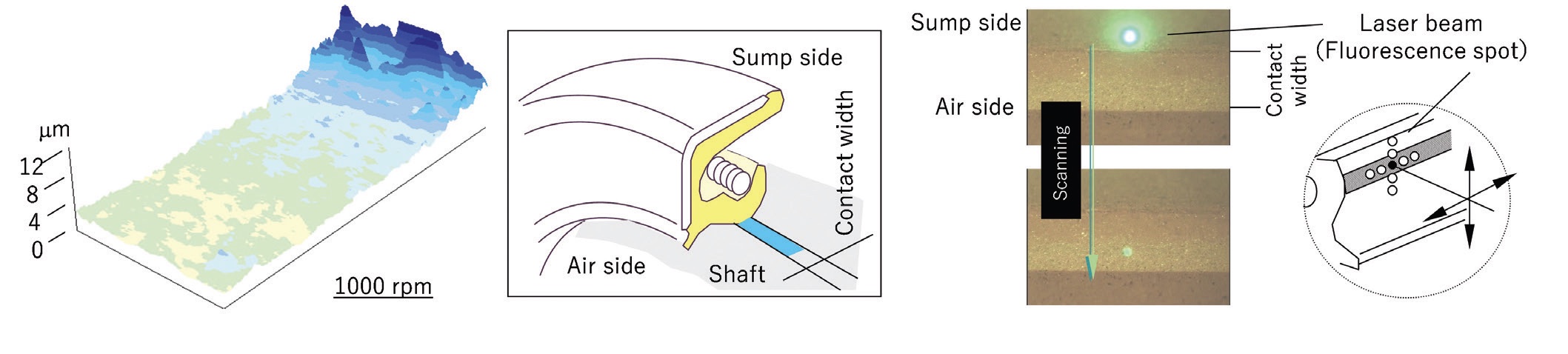
Figure 1. Typical 3D film profile while sealing, and LIF technique applied to measure the profiles of radial lip seals.
TLT: Which technological aspects are important in improving radial lip seals?
Sato: It had long been thought that the lubrication of a radial lip seal is hydrodynamic, but the latest results we’ve obtained show that the actual lubrication film profile differs from place to place. So, it would be reasonable to consider mixed or boundary lubrication rather than hydrodynamic, which is dominant in many parts on the sealing surface. In order to clarify that, microscopic or molecular scale investigation for the sealing surfaces is required. Through those investigations, I believe that we could propose innovative solutions to further reduce friction and to extend the lives of radial lip seals. All machinery requires seals for safe operation throughout its life.
TLT: What are your current tasks and issues as a general manager?
Sato: Needless to say, pursuing a sustainable society is one of the most important tasks throughout the world. And for this purpose, electrification and decarbonization are occurring. Our industrial and automobile customers are changing to introduce renewable energies, ecofriendly materials and electrifications. These often make the operating conditions of radial lip seals more severe than ever—and, for instance, the rotating shaft speed of battery electric vehicle motors may reach much higher speed than that of internal combustion engines, and the viscosity of motor oil is getting lower for the reduction of dragging energy, which causes much heat around the sliding surfaces of the seals.
Yuki Sato standing next to the LIF test rig to measure fluid film.
In the meantime, restriction of using synthetic materials, which have excellent properties (e.g., good chemical and thermal resistance), is becoming more strict than ever because of the environmental concerns. Consequently, we should continue proposing better sealing solutions for electrified machineries and decolonized industries, by using ecofriendly materials and processes. I would say this looks impossible if we act discretely. We should be more inclusive, get many internal/external technologies and divisions involved and keep challenging to find the comprehensive solutions for a sustainable society.
TLT: Please give any suggestions or advice to young researchers and engineers.
Sato: Doubt common sense—the truth is always at the sliding boundary. Dive into it!
You can reach Yuki Sato at Sato.Yuki@jp.nokgrp.com.