Meet the Presenter
This article is based on a webinar presented by Min Zou on Nov. 2, 2021, titled Bioinspired Surface Micro/ Nano-Topography Engineering for Tribological Applications, for the Beard Tribology Webinar Series organized by Auburn University. The webinar series is named after the late Ralph Beard, who pioneered the study of tribology at Auburn. For more information on the webinar series, visit www.eng.auburn.edu/programs/tribology/beard-tribology-webinar.html.
STLE Fellow Min Zou is a distinguished professor of mechanical engineering at the University of Arkansas and currently holds the Twenty-First Century Chair of Materials, Manufacturing, and Integrated Systems. She is the director of the Nanomechanics and Tribology Laboratory (NMTL) and director of the NSF Center for Advanced Surface Engineering (CASE).
Her research focuses on advanced surface engineering that incorporates nanomaterials, coatings and micro/nano-surface topographies (many of which are inspired by nature) to produce functional surfaces that have practical applications. Her lab has developed several technologies that are being commercialized by spin-off companies with products on the market.
You can reach Zou at mzou@uark.edu.
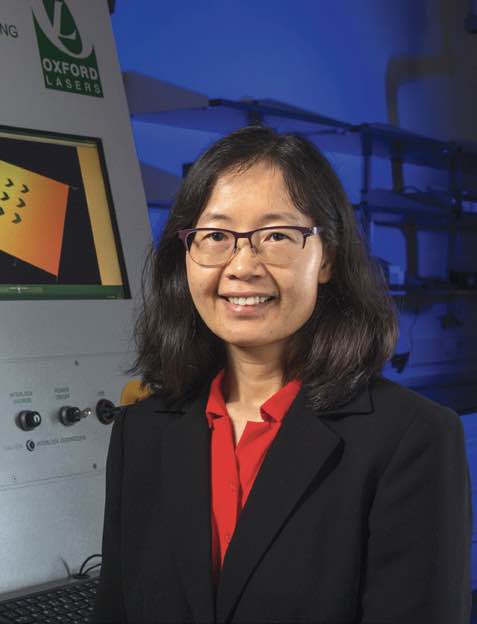
Min Zou
KEY CONCEPTS
•
Bioinspired surface textures can significantly reduce friction by reducing surface contact areas, storing and distributing lubricants and enhancing lubricant film formation.
•
Fabricating simplified structures with key functional features can be more efficient than duplicating complex biological surfaces.
•
Advanced 3D nanoprinting techniques enable new capabilities for making micro- and nano-textured surfaces.
Surface engineering is “mission critical” in many key fields, including the automotive, aerospace, transportation and mining industries. Surface engineering traditionally focuses on coating technologies. However, surface topographies, from the macroscale treads that provide traction between tires and road surfaces to the microscale (or nanoscale) pillars that reduce friction in microelectromechanical devices, play key roles in the ways that surfaces interact with each other and with their environments.
This article is based on a webinar titled Bioinspired Surface Micro/Nano-Topography Engineering for Tribological Applications, presented by STLE Fellow Dr. Min Zou— distinguished professor of mechanical engineering and Twenty-First Century Chair of Materials, Manufacturing, and Integrated Systems at the University of Arkansas. See Meet the Presenter for more information.
Nature provides a wealth of examples of functional surface structures at scales from the macro to the nano. Seashells, human cartilage, frog toe skin, lotus leaves and many other complex, renewable biological surfaces have evolved over millennia to provide water repellence, surface adhesion, lubricant reservoirs and a multitude of other useful properties. Thus, it seems only natural that scientists and engineers would turn to these surfaces for inspiration.
Human-engineered surface topographies at the micro- and nanoscales affect contact zone conditions in various ways, depending on lubrication and loading conditions. For example, microscale and nanoscale topographies provide hydrodynamic lift in fully lubricated interfaces. They enhance the formation of elastohydrodynamic lubricant films in heavily loaded contact regions. Low spots in surface topographies serve as lubricant reservoirs in starved lubrication and as traps for wear debris under boundary lubrication. Under dry contact, micro- and nanoscale surface topographies reduce adhesion and friction by reducing the contact area between two surfaces
(see Figure 1).
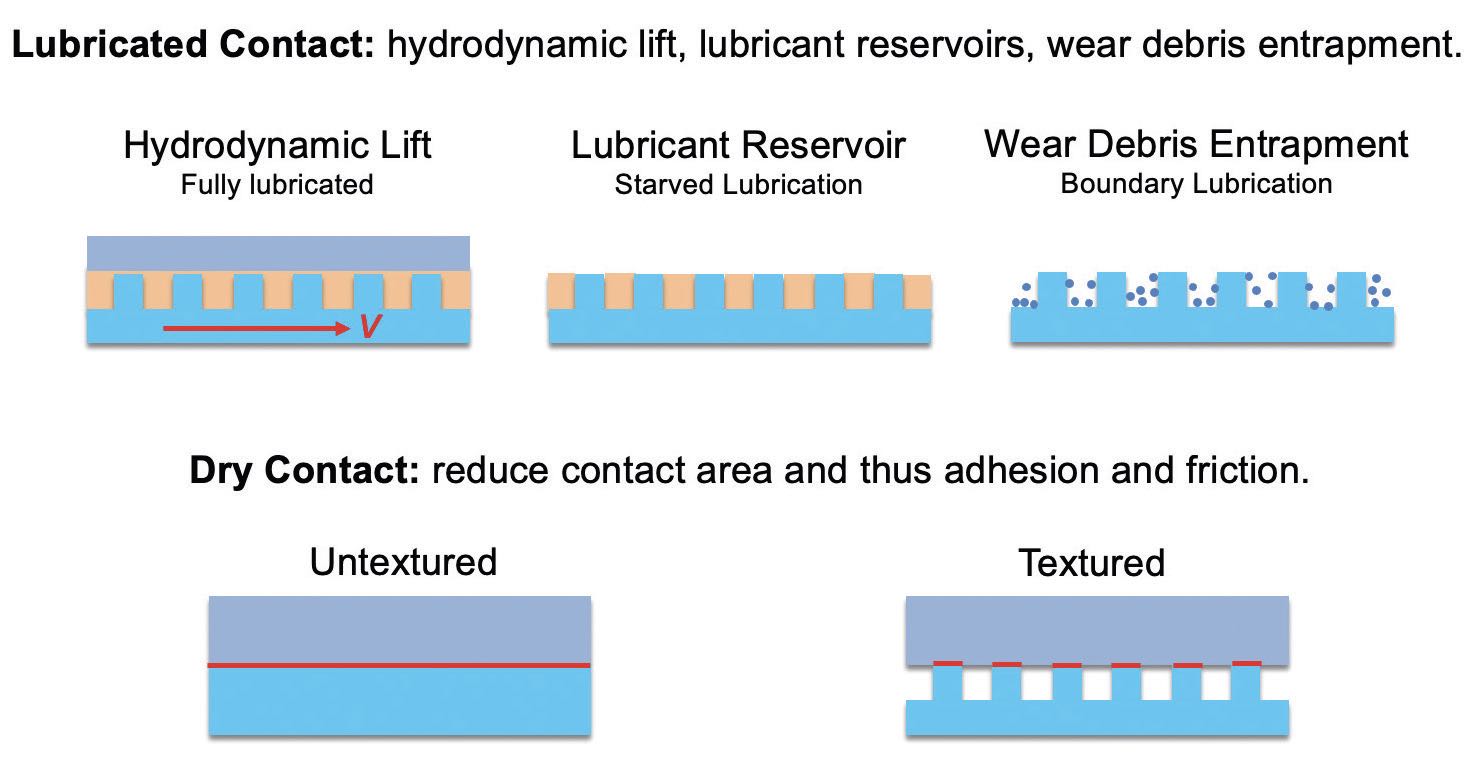
Figure 1. Engineered surfaces affect friction under lubricated and dry contact conditions. Figure courtesy of Min Zou.
Tire treads to micro-gears
Microscale surface textures serve a variety of functions in tribological applications. For example, lubricant stored in micron-scale crosshatch grooves on the surfaces of automotive engine cylinder liners helps to form a film over the entire surface, reducing friction when the piston ring passes against the bore. Micro-dimples on the surfaces of mechanical face seals and bearings perform in a similar manner, reducing friction by helping to form a continuous lubricant film.
For miniaturized devices, smaller textures are needed. For example, the high density of the recording area on a computer hard drive requires the read/write element on the recording head to be in close proximity to the disk. Microscale laser textured bumps on the disk landing zone have been used to reduce the contact area between the head and disk and, thus, adhesion and friction between them. On an even smaller scale, high surface forces come into play. Gears and other components of microelectromechanical systems (MEMS) and their nanoscale counterparts (NEMS) have a high surface-to-volume ratio
(see Figure 2). De vices with sliding interfaces rely on surface engineering to prevent adhesion, stiction and friction problems.
Figure 2. (a) Macroscale grooves or dimples can reduce friction for metal parts like car cylinder liners, (b) mechanical face seals or (c) MEMS devices. Figure 2a courtesy of Emok, CC BY-SA 4.0, via Wikimedia Commons. Figure 2b courtesy of Ma, C., Gu, W., Tu, Q. and Sun, J. (August 2016), “Experimental investigation on frictional property of mechanical seals with varying dimple diameter along the radial face,” Advances in Mechanical Engineering, 8 (8), DOI:10.1177/1687814016664837, CC BY 3.0, via ResearchGate. Figure 2c courtesy of Sandia National Laboratories, SUMMiT™ Technologies, https://www.sandia.gov/mesa/mems-video-image-gallery/.
Surface topographies at the micro- and nanoscales can be fabricated using lasers, photolithography, e-beam lithography or soft lithography (which uses elastomeric stamps, molds or conformable photomasks). Such techniques can be expensive and have limited shape control or flexibility. However, the development of 3D nanoprinting techniques has opened new avenues for surface topography engineering at these small scales. Bioinspired surface topographies, executed using 3D nanoprinting techniques, hold promise for producing a wide range of novel surface properties for traditional and new applications.
Key features provide key functionalities
Biological surfaces are complex. Their topographies and chemistries are complex, and they are made from heterogeneous materials. Duplicating these features and functionalities is extremely difficult. A better approach is to identify the features that are key to the desired functionality and then produce simplified structures that contain these features. Engineered surfaces also can combine features from different species or fine-tune fabrication processes to achieve properties not found in nature.
Making durable biomimetic surfaces presents another challenge. Durability is less important in biological organisms than in artificial materials because biological organisms can self-renew damaged surfaces. However, it is often easier to fabricate and apply surfaces that resist damage in the first place. For example, biomimetic surfaces based on the lotus leaf’s surface topography are superhydrophobic and self-cleaning, but they are easily damaged and not so easily repaired. On the other hand, seashells must stand up to water pressure, abrasion and impact stress to protect the soft organism inside. Their durable dome shapes distribute stress effectively, and their composite structures that alternate soft and hard layers give them both hardness and toughness.
Zou’s lab has fabricated deformation-resistant nanostructures with metallic or polymer cores, covered with hard amorphous shells, that mimic the domed shape and alternating layers of seashells
(see Figure 3). For example, nanostructures with soft aluminum cores and hard amorphous silicon shells resist deformation under much higher nanoindentation loads than those required to deform and fracture the core structures.
1,2 The structures also resist scratching with a diamond tip, even under high contact pressures, and they have a much lower coefficient of friction than core-only structures.
3,4 Fatigue tests show that the core-shell nanostructures maintain their shapes after 50,000 loading cycles under high contact pressures.
5 In contrast, the core-only structures show obvious denting after 10,000 loading cycles under a much lower contact pressure.
Figure 3. Fabricated core-shell nanostructures inspired by seashells resist friction, wear and deformation. Surfaces patterned with nanostructures having IP-DIP polymer cores and aluminum oxide shells have an 85% lower coefficient of friction than IP-DIP nanodots without the shells. Figure courtesy of Chris 73, CC BY-SA 3.0, via Wikimedia Commons (left) and Mahyar Afshar-Mohajer (right).
IP-DIP photoresist polymer, often used for 3D nanoprinting, forms the cores of similar dome-shaped nanostructures. Coating these cores with amorphous alumina shells helps them resist deformation and reduces friction along the nanostructured surface. The core-shell structures, made using 3D nanoprinting, show low friction and high resistance to deformation under more than 20 GPa of contact pressure. In contrast, nanostructures without hard shells are easily removed from the substrate or deformed.
6
Human articular cartilage, which covers the ends of bones where they come together to form joints, serves as the inspiration for orthopedic implant textures that increase lubricant film thickness
(see Figure 4). The surfaces of this cartilage feature microtextures of 20-50 μm in equivalent diameter and 0.5-2.0 μm in depth. Low spots in these textures store synovial fluid, which lubricates the joints. Zou and colleagues studied the ability of artificial surfaces with square, triangular and elliptical dimples to affect the thickness of a lubricant film (bovine serum in water) in artificial hip joints.
7 They used a pendulum hip simulator to mimic natural leg movements and measured changes in film thickness using a chromatic interferometer. They found that square- and triangular- shaped dimples provide significantly thicker lubricant films than flat surfaces do, and that surfaces with square dimples showed no visible wear.
Figure 4. Surface microtextures in human articular cartilage and orthopedic implants contain reservoirs for synovial fluid, which lubricates the contact zone between bones. Figure courtesy of Qiu, M., Chyr, A., Sanders, A.P. and Raeymaekers, B. (2014), “Designing prosthetic knee joints with bio-inspired bearing surfaces,” Tribology International, 77, pp. 106-110, doi: 10.1016/j.triboint.2014.04.025.
3D printing opens up new capabilities
Natural surfaces typically have 3D topographies that cannot be fabricated easily. Zou’s group has found that advanced 3D nanoprinting helps them to fabricate simplified versions of natural surfaces that mimic the 3D forms and functionalities of their natural inspirations. In one study, they fabricated truly 3D cone surface textures
(see Figure 5). They compared friction and wear on these surfaces with similar surfaces textured with 2.5D cylinders having the same tip or base diameters as the 3D cone structures.
8 (A cylinder is a 2.5D structure because it can be made by extruding a circle into a solid shape along a perpendicular axis. Truly 3D structures have cross-sections that vary with height.)
Figure 5. Truly 3D structures, whose crosssection varies along a third axis, reduce friction better than 2.5D structures with a constant cross-section. Figure adapted from Mahyar Afshar-Mohajer.
To fabricate the surface textures, Zou’s group used a Nanoscribe 3D nanoprinting system, which works with a variety of photosensitive polymers and substrate materials. The system uses a two-photon polymerization (2PP) process that selectively hardens photosensitive polymers at designated focal points. The 2PP process has a resolution of less than 200 nm, and its flexibility makes it easy to optimize shapes by changing designs. They also developed methods to perform
in situ tribological studies on their microtextured surfaces, which they observed using a camera for macroscale tests and a scanning electron microscope (SEM) for microscale tests.
They found that the tips of the truly 3D structures provide smaller contact areas, and, thus, less friction than 2.5D structures, resulting in smoother movement and less wear. What’s more, the wide bases of the 3D structures provided stability and resistance to shearing away from the substrate. When their 2.5D nanostructures buckled, they provided a sudden push to the counterface, resulting in negative friction.
Zou and colleagues also used 2PP to fabricate hexagonally arranged dimples connected by grooves, inspired by the hexagonally arranged grooved patterns on frog toes
(see Figure 6). This type of groove pattern can easily remove water from the frog toe surface to provide a drier, more adhesive contact. The synthetic patterns added dimples to enable a lubricant to spread more easily over the entire contacting surface and to retain the lubricant across the surface. The researchers compared tribological performance for various groove lengths, widths and depths. They then applied this texture to a piston liner and compared it with ideal crosshatched structures and industrial crosshatched structures.
9 Their best hexagonal texture reduced friction by 22% compared to a flat surface and 10% compared to the industrial crosshatched texture.
Figure 6. Surface structures inspired by frog toe skin contain dimples and grooves that act as lubricant reservoirs and channels in a piston liner. Figure courtesy of Shelby Maddox.
Reptiles, especially those found in sandy environments, also are masters of the low-friction textured surface. Their durable, scaly, slippery surfaces allow them to move easily across rough sand. The sandfish lizard, a well-studied type of skink, has skin with lower adhesion forces than polytetrafluoroethylene (e.g., Teflon
®). Zou’s group studied the ocellated skink, which has skin with a similar surface texture.
10 Ocellated skink skin reduces friction and wear using a hierarchical topography with a wavelike microtexture and nanoscale scalloping at the edge of each wave
(see Figure 7). The small size of the texture helps reduce wear by restricting stress buildup on the surface, thus reducing the need to release stress by forming large cracks. However, when stress reaches a certain point in the textured surfaces, microcracks form, releasing the stress in a controlled manner and providing locations where damage can accumulate. The result is cleaner cracks forming in the textured surfaces, compared with smooth surfaces.
Figure 7. Oscillated skink skin reduces friction on rough surfaces using a hierarchy of wavelike microtexture features with nanoscale scalloping at the edges. Figure courtesy of Julia Hoskins.
Lotus leaves are a well-known example of hierarchically structured surfaces with features on the micro- and nanoscales. These self-cleaning leaves repel water droplets using tapered micropapillae covered with short and long hairs. Zou’s group used 2PP to fabricate lotus leaf inspired synthetic structures, some with tapered micropillars and nanohairs and some with just the tapered micropillars
(see Figure 8). They conducted tribological testing of the textures using a flat diamond tip counterface inside an SEM to observe friction and deformation behavior.
11 The long nanohairs provided superhydrophibicity, but under high loads, they could collapse and cause the microstructures to deform. Shorter hairs did not collapse, and they helped to reduce the contact area, and, thus, the friction.
Figure 8. Fabricated surfaces with tapered micropillars and long nanohairs, inspired by a lotus leaf’s surface, show lotus leaf-like superhydrophobic behavior while, in the meantime, reducing friction better than micropillars alone. Figure courtesy of Mahyar Afshar-Mohajer.
Zou’s group also examined surfaces with arbitrary topographies.
12,13,14 They developed a process that uses 3D nanoprinting to fabricate surfaces that duplicate any type of topography
(see Figure 9). To create the patterns, they used a laser scanning confocal microscope to create 3D digital replicas of the original surfaces. So far, they have created high-fidelity replicas of the irregular surface textures of a banana peel, the eastern wahoo bush, daffodil petals and a speck of dust on a coin. Their replications of banana peel and daffodil petal surfaces, coated with a thin zinc oxide layer and lubrication, reduced friction by 42% compared to smooth surfaces.
Figure 9. Surface topography from nature can be imaged at a high resolution and converted to a computer-aided design (CAD) file for 3D printing, which directly replicates those surfaces for tribological and other applications. For example, replicated banana peel textures show low-friction properties. This approach also enables bioinspired surface topographies to be designed and printed to realize targeted surface properties. Figure courtesy of Min Zou.
Inspired by nature
Turning to nature for inspiration and technology for replicating natural surface topologies has proven to be an effective way to produce low-friction, wear-resistant surfaces. In many cases, these surfaces perform better than conventional engineered surfaces currently in use. In particular, 3D nanoprinting has made it possible to fabricate bioinspired surface structures with properties that are similar to—or better than—their natural counterparts.
Acknowledgments
Zou thanks the Center for Advanced Surface Engineering, Arkansas Research Alliance, National Science Foundation, Department of Energy, National Aeronautics and Space Administration, Oak Ridge Associated Universities, Arkansas Biosciences Institute, Arkansas Department of Higher Education, Ford Motor Co., Southwest Research Institute and Arkansas Economic Development Commission for funding support. She also thanks all the past and current Nanomechanics and Tribology Laboratory group members, especially Robert Fleming, Jason Steck, Josh Goss, Dipankar Choudhury, STLE member Mahyar Afshar-Mohajer, Shelby Maddox and Julia Hoskins, who provided data. Her collaborators include STLE Fellow Arup Gangopadhyay (Ford); STLE member Hamed Ghaednia (Gehring L.P., previously Ford); Henry Meng (University of Arkansas); David Rebenda, Pavel Hekrle and Martin Vrbka (Brno University of Technology); and Shinya Sasaki (Tokyo University of Science).
REFERENCES
1.
Tidwell, W., Scott, D., Wang, H., Fleming, R.A. and Zou, M. (2011), “Nanoindentation study of deformation-resistant Al/a-Si core–shell nanostructures,”
Acta Materialia, 59, pp. 6110-6. Available
here.
2.
Fleming, R.A. and Zou, M. (2017), “The effects of confined core volume on the mechanical behavior of Al/a-Si core-shell nanostructures.”
Acta Materialia, 128, pp. 149-159. Available
here.
3.
Morton, B.D., Wang, H., Fleming, R.A. and Zou, M. (2011), “Nanoscale surface engineering with deformation-resistant core–shell nanostructures.” Tribol Lett, 42, pp. 51-58. Available
here.
4.
Fleming, R.A. and Zou, M. (2016), “Nanostructure- textured surfaces with low friction and high deformation resistance,”
Tribology Transactions, 61 (1), pp. 80-87. Available at http://dx.doi.org/10.1080/10402004.2016.1274066.
5.
Steck, J.G., Fleming, R.A., Goss, J.A. and Zou, M. (2018), “Deformation and fatigue resistance of Al/a-Si core-shell nanostructures subjected to cyclic nanoindentation,”
Applied Surface Science, 433, pp. 617-626. Available
here.
6.
Steck, J.G., Afshar-Mohajer, M., Sun, Q., Meng, X. and Zou, M. (2019), “Fabrication and tribological characterization of deformation-resistant nano-textured surfaces produced by two-photon lithography and atomic layer deposition,”
Tribology International, 132, pp. 75-84. Available
here.
7.
Choudhury, D., Rebend, D., Sasaki, S., Hekrle, P., Vrbka, M. and Zou, M. (2018), “Enhanced lubricant film formation through micro-dimpled hard-on-hard artificial hip joint: An
in-situ observation of dimple shape effects,”
J. Mech. Behav. Biomed., 81, pp. 120-129. Available
here.
8.
Afshar-Mohajer, M. and Zou, M. (2020), “Multi-scale
in situ tribological studies of surfaces with 3D textures fabricated via two-photon lithography and replica molding,”
Advanced Materials Interfaces, 7 (13), pp. 2000299. Available
here.
9.
Maddox, S.R., Gangopadhyay, A., Ghaednia, H., Cai, J., Han, X., Meng, X., Goss, J.A. and Zou, M. (2021), “Fabrication and testing of bioinspired surface designs for friction reduction at the piston ring and liner interface,”
J. Tribol., 143 (5), 051109. Available
here.
10.
Hoskins, J.K. and Zou, M. (2021), “Designing a bioinspired surface for improved wear resistance and friction reduction,”
J. Tribol., 143, 051107. Available at
here.
11.
Afshar-Mohajer, M., Yang, X., Long, R. and Zou, M. (2022), “Understanding the friction and deformation behavior of micro/nano-hierarchical textures through
in-situ SEM observation and mechanics modeling,”
Tribology International, 165, 107271. Available
here.
12.
Maddox, S., Afshar-Mohajer, M. and Zou, M. (2020), “Digitization, replication, and modification of physical surfaces using two-photon lithography,”
J. Manuf. Proc., 54, pp. 180-189. Available
here.
13.
Maddox, S., Han, X., Meng, X. and Zou, M. (2020), “Fabrication and friction characteristics of arbitrary biosurfaces,”
Biointerphases, 15, 061016. Available
here.
14. Afshar-Mohajer, M., Goss, J., Choudhury, D., Zou, M. and Maddox, S. (2020), “Digitization and fabrication of custom surface topographies with submicron resolution,” U.S. Patent 10,875,248.
Nancy McGuire is a freelance writer based in Albuquerque, N.M. You can contact her at nmcguire@wordchemist.com.