HIGHLIGHTS
•
The complex nature of MWFs is leading to difficulty in understanding the basic types, applications and functions.
•
A review is provided about MWF applications, functions and types.
•
Key end-user operational issues that cover the complex nature of MWFs are discussed.
•
Global regulations are one of the important challenges that the MWF industry will continue to be facing in the future.
Most lubricants operate under specific methodologies that govern their composition and the requirements they must meet for specific applications. For example, passenger car engine oils must be formulated to meet the requirements of specific global specifications such as the ILSAC GF-6A and 6B in North America.
Metalworking fluids (MWFs) are needed to facilitate specific metalworking operations on a particular piece of metal known as a workpiece. There are a large number of operations and metal alloys that undergo metalworking where MWFs are required. For this reason, MWFs do not operate under the guidelines used by other lubricant types. Formulators must design specific MWFs that meet unique operating environments. In fact, there are circumstances where two machine tools conducting the same operation in the same plant may require different MWFs.
This challenge has made it difficult to understand what the basic types of MWFs are and what their applications and functions are. The purpose of this article is to make clear these points and also, from our perspective, present our viewpoints on key operational issues facing MWF end-users and future challenges.
Further information on the basic concepts discussed in this article can be found in the book, “Metalworking Fluids, 3rd Edition.”
1 This is a mandatory reference for all individuals working with MWFs.
Input on this article was obtained from the following members of the STLE MWF Education & Training Committee.
1.
Patrick Brutto, chair, Faith-Full MWF Consulting
2.
Jennifer Lunn, vice chair, JTM Products Inc.
3.
Ann Ball, Qualichem
4.
John Burke, Consultant
5.
Rick Butler, New Age Chemical
6.
Dr. Neil Canter, Chemical Solutions
7.
Dr. Alan Eachus, Consultant
8.
James Justice, John Deere
9.
Dr. Peter Küenzi, Blaser Swisslube
10.
Dr. Fred Passman, Biodeterioration Control Associates, Inc.
11.
Kevin Saunderson, BP Lubricants USA
12.
Dr. Don Smolenski, Strategic Management of Oil.
MWF APPLICATIONS
The first step in understanding the complexity of MWFs is to learn about their large number of applications that can be segmented into four categories: metal removal, metal forming, metal preventive and metal quenching.
Metal removal
The largest segment of MWF applications involves metal removal. In this application, metal is removed from a workpiece in the form of chips through the use of a cutting tool. A number of applications are used that can be divided into large chip and small chip removal. Examples of large chip and small chip operations are provided in Table 1.
Table 1. Examples of large chip and small chip metal-removal operations are shown. Table courtesy of the STLE MWF Education & Training Committee.
In large chip operations such as drilling, a significant amount of metal can be removed from the workpiece
(see Figure 1). For small chip operations such as grinding, very little metal is removed as the workpiece may be in the midst of a finishing operation where the metal surface needs to meet a specific parameter required by the end-user
(see Figure 2).
Figure 1. Twist drilling, an example of a metal-removal operation, involves the use of a tool known as a drill to remove metal from a workpiece with the removal of large chips. Figure courtesy of the STLE MWF Education & Training Committee.
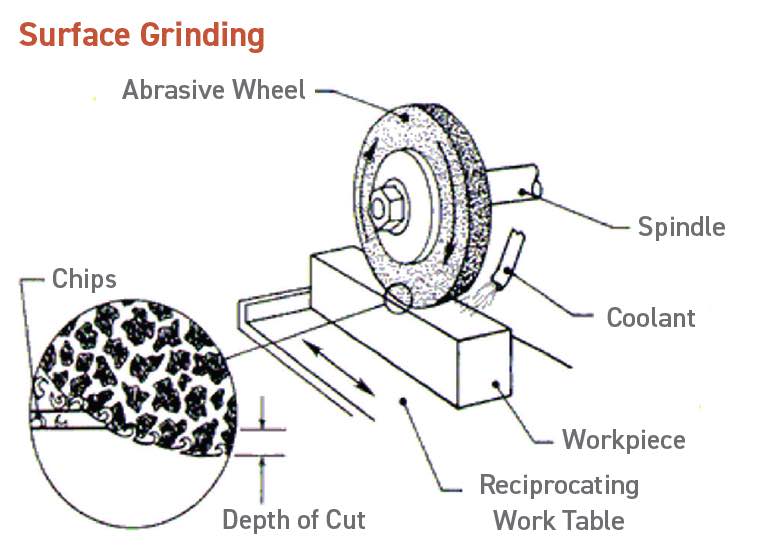
Figure 2. Small sized chips are removed in surface grinding. Figure courtesy of the STLE MWF Education & Training Committee.
Metal forming
In contrast to metal removal, minimal metal is removed when a workpiece undergoes a metal-forming operation. Instead, the shape of the workpiece is changed typically by putting it into a specific die. Metal-forming operations can be divided into six general types as shown in Table 2.
Table 2. The six general types of metal-forming operations are listed. Table courtesy of the STLE MWF Education & Training Committee.
Each of these metal-forming operations can be further subdivided into many related processes. Some operations change the shape of a small piece of metal while others are used on much larger workpieces. For example, cold heading is typically used to make small metal parts such as bolts and screws
(see Figure 3). In contrast, forging is a severe metal-forming operation where a large piece of metal is forced into the shape of a die as shown in Figure 4.
Figure 3. Small metal parts such as bolts and screws are typically produced through the metal-forming operation cold heading. Figure courtesy of the STLE MWF Education & Training Committee.
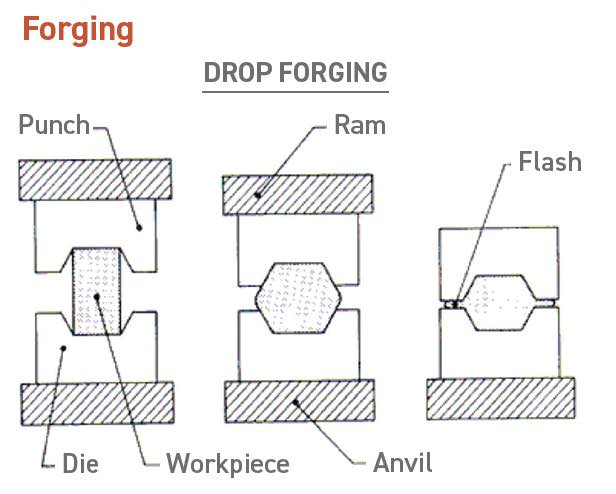
Figure 4. In the metal-forming operation forging, metal is forced into the shape of the die under severe conditions. Figure courtesy of the STLE MWF Education & Training Committee.
Metal preventive
Metal-preventive fluids are used to protect metal surfaces from corrosion on a temporary or a semi-permanent basis depending upon the process. They function by forming a protective coating on a metal surface that prevents oxygen and water from interacting with the specific metal part.
Temporary metal-preventive fluids are needed if a specific workpiece is transported from one manufacturing location to another for further processing. A more permanent metal-preventive fluid will be used to protect the metal used in a bridge, pier or dock.
Figure 5 shows that metal-preventive fluid can be formulated to provide protection from three weeks up to five years depending on the application.
Figure 5. Metal-preventive fluids act to protect metal surfaces from corrosion through formation of a protective coating. There are at least seven types of metal-preventive fluids that are formulated to provide corrosion protection ranging from three weeks up to five years. Figure courtesy of the STLE MWF Education & Training Committee.
Metal quenching
Metal is heated to high temperatures to help normalize it or relieve stress. The purpose of the former process is to adjust the hardness and ductility of a specific workpiece. To maintain the dimensional integrity of the metal, a controlled cooling process known as quenching is conducted, which also serves to develop desirable mechanical properties and microstructure.
A metal-quenching fluid is used to control the cooling process to achieve this objective. Most quenching is conducted on ferrous alloys and is segmented by temperature and rate (or speed) of cooling as shown in Figure 6.
Figure 6. Quenching is the cooling phase of heat treatment. Metal-quenching fluids help to control the dimensional integrity of a metal as it is cooled from high temperature to ambient temperature. Different types of quenching fluids are used based on operational temperature, rate of quenching speed (as measured by the GMQS – GM quench-o meter) and a form of quenching known as martempering. Figure courtesy of the STLE MWF Education & Training Committee.
MWF FUNCTIONS
The four types of MWFs exhibit different functions because each of the four applications have distinctive performance requirements.
For metal removal, an MWF must perform the following main functions.
•
Lubricity is required to minimize friction that can develop during the interaction between the workpiece and the cutting tool.
•
Cooling is important because significant heat can build up as the cutting tool encounters the workpiece. If no cooling occurs, then tool life and workpiece characteristics will be compromised.
•
Transport of chips away from the machining operation is necessary to ensure they do not compromise the cutting tool or the workpiece.
•
Corrosion protection is needed on a temporary basis particularly because machining can remove an oxide coating leaving bare metal exposed to oxygen and water, which can lead to negative issues such as rust and staining.
In metal forming, lubrication is an important issue but for a different reason. Sufficient lubrication must be present to reduce friction in order to ensure that the part can be produced. Corrosion protection is a second important characteristic for a metal- forming fluid because once an operation is completed, the workpiece may be placed in storage or transported to another manufacturing facility for further processing. The metal-forming fluid must act to prevent corrosion for up to several months.
Other functions that metal-forming fluids perform include:
•
Separation. The metal-forming fluid must keep the workpiece separated from the die either through a physical (through viscosity) or chemical mechanism to make sure the two components do not meet. This is necessary to ensure extended die life.
•
Cleanliness. This is another important function where a metal-forming fluid must minimize the build up of metal debris or fines on the die. This function extends to the fluid needing to be compatible with cleaners used on the metal part after the operation.
The primary function of a metal-preventive fluid is to provide corrosion protection in a specific application for the required timeframe. This characteristic may need to be adjusted so the metal-preventive fluid can provide protection in extreme environments such as the presence of acids and metal salts. Metal-preventive fluids also may be used in a dual function as, for example, a metal-forming fluid. In this capacity, they may need to exhibit lubricity and prevent welding of metal parts.
The main task for metal-quenching fluids was detailed in the previous section of this article.
MWF TYPES
The four main types of MWFs are straight oil, emulsifiable oil, semisynthetic fluid and synthetic fluid. The definitions for these fluid types are detailed in ASTM D2881,
2 Standard Classification for Metalworking Fluids and Related Materials.
Straight oil
This MWF type is prepared from a petroleum oil that can be formulated with specific additives to boost performance. No water is present, and the straight oil cannot be emulsified when exposed to water. In this regard, a straight oil has a similar appearance to other automotive and industrial lubricants that also are formulated with petroleum oils and suitable additives.
Emulsifiable oil
One of the major weaknesses of a straight oil used in MWF applications is inferior cooling properties. An emulsifiable oil is designed to combine the lubricity present in straight oils with cooling by being compatible with water. This is accomplished through including an additive type known as emulsifiers with other additives and petroleum oil in the formulation, which is known as the concentrate.
Once the concentrate is prepared and shipped to an end-user, the concentrate is added to water at a specific treat rate to produce a macroemulsion that has the appearance of milk
(see Figure 7). The opaque nature of the emulsion is created because the average size of the micelle is greater than one micron.
Figure 7. An emulsifiable oil concentrate is shown on the right, and once a specific treat rate is added to water, a macroemulsion is formed (as shown on the left), which is used in metalworking operations. Figure courtesy of the STLE MWF Education & Training Committee.
The original name for this MWF type is soluble oil, but this term is not reflective of the fluid because oil is not soluble in water. Emulsifiable oil is a better name because the finished fluid produces a macroemulsion.
Semisynthetic fluid
When the term semisynthetic fluid is discussed for conventional lubricant applications, the assumption is made that the lubricant contains two different base stocks. One is a petroleum oil, and the second one is a synthetic such as polyalphaolefin (PAO).
The semisynthetic MWF does not meet this definition. Due to the need for cooling, water is introduced as the second “base stock” to be used with petroleum oil in the semisynthetic fluid concentrate. Functional additives are compatible with petroleum oil, water or both base stocks and are added to provide the necessary performance for a specific application.
In a similar manner to an emulsifiable oil, the semisynthetic fluid is shipped to an end-user, and the concentrate is added to water at a specific concentration. The difference is that a semisynthetic fluid has the appearance of a microemulsion
(see Figure 8) with a translucent appearance that an individual can see through.
Figure 8. A semisynthetic fluid forms a translucent microemulsion (shown on the left) once the concentrate (shown on the right) is added at a specific treat rate to water. Figure courtesy of the STLE MWF Education & Training Committee.
Translucency is present because the average micelle size of a microemulsion is less than one micron.
Synthetic fluid
If the term synthetic fluid is raised with most tribologists, then the response will be that the fluid type is not formulated with a petroleum oil base stock. Instead, one of a number of base stocks (PAOs, esters, polyalkylene glycols and phosphate esters) is incorporated into a synthetic fluid. The primary synthetic fluid used in MWFs is not prepared with any of these base stocks. Rather, the primary base stock used in a synthetic MWF is water.
A synthetic fluid used in MWFs is prepared from water and functional additives. Most importantly, a synthetic fluid contains no petroleum oil
(see Figure 9). This concentrate is a single-phase true solution that contains no micelles. The appearance of a synthetic fluid looks similar to that of a glass of water. An individual can see completely through it.
Figure 9. A solution synthetic fluid is the most widely used synthetic fluid where the primary base stock is water. Figure courtesy of New Age Chemical.
This type of synthetic fluid is known as a solution synthetic fluid. There are two other types of synthetic fluids known as an emulsion synthetic fluid and a straight synthetic oil.
An emulsion synthetic fluid is similar to an emulsifiable oil except that a synthetic base stock such as PAO is used with functional additives in the concentrate. No petroleum oil is present. Further dilution with water is done prior to use and generates typically a macroemulsion.
A synthetic base stock also can be formulated with functional additives into a straight synthetic oil. No petroleum oil and no water are present in this MWF type. Base stocks that can be used include esters, synthetic hydrocarbons and vegetable oils.
The tradeoff between lubricity and cooling for the four MWF types is shown in Figure 10. Straight oils and true solution synthetic fluids demonstrate the best performance at the extremes of lubricity and cooling, respectively. The MWF types forming emulsions (emulsifiable oil, semisynthetic fluid and emulsion synthetic fluid) offer the best compromise between lubricity and cooling making them more attractive for use by end-users.
Figure 10. Selection of one of the four MWF types is based on their ability to provide lubricity and cooling. As shown, there is a tradeoff between lubricity and cooling. The best compromise can be found with emulsifiable oils and semisynthetic fluids. Figure courtesy of the STLE MWF Education & Training Committee.
Besides the base stocks, MWFs are formulated with a large number of functional additive types that can be used with one or more fluid types. Figure 11 lists 13 specific additive types that can be used by a formulator in MWFs. Further complicating MWF formulations is that more than one of any of the additive types can be used in a specific fluid. This means that the number of components in a MWF can reach 20 or more.
Figure 11. MWFs are prepared from complex formulations that may include all of the 13 additive types shown. Figure courtesy of Chemical Solutions.
KEY END-USER OPERATIONAL ISSUES
STLE member Ann Ball, regulatory affairs manager for Qualichem in Salem, Va., highlights three issues. She says, “Almost universally, the key operational issue facing MWF users is one of human resources. Maintenance departments, frequently tasked with fluid maintenance, are often understaffed and/or lack proper training for this responsibility. End-users understand the importance of fluid maintenance but lack the time and may not be getting sufficient support and training from their suppliers.”
To overcome this problem, Ball indicates that end-users are turning more to their suppliers for training and support. She adds, based on comments from her colleagues, “Forward thinking companies are looking to automate as much of the maintenance process as possible to overcome the lack of personnel. Centralized coolant distribution systems are becoming more common. This trend is taking place even in smaller machine shops that historically have been averse to spending money on fluid maintenance.”
STLE member John Burke, consultant in Concord Township, Ohio, lists price increases, lack of understanding of why MWFs fail, methods to optimize MWF to extend their useful life, lack of timely field support from MWF suppliers and the delay in data turnaround (usually about one week) as five issues facing end-users.
He says, “Overcoming these operational issues can be accomplished through the use of remote monitoring and control systems, to assist in minimizing product consumption.”
STLE member Rick Butler, director of technology at New Age Chemical in Delafield, Wisc., feels that end-users have trouble maintaining MWF concentrations within upper and lower control limits. He says, “This also is leading to trouble with keeping microbial growth at 1,000 colonies per milliliter or less particularly with emulsifiable oils and high oil semisynthetic fluids.”
Butler believes that end-users must recognize that microbial growth is a significant issue because it can enhance corrosion. End-users need to be willing to treat high microbial growth tankside if necessary and recognize that spent MWF must be replaced eventually.
STLE Life Member Dr. Alan Eachus, consultant in Plantation, Fla., indicates that supply chain problems are a key problem facing end-users. He says, “Supply problems with key ingredients are making it difficult for end-users to obtain their desired MWFs. Adding to the issue are transportation problems that are delaying concentrate shipments. End-users need to maintain sufficient inventories and also develop alternatives to overcome these supply chain issues.”
The supply issues have led to an increase in fluid costs, which makes it imperative for end-users to practice better fluid maintenance. Eachus adds, “Experienced workers have been leaving end-user-companies to take retirement particularly since the onset of the COVID-19 pandemic. End-users need to partner with trade schools to expedite the identification of suitable replacement personnel and also need to enhance in-house training programs.”
STLE member James Justice, senior engineer at John Deere in Waterloo, Iowa, expressed concern that end-users treat MWFs as commodities and give little thought to the synergistic system that they “live” in with filtration, tooling and other components. He says, “Beyond pricing, logistics, environmental health and safety/ compliance and quality, typically little thought is given to the impacts of a specific MWF in a system. A true understanding of the total cost of ownership and how improvements to technology and management of MWFs impact many other aspects of manufacturing is both an issue and an opportunity. Awareness and education would be some of the first steps. In addition, generating the tools to communicate these messages to end-users is required.” Supply chain problems are a key problem facing end-users.
STLE member Dr. Peter Küenzi, microbiologist at Blaser Swisslube AG in Hasle-Rüegsaw, Switzerland, feels that end-users lack the understanding about the link between bacteria in the planktonic phase (present in the fluid) and in biofilms. Figure 12 shows how bacteria in both environments interact producing a vicious cycle that prevents an end-user from minimizing microbial contamination.
Figure 12. Dr. Peter Küenzi thinks that microbial contamination is a cyclical process that can quickly get out of control if inadequate measures are taken. It is nearly impossible to remove biofilm from the surfaces of MWFs by just using biocides and cleaners. Metalworking systems often show no signs of microorganisms in the liquid, although microbes start to colonize on system surfaces and form so-called biofilms (a). Since only the liquid is analyzed, these biofilms remain unnoticed. As the MWF is used, biofilms may spread, and the coolant is then colonized by planktonic (freely swimming) microorganisms. As there are no early warning systems in place, both phenomena often go unnoticed (b). Operational problems, however, prompt the end-user to analyze the MWF, while the root cause (the biofilm) remains undetected (c), which is why biocides are often added to control the situation. While planktonic organisms are often eliminated, biofilms are only reduced, and the survivors remain in the system (d). Surfaces are seldom cleaned, thus biofilms regrow (e). As soon as biocide additions stop or the microorganisms even develop resistance to the biocides used, this leads to worsening of the situation as these organisms also recolonize the fluid, but can now no longer be killed by the same biocide. This results in the so-called sawtooth curves where detectable colonization of the coolant alternates with additions of biocide and system cleaners. As long as the surfaces are not thoroughly cleaned, the cycle will start all over again at (a). One possible way out of the dilemma besides regular cleaning is to alternate the use of differently designed MWFs, which provide different ecological environments so that the microorganisms have to adapt again and again before spreading. Figure courtesy of Blaser Swisslube AG.
He says, “End-users misuse biocides in all kinds of situations by considering them to be the answer in the case of operational issues instead of going through a detailed root cause analysis. At the same time, prevention is delegated directly and exclusively to MWF suppliers. Another concern is that end-users misunderstand the importance of molds in systems, leading (often) to wrong conclusions and useless measures.”
Küenzi sees the need for personnel to be trained to perform thorough onsite analyses and to resolve operational problems by thinking outside the box.
The No. 1 complaint that STLE member Jennifer Lunn, senior chemist at JTM Products in Solon, Ohio, receives from end-users is the presence of foam in systems that run under high pressure and use smaller sumps. She says, “Throughthe- tool delivery is a big contributor to foaming as well as the smaller sumps not allowing adequate downtime for foam to dissipate before being recirculated through the systems. Defoamers/antifoams are obviously a great way to alleviate foaming; however, they can be removed from the fluid by certain filters or be detrimental to downstream operations. There are specific defoamers that will eliminate downstream issues; however, they rarely work as well.”
Lunn believes that careful selection of specific additives also can be helpful in alleviating foaming. She says, “Formulators can evaluate and use emulsifiers that are naturally low foaming. Using self-emulsifying esters for lubricity can decrease or even eliminate reliance on mineral oil and therefore emulsifiers, producing lower foaming fluids.”
Besides carrying out an active MWF maintenance program to reduce fluid usage and costs, Lunn advocates purchasing a higher quality MWF that may cost more per gallon but will last longer resulting in an overall lower cost over time.
STLE member Dr. Fred Passman, president of Biodeterioration Control Associates, Inc. in Princeton, N.J., considers the challenge for formulators and end-users to identify MWFs that are suitable for the new metal alloys that are now in use to be a key operational issue. He says, “Optimizing production of parts made from new alloys with different hardness and malleability properties compared to traditional alloys will require formulators and end-users to collaborate in lab and field testing of MWF candidates to meet performance objectives.”
STLE member Kevin Saunderson, senior technologist at BP Lubricants USA in Chicago, Ill., states that the challenge for end-users is to consistently manage in-use MWFs to avoid production downtime that may be caused by corrosion, foam, microbial contamination or tool wear due to insufficient cooling and lubrication. He says, “Selection of the proper fluid by keeping in mind the severity of the operation and the type of metal machined is the first step in avoiding these issues. During use, the fluid needs a consistent and comprehensive condition monitoring program to allow the end-user or fluid manager the ability to anticipate any potential issues so they can apply the appropriate corrective action as needed.”
Careful selection of specific additives also can be helpful in alleviating foaming.
FUTURE CHALLENGES
The complex issues facing MWF raw material suppliers, formulators and end-users means that there are significant future challenges that will need to be overcome.
STLE member Patrick Brutto, scientist: metalworking fluids at Faith-Full MWF Consulting in Bloomingdale, Ill., lists the following four future challenges facing the use of MWFs.
•
Complying with the performance and sustainability/life cycle requirements, especially of large global end-users
•
Business sustainability issues associated with declining metal-removal fluid volumes as electric vehicle motors replace internal combustion engine powered vehicles
•
Attracting new talent to a declining market
•
Meeting the most challenging lubricity requirements, in the event all chlorinated paraffins are banned due to persistent, bioaccumulative and toxic (PBT) issues.
STLE member Dr. Don Smolenski, president, Strategic Management of Oil in St. Clair Shores, Mich., focuses on sustainability as a key issue that will become increasingly important in influencing the selection of MWFs. He says, “Linked to sustainability and MWF selection is the growing trend for recycling. End-users have successfully implemented such programs in the past, which involved segregation of different use streams. This strategy must continue into the future to maximize MWF productivity and minimize emissions.”
Justice feels that end-users will focus on manufacturing of metal parts but will, unfortunately, allow management/understanding of chemical systems to fall by the wayside. He says, “I foresee automated system management seeing considerable growth over the next decade as end-users will continue to be with labor constraints in reference to factory operations. The motivation is the need for manufacturing to be conducted and managed even if there is not an overwhelming business case, from an ROI standpoint, to develop and implement automation.”
Justice also considers compliance with global regulations from organizations such as ECHA (REACH), OSHA and EPA as continuing to be ongoing issues that end-users will continue to have to deal with as they keep their operations moving forward.
Saunderson indicates that global regulations will affect the formulator’s ability to prepare future products to meet industry needs. He says, “Formulating challenges will exist due to new or pending regulatory requirements that may eliminate or significantly curtail the use of proven and cost-effective chemistries. Ongoing supply chain volatility will continue to impact how MWFs are formulated and ultimately influence their availability and cost to the end-user.”
Passman focuses on the increasing challenge that formulators will have in formulating biostable but readily biodegradable MWFs. He says, “Finding (using) and formulating MWFs that meet both green and performance goals as the list of regulatory agency-approved functional products shrinks will become increasingly difficult. As the list of approved microbicides shrinks, it will be a challenge to replace them with additives that are less toxic than FIFRA-registered products they are replacing. Formulators and end-users will need to collaborate to agree on performance and environmental fate and persistent objectives.”
Küenzi agrees, “Designing MWFs that are both stable during use, but easily degraded once they need to be disposed, is a current and future challenge that the formulators and end-users will continue to have to address.”
The multidimensional nature of MWFs is cited by Ball as a challenge that an end-user needs to meet in multiple business disciplines. She says, “The environmental, health and safety (EHS) staff will face the need to stay compliant with an ever-growing list of regulations, foreign and domestic. Maintenance will continue needing to do more with less and somehow find the time to keep fluids in good operating condition. Operations will be challenged to keep fluids in tune with the almost ubiquitous use of high-pressure delivery, recycling and filtration systems. Programmers will be pushed to simultaneously apply multi-axis technology on difficult materials with coolant through tooling, balanced against MWF supply no greater than it was 30 years ago.”
Lunn cites four specific challenges that the end-users will face into the future. She says, “Formulators will need to assist end-users by providing products that last longer and produce less waste. Training to help end-users maintain their systems for longer periods of time also is important to reducing waste. These approaches can be combined with the introduction of sustainable additives and base stocks based on renewable resources such as vegetable oils. These additives and base stocks decrease dependency on mineral oils while providing outstanding performance and extending MWF operating life if properly maintained/formulated.”
Regulations will continue to be a constant challenge that will prompt formulators to find smart, innovative strategies for developing new sustainable products to replace older ones. Lunn says, “The need for new MWFs can become more challenging as fewer raw material options are available and end-users face the need to machine new metals/alloys to meet new vehicle designs.”
The increasing number of regulations that forbid the continuing use of previously- available functional groups is a continuing challenge for MWF formulators according to Eachus. He says, “Formulators need to maintain awareness of changing regulations and try to anticipate where possible in order to develop alternative fluids. One example is the increasing pressure on the acceptability and availability of hydrocarbon- based MWFs, which is leading formulators to look to petroleum-free products.”
Two of the key operational issues that Burke previously claimed (price increases and lack of field support by some MWF product suppliers) will continue to be future challenges. In addition, Burke sees the loss of specific MWF functional additives and the growing production of electric vehicles as future concerns. He says, “Two classes of additives that will be unavailable to MWF formulators in the future will be certain extreme pressure (EP) additives based on chlorine and phosphorus and the loss of certain biocides (such as hexahydrotriazine). Electric vehicle production will lead to a reduction in demand for MWFs in the automotive market.”
Butler predicts that waste treatment of MWFs will become more of an issue for end-users in the future because of growing concerns from smaller towns where manufacturing plants are situated. He says, “This trend will eventually force smaller end-users to start having wastewater hauled away increasing disposal costs. Synthetic MWFs, if kept clean of tramp oil and well maintained, can last for years minimizing water generation issues. Emulsifiable and semisynthetic fluids cannot provide this durability as both fluid types will exhibit sump lives of one year maximum.”
Waste haulers also are becoming more demanding about whether they will accept MWFs. Butler continues, “Effluent streams containing MWFs formulated with chlorinated paraffins will only be acceptable to waste haulers if the very long chain (vLCCP) type is present.”
In summary, the basics of MWFs need to be better grasped to better understand key operational issues and future challenges. As noted in this article, there are many concerns that the industry must address now and in the future.
REFERENCES
1.
Byers, J. (Ed.) (2018),
Metalworking Fluids, 3rd Edition, CRC Press: Boca Raton, Fla.
2.
ASTM D2881:
www.astm.org/d2881-19.html
The STLE MWF Education & Training Committee is responsible for providing pertinent courses and education activity for STLE programming, including at the STLE Annual Meeting. Any questions about STLE MWF educational offerings can be directed to Pat Brutto, chair, at patrick.e.brutto@gmail.com or Jennifer Lunn, vice chair, at jlunn@jtmproducts.com.