TLT: How long have you worked in a lubrication-related field, and how did you decide to pursue a career in the lubricants industry?
Barraclough: I have worked in the lubrication industry for 26 years and started out as a senior research assistant at the University of Wales Swansea under the expert tutorship of Dr. Brian Roylance and Mervyn Jones. During this time, I worked on various Ministry of Defense sponsored research programs to develop wear debris analysis procedures using wear particle morphology to detect the early onset of failures in the C-130 Hercules turboprop and Tornado RB199 turbofan jet engine systems
(see Figures 1 and 2). The goal of the project was to remove some of the subjectiveness out of the microscopy analysis of the wear debris collected from the magnetic plugs in these engines and replace it with a simplified computerized expert imaging system. The wear debris pulled from aircraft lubrication systems is a mixture of benign and severe wear particles and is extremely difficult to distinguish with an untrained eye. This software was then installed and used as an additional tool to assist ground technicians at the RAF Early Failure Detection Centers (EFDCs) with very little to no knowledge of wear particle analysis.
Figure 1. Tornado RB199 engine. Figure courtesy of Nimbus227, CC BY-SA 4.0, via Wikimedia Commons.
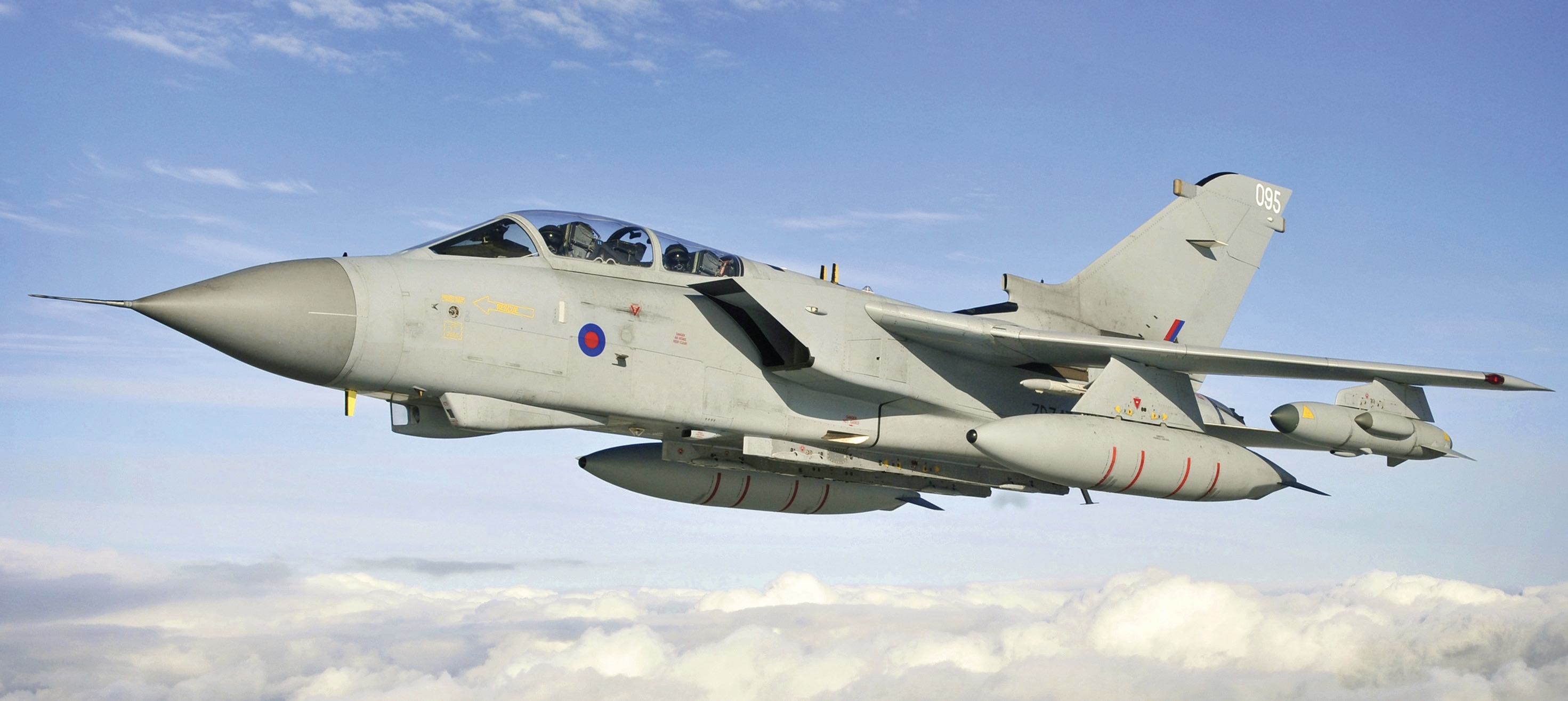
Figure 2. RAF Tornado GR4. Figure courtesy of Corporal Mike Jones/MOD.
Later in my career at Swansea I began work on a contract sponsored by the Office of Naval Research in partnership with the Naval Research Laboratory (NRL) in Washington D.C. This project involved providing digital wear particle images to develop the wear particle shape classifier used in a direct imaging system
(see Figure 3). Utilizing the various test rigs available in the university’s tribology department, we were able to synthetically simulate different wear modes and mechanisms up to failure and subsequently collect and image the wear particles from the lubricating oil. These images would form the basis of the training set for the neural net wear particle expert shape classification system in a particle counter and shape classifier. In 1999 I presented much of my work at the STLE Annual Meeting in Las Vegas, Nev. During this conference I had the privilege to meet and discuss my work with Dan Anderson, one of the most renowned and respected oil analysis experts in this field. Anderson was one of the pioneers of ferrography and had authored the Wear Particle Atlas. Luckily for me I made an impression, and soon afterward Spectro offered me my first job working for a private company as an applications engineer. I packed my bags a few months later and left the shores of Swansea for the East Coast of the U.S. to embark on the next stage of my career, working in the oil analysis commercial analytical instrumentation division. Little did I know then that 26 years later I would be working for the same company as technical director as a U.S. citizen with a wife and family!
Figure 3. A wear particle image classifier: wear classifications. Figure courtesy of Ametek Spectro Scientific.
TLT: What has been your most rewarding accomplishment throughout your career in the lubricants industry?
Barraclough: During my career, I have had many rewarding accomplishments. I have been named a co-contributor on five patents and a primary contributor on two patents on various new and innovative technologies used in analytical instrumentation for the oil condition monitoring field. Developing new and innovative technology takes a large collaborative effort and teamwork across all the engineering disciplines. As anyone who works in R&D knows, getting to the final working design that meets your desired performance specifications can be a long road that results in failure many times over before the solution to the problem is found, which makes finally getting to the solution so rewarding. I was granted the filtration particle quantifier (FPQ) patent in November 2015
(see Figure 4). On reflection this was by far the most challenging technical project I have undertaken. This project involved designing a solvent-free, field portable pore blockage particle counter that can count particles accurately for a wide range of fluid types and concentrations across multiple oil analysis applications. The development of this technology took many years of engineering iterations, testing and refinement to reach the desired performance requirements initially set out. Since being granted the patent on this technology, the FPQ product has further matured and is now a staple component in the company’s field portable product line.
Figure 4. Filtration particle quantifier, solvent-free pore blockage particle counter. Figure courtesy of Ametek Spectro Scientific.
TLT: What is the No. 1 piece of advice you would give to a person who might be interested in starting a career in the lubricants industry?
Barraclough: Firstly, from a technical standpoint, the tribology/lubrication industry is a vast sphere that encompasses the study of many different facets of lubrication friction and wear. I know from personal experience that it can be very overwhelming at first for those starting a new technical career in this field. My advice, if you are just beginning your journey in the lubrication industry, would be to start by finding a niche within this field that really interests you, then research it as much as possible by studying all the past literature and technical publications documented on the subject. From here you can begin to call yourself a subject matter expert and expand upon the technical evolution with your own experimental research, thoughts and findings. This will undoubtably lead to the continuation of new innovations and discovery in your subject field.
Secondly, I think it’s very important in any career field to forge professional relationships in your workplace with your peers to help further your career. I never want to lose sight of the fact that over the years I have had the privilege to have worked with and been mentored by some very knowledgeable experts in and around my field and forged some great relationships along the way on both a personal and technical level. This has unequivocally helped me progress in my career.
TLT: Throughout the different segments within your career, which one has been the most interesting, challenging and/or rewarding?
Barraclough: One of the most interesting and challenging segments of my career has been the ongoing development of liquid- and solid-based instrument-specific verification check standards—and the subsequent transition of this into a small-scale commercial blending operation.
In-service oils being tested are generally not clean, and they will often contain contamination such as water, fibers or an immiscible fluid, which can foul up an instrument, clog a flow cell and cause erroneous results unbeknown to the operator. Due to the inability to source various types of standards comprising particulate analyte, it has become a necessity to formulate these ourselves to ensure customers can continually check the integrity of their instruments.
I started this work by seeing if I could blend some of these standards myself into small batches to use in house as simple instrument check fluids. This used unique analytes such as a dissolved ferule fluid and ferrous spheres for a ferrous verification fluid, elemental nanoparticles in epoxy for an X-ray fluorescence solid verification sample and finally using unique properties within blended fluid additives for infrared detection and viscosity verification. In addition, I looked at multi-instrument analyte blending into a single standard for convenience for field users. Some portable instruments can have up to four instruments in a device that need to be verified in the field. After the initial developmental period, it was demonstrated that this could all be accomplished on a relatively small scale. To ramp up production and to meet the demand for verification fluids, a small-scale blending lab needed to be built in the company to house the entire operation
(see Figure 5). This would pose many challenges not anticipated along the way! The biggest challenge was the space limitation and access to the building ventilation system required to install a walk-in fume hood and to house a 55-gallon drum of oil, floor scale and mixing apparatus. In addition to this, the walk-in fume hood needed to be housed in a custom-built clean room to maintain the ISO cleanliness levels required for particle count standards. This quickly turned into quite the project and challenge on a tight timeline and budget. I became my own general contractor and was scheduling HVAC technicians, electricians and making sure we met fire regulations, safety and building codes, etc. The project was completed on time, in only a few months and now supplies over 20 unique solid and liquid verification standards and flushing fluids to all of our oil analysis customers to help ensure their instruments are properly calibrated, serviced and maintained.
Figure 5. Custom built blending lab clean room with walk-in fume hood. Figure courtesy of Ametek Spectro Scientific.
TLT: What are some of the most important technical lubrication-based concepts or topics you have encountered throughout your career?
Barraclough: Large wear particles coupled with dynamic equilibrium, although not intuitively obvious, is a critical concept for the equipment owner to understand in order to predict when an abnormal wear event is occurring and set appropriate limits. Large wear particles need to be tracked closely because they are predominantly the first signs of an increasing wear rate and abnormal wear mode in a machine
(see Figure 6). The fundamental premise of machine condition monitoring by wear particle analysis is that an abnormal wear mode causes an increase in the size and concentration of wear particles above a previously defined baseline.
Figure 6. Abnormal machine state; large sliding wear 20-25 microns limit exceeded. Figure courtesy of Ametek Spectro Scientific.
Extensive work on dynamic equilibrium models of wear particles was undertaken during the early 1980s to better help analytical ferrography analysts identify abnormal wear using optical microscopy. It was demonstrated how particles reach an equilibrium concentration by summing a geometric series based upon particle production and decay for a constant wear rate and given size. During passage of oil through a closed loop system, it is assumed there are various mechanisms for the removal of particles such as filtration and particle settling. What this means is that the concentration of very fine and dissolved wear debris will continue to rise until the oil is changed. This is because they are never really lost in the lubrication system, and only the detection of an increase in wear rate can identify real changes in the overall machine’s condition. On the flip side, the larger more important severe wear particles will be removed mainly by settling or filtration as the lubrication system cycles and the concentration of these particles will slowly build to a dynamic equilibrium state as soon as the wear rate equals the loss rate.
The practical consequence of dynamic equilibrium is that if samples are taken periodically from a normally running machine, the concentration and size distribution of the wear particles should be more or less the same.
Understanding this concept is critical to setting the right alarm levels to monitor the large abnormal particles in a machine.
You can reach Tom Barraclough at thomas.barraclough@ametek.com.