TLT: How did you get involved in this field?
Nyman: I’ve always found oil and machines very interesting and worked on my mopeds and motorcycles since the age of 15.
The interest steered me toward studying mechanical engineering, and I finished my bachelor degree in 1996. My first job was at Alfa Laval within technical sales support, and it was during these 3.5 years I discovered that training was my calling. The most interesting days were when I assisted colleagues and conducted training, so in February 2000 I devoted all my time to education and started at the Poul Due Jensen Academy with Grundfos. I really enjoyed the years with the Grundfos team, where I also got the education as 4MAT trainer in adult teaching skills.
An opportunity to combine my passion for oils, machines and training arose in the summer of 2004, and I started working for C.C.JENSEN Filtration Systems, responsible for developing and conducting technical training and documentation for sales, service and technical staff. The job included training of their subsidiaries and distributors worldwide, so during the last 18 years I have seen many countries.
I was stationed in Georgia, U.S., for C.C.JENSEN from December 2010 to December 2012, which gave me the possibility to participate in courses and serve as co-trainer for Noria Corp., becoming their partner in Denmark from 2013. I’m a certified International Council for Machinery Lubrication (ICML) Level II Machinery Lubrication Technician (MLT II) and Level II Machinery Lubrication Analyst (MLA II).
TLT: What are your most rewarding experiences throughout your career in the lubricants industry?
Nyman: Sharing knowledge with technical peers, e.g., during events like the Oil-Doc Conference & Exhibition and Reliable Plant Conference & Exhibition, gives me great pleasure—also, when I experience participants “growing” during a training course, and afterward in their jobs, because they understand the benefits of oil maintenance.
Steffen D. Nyman in action training customers.
TLT: What aspects of oil maintenance do you think are critical but are mostly forgotten?
Nyman: Everyone talks about saving energy and switching to renewable sources but forgets the fact that maintenance is the easiest way to prolong oil life and, thus, reduce our carbon footprint. Solar, wind, electric cars, etc., are, of course, important steps toward a cleaner world, but replacing oil in machineries every 200 operation hours due to contamination is simply a waste of resources. Most lubricants can be in service many thousands of hours if properly maintained. Longer oil and component life will yield so much savings with in manufacturing, transportation and maintenance of machines. Proper maintenance and filtration of oil, e.g., in cement and mining industries, will reduce the need for oil changes by 75% and for new mechanical spare parts by 60%. This will result in huge CO
2 savings
(see Figure 1)!
Figure 1. CO2 reduction using filtration. Figure courtesy of C.C.JENSEN.
TLT: What aspect of oil maintenance do you think is given more weight than is relevant?
Nyman: Inductively coupled plasma (ICP) element analysis is an important tool to monitor wear and additives in used oil, but most people don’t understand the technology completely, which can result in misinterpretations. The ICP technology mostly measures elements below 3 microns and is completely blind to particles larger than 5 microns, meaning all issues cannot be detected. A severe wear situation on a gear (e.g., adhesive wear) will create particles much larger than 5 microns, but these will not be measured initially if only ICP is used. In this case particle counting and particle quantification (PQ) index or ferrous density wear particle concentration (WPC) analysis are needed. Furthermore, it is important to understand that the ICP element analysis cannot distinguish between an active working additive and a depleted one. Zincdithiophosphate (ZDDP) will show as zinc (Zn) and phosphorous (P) in the ICP analysis, both when the antiwear additive is active but also when the ZDDP molecules are latched onto iron wear particles floating in the oil. The ZDDP is then not active anymore and not ready to help create an antiwear carpet on machine surfaces. The ICP result will, however, still measure Zn and P as if the ZDDP additive was there, which gives a faulty reading on highly contaminated lubricants. The true amount of polar additives may not be as high as you think, looking at the ICP analysis results. This also has resulted in the misunderstanding that fine filtration of oil will remove all additives—which is definitely not the case.
TLT: Why focus on oil maintenance to improve reliability?
Nyman: The primary objective of keeping oil clean in a hydraulic or lubrication system is to protect machine components in order to optimize reliability and function, as the cost of a breakdown and loss of availability is very high. Malfunction of a gear or hydraulic system will result in consequential damages, expensive downtime or even safety concerns.
The secondary objective is to reduce operation costs by prolonging the useful life of all system components, as well as the oil itself, to ensure optimum economic performance and lowest return on investment (ROI). In most oil systems, you’ll find silt size particles between 1-10 microns, with 1 micron (μm) equaling 1/1,000 of a millimeter. In comparison, a human hair has a diameter of 70 μm. Most particles are invisible to the naked eye but can enter the oil system in large numbers via system openings, e.g., shaft seals and inadequate air vents/breathers.
Airborne particles are highly abrasive, as they get trapped in the oil film clearances in between gear teeth, valve plungers and housings or between the piston and cylinder in a piston pump. The result is abrasive wear, known as seizing or grinding, which can generate wear rates a thousand times greater than that anticipated by the machine manufacturer.
The same applies to the combustion of diesel and gas oil, where impurities in the form of particles and water accelerate wear on the fuel pump, needle valves in injectors and other components in the fuel system. Modern common rail diesel engines with high injection pressures have very fine tolerances, typically 2-5 μm, so very clean diesel is required to get reliable operation and avoid costly downtime. Oil maintenance can vastly improve reliability
(see Figure 2).
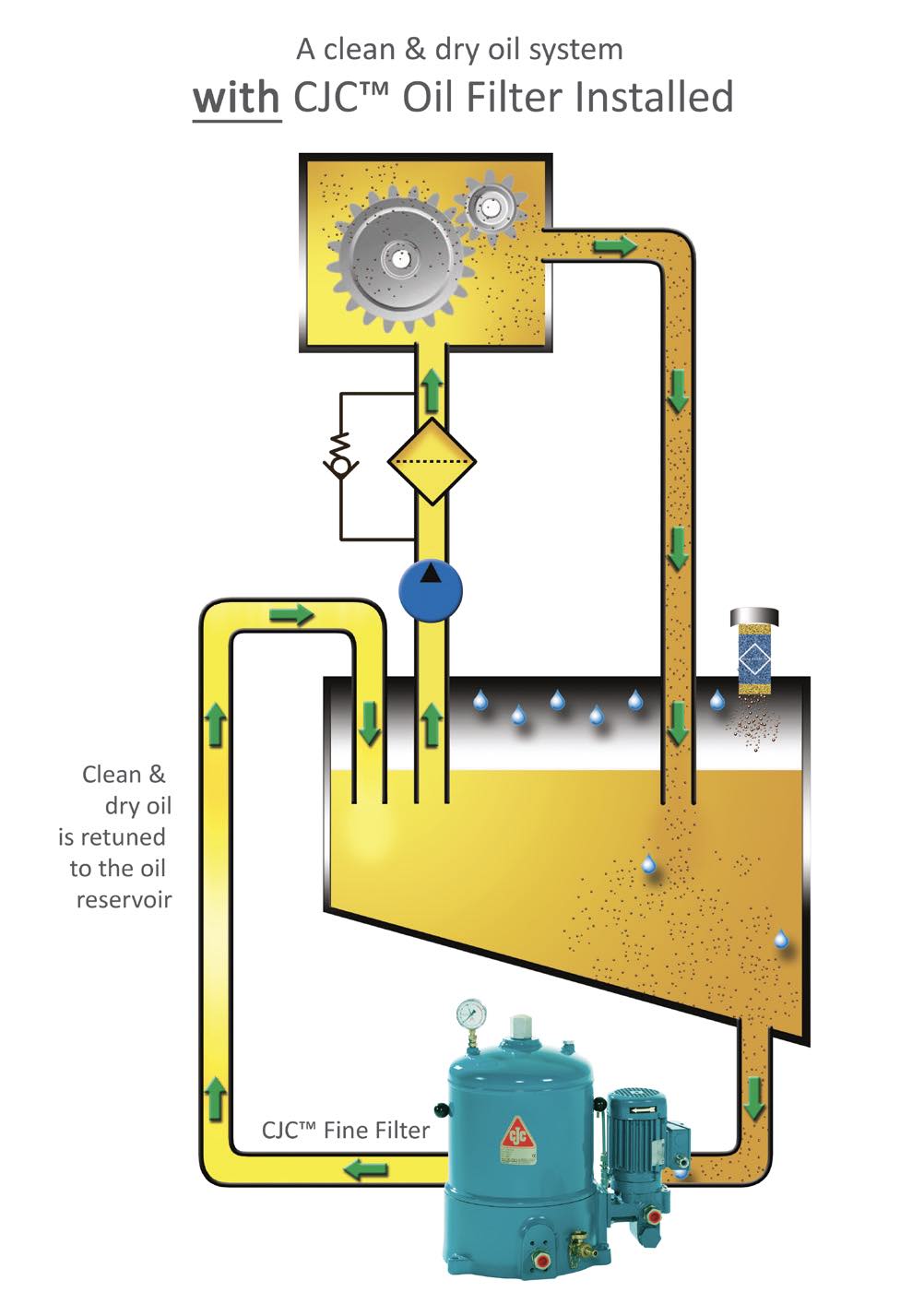
Figure 2. Principle drawing of oil filtration. Figure courtesy of C.C.JENSEN.
TLT: What is the No. 1 piece of advice you would give to someone responsible for an oil-run system for the first time?
Nyman: Get assistance—many organizations can help you implement best practices in oil maintenance. Also remember that new oil is not clean. New oil and diesel are often eight times more contaminated in terms of particles than recommended for high pressure hydraulics or common rail diesel injection. Typical ISO is 19/17/14 compared to the recommended ISO 16/14/11 according to ISO 4406. So remember to filter new oil and diesel before use in machines.
TLT: If I have no predictive maintenance procedures in place, what measurement parameters should I start measuring?
Nyman: Start with the most critical machines and make changes, which will give you the most bang for your buck. This is to stop ingression of contamination and to clean the oil continuously while in operation. Establish the current baseline, so you can clearly see the improvements, which the implementing best practices will give. Baseline could include current oil drain intervals and in-service life of parts like bearings, pumps, etc. Also make note of how often the systems have reliability issues and downtime. Do a standard oil analysis including particle count and water content (ppm by Karl Fischer Titration) to know the current oil cleanliness. Then implement best practices in oil handling and maintenance.
Changes with the best ROI on critical machines will be to install a 10-micron breather (preferably with desiccant), a 10-micron pleated inline filter and a 3-micron offline depth filter (kidney loop), capable of removing particles, water and varnish from the oil.
Follow the results in oil cleanliness with analysis every month until you have established a trend. Monitor the improvements in oil and component life, as well as reduced downtime for a minimum of six months. Present these improvements for management and it will for sure make you popular, plus it will open their wallets, so you can implement more best practices in the plant.
You can reach Steffen D. Nyman at sdn@cjc.dk.