Performing seals
By Drs. Wilfred T. Tysoe & Nicholas D. Spencer, Contributing Editors | TLT Cutting Edge December 2022
Using concentrated polymer brushes as seals may be a useful way to reduce leakage while still maintaining low friction.
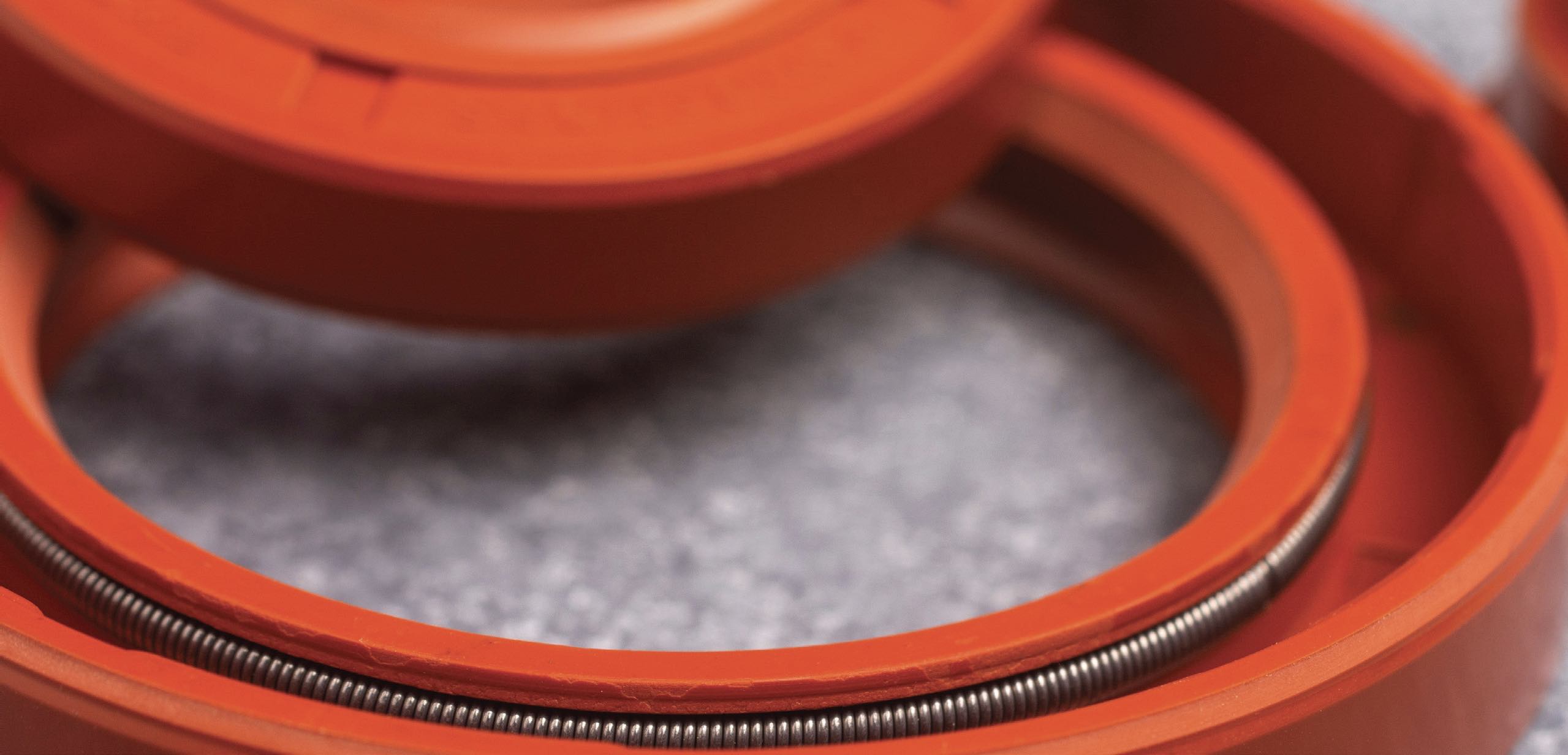
We have previously reported on the slippery nature of polymer brushes,
1 but practical applications of these surfaces outside the world of biomedical devices have been few and far between. This is because, while polymer brushes provide low-friction interfaces, they do not generally survive in high-pressure contacts, such as those found in most steel-based machines. One potential application area, however, may be that of seals, where the contact pressures tend to be relatively low.
In order to function, however, polymer brushes need to be in the presence of a good solvent, which may not be the same as the fluid that the seal is trying to hold in place. This is a serious limitation, unless one thinks substantially outside the box, which is precisely what a team from Japan, professors Chiharu Tadokoro and Takuo Nagamine of Saitama University, Japan, together with their colleagues Daichi Kitafuji (Saitama University), professor Ken Nakano (Yokohama National University), professor Shinya Sasaki (Tokyo University of Science), professor Takaya Sato (National Institute of Technology, Tsuruoka College) and professors Yoshinobu Tsujii and Keita Sakakibara (both of Kyoto University), has done.
2
The novelty in their approach is to grow concentrated (i.e., high-grafting-density) polymer brushes from the sealing surface using their best brush solvent, which is an ionic liquid,
N-(2-methoxyethyl)-
N-methylpyrrolidinium bis(trifluoromethanesulfonyl)imide (MEMP-TFSI). They then slide the coated surface, still wet with the MEMP-TSI, against a countersurface and test the seal in the presence of a lubricant that is not solvent for the brush, and is immiscible with the ionic liquid. Interestingly, the affinity of the MEMP-TFSI for the brushes is such that it is not depleted by the presence of the surrounding non-solvent, so it is still able to impart high lubricity to the brush-coated surface.
However, seals involve an intrinsic design challenge, which pits attaining low friction against forming a tight seal. The crucial parameter is the clearance, which when too small leads to high friction but when too large leads to lubricant leakage. In real systems this is tackled by incorporating an elastomeric layer (e.g., as in a syringe) or by structures such as piston rings in engines. However, these approaches come with a friction penalty, which a polymer brush could potentially reduce.
In order to monitor both leakage and friction for a polymer-brush seal, the authors constructed an apparatus
(see Figure 1) that measured both parameters under reciprocating motion.
Figure 1. Schematic diagram of experimental apparatus: (a.) configuration of experimental apparatus, (b.) rod-ring configuration in leakage-rate measurement and (c.) rod-ring configuration in friction-coefficient measurement. Reproduced by kind permission of Springer-Nature from Ref. 2.
The results of the study are dramatic. The authors found that the presence of the polymer brush led both to better sealing behavior (as determined by leakage rate at a given clearance) and to far lower friction than was found for the metal-metal contact. They also found that the MEMP-TFSI-imbued brushes remained both leak-tight and lubricious for up to 100 reciprocating cycles. Of interest was the observation that the brushes also seemed to work when applied to surfaces with micrometer-scale roughness, suggesting that they can act to “fill” the concave grooves on the rough surface, thereby mitigating any leakage when pressed against a smooth steel countersurface.
Clearly this topic requires further study under conditions that are closer to those of real sealing systems, but the observation that polymer brushes under lubricant-immiscible solvents can still function as lubricious surfaces opens the door to new and exciting approaches that can be used in the design of future tribological systems.
REFERENCES
1.
Tysoe, W.T. and Spencer, N.D. (2004), “Water: From chicken stock to base stock?” TLT,
60 (4), p. 64.
2.
Tadokoro, C., Kitafuji, D., Nagamine, T., Nakano, K., Sasaki, S., Sato, T., Sakakibara, K. and Tsujii, Y. (2022), “Concentrated polymer brush in reciprocating seal improves sealing performance with low friction even for rough surfaces and immiscible fluids,”
Tribology Letters, 70, p. 106.
Eddy Tysoe is a distinguished professor of physical chemistry at the University of Wisconsin-Milwaukee. You can reach him at wtt@uwm.edu.
Nic Spencer is emeritus professor of surface science and technology at the ETH Zurich, Switzerland, and editor-in-chief of the STLE-affiliated Tribology Letters journal. You can reach him at nspencer@ethz.ch.