Supercritical carbon dioxide occurs at a temperature and pressure above the compound’s critical point.
This material can be substituted for water in power generation applications and has the potential to increase energy output more efficiently.
Additive manufacture of complex gas turbine parts enables the use of complex designs in gas turbine designs utilizing supercritical carbon dioxide.
A new study demonstrates that 316L stainless steel produced by additive manufacturing can exhibit comparable stability when exposed to supercritical carbon dioxide compared to the currently used wrought alloy.
Efforts to improve the efficiency of gas turbines are leading researchers to examine the potential for using supercritical carbon dioxide as a thermal medium in power cycles. Gas turbines operate using the Brayton thermodynamic cycle, which evaluates efficiency as the ratio of work output to heat input.
Water has traditionally been the preferred thermal medium, but supercritical carbon dioxide is being investigated because it can lead to efficiency improvements by as much as 10%. Dr. Florent Bocher, senior research engineer at Southwest Research Institute (SwRI) in San Antonio, Texas, says, “Carbon dioxide transitions to the supercritical phase when the temperature and pressure are above its critical point. Under these conditions, supercritical carbon dioxide exhibits a combination of liquid and gaseous properties. The density of supercritical carbon dioxide is higher than the gaseous phase but not quite that of a liquid.”
An additional motivation for using supercritical carbon dioxide is that the gas turbines can now be much smaller. The reason is that smaller changes in temperature or pressure will cause much more significant shifts in the density of supercritical carbon dioxide compared to water.
Bocher says, “Supercritical carbon dioxide can be used in gas turbines in power generation applications either using legacy fossil fuel technologies (coal and natural gas) or novel solutions being considered, such as concentrated solar power and geothermal. The potential exists for substituting supercritical carbon dioxide for water in existing power generation sources and increasing energy output even when using existing capital equipment.”
One challenge to implementing the use of supercritical carbon dioxide is how metal alloys exposed to this thermal medium will maintain their integrity under high temperature and pressure operating conditions. Bocher says, “Operating conditions can range from 700 C to 1,200 C in these applications. There are lots of questions about how a material exposed to supercritical carbon dioxide will be able to withstand oxidation.”
The cost of supercritical carbon dioxide turbines will be higher than that of current designs for gas turbines. High-performance nickel alloys will be required, and advanced coatings must be used to improve durability. Optimizing the efficiency of gas turbines also is stifled by the current limitation of manufacturing processes. Additive manufacturing has the potential to make those complex designs a reality.
Bocher says, “Additive manufacturing is emerging as a viable technology for the production of complex metal parts and has the potential to be more economically viable than conventional means. The increase in complexity of gas turbine designs also makes it advantageous to use additive manufacturing. As a result, complex designs will be possible.”
The structure of a metal alloy prepared by additive manufacturing differs from the same metal alloy produced by conventional means. No research has been reported to date about how an additive manufactured metal alloy can handle extreme conditions found in supercritical carbon dioxide gas turbines. A new study has now been conducted that compares the stability of wrought 316L stainless steel to this same alloy produced by additive manufacturing
(see Figure 1).
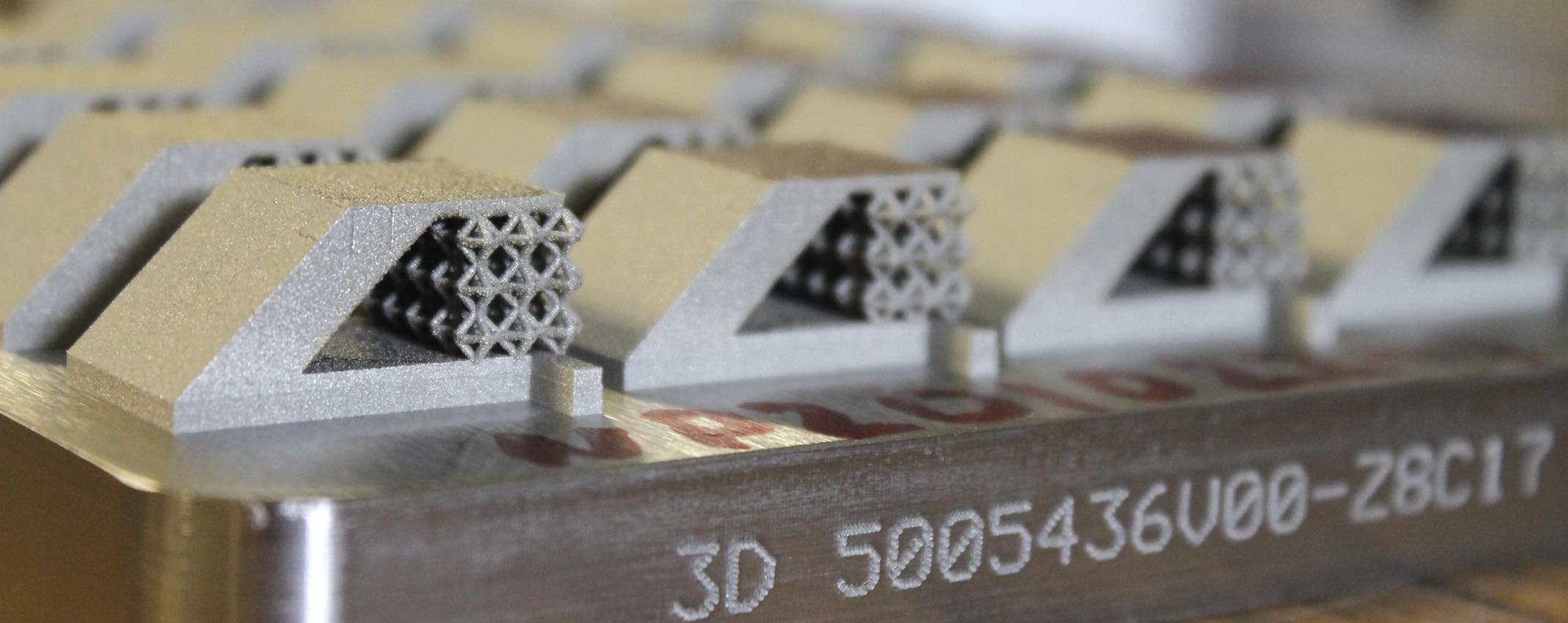
Figure 1. A complex part prepared from 316L stainless steel by an additive manufacturing process displays comparable performance to wrought 316L when exposed to supercritical carbon dioxide. Figure courtesy of Southwest Research Institute.
Stability study
Bocher and his colleagues exposed the 316L stainless steel alloys to a supercritical carbon dioxide environment by placing metal samples in an autoclave at a temperature of 450 C and a pressure of 76 bar for two weeks. The additive manufactured samples were prepared using a powder bed fusion method. The researchers tested the additive manufactured material in the printed state and when ground to a 1200 grit finish with silicon carbide paper.
Bocher says, “The reason we evaluated two versions of 316L stainless steel produced through additive manufacturing is because the surface of the printed metal alloy is different from the bulk material. The grinding process removes this printed surface facilitating the evaluation of just the metal’s microstructure.”
The additive manufactured 316L stainless steel samples were found to exhibit comparable stability after the two-week test to the wrought alloy. Extensive analysis was conducted using a scanning electron microscope to determine the oxide growth on the surface of the metal samples during the two-week test procedure.
An oxide coating covered 72% of the wrought produced and 54% of the additive manufactured prepared 316L stainless steel. Negligible oxidation was seen with either metal alloy.
The results show the potential for using additive manufactured metal alloys as materials in gas turbines. Oxide coating thickness also was measured, and the additive manufactured metal alloy exhibited a slightly thinner average oxide coating of 51 microns compared to the 95 microns observed for the wrought 316L stainless steel.
The additive manufactured stainless steel contained a high percentage of chromium on the surface. Bocher says, “Chromium is added to stainless steel to contribute to the metal alloy’s corrosion protection. The fact that there is a higher chromium content on the surface of the additive manufactured stainless steel probably means the alloy is more able to withstand oxidation at the surface. But there is uncertainty about whether the printed alloy’s bulk structure has been altered and may not provide the required mechanical properties for gas turbine applications.”
This study shows that additive manufactured metal alloys have the potential to be used in high-performance applications. Bocher says, “More research needs to be done to better understand how the structure and mechanical properties of printed metals change after exposure to supercritical carbon dioxide. Higher temperature and pressure experiments are planned for the future to determine how metal alloys will perform at temperatures up to 1,150 C and pressures up to 300 bar. Coatings also will be applied to the metal alloys to better understand how that will impact the oxidation process. Nickel alloys will be additive manufactured and included in future studies because they are better able to withstand these severe conditions.”
Additional information on this research can be found in a recent paper
1 or by contacting SWRI at
ask@swri.org.
REFERENCE
1.
Melia, M., Rosenberg, S., Kotula, P., Bocher, F. and Schaller, R. (2022), “Initial stages of oxide growth on AM stainless steel exposed to a supercritical CO
2 environment,”
Corrosion Science, 201, 110259.