MÜNZING
FOAM BAN® Hybrid Technology for Defoaming and Air Release in Non-Aqueous Lubricants
By Stefanie Velez, Industrial Applications Manager, Münzing | TLT CMF Plus November 2022
Foam minimization during the use of non-aqueous lubricants is required in many applications such as gears, compressors, engines, transmissions, hydraulics, turbines and more. It is imperative that foam and entrained air are minimized for optimal performance. For these reasons, non-aqueous lubricants commonly contain antifoams, which control the foam as it forms by disrupting the interfacial energies that stabilize the foam bubbles. Although the antifoam is expected to provide good surface foam control, it is important to balance foam control with the negative effect that an antifoam can have on the air release time.
Foam in Non-Aqueous Lubricants
In most non-aqueous lubricants, many factors drive the foaming tendencies. The Solutocapillary Marangoni flow
(Figure 1) is one of the naturally occurring factors that can increase the stabilization of foam in non-aqueous lubricants. In short, the lamella (area of fluid between air bubble and air surface) has an evaporative concentration of high surface tension materials which increases the surface tension. This causes the lower surface tension fluid in the bulk to flow towards the lamella, minimizing the surface tension gradient and slowing the ability for the fluid to drain.
Figure 1. Solutocapillary Marangoni Flow (Left) and Elastic Network caused by insoluble additives (right).
One of the most influential factors on foam tendency is the high molecular weight precipitates and additive packages used in most non-aqueous lubricants
(Figure 1). Some additives that may have an impact on foam are detergents, dispersants, friction modifiers, anti-wear agents, antioxidants, corrosion inhibitors, and VI improvers. Elastic networks within the lamella can form due to these insoluble surfactants, polymers and other additives causing an increase in the viscosity of the liquid in the lamella. The increase of viscosity tends to retard the ability for the liquid to drain, further stabilizing the foam bubbles.
Additionally, other factors such as surface viscosity, bulk viscosity, and contaminations play a role in the foam tendencies of these fluids.
Defoaming and Air Release in Non-aqueous lubricants
Antifoams are used to help mitigate the foam in non-aqueous lubricants. The antifoam droplet will enter into the air interface of the lamella and begin to spread in order to maximize the surface area of the antifoam-air interface. This occurs due to the antifoam droplet having a lower surface tension than the fluid, therefore, the antifoam-air interface will have lower interfacial energy than the antifoam-liquid interface. As the antifoam droplet spreads, it will eventually bridge and then rupture the foam bubble.
Entrained air and air release time play a large role in the performance of many nonaqueous lubricants
(Figure 2). While anti foams can help reduce the surface foam and entrained air during the process, they tend to prolong the air release time by reducing the velocity of the rising bubbles. Owing to lower surface tension than the oil and insolubility, an antifoam will begin to coat and isolate the air bubble, causing it to become “rigid”. Based on the Hadamard-Rybcynski equation, a “soft” bubble will rise at a faster rate compared to “rigid” bubbles, defined by Stokes law.
Figure 2. Initial entrained air vs air release time of a fluid with no antifoam and a fluid containing silicone antifoam.
High amounts of air entrainment can negatively impact the performance of nonaqueous fluids by altering the friction and lubricity among other properties during operations. Therefore, it is important to balance the foam control, amount of air entrainment and air release time effectively.
Antifoam Active Chemistries
Several chemistries can be considered as antifoams for non-aqueous lubricants, including but not limited to silicones, modified siloxanes, polyacrylates, and fluorosilicones. The two most widely used chemistries are silicones and polyacrylates. The benefit of silicone chemistry is the excellent foam control and less initial air entrainment due to the extremely low surface tension. Unfortunately, the low surface tension of silicones also leads to slower air release times for the air that has become entrained. Conversely, polyacrylate antifoams have a higher surface tension compared to silicones, leading to improved air release time but less foam control.
Based on the decades long experience Münzing has with non-aqueous lubricants and antifoams, a new hybrid technology has been introduced to the market. The hybrid technology contains both silicone and polyacrylate chemistry in order to achieve the optimal balance between foam control, entrained air and air release time
(Figure 3).
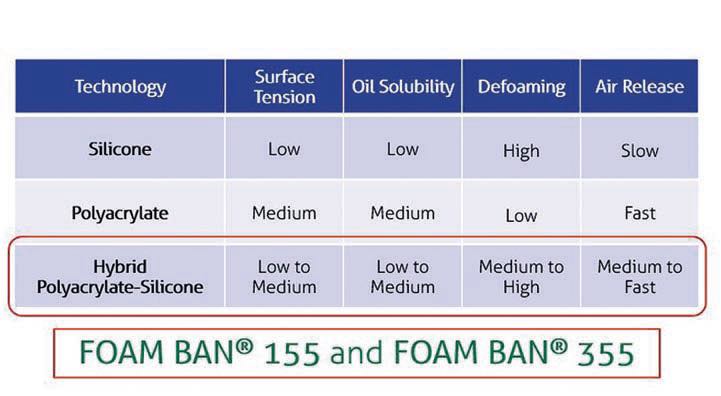
Figure 3. Antifoam Technologies and their basic properties.
Discussion Performance Study
In this study, Münzing evaluates several silicone, polyacrylate and hybrid technology antifoams to understand the trends and performance of each. The test methods used for evaluating the performance include ASTM D892 for surface foam and ASTM D3427 for entrained air and air release properties. Silicone 1 and Silicone 2 are typical silicone-based antifoams found in the market. PA 1 and PA 2 are typical polyacrylate non-si antifoams. FOAM BAN® 155 and FOAM BAN® 355 are Münzing’s two hybrid technology antifoams.
The first fluid evaluated is a typical Engine oil. As shown in
Figure 4, the polyacrylate antifoam does not provide significant foam control compared to the blank fluid (no antifoam present) throughout all three sequences of ASTM D892 testing. Furthermore, the polyacrylate antifoam does not provide a benefit in the initial entrained air
(Figure 5) but does provide a faster air release time compared to the sample containing silicone. The silicone antifoam shows the opposite trend, the foam control is good during the ASTM D892 testing but the air release time is longer than all other tested samples. Both hybrid antifoams provide a benefit during the ASTM D892 foam control testing and FOAM BAN® 355 provides the lowest entrained air and fastest air release during the ASTM D3427 test.
Figure 4. Evaluation of Antifoam in Engine Oil - Foam control via ASTM D892 Method.
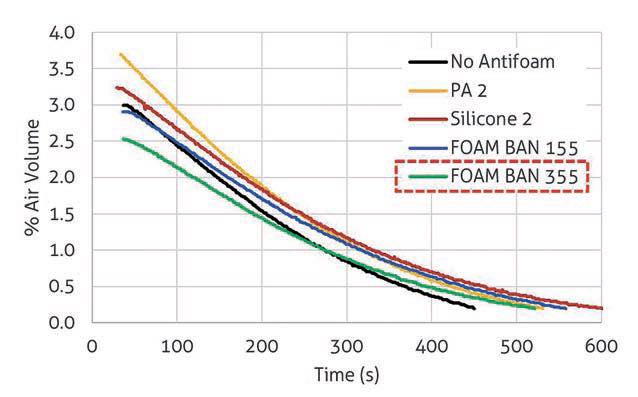
Figure 5. Evaluation of Antifoam in Engine Oil – Initial Entrained air and Air release time via ASTM D3427 Method.
The second fluid evaluated is a marine lubricant oil. Throughout the ASTM D892 foam test, FOAM BAN® 155 provided the most foam control
(Figure 6). Both hybrid antifoams provided lower initial entrained air and faster air release time compared to both silicone and polyacrylate technologies when tested on their own
(Figure 7).
Figure 6. Evaluation of Antifoam in Marine Lubricant Oil - Foam control via ASTM D892 Method.
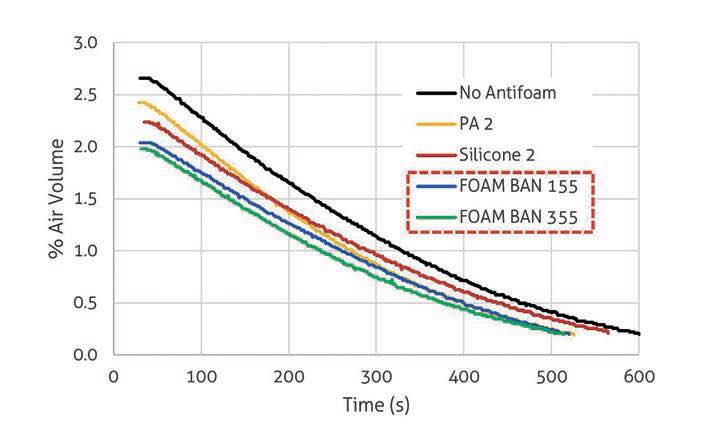
Figure 7. Evaluation of Antifoam in Marine Lubricant Oil – Initial Entrained air and Air release time via ASTM D3427 Method.
Conclusion
Based on the data collected during evaluations of these non-aqueous fluids, it is clear that the hybrid technology of the two chemistries, polyacrylate and silicone, can provide a significant benefit in foam control, entrained air and air release time. In all three examples, FOAM BAN® Hybrid Technology, FOAM BAN® 155 and FOAM BAN® 355, provided significant benefit compared to single chemistry technology antifoams.