Additives and engine oils
By Dan Holdmeyer, Contributing Editor | TLT Lubrication Fundamentals November 2022
Engine oils contain a complex blend of additives to minimize emission and aid efficiency.

Engine oils have the highest percentage of additives compared to the additive packages of turbine, hydraulic and gear applications that we discussed over the past two months. Engine oils do contain many of the same types of additives found in those applications and for the same reasons. Specifically, the additives used are rust and oxidation inhibitors, corrosion inhibitors, foam inhibitors, pour point depressants, antiwear additives and viscosity index improvers. The most significant differences in additives for engine oil applications are the detergents and dispersants.
Internal combustion engines create a rapid burn of a mixture of atomized fuel and air (specifically oxygen), which creates great expansion of the mixture. The expansion creates pressure against the engine pistons inside the cylinders to force rotation of the crankshaft connected to the pistons, thus converting fuel to mechanical energy. The engine bearings obviously need lubrication similarly to the bearings in the previously mentioned applications. However, the mechanics of the piston and cylinder, along with the combustion of the fuel in the engine, create many challenges for the engine oil. In addition, these challenges are even more difficult due to the wide variations of speed, load and temperature in the engine providing more than one lubrication regime for each component.
Boundary and mixed lubrication are predominant during engine start-up for all engine moving components. Thus, the engine oil must have the right amount of antiwear additives.
Engine crankshaft and camshaft bearings are fed lubricant via oil passages in the shafts providing enough lubricant film to create full fluid film lubrication, or a hydrodynamic lubrication regime, in the bearings when the engine is operating at normal speeds (see Figure 1). Demand for improved engine efficiency has resulted in lower viscosity engine oils used today to reduce the internal friction of the engine. Fortunately, better machining of the engine bearings, i.e., smoother bearing surfaces, enables a hydrodynamic lubrication regime to still form with lower viscosities. We discussed this relationship in the July 2022 TLT Lubrication Fundamentals article titled “The Stribeck curve.” This thinner lubricant film does result in greater particulate contamination sensitivity—i.e., cleaner oil is even more critical.
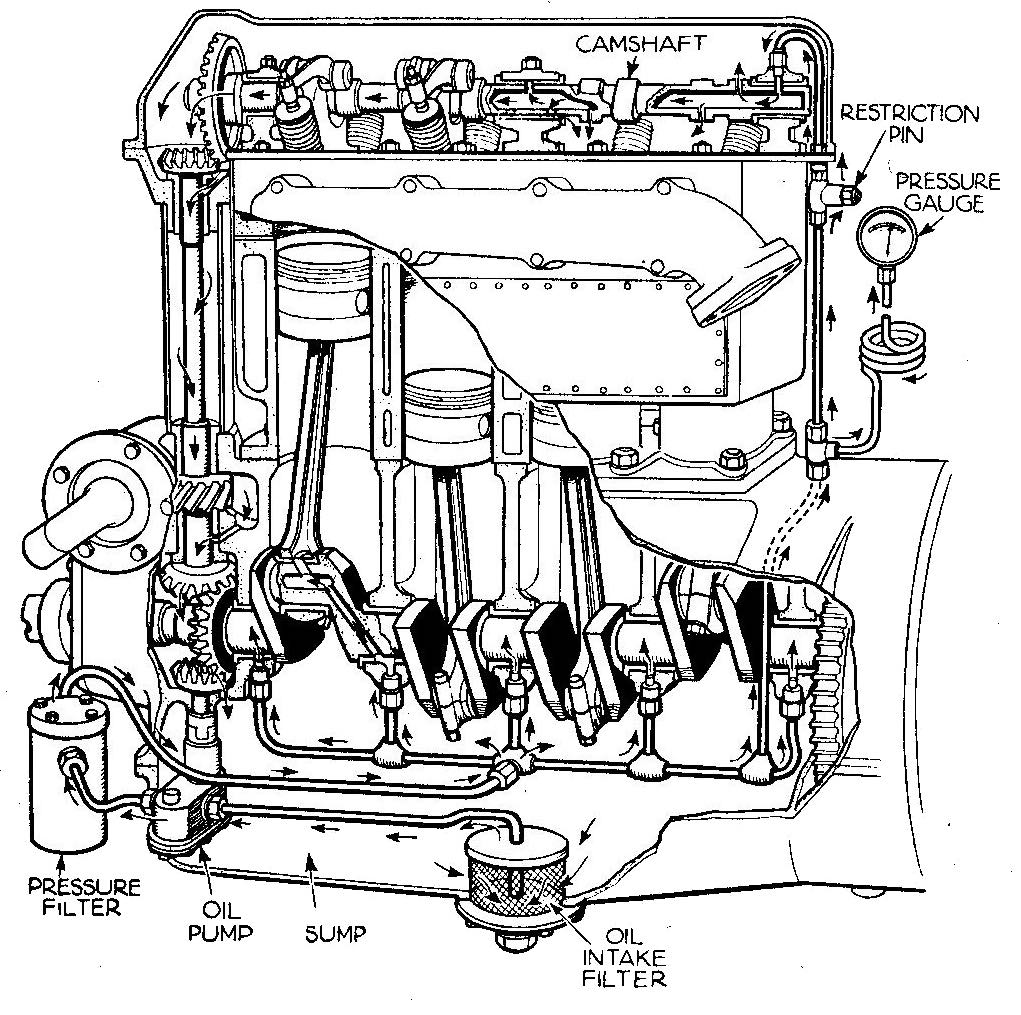
Figure 1. Engine lubrication. Figure courtesy of Andy Dingley (scanner) - Scan from The Autocar (thirteenth edition, circa 1935), Autocar Handbook, London: Iliffe & Sons, Public Domain, via Wikimedia Commons.
The piston, ring and cylinder assembly relies on splash lubrication. The piston ring against the cylinder wall has the most complicated lubrication mechanism in the engine. It experiences boundary lubrication at the top, bottom and dead centers where the sliding action stops and reverses direction. The lubricant wedge must reestablish at each reversal of direction. Hydrodynamic lubrication regimes may form between the ring and the cylinder during mid-stroke. The lubricant film between the ring and cylinder wall must provide a seal for the combustion chamber to prevent blow-by, minimize wear, control oil consumption, reduce friction and transfer heat.
The lubricant film thickness between the ring and the cylinder wall is critical to not allow too much oil into the combustion chamber. Too much oil in the combustion chamber causes excessive oil consumption, which leads to fouled spark plugs in gasoline engines, deposits on the exhaust valves, deposits on the piston, plus other engine maladies. Excessive oil consumption also will damage catalytic converters in the exhaust system that is designed to reduce emissions.
The ring designs and cylinder cross-hatching are part of the engine design to control the oil in the combustion chamber, but the multigrade engine oils also help control the oil consumption rate. Multigrade oils are formulated with viscosity index improvers (VII), which are long polymers that uncoil as temperature rises, effectively increasing their size and the oil’s viscosity. At low temperatures, these polymers coil up again to return the oil to its original viscosity. This reduces the rate of change of viscosity with temperature and makes possible the formulation of multigrade oils. Multigrade oils allow for easier start-up and quicker oil flow throughout the engine during cold temperatures and yet provide enough lubricant film at high temperature to protect the moving components of the engine. These VII additives also exhibit temporary viscosity loss under the high stress of the ring and cylinder wall area. This temporary lower viscosity helps reduce the amount of oil that enters the combustion chamber.
Counterintuitively, a higher viscosity oil does not reduce oil consumption and may actually increase oil consumption. Using a higher viscosity oil will increase the engine oil pressure, which may stop the “low-oil pressure” alert, but over time the higher viscosity may lead to more oil in the combustion chamber. A caveat on this is that a higher viscosity oil may slightly decrease oil leakage, but not for long. High mileage engine oils may have a better fix to oil leaks.
The rings on the piston are subject to the very high combustion temperatures, as is the oil lubricating and sealing the rings. The engine oil, therefore, needs to have a very good oxidation inhibitor additive package plus detergents. The oxidation inhibitors provide protection against oil degradation and the formation of varnish deposits, but more protection is needed in this extreme environment. Excessive deposits in the ring grooves of the piston prevent the rings from “floating” freely within the grooves and from sealing properly, leading to blow-by, more oil consumption and possibly broken rings. The detergents, as the name implies, help keep the ring grooves and piston crown clean of deposits at those high combustion temperatures (see Figure 2). Detergents chemically react with oxidation products, such as varnish and other deposits, to prevent them from sticking to metal surfaces of the piston and rings, and throughout the engine.
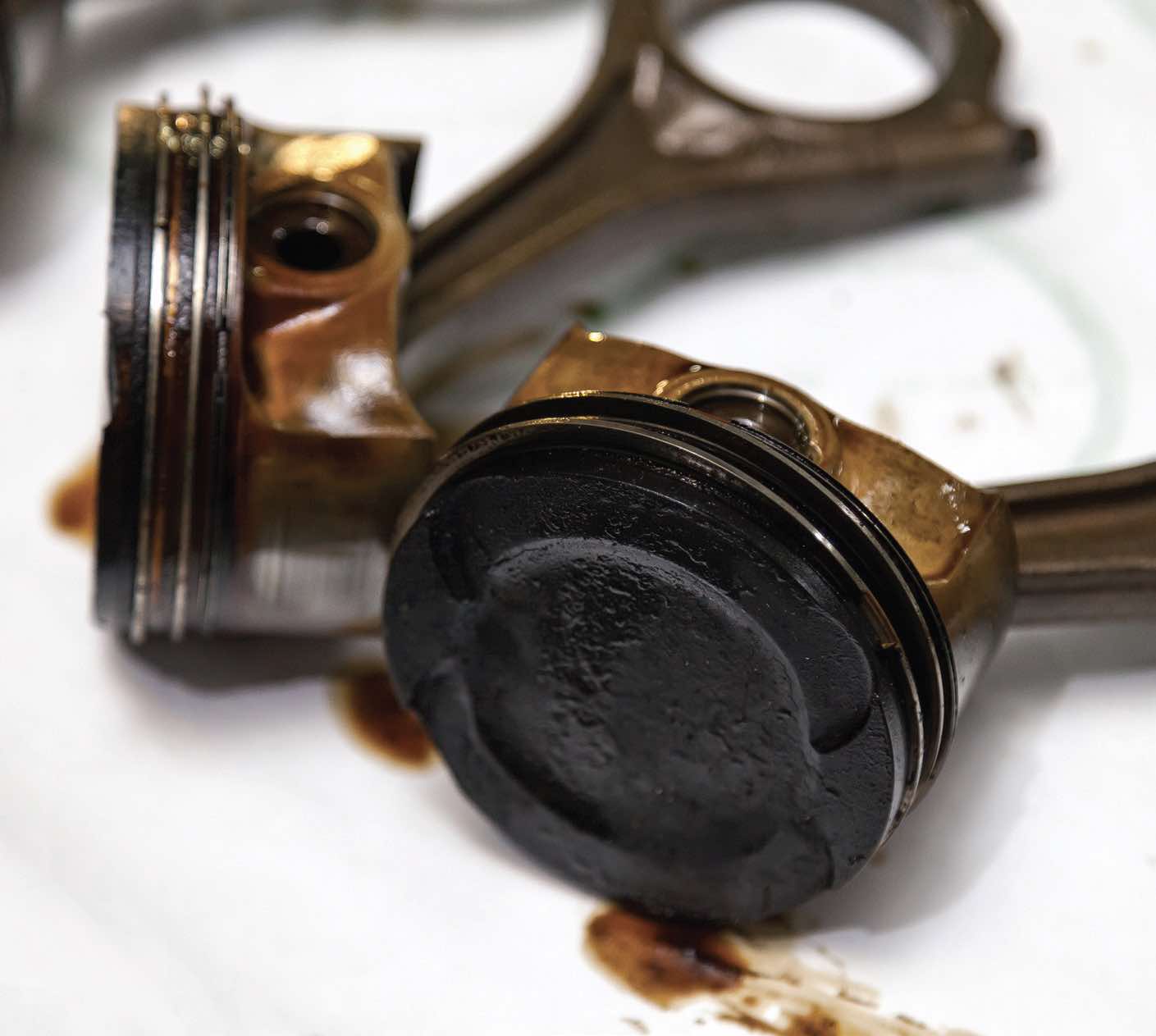
Figure 2. Two metal car pistons in poor condition.
Bearing corrosion is a potential failure process due to the acids and water combustion byproducts that get into the oil. If left unchecked, these acids and water will corrode and rust metal surfaces throughout the engine. Therefore, the engine oil detergents along with the rust and corrosion inhibitors are designed to not only neutralize these acids, in addition to the acids formed by oil degradation, but also to provide a protective coating on the metal surfaces.
Detergents may be neutral or alkaline. The alkaline detergents are commonly “overbased” and provide a base reserve in the oil known as the base number (BN), previously known as total base number. Oils with higher BN provide greater acid neutralizing capability. Again, too much is not good. Too much detergent additive can interfere with antiwear protection or lead to excessive deposit formation at high temperatures—just the opposite of the intended purpose of the detergents.
Too much detergent additive also can lead to excessive ash in the engine. Detergents contain metal elements in them. Typically, these metals are calcium, magnesium, boron or sodium. These metallic-based detergents produce ash when burned. A small amount of ash can help protect engine valves against excessive wear and valve recession. However, too much ash on the valve seats can lead to gaps in the valve seat sealing that may result in torched valves that need to be replaced.
Ash content of the oil is measured by ASTM D874. It is the weight percentage of the residue from a given amount of the oil burned in the presence of sulfuric acid. Thus, it is often called the sulfated ash content, or just ash content and is reported as “mass %.” Directionally, the higher sulfated ash content indicates higher BN, or alkaline reserve to neutralize acids, but the two are not directly correlated. Certain metallic-based detergents provide greater BN than others with the same amount of sulfated ash content. Additionally, other oil additives also may contain metallic components, such as zinc in some antiwear additives, that contribute to the sulfated ash content. Gasoline and diesel engine oils have a sulfated ash content of 1% or less. Marine engine oils have higher sulfated ash content and higher BN because they have to neutralize the acids formed from burning higher sulfur content fuels. Although, EPA regulations are lowering the allowable sulfur in some of the marine fuels as well.
EPA emissions requirements for internal combustion engines also dictate the maximum amount and type of additives used in engine oils and fuels. With such large numbers of internal combustion engines in the world, even the smallest improvement in emission has an effect. Catalytic converters are installed in all automobiles and over-the-road trucks today. Marine and railroad engines also are subject to emission requirements. The after-engine treatments, such as catalytic converters, can easily become plugged or inactive with too much ash content, phosphorous additives and too much sulfur in the oil or fuel, or just too much oil burned by the engine. Thus, today’s additive systems are quite different from the additives used even as little as 10 years ago to give improved performance without the ash forming additives.
Dispersant additives compliment performance of detergents in today’s engine oils. Dispersants are, however, ashless, or free of metal elements. They help keep the metal surfaces clean in lower temperature areas. The dispersants attach to soot and varnish precursors to prevent them from agglomerating or becoming so large that they drop out of suspension in the oil. Dispersants also reduce soot, and sludge-related viscosity increases by keeping these contaminants separated. Because they are ashless, they do not contribute to the sulfated ash content. They do minimally contribute to BN but do not have the “staying power” of detergents in regard to BN.
Seal conditioners, or sometimes called seal swell additives, may be used in some high mileage engine oils. These additives tend to be a little aromatic and replenish some of the oil in old and worn engine seals. This helps the seals remain soft versus becoming brittle and, thus, helps older, higher mileage engines minimize seal leaks. High mileage engine oils also may be blended at the higher end of the SAE viscosity grade to help keep the oil pressure in range, particularly at idle. Older engine bearings may have slightly wider clearances, so the lower viscosity oils of today’s engine oils might not stay in the bearing as long resulting in lower oil pressure and a thinner lubricant film. A slightly higher viscosity, still within the SAE grade, will help maintain the oil pressure and proper lubricant film.
Another engine oil performance characteristic that helps with meeting emission requirements of today is oil volatility. Lower oil volatility results in less oil burned, or vaporizing, in the engine. Engine oil volatility is mainly controlled by the base oil used in the engine oil. Lower viscosity oils generally have higher oil volatility than higher viscosity oils of the same base stock. Most synthetic base stocks have lower oil volatility than mineral base stocks of the same viscosity. This is why so many engines require synthetic-based engine oils.
This is the third and final article in the series on additives. In the first article, we started with base stock selection to meet certain performance criteria enhanced by the right additives required for specific lubrication applications. We’ve now come full circle with identifying the predominant engine oil additives in use today and using a specific base stock type to help meet emission requirements.
Dan Holdmeyer is retired from Chevron Lubricants and is based in Washington, Mo. You can reach him at dan.holdmeyer@gmail.com.