More on how additives finish the lubricant
Dan Holdmeyer, Contributing Editor | TLT Lubrication Fundamentals October 2022
Some applications require a complex blend of additives, but skilled lubricant formulators can develop the precise product for the job.
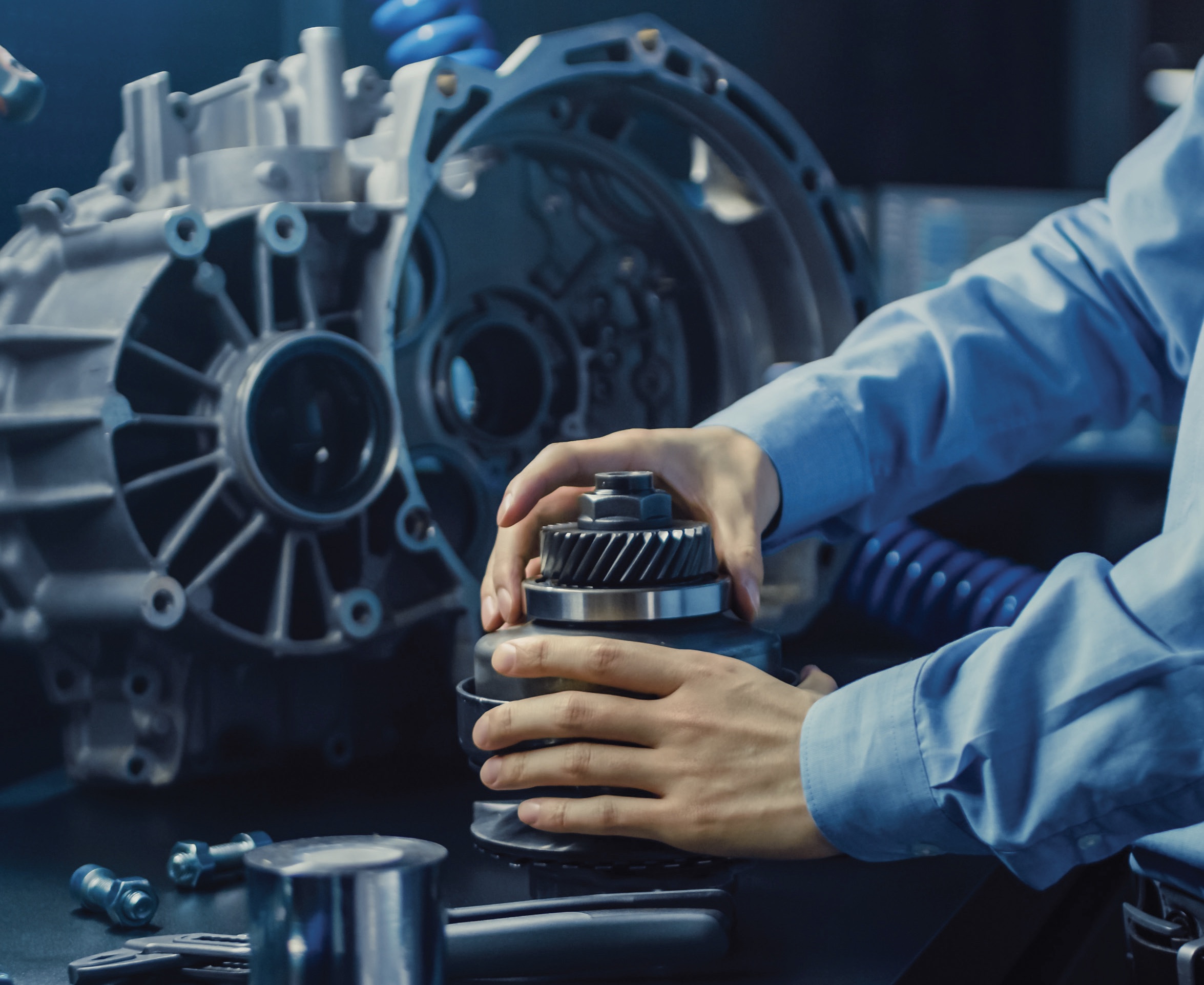
Last month, we covered rust and oxidation inhibitors, corrosion inhibitors, metal deactivators, foam inhibitors, pour point depressants, antiwear (AW) additives, demulsifiers and viscosity index improvers for turbine and hydraulic applications. Now let’s look at other applications that require some of these same additives but also require other additives.
Gear oils
Gears transfer power from one rotating shaft to another. Most often the gear sets either increase the speed and decrease torque or decrease speed and increase torque. Occasionally gears simply change the direction of power without changing speed or torque. The gear teeth are subject to heavy, fluctuating loads with frequent shock loads.
Think of the differential gears of the drive axles on an over-the-road tractor-trailer truck. The drive shaft sends power through the differential to the wheels to power the truck across the country with its heavy loads. Typically, only three to four gear teeth (see Figure 1) are in contact with each other to transfer the power through the gear set as it rotates and moves 80,000 pounds down the road. That is a lot of pressure on the gear teeth and the oil between them protecting them from excess wear. The AW additives used in hydraulic oils do not provide enough protection against wear in these extreme conditions. Therefore, additives for the extreme pressure associated with these heavily load gear applications are required and historically were called extreme pressure additives.
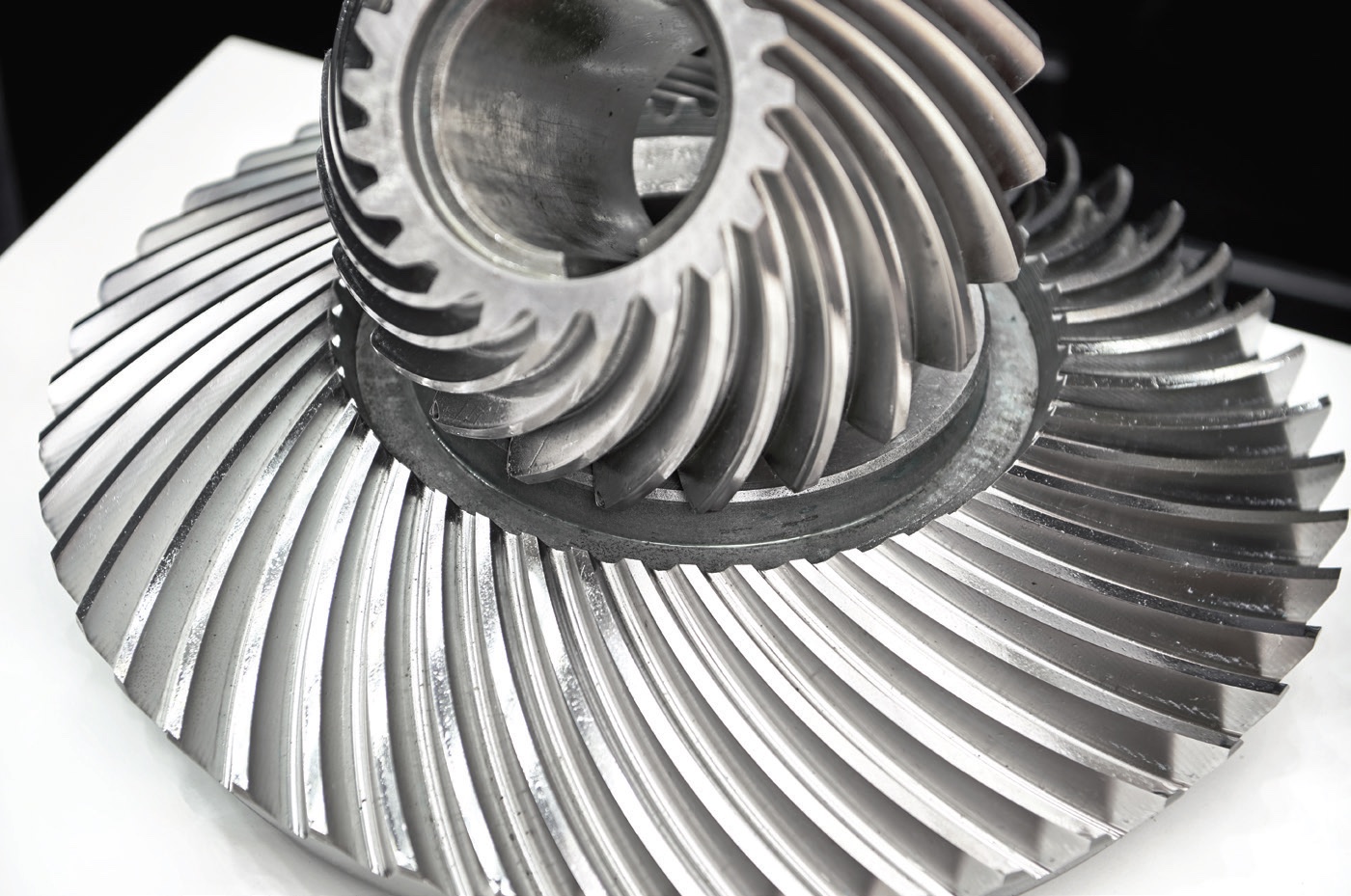
Figure 1. Spiral bevel gear.
In 2016, ANSI/AGMA 9005-F16 was updated to aid in lubricant selection with enhanced characteristics. A myriad of technical updates were made to the predecessor document, ANSI/AGMA 9006-E02, and one minor nomenclature update recommended transitioning to anti-scuff (AS) terminology from the previously common term extreme pressure (EP), because the old terminology didn’t accurately depict the lubricant characteristic. EP is the condition that requires the AS additives to protect the gear teeth from excess wear. The new terminology is not ubiquitous yet, as you will still hear and read about EP gear oils referencing gear oils with AS additives.
AS additives are activated by the elevated pressures and resulting high surface temperatures in the meshing of the gear teeth. When activated, the AS additives chemically react with the gear metal surface to form a wear reducing film that reduces friction, prevents metal-to-metal contact and stops welding between meshing gear teeth. Without the AS additives, the EPs and temperatures would friction weld the meshing gear teeth together, so when the gear set continues to rotate and the gear teeth separate, the weld being stronger than the gear teeth metallurgy tears out a chunk of the gear, leaving a pit or spall. The AS additive prevents this weld-and-tear action.
Not all AS additives are activated at the same pressure and temperature—nor do they decompose and become ineffective at the same temperature. Well-formulated AS gear oils utilize different AS and AW additives to protect against wear from low pressure and temperature continuously to the maximum pressure and temperature. Figure 2 depicts this additive performance transition from low to high temperatures and pressures. The base oil and fatty AW additives provide wear protection at relatively low temperatures, whereas the various types of AS additives are activated at different elevated temperatures. Also note that the additives decompose or become ineffective at various temperatures where the coefficient of friction would consequentially increase if not for another AS additive becoming active.
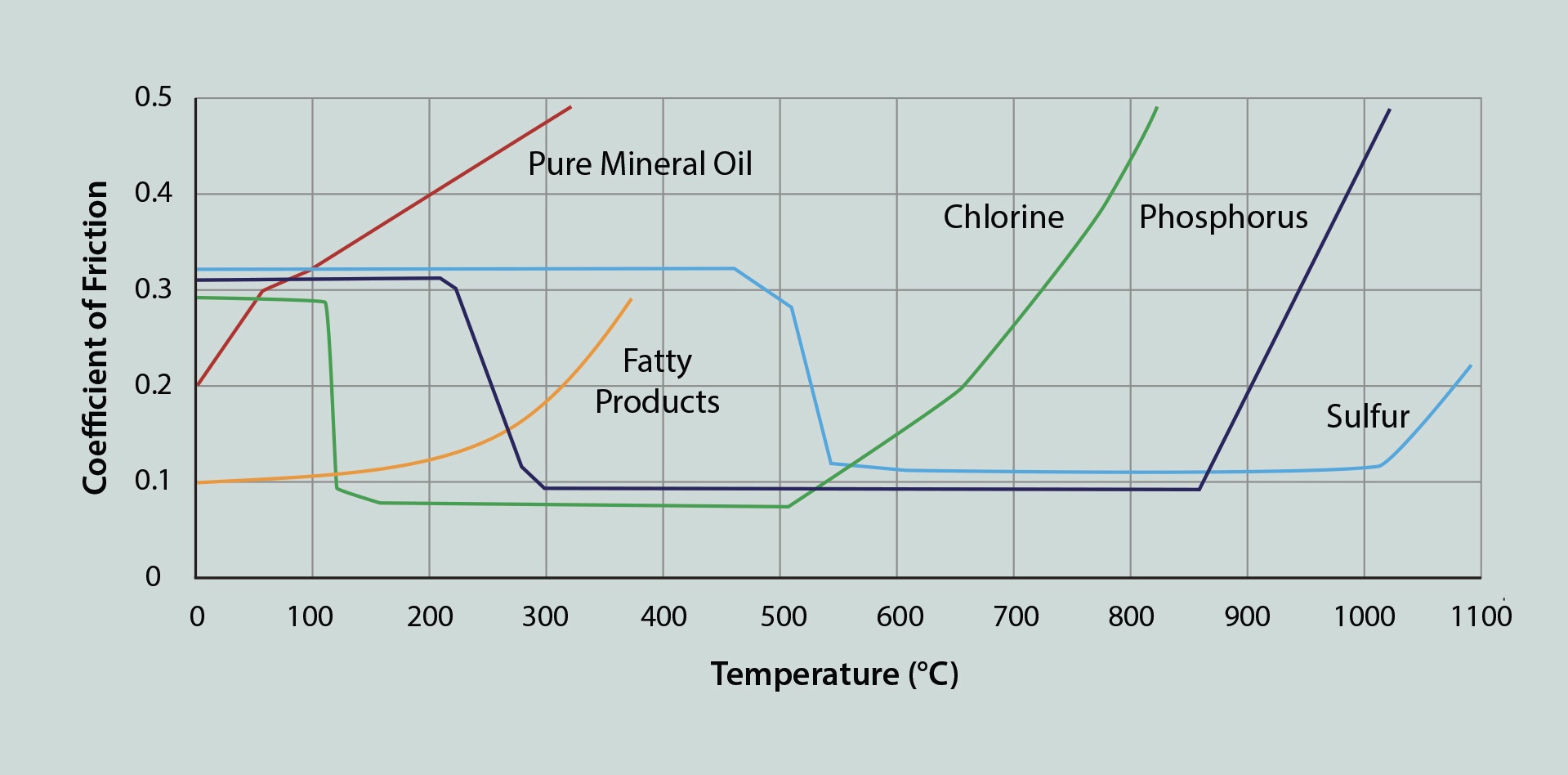
Figure 2. Effective temperature ranges of AW and EP additive chemistries. Figure courtesy of King Industries, Inc., originally created by Rhône-Poulenc.
Here again we must not use more AS additive than needed because too much AS additive can be corrosive to various metals in the gearbox, or if used in other applications such as hydraulic systems, component life can be severely shortened. For enclosed gear sets, ANSI/AGMA 9005-F16 designates three distinct oil categories: inhibited, AS and compounded.
Inhibited gear oils are generally called rust and oxidation inhibited oils (R&O) as discussed in last month’s TLT Lubrication Fundamentals article, “How additives finish the lubricant,” for turbine applications. They contain rust, corrosion, oxidation and foam inhibitors, along with demulsifiers. They also may have mild AW additives to help protect against wear in addition to the lubricant film, particularly during start up. Many industrial gear OEMs recommend against AS, formerly called EP, additives in their enclosed gear sets because the additives can be corrosive to softer metals used in the cages of the rolling element bearings in the gearbox. The OEMs design their gear sets so the gear meshing pressures are not extremely high.
AS gear oils contain the same additives as inhibited oils plus AS additives. AS gear oils, quite often still referred to as EP gear oils, are required in heavily loaded gear sets or when subjected to shock or reversing loads as these increase gear teeth pressures and temperatures. These conditions are most common in over-the-road vehicles where the size of the gearbox is limited and the horsepower throughput is great, but many industrial applications, such as plastic extruder gear sets, also are subject to these high pressures and temperatures. Always refer to the OEM’s operator or maintenance manuals to know if R&O or AS gear oils are recommended.
Compounded gear oils are typically recommended for worm gear applications and contain 3%-10% natural or synthetic fatty additives. Worm gears experience a relatively high amount of sliding action across the gear teeth, relative to helical and gear types, and the fatty acids provide additional slipperiness, particularly in mineral-based oils. Synthetic base oils, with their lower friction coefficients compared to mineral oils, are common in worm gears as they help improve the efficiency of the gear set, provide improved oxidation resistance and provide wider operating temperature ranges.
Automotive gear applications are addressed by the American Petroleum Institute (API) Gear Oil Specifications API GL-1, API GL-4, API GL-5, API GL-6 and API MT-1. Each grade has a set of quality and performance standards. API GL-1 could roughly be compared to an inhibited oil as discussed previously, whereas API GL-4 would more closely resemble the AS gear oil. API GL-5 is a more common designation for most over-the-road off-set hypoid gears found in the differentials. API GL-6 is for extremely off-set hypoid gears. Each numerically increasing level most notably represents an increase in AS additive and performance standard to minimize scoring of the gear teeth. API MT-1 designation for manual transmissions is certified to provide protection against the combination of thermal degradation, component wear and oil-seal deterioration, which is not specified in meeting only the requirements of API GL-1, 4 or 5.
Viscosity index improvers (VII) are rarely used in enclosed gear sets as the VII additives tend to be sheared down in the meshing of the gears. (VII shearing will be discussed in more detail as we discuss engine oil additives.) To give inhibited gear oils wider operating temperatures and longer oil life, synthetic base oils are common in gear oils where the oils are not overly susceptible to contamination requiring frequent oil changes that would make them less cost effective.
Automatic transmission fluids
There are a few types of automatic transmissions in the market today, and we will limit our discussion on the most common in use today to introduce friction modifier additives. The automatic transmission is powered from the engine via the torque converter, which relies almost solely on the oil’s viscosity to transmit power to the rest of the transmission. A pump in the transmission powers the internal hydraulics to activate certain clutch packs, friction bands or brake packs to engage the various gear ratios to apply the appropriate torque and speed to the transmission output shaft. As you can imagine from that, an automatic transmission fluid (ATF) requires many of the additives we’ve already discussed: R&O, AW, antifoam and VII (because it needs to operate in the cold of winter and heat of summer), to name a few of the common additives. Now comes the truly challenging formulation design. We have AW additives designed to minimize wear and friction, but in the automatic transmission we have clutch packs, friction bands and brake packs that require friction to work. That is a conundrum. Fortunately, there are some very creative and intelligent scientists that have come up with additives designed for the ATF to allow just the right amount of friction and yet not so much as to allow excessive wearing of the bearings and gears in the transmission. The additives are called friction modifiers. There are many different types of friction modifiers to work with various types of clutches, friction bands and brake materials that will provide the ideal transfer of power preferred by each OEM. Some transmissions will exhibit a smooth gradual transmission of power, while others will present a much more dramatic and quick transition. This is why today there is no one ATF for all automatic transmissions.
Another unique additive for ATFs is the dye. It does not affect the performance of the ATF but enables the automobile owner to recognize an ATF leak on the garage floor as an ATF and not an engine oil or coolant or differential fluid. Well, that was the original reasoning for the dye, but today’s ATFs are not all red.
So far, the ATF has been the most complex oil application discussed in this series of articles on lubricant additives. ATFs typically contain VIIs, oxidation inhibitors, rust inhibitors, foam inhibitors, AS additives, AW additives, demulsifiers, friction modifiers and dyes. Next month, we will tackle the engine oil additive makeup.
Dan Holdmeyer is retired from Chevron Lubricants and is based in Washington, Mo. You can reach him at dan.holdmeyer@gmail.com.