KEY CONCEPTS
•
Key parameters to consider when selecting additives are solubility, performance, longevity and formulation stability.
•
Main trends are environment, health and safety, sustainability, regulatory and availability.
•
Diversity of applications creates opportunities for innovation.
Very little neat oil is used as a lubricant. Almost all commercial lubricants contain additives from less than 1% to greater than 25% concentration. By far the largest market for such additives is in the transportation field, including engines and drivetrains in cars, trucks, buses, locomotives and ships. However, lubricant additives also are critical in the industrial and food and beverage markets.
The high-level functions of additives can be summarized as:
•
Protect metal surfaces (rings, bearings, gears, etc.)
•
Extend lubricant life
•
Expand the range of lubricant applicability.
Specific types of additives include but are not limited to the following:
•
Antiwear
•
Extreme pressure
•
Antioxidant
•
Rust inhibitor
•
Yellow metal deactivator
•
Dispersant
•
Detergent
•
Pour point depressant
•
Viscosity index improver
•
Emulsifier
•
Demulsifier
•
Tackifier
•
Bactericide
•
Gelling agents (for grease).
Manufacturers of formulated lubricants require these additives to possess certain characteristics for acceptance. They must be stable in storage, free of offensive odor and nontoxic by normal industrial standards. Additives should be sufficiently soluble or capable of being processed in conventional blending equipment. Since many are highly viscous materials or actual solids, they are generally sold as concentrated solutions in diluent oil.
Additives impact different parts of the tribosystem and can be classified in the following way:
1
1.
Influence the physical and chemical properties of the base fluid:
a.
Physical effects: e.g., viscosity-temperature (VT) behavior characteristics, demulsibility, low temperature properties, etc.
b.
Chemical effects: e.g., oxidation stability
2.
Affect primarily the metal surfaces, modifying their physiochemical properties: e.g., reduction of friction, increase of extreme pressure (EP) behavior, wear protection, corrosion inhibition.
Besides their many beneficial effects, additives can have some negative side effects as well. They can have an undesirable interaction with each another if the wrong chemistry choice is used or its percentage in the finished lubricant is not optimal. Common additive synergies, antagonists and the potential for interactions should be anticipated by the lubricant manufacturer to ensure optimal performance in the intended application.
Although additives can dramatically influence lubricant performance, they often cannot address certain characteristics sufficiently well. This includes volatility, thermal stability, thermal conductivity, compressibility, boiling point, etc.
1 In addition, a formulated high-performance lubricant often requires a premier quality base fluid.
1 Presently, there is a trend to use hydrocracked and severely hydrotreated highly refined mineral oils, synthetic polyalphaolefins (PAOs) and esters. Variations in formulation strategies with additives and base oils are becoming commonplace.
1
In view of formulated products and components, there are performance, regulatory and application aspects to be considered. STLE member Dr. Bryan Bergeron, industrial lubricants innovation manager, A.W. Chesterton Co., says: “Business plans; industry requirements; voice of customer; and federal, state and local regulations drive projects. Product functionality and safety are often diametrically opposed forces. This is true of solvent reduced lubricants where penetrating ability, volatility, viscosity and flammability are common topics. Aerosolized products are designed with certain spray characteristics and promoted to approved applications with regulatory compliance, but importation rules of some countries are strict. At the component level in bulk products, antiwear (AW), EP, antioxidant (AO) and rust inhibitor (RI) additive technologies are usually essential in hot, heavy and humid environments. Tackifiers, emulsifiers, dispersants and detergents are needed in certain scenarios. Various Group I through V base stocks are all implemented.”
He continues: “We review safety data sheets (SDSs) for air emission, waste disposal, compliance, health and safety, assess global inventory listing and provide Toxic Substances Control Act (TSCA) and/or research exemption import forms as needed to our global affiliates and partners. A standard practice is to minimize use of raw materials, which SDSs contains globally harmonized system (GHS) pictograms or hazard statements to reduce risk throughout the value chain.” For example, he says: “Specific topics include exclusion or limitation of perfluorooctanoic acid (PFOA), perfluorooctane sulfonic acid (PFOS), substances of very high concern (SVHC), volatile organic compounds (VOCs), dimethyl sulfoxide (DMSO) extract and Superfund Amendments and Reauthorization Act (SARA) reportable items to the Environmental Protection Agency (EPA). Numerous safety aspects of raw materials are identified and controlled in our enterprise resource planning (ERP) system
(see Table 1).”
Table 1. List of several safety aspects for raw material storage
“There are challenges simultaneously achieving high performance, attaining H1 lubricant registration, gaining environmentally acceptable lubricant (EAL) certification, reaching industrial standards and addressing safety concerns,” Bergeron says. “Limited availability of food-grade HX-1 raw materials do simplify permutations of formulated prototypes but sometimes at the expense of performance such as EP capability of oils. Scrutiny of AOs (e.g., aminic, phenolic) and yellow metal deactivators (e.g., benzotriazole derivative,
see Figure 1) necessitated formulation modification to maintain compliance with H1 registration and limit hazard statements and pictograms on global SDSs.” (For more information, see the June 2022 TLT Feature article titled “Safer lubricants for food processing equipment.”)
Figure 1. Chemical structures of a triazole, dithiophosphate ester derivative and butylated hydroxytoluene (BHT). Figure courtesy of A.W. Chesterton Co.
He suggests: “Organizations should vet opportunities where use of EAL-certified lubricants is financially viable for performance needs. Hydrolytic and oxidative stability of synthetic esters are advantageous in wet environments, but their excellent high-temperature stability could be immaterial in some applications. Therefore, one also should account for ease of system access, cost of maintenance, lifetime expectations and economies of scale for their use on large, isolated and/or closed systems to recognize a broader perspective. Rather than purchasing multiple lubricants, an industrial plant could simply use an EAL lubricant even if it is over-engineered for some applications to reduce stock keeping units.”
Bergeron adds: “In industrial applications such as chains, wire ropes, small- to medium-sized open gears, bearings and bolting systems, there are other limitations. Sometimes end-users and OEMs restrict halogens, low melting point metals, heavy metals, nitrites and nitrates. The nuclear industry often caps sulfur content and may require product certification from a third party. Sulfur containing compounds, including dithiophosphate ester derivatives as shown in Figure 1, may need to be avoided.”
In addition, he continues: “New products launched in Europe must account for REACH regulations. In some instances, raw materials that derive from the region are used and products manufactured locally as well. Otherwise, new products may be developed and initially shipped to European Union (EU) countries per logistic requirements and within raw material registration band limitations. Diligence and scrutiny should be taken to review SDSs of additive packages available in EU for SVHCs, including butylated hydroxytoluene (BHT), which is shown in Figure 1.”
Difficulty exists incorporating additives into some lubricant systems (e.g., water, solvents, oils, hybrids, greases). Bergeron explains: “Attaining solubilization of additives and uniform distribution of particles in formulated products sometimes requires trial and error. At the component level, confirmation that micelles are sufficiently broken and distinction between thixotropic versus polymer degradation can be tedious. Dissolving additives in volatile solvents or solvent blends requires use of timed mixing, thermal control and system design while reflecting on safety concerns. Precipitation rates are more pronounced with larger diameter particles in low density fluids and magnify during agglomeration if interfacial forces with proper dispersants, pH, etc., are not refined. The terminal velocity of a particle falling in a fluid, v (m/s), is given by Equation (1) after solution to Stokes’ Law.
2 Here, r
p, r
f, m, g and R refer to density of the particle (kg/m
3), density of the fluid (kg/m
3), dynamic viscosity of the fluid (kg/m
.s), gravitational acceleration (m/s
2) and particle radius (m), respectively.”
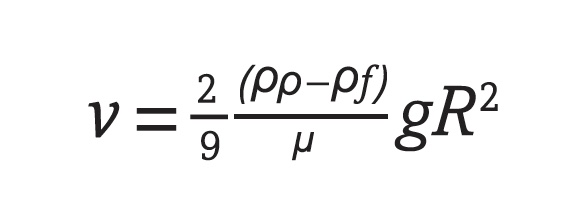
(1)
He adds: “In many instances, the answer resides with appropriate processing at the R&D, pilot and manufacturing level. The type of equipment and scale are relative and absolute among organizations. Twin-screw extruders, homogenizers, planetary mixers, high-speed mixers, dual shaft mixers, versators, heating elements, wiper blades, ultra-filtration systems and so forth are often critical on a production floor but not always available in a lab environment. The linch pin is often an excellent, hands-on process engineer.”
Formulators need to be mindful of interactions that may occur when lubricants are taken to the field (storage conditions, aging, application variation, contamination from previously used lubricants, etc.). Bergeron explains: “Some fundamental challenges arise during unexpected field test or post launch. Color change due to AO activity may occur when the sample is exposed to higher temperature conditions, oxidizing environments or light if stored in a transparent container or used in an open system. Additives may crystallize when exposed to low temperature and require thermal equilibrium and remixing by the end-user. Paneling or bloating of plastic containers (e.g., high density polyethylene [HDPE], polyethylene terephthalate [PET]) is possible and should be evaluated with the oil (e.g., ester, mineral oil, naphthenic) or solvent in advance. Finally, compatibility of the lubricant with specific process fluids and metallurgy should be handled by inquiries to application engineering prior to use.”
When formulating with esters to improve thermal-oxidative performance, STLE member Tyler Housel, sales director, Zschimmer & Schwarz, recommends starting with AOs: “Even with the most stable synthetic esters, AOs are needed to formulate long-life lubricants that resist thermal and oxidative degradation. Aromatic amines and phenolic AOs are readily soluble in esters and are highly effective in extending the lifetime of the lubricant. There has been debate about whether combinations of amine and phenol AOs give a synergistic boost. I have seen surprising results in both directions, so I recommend testing under conditions that closely mimic the final application.”
Dr. Jun Dong, global technical manager, Business Unit Fuel and Lubricant Additives, Songwon, suggests that when adding AOs in more refined Group II and Group III base fluids, some considerations should be made: “Group II and Group III base oils are usually selected for higher temperature, more service demanding applications. From a performance standpoint, amine type AOs such as alkylated diphenylamines would usually perform better than the phenolic types in these base oils, thus usually selected as the primary choice. Further consideration would be given to the solubility. Highly refined base oils tend to provide less solubility to the additives. Some solid AOs may have solubility or long-term stability issue in these types of base oils if the formulation is not properly crafted.”
There are some basic screening tests that Dong recommends for optimizing AOs with other additives for oxidative performance: “Performance optimization should be conducted in the formulation that the AO is intended for. To begin with, pressurized differential scanning calorimetry (Pressure Differential Scanning Calorimetry [PDSC], ASTM D6186) would be a useful tool for general purpose screening. For crankcase oils, Thermo-Oxidation Engine Oil Simulation Test (TEOST 33C, ASTM D6335), Moderately High Temperature, MHT-4 (ASTM D7097) and Thin-Film Oxygen Update (TFOUT, ASTM D4742) are important tools. Rotating Pressure Vessel Oxidation Test (RPVOT, ASTM D2272) and Turbine Oil Oxidation Stability Test, TOST (ASTM D4310, ASTM D7873) are commonly used for industrial lubricants. For transmission fluids including those for the electrified vehicles, DKA friction bench test (CEC-L-48) is usually used. The ASTM D942 and PDSC-based ASTM D5483 are employed for greases.”
A lubricants formulator also needs to keep in mind some common antagonism factors for AOs. Dong says: “AO antagonism may occur when two or more AOs are incorrectly used. The issue may rise due to overdose, incompatible chemistries or incorrect ratio. It also is noteworthy that reduced performance can be caused by the dilution effects on the dominant AO from the lower performing counterpart, which may be interpreted as antagonism.”
Dong explains that when selecting AOs used in biobased fluids, there are different considerations to be made: “Different AO types and chemistries would display different performance levels in biobased fluids. Significantly higher treat levels may be required if the finished lubricant is intended for use at elevated temperatures with prolonged service life. Solubility is generally of less concern. An AO being on the LuSc-list may be a requirement for making environmentally friendly lubricants. AO selection would be dependent on the intended applications, operating temperatures, lifespan and also the oxidation performance requirements or specifications that the fluid needs to meet.”
To the point of AOs selection, specifically when it comes to a finished fluid performance, one question that stands out is whether to incorporate a synthetic ester over a vegetable-based ester. Housel adds that the right answer lies with the chemistry: “Vegetable oils are triglycerides—meaning that they have three fatty acids bonded to glycerin through ester bonds. A trimethylolpropane (TMP) polyol ester can have the same three fatty acids esterified to TMP. Figure 2 compares the chemical structures of a triglyceride and TMP ester. They appear almost identical, and, in fact, the viscosity, lubricity, flash point and many other properties are very similar.” However, he continues: “The central carbon of a TMP ester is bonded to four other carbon atoms while the middle carbon in a triglyceride has a carbon-hydrogen (C-H) bond. This C-H bond is the weakest bond in the triglyceride and is readily oxidized. It only takes moderate heat to break the C-H bond in a triglyceride. By avoiding the weak C-H bond, polyol esters are significantly more stable. To paraphrase the old saying, a triglyceride is only as strong as its weakest bond.”
Figure 2. Comparison of the chemical structures of a triglyceride and TMP ester. Figure courtesy of Zschimmer & Schwarz.
For fluids used in extreme environments, there can be some challenges with incorporating esters. Housel says: “The biggest challenge is choosing the right ester. Esters can be made from a wide variety of feedstocks (acids and alcohols) and the ingredients determine characteristics such as viscosity/viscosity index, volatility, high temperature/oxidative stability, low temperature fluidity, biodegradability, lubricity, hydrolytic stability, etc.” He adds: “The first step is to identify possible failure modes that the lubricant must withstand,” he continues, “then the ester is designed to maximize performance in those areas. Once the formulator has the right ester, the lubricant is optimized with additives.”
Lubricant enhancement with additives to yield an optimized tribosystem is critical. Bergeron provides insight: “A superior performance lubricant should increase chain life while reducing energy consumption. It needs effective dispersive and detergency properties, as well as sufficient AO, AW, RI and EP performance, to operate in industrial environments. These attributes allow its use on drives, pins and bushings in systems to remove dust and dirt and rust as shown on a hoist in a shipyard
(see Figure 3a and 3b).”
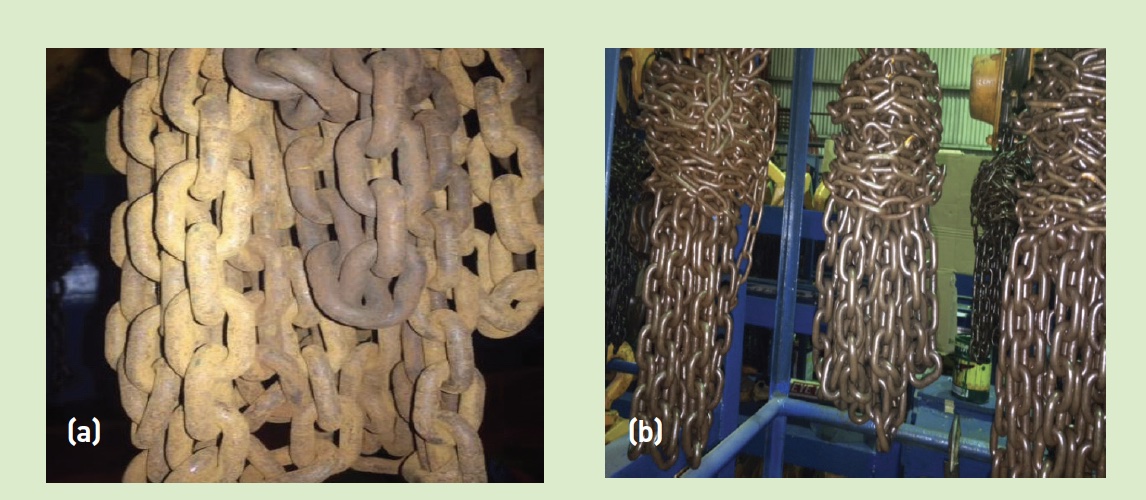
Figure 3. (a) Dirty chains prior to use of lubricant and (b) cleaned chains after use of lubricant. Figure courtesy of A.W. Chesterton Co.
He continues: “A versatile chain, cable and gear lubricant may be designed using a semi-fluid polymer base, calcium sulfonate complex (CSC) thickener and specific additives to yield 000 NLGI consistency by ASTM D217, 800 kgf weld load by ASTM D2596 and >1,000 hours corrosion resistance by ASTM B117. A diluent version of the product in a solvent would flow readily into tight tolerances, remain with slight tack and no drip during operation and reduce contamination. The need for flammable pictogram is eliminated and global shipment logistics simplified if a flash point > 62 C is maintained.”
Indeed, considerations for an optimal additive system are not only application- and performance-specific, but they are rather holistic and account for all touch points. For example, according to STLE member Dr. Clifford Pratt, manager rust preventives, technical service, Lubricant Additives Division, King Industries Inc., when it comes to formulating finished products that call to provide superior rust prevention, there are numerous additive performance considerations that need to be made:
Type of metal that is to be protected
•
Steel
°
Carbon steel—most common
°
Alloys steel
°
Stainless steel
°
Tool steel
•
Aluminum
°
6061
°
7075
°
3003—most common
°
6063
°
2024
°
1100
•
Galvanized
°
Hot dipped
°
Cold dipped
•
Black iron.
Performance criteria
•
How long to be stored
°
Inside
°
Outside
•
Testing specifications
°
Humidity cabinet
°
Salt fog
°
Stack staining
°
Kesternich cabinet
°
Water separation
°
Rust preventative (RP) removability.
How is RP to be applied
•
Dipped
•
Sprayed
•
Brushed.
Base fluid types to be used
•
Oil/solvent
°
Oil (Note: Naphthenic and Group I paraffinic oils are typically the best options.)
°
Solvent (Note: The lower the flash, the better the performance.)
°
Water
–
Tap
–
Distilled
•
Water/emulsion
°
Oil.
Pratt states that there are some challenges related to incorporating additives into different fluids (water, solvents, oils and hybrids): “Rust preventive fluids are combinations of additives and a base fluid. As such, the combination must be optimized to achieve the best possible results. Often there are significant variations in performance of rust preventive additives in different types of base fluids. The additive response varies in different fluids, and, in general, the effectiveness of rust preventive additives declines as the degree of refining of the base fluid increases.” Dr. Pratt describes each fluid’s challenges separately.
Mineral oils
Among mineral oils, naphthenic and Group I paraffinic oils are generally best for formulating rust preventive fluids. The reason for this is that they are the most polar of the mineral oils, and they have the best solubility characteristics. Naphthenic oils have ring structures and are more abundant in saturated structures compared with more highly refined mineral oils. For more highly refined oils such as Group II and III mineral oils and PAOs, additives may appear to be fully solubilized, but it is often determined by test performance that the additive response is less effective in these less polar base fluids.
Solvents
Solvent-based rust preventive systems perform similarly to oil-based systems. However, they tend to be more effective than oil-based systems because the rust preventive additives are easier to dissolve and disperse in the bulk fluid. This tends to allow for more consistent substrate coverage of the rust protective film, and this translates into higher test performance. The use of solvents also allows for thicker coatings to be deposited, which can improve performance as well. However, using more refined solvents hurts additive solubility, which is undesirable.
Hybrid oil/solvent combinations
The combination of solvent with an oil often is significantly more effective than using either alone. With the combination, it is possible to dissolve and disperse the additives and then apply the rust preventive film more consistently to the metal surface than with oil systems alone. Additionally, with the combination of oil and solvent, the deposited rust protective film is a more effective barrier to moisture, which increases protection, notably in salt fog testing. The downside of this compared to solvent systems alone is that the deposited protective film is oilier. This may lead to problems with parts storage or trapping contaminants or dirt, which can disrupt the protective film and lower performance.
Aqueous
Aqueous formulations can be either clear solutions or milky emulsions. Formulating aqueous rust preventives is similar to formulating oil and solvent systems, where it is necessary to solubilize and completely disperse the rust preventive additives. This is accomplished through the careful selection of specific chemistries. A major difference is the type of performance generated by the different formulation types. Clear solution rust preventives (often used in indoor, sheltered conditions) give shorter, less robust protection due to the thinner protective films formed because of the lower additive levels in the solution. Emulsions give higher performance because a greater variety of hydrophobic barrier components can be added to the formula and encapsulated in the emulsion’s micelles. The downside of these systems is that it is often very difficult to stabilize emulsions, and changes in water hardness can have a significant impact on product performance as well.
According to Pratt, there are few examples of a mechanism of drop out that is common in rust preventive fluids:
1.
Probably the most common cause of dropout in a rust preventive fluid is the interaction of different components that are present in it. Many rust preventives have an acid number, which is essential for good corrosion protection. Combining a basic component with the rust preventive can lead to an acid-base reaction, which can form polar salts that will drop out of solution in a non-polar base oil environment. To avoid this interaction, it is recommended to either remove the basic component or switch to a neutral or even slightly basic rust preventive additive. One must consider that switching to a neutral rust preventive additive may not give the desired corrosion protection for a specific application.
2.
Sometimes AW agents are added to rust preventive f luids. AW agents that are of the amine phosphate type will react with metal sulfonates and cause dropout. We normally recommend switching to a non-amine phosphate AW agent to prevent this from happening.
3.
Salicylates and sulfonates also can interact and cause dropout to occur.
4.
Oxidated petrolatum and waxes are commonly used as film formers to help aid the rust preventive additive in corrosion protection. When immediately formulated, petrolatum and wax containing rust preventives tend to be completely soluble, but, over time, a wispy dropout may form. This can be caused by some of the shorter chain, more polar compounds in the wax to drop out of solution. This usually does not affect the rust preventive corrosion performance but may be important if an aerosol application is desired due to possible clogging of the nozzle. Solubility issues using high wax concentrations in straight oil formulations also can occur. To avoid this, one can try adding a non-polar solvent or reduce the amount of wax used. Sometimes increasing the amount of the rust preventive relative to the wax content can help solubilize it. Also, the type of wax used can be important as well. Low melting paraffinic waxes tend to be more soluble in oil-only formulations as compared to higher melting microcrystalline waxes, which are better at forming thixotropes.
Summary
In the modern world of technology, the lubricants industry has risen to numerous challenges through improved base oils and additives. However, increasing environmental, safety, health and regulatory pressures will continue to limit new additive chemistry, leaving formulators to become even more creative, leading to exploring approaches to challenges while uncovering opportunities for innovation. The task to develop lubricant additive systems with optimized solubility, simultaneously high tribological characteristics, resistance to operational influences, extremely low toxicity, high biodegradability and global/ regional availability remains urgent.
REFERENCES
1.
Mang, T. and Dresel, W. (2001), Lubricants and Lubrication, Wiley-VCH, Weinheim.
2.
Lamb, S. H. (1945),
Hydrodynamics, 6th edition, New York: Dover, p. 599.
Dr. Yulia Sosa is a freelance writer based in Peachtree City, Ga. You can contact her at dr.yulia.sosa@gmail.com.