Sensors that detect vibration
R. David Whitby, Contributing Editor | TLT Worldwide September 2022
These are useful for vibration monitoring and balancing operations on rotating machinery.
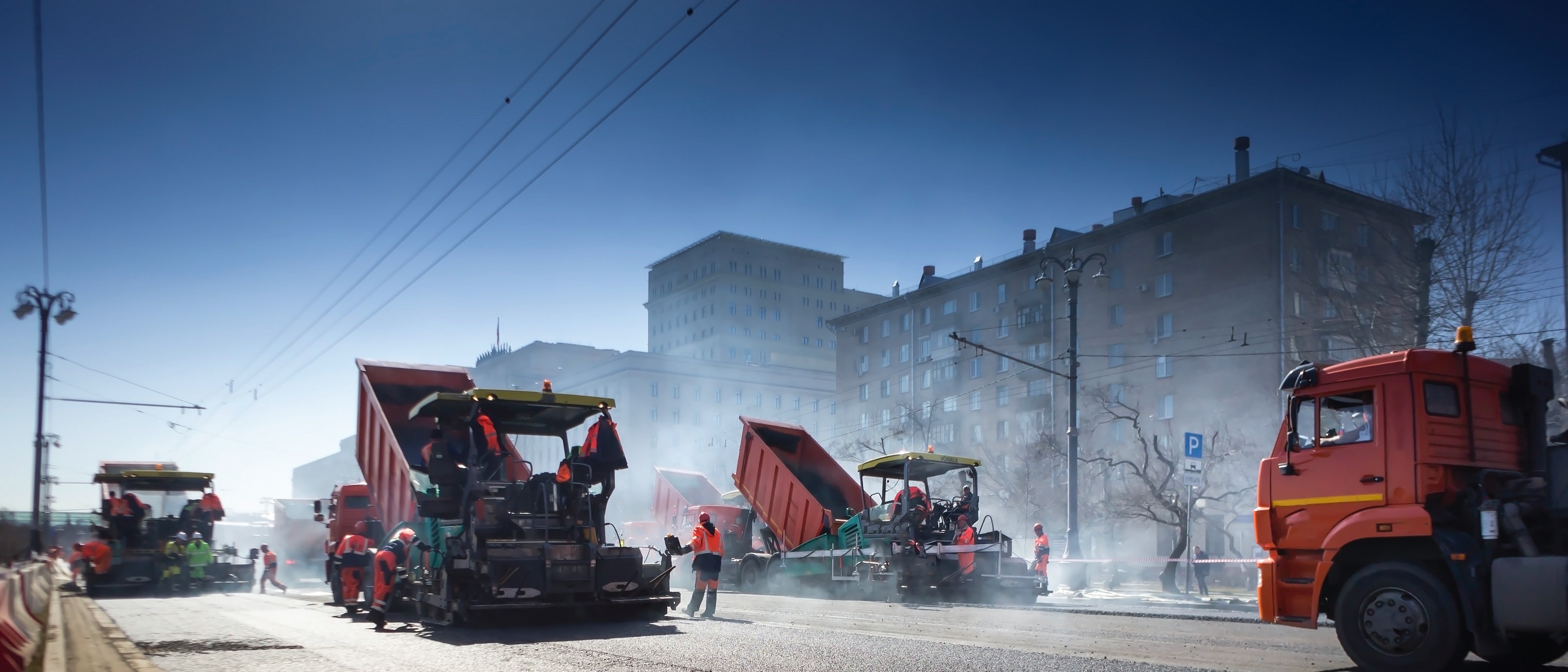
Vibration is defined in the Oxford English Dictionary as “an oscillation of the parts of a fluid or an elastic solid whose equilibrium has been disturbed or of an electromagnetic wave.” Webster’s International Dictionary has a very similar definition.
It is a physical phenomenon in which oscillations occur about an equilibrium point. The oscillations may be periodic, such as in a tuning fork, or random, such as the movement of a wheel on a gravel road.
In many cases, vibration can be desirable. Obvious examples include human voices, violin strings, mobile phones and television speakers. Unfortunately, when vibration occurs in operating machinery, it can be undesirable, resulting in wasted energy, causing unwanted noise and leading to increased rates of wear. Even in machinery that is stationary, for example, while being transported from a manufacturer to a user, unwanted vibration can cause fretting corrosion and wear.
Vibrations in machines could be caused by imbalances in the rotating parts, the meshing of gear teeth or uneven friction. Careful design of equipment and selection of materials is likely to eliminate or minimize unwanted vibrations. While vibration in equipment is often a normal part of machine operation, excessive vibration may be a sign of impending mechanical failure. If left unchecked, increasing vibration can cause a deteriorating fault condition, leading to component damage or eventual equipment failure.
Monitoring vibration is the best way to prevent or minimize catastrophic failures, in addition to helping to reduce downtime and lowering maintenance costs. A vibration sensor is the most effective means for monitoring vibration.
Vibration sensors detect one of three parameters representing motion, either displacement, velocity or acceleration. Velocity is the first-time derivative of displacement, and acceleration is the first-time derivative of velocity. Selection of a sensor proportional to displacement, velocity or acceleration depends on the type and design of the equipment to be monitored, the frequencies of interest and the signal levels involved.
Displacement sensors are non-contact devices that use eddy currents to detect shaft radial vibration, shaft/rotor position and clearance and rotational speed. They are also known as proximity probes or displacement probes and are typically fitted on machines that have sleeve/journal bearings.
Velocity sensors are useful for vibration monitoring and balancing operations on rotating machinery, being used for low to medium frequency measurements. They have lower sensitivity to high frequency vibrations compared to accelerometers. Traditional, “self-generating” velocity sensors use an electromagnetic (coil and magnet) system to generate the velocity signal, which gives a direct measurement of velocity. However, they wear out over time and are sensitive to mounting orientation. Piezoelectric velocity sensors (internally integrated accelerometers) have improved capabilities, are more rugged and are smaller.
Piezoelectricity (also called the piezoelectric effect) is an electric polarization (voltage) produced in certain crystals by the application of a mechanical stress. Piezoelectric accelerometers are the most versatile, reliable and popular vibration sensor for monitoring machinery. For a given mechanical acceleration level, piezoelectric accelerometers have a constant signal over a wide frequency range and are very useful for all types of vibration measurements. Acceleration integrated to velocity can be used for low frequency measurements.
A number of companies manufacture and market vibration sensors for numerous types of machines. One company in the UK designs wireless piezoelectric sensors used to monitor the condition of railway rolling stock. Sensors installed in motors, gearboxes and wheels are able to assess the condition of those components by detecting thermal and vibrational signals of mechanical defects in real time. They also are able to monitor the condition of the railway tracks. The railway networks of several countries, including the U.S., Australia and India, make use of them to varying extents.
One Swedish company manufactures electromagnetic induction sensors that convert vibrations into energy. These can be fixed to the wheels of many types of vehicles to monitor their position, in addition to the stresses on their bearings. The company’s sensors also are being applied in the mining industry, to detect unusual patterns of movement in machines involved in the crushing and transport of aggregates.
David Whitby is chief executive of Pathmaster Marketing Ltd. in Surrey, England. You can reach him at pathmaster.marketing@yahoo.co.uk.