TLT: What about tribology drew your attention in the first place?
Schneider: In 2005, I started to learn about this exciting scientific field at AC²T in Austria as a chemist. I was very lucky to have had the chance to work with tribology experts like professor Dr. Pauschitz and professor Dr. Franek at that time, who awakened my interest in tribology even more, as tribology is everywhere in our daily lives—in writing with our pens, in playing musical instruments and, of course, in many industrial applications such as automotive, lubricants and additive industry.
This interdisciplinarity of tribology fascinated me from this first encounter to the present day. All team members were motivated by working together with various highly qualified scientists (chemists, physicists, mechanical engineers) in one project and being able to solve the tribological issues successfully.
To summarize the diversity of measuring tribological phenomena, which inspires me in my daily tasks:
•
Application in different industries such as automotive industries, lubricant and additive producers, component producers, layer and coating producers
•
Different advantages for the industries such as improving their quality, quality control, meeting the challenges and competitive advantages.
However, the most important output of tribological investigations for any industry today is the impact on the environment such as less energy loss, less CO
2, less material loss, less heat emissions, less noise emissions and finally improving the energy and material efficiency.
TLT: What part of tribology is of special interest to you?
Schneider: As a chemist, improving the performances of additives and lubricants through tribological investigations is of most interest to me. Tribochemistry investigations help us to understand more about the interaction of different surfaces with lubricant molecules. For example, differences in load carrying capacities of a lubricant are most likely due to the formation of different tribolayers, where both physical adsorption and chemical bonding
are possible.
Fortunately, in one of my first projects, we searched for a new generation of additive for lubricants based on ionic liquids. After running the tribotests with SRV® (stands for schwingung [oscillating], Reibung [friction] and Verschleiß [wear]) and analyzing the tribofilm with X-ray photoelectron spectroscopy (XPS) or a raster electron microscope (REM), we were able to get more insights on the mechanism of the action of ionic liquids as additives.
1
Recently, by measuring the electrical contact resistance during the tribotesting with a special sensor, we were able to get more details about the time and the performance of the formation of tribofilm. The paper concerning the evaluation of electrical contact resistance during standard tribotesting was presented at the 2022 ELGI Annual General Meeting.
Furthermore, tribotesting is one of the most useful parts of tribology. It is not only the matter of measuring friction and wear values but to investigate the whole tribosystem in the lab scale with operating conditions very close to field application. In most cases, the number of intensive rig tests and consequently time and costs can be reduced. This can be done with a highly qualified and versatile tribometer like SRV®, based on my experiences
(see Figure 1). A few interesting examples of my recent project concerning tribotesting involve the following:
•
Condition monitoring of lubricants as a “machine element” in a tribosystem is important for ensuring the reliability of a system. The tribological performance of used lubricants (friction and wear) is usually not taken into consideration in condition monitoring tests and consequently in the assessment of the quality of lubricant in the machine.2
•
The developed short and repeatable test method including tribological quantities complete the functional profile of an operational lubricant. It helps operators to ensure safe and reliable operation by making the right decision at the right moment.
•
The elastomer compatibility of lubricant oils is normally tested according to ISO 1817 under static conditions. Sealing’s damages caused by tribological dynamic issues can often be observed in machinery. These damages result not only from the sealing material but also from the counter surface, its lubrication and type of lubricants and the sliding speed as well as other parameters.
Figure 1. Tribotesting with SRV®5 machine.
A new developed method, evaluated with SRV®, could offer advantages such as the inclusion of the tribological dynamic components, which are frequently encountered in practice, or is time saving as an added value in the testing of compatibility of polymers with the lubricants. This method also was presented to the public at the International Colloquium Tribology Conference hosted by TAE in January 2022 and co-authored by Felix Zak.
TLT: Please describe your career journey. This can serve as an inspiration to young women who want to pursue STEM careers.
Schneider: After my journey of tribology research in Austria, I started working at Optimol Instruments in Germany and have been there since 2017. Together with experienced tribologists like STLE members Gregor Patzer and Dr. Mathias Woydt, we developed application-oriented test methods for the industry. We published the new methods and presented the application-oriented results at conferences such as the STLE Annual Meeting, NLGI Annual Meeting, ELGI Annual General Meeting, World Tribology Congress (WTC), OilDoc Conference, etc. It is great and motivating to see that the results of our work and developed methods find acceptance in the industry and can be used in a short time.
Since 2005, when I started working in the field of tribology, taking part in various tribological conferences and presenting my research results, I noticed that this is a male-dominated field of science. At the 2022 ELGI Annual General Meeting in Hamburg, Germany, I realized that, fortunately, the number of women who were participants as well as speakers had increased. I am sure that this trend will continue in the future. I always try to motivate young women in school to go for technical sciences and will continue to do so, especially for the field of tribological science. At AC²T research and at Optimol Instruments, I always work with students and support them in learning more about tribology. We had many students writing their bachelor’s or master’s thesis in doing research work with Optimol Instruments and some of them directly with me
(see Figure 2).
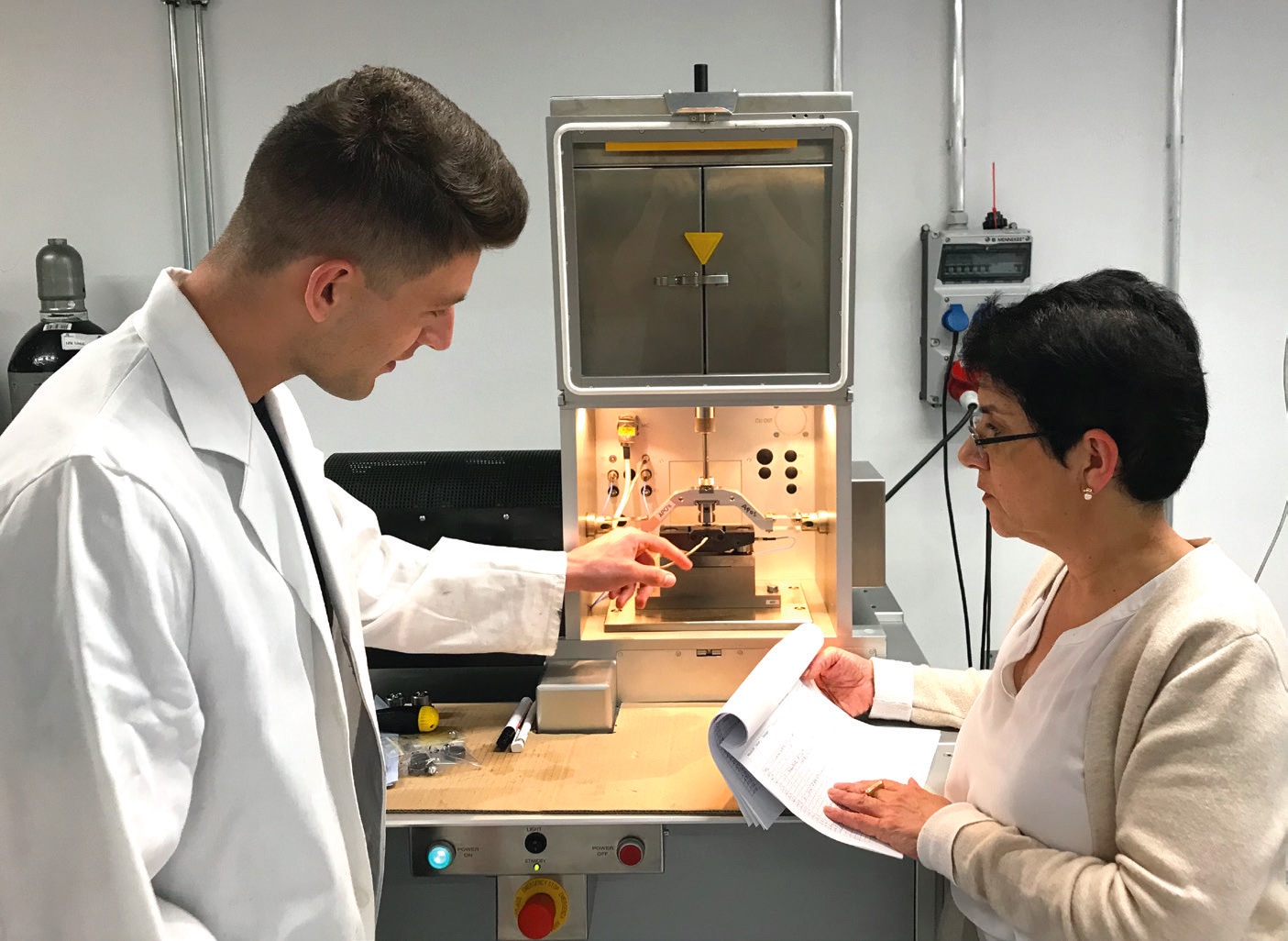
Figure 2. Ameneh Schneider in discussion and working with her undergraduate student.
I am now active in two working groups (ELGI and ALIA) regarding tribotesting methods. It is the perfect platform to share ideas and results with other experts.
Additionally, to develop new testing methods, I am responsible for consulting our customers to get the best machine configuration for their tribological issues in the field of lubricants and additives.
TLT: Describe a project you are currently working on and how this project will impact or help the grease industry.
Schneider: Greases are the most versatile and functionalized lubricants, and they can be used in a wide range of applications and conditions.
It is well known that lubricating greases and lubricating oils behave differently in tribological contacts. In the last five years, we worked with some lubricating grease manufacturers in different projects. There are various lubricating grease types with complex behaviors depending on the type and concentration of thickeners, additives and base oil viscosities. Fortunately, there are many standard test methods with SRV®5 for testing lubricating grease performances.
2
The future of grease development is moving toward energy efficient greases. Optimization of bearing lubrication is predicted to improve energy efficiency, because lower friction greases mean range extensions for electric vehicles. In addition to the linear oscillating motion of the ball on disk with SRV®, a new adapter has recently been developed to determine the friction under rolling motion. This special method can distinguish between rolling friction and the resulting wear of the formulated grease. The test method is highly mature as draft ASTM WK71194. Rolling friction can be simulated and measured to the 5th decimal place.
3
The feedback and interest of the industry were very good, and this method is on its best way to be established as an ASTM standard method. We will continue to investigate this new method because the first investigations and comparisons have shown good correlation with the results of FE8 tests. We hope that by the end of 2022 there will be a prescreening method for FE8 tests for greases like the one for gear oils concerning FZG prescreening tests. The SRV® users appreciate and use FZG prescreening worldwide, and I hope that will be the case for FE8 and greases in the future as well.
A current new project with greases is about grease applications at deep temperatures down to -45 C. The additional measurements for SRV®, which might be very helpful in this project, are electrical contact resistance and acoustic emission values. These investigations might help the grease producer to differentiate easily between the quality of formulated special greases for the application at a low temperature only with one tribotest.
TLT: Are there any other experiences or research applications of yours that might be helpful to our readers?
Schneider: One experience, which I would like to share, is the experience with a twine-disk machine. In one exciting project, Woydt and myself investigated the performances of different greases in rail wheel applications by using the twine-disk machine (for determining the tribological profile under slip-rolling and high load). The slip-rolling tribological tests were carried out on a twine-disk tribometer. It consisted of a spherical and a cylindrical disc with the same outer diameter slip-rolling against each other on their circumference as shown in Figure 3. The two disks are mounted on two individually driven shafts. Synchronous or asynchronous operations at the contact surfaces are possible as different rotational velocities, and slip ratios can be set for each of the two disks, because each shaft is driven by a high-speed step motor, which are synchronized by a computer. With the geometry used, it is possible to perform tests up to an average Hertzian contact pressure of P
0mean = 2.62 GPa (F
N = 5.000 N or P
0max = 3.92 GPa).
Figure 3. Investigation on greases for rail wheel with a twine-disk machine.
For the purposes of railway greases, two different test modes are appropriated:
1.
Retentivity (residence time) test in which the retention of the lubricity (or number of wheel passes) is measured at a fixed slip-ratio and speed. This mode also may be seen as a lubrication starvation test, where the test is run until all of the grease is consumed. This is indicated by an increase in the coefficient of friction.
2.
Traction curve, where the variation of the coefficient of friction is recorded versus the slip ratio (or creep) at a constant rotational speed.
The investigated greases were differentiated by their form and evolution in traction curves. The impact of water on traction curves for individual greases was quantified as well. Some railway greases offer remarkably long retention of lubricity.
The newest developed method concerns the evaluation of tribological performances of metalworking fluids and coolants. Writing about this amazing project will exceed the time frame, but we will publish a paper about this method soon.
REFERENCES
1.
Schneider, A., Brenner, J., Tomastik, C., Dörr, N. and Franek, F. (2009), “Capacity of selected ionic liquids as alternative EP/AW additive,” Conference Proceedings, ECOTRIB 2009, Edizioni ETS, Pisa, Italy, 07-10.06.2009, ISBN 978-884672426-7, pp. 923-929.
2.
Schneider, A. and Woydt, M. (2021), “Tribological performance of greases – different tribological test modes,”
NLGI Spokesman, 85 (5). Available
here.
3.
Schneider, A. (2018), “Rolling grease test adapter offers new test opportunities,”
Lubes’N’Greases EMEA, 12 (4), pp. 32-39. Available
here.