TLT: What have been the key factors that have kept you in the lubricant industry for 30 years?
O’Malley: The wide variety in my jobs has been one key to keeping my interest. I feel very fortunate that I was able to see many aspects of the lubricant business. I started in the R&D lab formulating lubricants and was able to build a solid base in lubricant fundamentals. I found the synergistic effects of different additives and their interactions with different base oils to be fascinating. Developing new products using innovative combinations of ingredients that improved performance in the field was very fulfilling. I have seen so much formulation development in the past 30 years. There are always new base oil and additive technologies being developed to improve different aspects of lubricant performance.
After spending time formulating products, I worked in a technical support role including troubleshooting problem applications. Early in my career, I was able to visit job sites and see difficulties firsthand. That was valuable experience for me. I learned to work with different customers and OEMs and develop solutions that had a real and positive impact on their businesses.
Working in small companies, I have been able to wear many hats, including raw material qualification, procurement, lubricant selection and managing different sized accounts from small local customers to very large global OEMs. I gained experience being a business team leader. I’ve been able to work with engineers, service people and business leaders from a wide variety of backgrounds, which has been very enjoyable. The relationships and friendships with customers, suppliers and distributors around the world is the part of my career I cherish the most.
After working primarily in North America for the first half of my career, I started to work with overseas accounts. Gaining a global perspective on the lubricant industry and getting the opportunity to visit so many different places around the world has been an excellent experience. I find it very interesting how businesses in different cultures operate.
Helping to build a new company from a startup into a successful lubricant business working with a team of friends and experts in our field has been my favorite experience to date. I really appreciate the opportunities the lubricant industry has provided to me.
TLT: With all your experience working with global compressor OEMs, can you comment on what the applications have in common? Is there anything that
is different?
O’Malley: There is a common need to select lubricants that maximize bearing life at the compressor operating conditions. This requires an understanding of how the gas and operating conditions will impact the lubricant. OEMs are typically focused on minimizing warranty issues while also maximizing efficiency and compressor performance. End-users want lubricants that require minimal service, provide maximum reliability and are cost effective in the application. Being able to design products that are reliable, offer long life and help compressors and systems to operate at maximum efficiency is of key importance in nearly all OEM compressor applications.
Some differences in lubricant requirements depend on the gas being compressed and the type of compressor being used. The applications I’ve been involved with include refrigeration, air, hydrocarbon gas and process gas compressors
(see Figure 1).
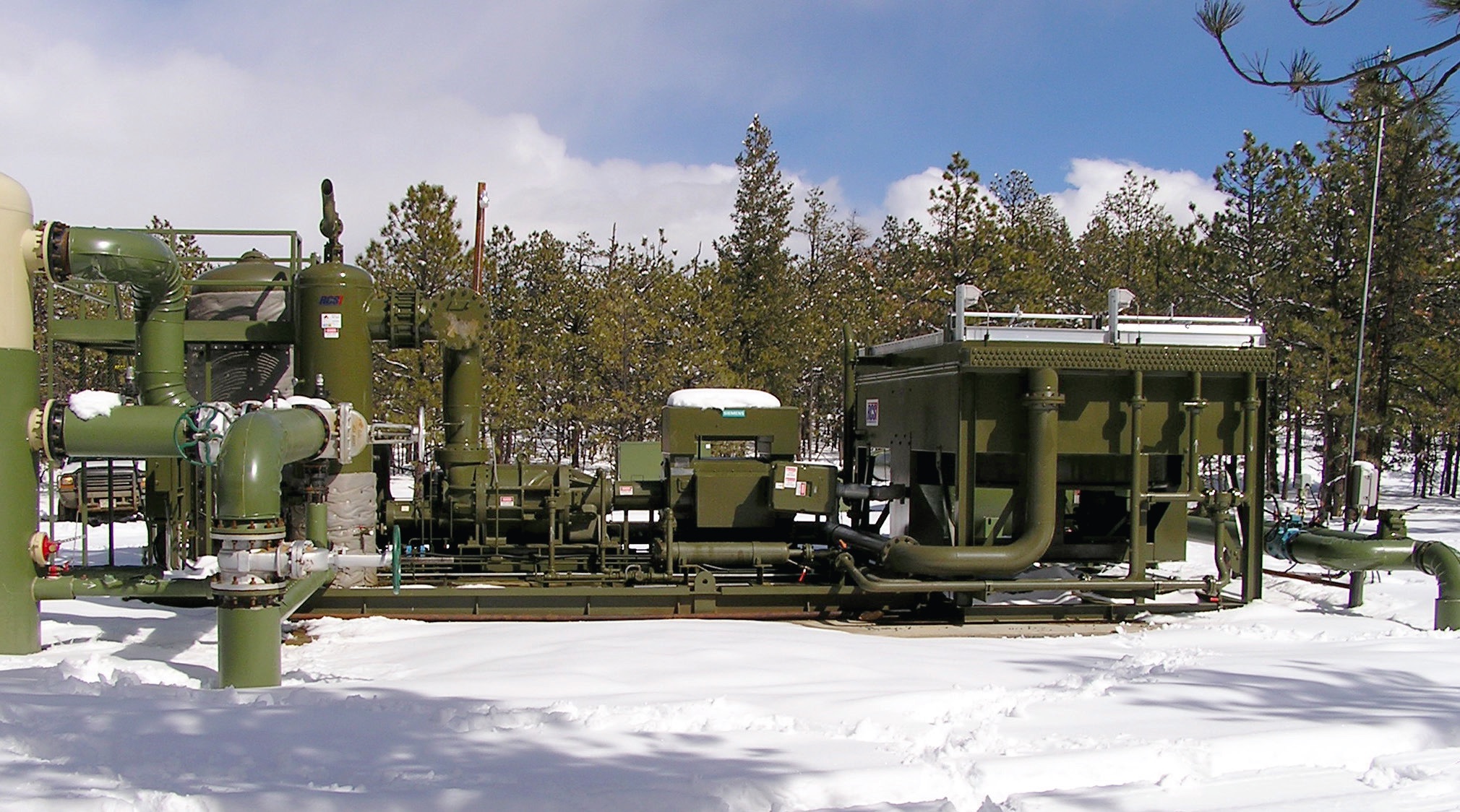
Figure 1. A gas compressor operating in a remote, low-temperature environment.
Gases that are soluble in the lubricant such as hydrocarbons, many refrigerants and process gases will dissolve in the lubricant and cause the viscosity to drop. The amount of gas that dissolves in the lubricant depends on the pressure and temperature in the compressor. A good deal of effort goes into physically measuring the amount of gas dilution at different conditions or modeling this dilution using vapor pressure and temperature equilibrium calculations. The goal is to understand the operating viscosity of the lubricant in the compressor and make sure it can properly lubricate the bearings
(see Figure 2).
Figure 2. A viscometer from Sean O’Malley’s oil laboratory.
Air and inert gases cause minimal dilution of most lubricants, so dissolved gases aren’t as much of a concern. But the operating temperature is still impacting the lubricant viscosity. It is important to work with the compressor OEMs to determine the acceptable viscosity required and the temperature range of the machines. This information allows me to select lubricants that meet their needs.
It also is important that the entire system be considered, not only the lubrication of the compressor. For example, in refrigeration applications, lubricants must lubricate the compressor, but also must allow the cold side of the system to operate efficiently. Much of the work with refrigeration oils centers around making sure the lubricant doesn’t cause issues in the evaporator and can return to the compressor. Properties such as liquid refrigerant miscibility with the lubricant and relative density between the lubricant and the refrigerant are very important when making a lubricant selection.
The main challenges in air compressors include maximizing lubricant life and optimizing compressor efficiency while not compromising the lubrication or cleanliness of the system
(see Figure 3). Much of the development work done on air compressor lubricants includes formulating for maximum oxidative stability. Matching the lubricant viscosity to the compressor operating conditions is important for efficiency optimization.
Figure 3. An air compressor factory filled with synthetic lubricant.
Hydrocarbon and process gases have their own challenges. Besides lubricant dilution, corrosive gas mixtures, including hydrogen sulfide, carbon dioxide and moisture, are often present. Protecting the system from corrosion is critical. Selecting the correct rust and corrosion inhibitors for this aggressive environment is a major challenge. Many of these applications are very difficult and costly to shut down, so long lubricant life becomes extremely important to the end-users in the field.
TLT: Do you have any examples where lubricant technology has changed to meet updated compressor lubrication demands?
O’Malley: Synthetic lubricants are becoming much more widely used than when I first began working in this industry. The ability to tailor the base oil characteristics to the specific bearing requirements and the batch-to-batch consistency with synthetic lubricants are major advantages. At the same time, additive technology has greatly improved, so lubricant life continues to be extended and properties such as corrosion protection improved.
In refrigeration compressors, the refrigerant chemistry has changed, and this has forced the lubricant technology to change over time. Prior to the early 1990s, the refrigerants used were primarily chlorofluorocarbons (CFCs) like R-12 and hydrochlorofluorocarbons (HCFCs) like R-22. Most of the lubricants were mineral oils, which were miscible and compatible with the refrigerants. CFCs and HCFCs were found to be ozone depleting, and they were replaced by hydrofluorocarbons (HFCs) like R-134a. Mineral oils were not miscible with HFCs, and synthetic polyalkylene glycols (PAGs), polyvinylethers (PVE) and polyolesters (POEs) were developed for the application. HFCs have now been found to have high global warming potential. New hydrofluoroolefin (HFO) refrigerants and a return to natural refrigerants like ammonia, carbon dioxide and hydrocarbon gases are the focus of much of the new development in the industry. In some cases, the same lubricants used for HFC will work with HFO refrigerants. Other cases require different tweaks to the lubricants so they can properly lubricate the compressor without causing other problems in the system. Natural refrigerants are being considered for systems where they previously were not a viable option, and again synthetic lubricants are the focus of much of the lubricant development in this area.
In air compressor lubricants, another major change in technology has been the ability to formulate very long-life synthetic lubricants that provide superior cleanliness and wider operating temperature ranges than mineral oils that were previously used. We’ve seen the air compressor lubricant market in North America go almost exclusively to synthetic lubricants. We’re seeing pushes now in other markets that have been dominated by mineral oils starting to convert to synthetic lubricants. I believe this change is inevitable because of the advantages that synthetics offer.
TLT: Looking to the next 10 years, do you have any opinions on what might be the new opportunities for compressor lubricant development?
O’Malley: I believe compressor efficiency is going to be a focus by the OEMs as they look to minimize energy costs and the environmental impact of energy production required to operate the compressor. Lubricants are going to be called on that enable maximum compressor efficiency while minimizing bearing and other compressor and system failures.
I think we may see a change in sustainable lubricant initiatives that focus more on synthetic lubricants that extend lubricant life and reduce petroleum usage. I think a wholistic carbon footprint and impact on climate change will be considered, including energy requirements required to produce lubricants and logistics impacts to transport lubricants. Lubricants with longer drain intervals will be viewed favorably. Producing products that are easily recyclable, non-toxic and non-hazardous will become more important over time.
The ability to remotely monitor machine performance should continue to improve, and the data provided will be a very valuable tool in optimizing lubrication. Remote online oil monitoring could have a major impact on our knowledge of the lubricant chemistry during operation over the lubricant’s lifetime. Being able to monitor large populations of compressors and measure impacts of lubricant formulation changes is an exciting opportunity.
We also continue to see trends toward higher pressures, more extreme temperatures and longer oil drain intervals. This creates great opportunities to improve lubricant formulations that excel in the most demanding lubrication environment. I feel like we’re still at the beginning stages of developing lubricants. Products are going to keep getting better over time. From that standpoint, the lubricant industry is very exciting.
You can reach Sean O’Malley at somalley@xaerusfluids.com.