Meet the Presenter
This article is based on a webinar presented by STLE Education on April 14, 2021. Troubleshooting Metalworking Fluid Field Problems - Part 2 is available at www.stle.org: $39 for STLE members, $59 for all others.
STLE member Patrick (Pat) Brutto is founder and technical application specialist for Faith-Full MWF Consulting, which provides services to all segments of the metalworking fluids (MWFs) value chain. Prior to founding this company, Brutto spent the early part of his career with Pennzoil Products Co. as an industrial grease formulator and most of his career serving in R&D and global technical services with ANGUS Chemical Co., a producer of specialty additives for MWFs and many other markets. He also provided field technical services for Hangsterfer’s Laboratories, a U.S.-based producer of MWFs.
Brutto holds a master of science degree in chemistry from DePaul University in Chicago, and he is an STLE Certified Metalworking Fluid Specialist™ (CMFS). He has served the STLE Chicago Section several times as program chair and education chair, and he also was section chair from 2012 to 2013. Brutto currently serves as vice chair of STLE’s Metalworking Technical Committee.
You can reach Brutto at patrick.e.brutto@gmail.com.
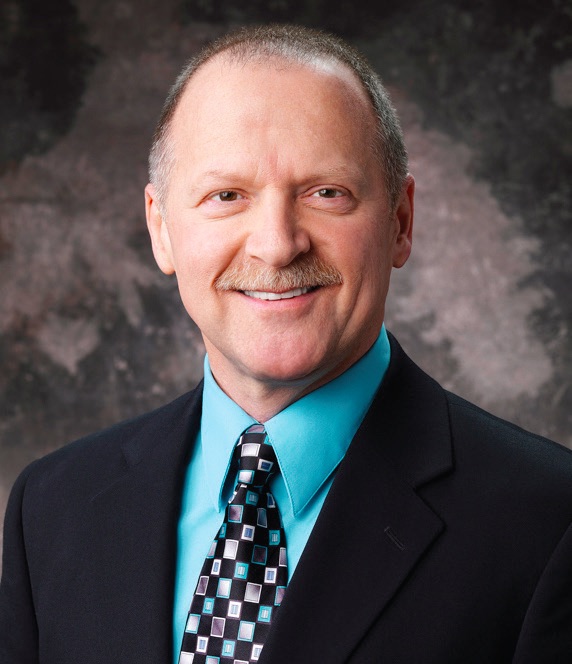
Patrick Brutto
KEY CONCEPTS
•
The right fluid formulation can improve performance and protect workers’ health.
•
Ongoing fluid maintenance and catching problems in the early stages helps keep problems under control.
•
Collaborations between end-users and fluid and equipment suppliers help keep machine operations, fluid formulations and maintenance practices working together.
Several problems related to metal-removal fluids (MRFs) can affect the cost per part in a metalworking operation, and these problems also can have a negative impact on working conditions. Identifying and solving these problems requires a systematic evaluation of symptoms, observations of the machinery and operating conditions and communication among the key stakeholders. Stakeholders include MRF suppliers (formulators, field services), suppliers of other fluids and chemicals (way lubes, hydraulic fluids, cleaners, biocides, etc.), end-user representatives (machinists, fluid and plant managers, health and safety officers) and equipment suppliers (tools, machines, filtration equipment, water treatment equipment, etc.).
This article is based on an STLE Webinar titled Troubleshooting Metalworking Fluid Field Problems - Part 2 and presented by Patrick Brutto, founder and technical application specialist for Faith-Full MWF Consulting. See Meet the Presenter for more information. This webinar focuses specifically on metalworking fluids while Brutto’s first webinar on this topic focused on operational factors.
The term “metal-removal fluid” (MRF) is often used interchangeably with the broader term “metalworking fluid” (MWF), which includes metal-forming fluids. The principles discussed in this article apply to all MWF types. Here, we review issues primarily associated with the MRF itself, continuing the troubleshooting information presented in Part 1 (published in the April TLT), which dealt more with metalworking operations. This article focuses on water-dilutable MRFs, which provide lubrication, cooling and chip removal for a variety of machining operations. End-users buy MRF concentrates, which they dilute with water, as specified by the formulator (typically 5%-10% concentrate, 90%-95% water).
Problem: Parts or machines are corroding or staining
Corroded or stained metal surfaces can be a sign that the MRF concentration is outside of the supplier’s recommended range. The MRF concentration should be checked using a refractometer at the start of every shift and adjusted as needed. Regularly checking the fluid pH, preferably using a pH meter, helps ensure that problems like biodegradation or fluid contamination are identified early, before the pH is driven out of range, resulting in corrosion or staining of workpiece and machine surfaces.
If the pH is below the range specified by the MRF supplier, adjustments to the fluid concentration might be needed. If the concentration is in range, the supplier may recommend a compatible pH booster that can be added to the fluid tank side. If the pH is above range, the fluid concentration might be too high. Partial dumping and refilling of the system with freshly diluted fluid at lower concentrations should be done until the concentration is in range.
Microbes can biodegrade corrosion inhibitors and form corrosive byproducts
(see Figure 1). If dip slide tests indicate unacceptable levels of bacteria or fungi, the fluid supplier might recommend adding a compatible biocide. The supplier also may recommend dumping and recharging the system with fresh fluid if microbial growth or other contamination is excessive
(see Minding the Microbes).
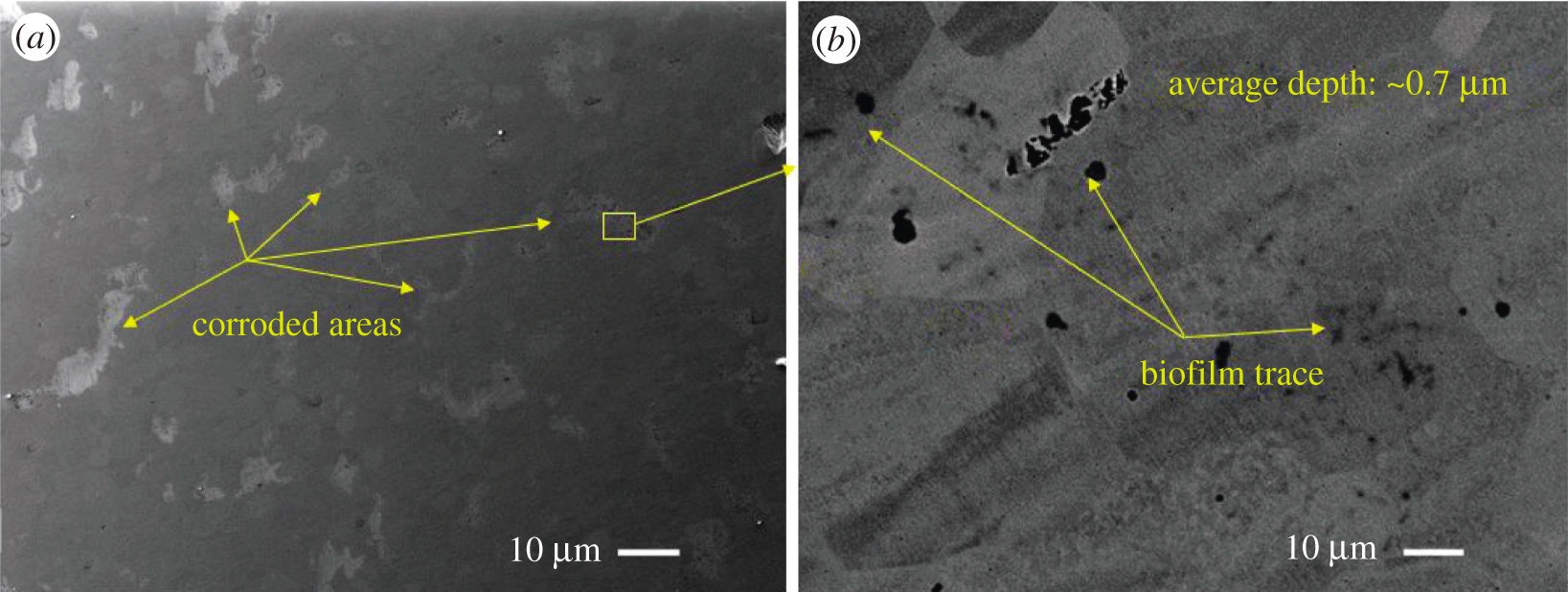
Figure 1. After six months of exposure to microbes, localized corrosion is evident in these SEM images of SS 420 stainless steel. Figure courtesy of T.T.T. Tran et al., Royal Society Open Science 2021, https://doi.org/10.1098/rsos.201577, CC BY 4.0.
Minding the microbes
Slimy or filamentous residues are generally the result of biofilms generated by microbial growth. Biofilms that form on workpieces or machines can create local environments that produce corrosion or staining
(see Figure A). Microbes can degrade or deplete specific components of the MRF, causing their concentrations to fall outside of the supplier’s specifications.
Figure A. A biofilm-coated sample of stainless steel, left outdoors for two months, demonstrates how microbially produced biofilms can set up conditions favorable to corrosion. Figure courtesy of Akiko Ogawa et al., MDPI Materials, 2020, CC BY 4.0.
If the fluid is still performing well, contact the MRF supplier to determine if a compatible tank-side biocide can be added. However, if microbial levels are high and fluid performance is decreasing, dump the fluid and mechanically remove biofilm from machine and sump surfaces, filtration equipment, slideways, sluices and circulation lines. Clean the system thoroughly with a biofilm remover and recirculate a compatible biocide solution, as recommended by the MRF supplier. Flush thoroughly with water and refill with fresh MRF. To prevent the problem from recurring, develop a fluid maintenance schedule in consultation with the MRF supplier.
Even if biofilm buildup is not evident, microbe levels in MRFs should be checked on a regular basis using dip slide tests. Dip slides are flat plastic slides coated with a microbial culture medium and sealed in sterile packaging. The slides are dipped into the MRF and then placed into an incubator to allow microbial colonies to develop for a specified amount of time. Check samples from multiple locations—sumps, fluid application areas, settling tanks and upstream/downstream of filtration equipment—since growth may not be evenly distributed.
If dip slide tests repeated over several weeks consistently indicate more than 100,000 colony-forming units per milliliter (CFU/mL) for bacteria or more than 1,000 CFU/mL for fungi, it is likely that fluid components have been partially degraded. The system should be dumped, thoroughly cleaned mechanically followed by a recommended quick-kill biocide solution, then rinsed and refilled with fresh MRF. Monitor the fresh fluid weekly for microbes (a pH change can be a symptom), and ask the MRF supplier for a tank-side biocide recommendation.
As a matter of routine, continuously recirculate the MRF, even when not in use, to aerate it and minimize growth of anaerobic bacteria that form odorous, corrosive, toxic hydrogen sulfide (H
2S). Regularly remove tramp oil to ensure air exchange at the surface; tramp oil films increase the risk of anaerobic (and aerobic) bacterial growth and H
2S formation.
Galvanic corrosion can occur when the same MRF is used to machine metal alloys having different electrochemical potentials. To minimize this type of corrosion filtration systems should be well designed and maintained to ensure that metal fines are being removed from the circulating fluid. All equipment, including sumps and sluiceways, should be cleaned and flushed regularly to minimize buildup of chips and fines. Fresh and used MRFs should be evaluated in the lab using a sandwich corrosion test with relevant alloy combinations. Fluid concentrations might need adjustment to reduce galvanic corrosion, or the fluid supplier might need to adjust the corrosion inhibitors, including any metal deactivators.
If corrosion or staining occurs when using a freshly diluted MRF, the formulation may need to be adjusted. To test the formulation, try to simulate the problem in the lab using relevant alloys and plant dilution water. If the lab simulation successfully reproduces the problem, further lab tests can help identify an appropriate solution. Possible solutions include increasing the oil concentration of the MRF, increasing corrosion inhibitor concentrations or using alternative inhibitors. If ferrous metal alloys are involved and if the pH can be kept in range, increasing the amine concentration or using less alkaline amines like triethanolamine (TEA) could help. However, with aluminum alloys, the amine concentration might need to be reduced and the pH lowered to 8.5 to 9.0
(see Figure 2). Alternatively, less aggressive amines could be substituted, potentially allowing higher-pH formulations. If staining occurs on copper alloys and an additive containing “active” sulfur is present, the fluid supplier can consider substituting a different lubricity additive without active sulfur or adding a copper corrosion inhibitor.
Figure 2. Evaluation of four aluminum alloys and one copper alloy in a 60% oil containing emulsifiable oil with (bottom row) and without (top row) a phosphate ester. Figure courtesy of Italmatch SC, LLC.
Problem: pH higher or lower than expected
MRF formulations should be alkaline enough to neutralize carbonic acid and acidic biodegradation products; otherwise, the pH may begin to drop quickly. MRFs generally contain TEA or other additives that counteract pH changes caused by microbes or oxidation during normal operations, a property known as “reserve alkalinity.” If possible, the reserve alkalinity of freshly diluted MRFs should be measured and compared with used fluid from the system. If alkalinity has decreased significantly, it could be due to low concentration, degradation by microorganisms, contamination or some combination of these factors. If significant alkalinity change is occurring, the MRF supplier should be consulted to troubleshoot and, if necessary, substitute a fluid with higher reserve alkalinity or greater bioresistance.
If the MRF concentrate has not been adequately mixed with water, the pH may be off. Verify the pH of MRF properly diluted in the lab with plant water, preferably using a calibrated pH meter. If the pH is more than 0.5 units above or below the range indicated by the fluid supplier, it could be due to chemical changes in the MRF concentrate, possibly caused by storage beyond the suggested “use by” date. The fluid supplier should be contacted to verify the pH results and, if indicated, to discuss possible substitution with fresh product.
If the pH of the lab test sample is in range, verify whether the MRF in the plant is being properly diluted and mixed with plant water. This can be done by sampling the sump and delivery nozzles after adequate mixing, based on system volume and pumping rates. Proportioners or other pre-mixing devices should be checked to ensure that they are set to deliver the correct ratio of water to concentrate. If a pre-mix tank is used, or the MRF concentrate is diluted in the sump (not recommended), the MRF should always be added to water, not water to MRF. An easy way to remember this is OIL (oil in last). This procedure helps ensure good distribution of the concentrate, and it reduces the likelihood of invert (water-in-oil) emulsions being formed. Keeping the temperature of the dilution water above 20 C reduces mixing time, especially with emulsion fluids.
MRF concentration should be verified using a refractometer, and if it is out of range, adjusted as needed until concentration and pH are in range. If the concentration is low, remove and save about 10% of the system volume. Add prediluted MRF concentrate at a higher concentration until the diluted fluid is in range. If the concentration is too high, the same volume should be removed, saved and replaced with prediluted MRF concentrate at a lower concentration to bring it into range. MRF removed from the sump, if properly aerated and not contaminated with excessive microbes, can be gradually added back over time. The concentration should be retested after the fluid has recirculated for a sufficient time to turn over the system at least twice, based on the MRF volume and pumping rate.
Sump contamination by old MRF, cleaners, tramp oil, microorganisms or other foreign material also can cause pH changes. If the system was not cleaned thoroughly before adding new fluid, high levels of residual microorganisms could be present and cause rapid pH changes. The MRF supplier should be consulted to determine if fluid analysis is required.
MRF concentrations should be checked at the start of every shift. Sudden or gradual changes in pH could indicate changes in the MRF concentration. If the concentration is decreasing, check for water inflows. If the concentration is increasing, confirm makeup fluid concentrations to ensure that they are dilute enough to compensate for water evaporation.
Ask the MRF supplier if non-biological degradation of certain fluid components could be causing chemical changes. Non-microbial sources of chemical changes in the MRF can include acids generated by hydrolysis, oxidation and catalytic effects on certain MRF components; for example, hydrolysis of certain esters can occur over time in the concentrated or diluted MRF. A more chemically stable MRF might be needed.
Microbial growth (bacteria and fungi) can generate acidic and alkaline biodegradation products; these vary with the types of nutrients in the MRF and other factors. If the pH change has been rapid, microbial concentrations are high and the fluid is underperforming, the system will probably need to be dumped, thoroughly cleaned, treated with a compatible quick-kill biocide solution (if recommended by the fluid supplier), rinsed thoroughly and refilled with fresh fluid. If the pH change has been gradual, microbial counts are not excessive and the fluid is performing well, ask the MRF supplier if they recommend addition of a tank-side biocide and pH adjuster.
Contamination with tramp oil, cleaners, metal fines or other substances also can cause pH changes. Machines should be checked for worn seals or other sources of tramp oil leaks, and tramp oil removal equipment evaluated for proper operation. Chip conveyors, sluiceways, sumps and filtration systems should be inspected for accumulated metals and cleaned if necessary.
Problem: MRF separates or forms solids
Reactions of anionic emulsifiers in the MRF with metals or multivalent cations from hard water can deplete the emulsifiers. This produces an unstable emulsion, in which the fluid separates into oil and water layers or forms a thick cream or solids on the surface. The fluid should be tested for bacteria and fungi, water hardness and, if possible, the levels of dissolved metals (Fe
2+, Fe
3+, Al
3+, Mg
2+, etc.). The MRF supplier can help determine causes and recommend solutions.
Some MRF chemistries are prone to suspending metal fines. Tramp oil contamination also can make a fluid more prone to suspending metal fines. Filtration and tramp oil removal equipment should be checked for proper operation and cleaned and repaired as needed. In some cases, the chip management and filtration systems might be inadequate. Factors to consider include settling equipment type and volume (which affect residence time, among other things) and filter media type (geometry, materials of construction, pore size, etc.).
Problem: Foaming
An MRF used above the recommended concentration range can be more prone to foaming, and some fluid types, such as certain semisynthetic fluids, are inherently more foamy than others. Modern system designs have smaller footprints, higher recirculation rates, higher pump pressures and shorter residence times, all of which can negatively influence foaming and air entrainment. MRF concentrations should be checked with a refractometer and adjusted with richer or leaner dilutions until in range.
Foaming also can indicate that the fluid volume in the system is too low. Low volumes reduce residence time, increase air space over the fluid and can cause waterfalls, all of which can exacerbate foaming. Systems should be checked for leaks and repaired as needed. The system should be filled, but not overfilled, allowing some free space for foam to accumulate. Sump volumes should be checked at every shift, and makeup fluid added to compensate for water evaporation, drag-out on parts and other factors. Installation of a low/high-fluid alarm can enable timely corrective actions.
Excessive foaming also may be an indicator of poor system design. The system should be evaluated for small diameter pipes and pipes with sharp bends. Pumps should be checked for proper sizing and to ensure that they aren’t prone to cavitation. Fluid delivery nozzles also should be evaluated for proper sizing (e.g., inside diameter).
Soft water (total hardness below 75 parts per million or ppm), and especially water that has been deionized or treated by reverse osmosis, can worsen foaming problems. Water hardness of 75-150 ppm should produce less foam, and water above 150 ppm hardness should foam least of all. If the available plant water is contributing to unacceptable foaming, the MRF supplier can advise if a tank-side defoamer should be added, or if calcium acetate solution should be added to artificially harden the water.
Microbes can generate biosurfactants that increase foaming. Tramp oil also can increase foaming indirectly, acting as a nutrient for microbes. If dip slide tests indicate that microbial concentrations are higher than desired, but the fluid performance is acceptable, the MRF supplier might recommend addition of tank-side biocide and defoamer.
Cleaners and tramp oils that contain certain types of surfactants also can produce foam. These sources can be confirmed using a simple hand shake test with glass jars or graduated cylinders. If cleaners are being introduced into the MRF system, the source should be determined and corrected. Tramp oil removal equipment should be inspected to ensure proper operation and regular use. Suppliers of hydraulic fluids, slideway lubricants and other fluids should be asked if their products can cause foaming and, if so, lower-foaming substitutes should be considered.
Some MRF formulations are inherently prone to foaming, and the MRF supplier should be consulted regarding lower foaming alternatives. If a similar lower foaming product is not available, ask the supplier if an antifoaming agent can be added to the concentrate
(see Figure 3). If antifoam is already present in the concentrate, ask the supplier to test your product to make sure that it hasn’t separated or stratified in the drum.
Figure 3. Defoaming additives rupture surfactant layers that can entrap air bubbles. Figure courtesy of Langbein Rise, Wikimedia Commons, CC BY 0.0.
Problem: Offensive or irritating odors
Strong odors might be a sign that the MRF concentration is too high. The concentration should be checked at every shift and adjusted. Cleaners and tramp oils also can be direct contributors to offensive odors, and the sources of such contamination should be identified and corrected.
Microbes degrade certain components of MRFs and tramp oils, forming odorous byproducts like short-chain fatty acids, and mist formation can increase the spreading of these odors. The MRF supplier should be consulted for recommendations, possibly including addition of a tank-side biocide.
Some odors come from the ingredients of the MRF. For example, sulfurized additives can form hydrogen sulfide (H
2S) and other odor-producers when degraded by certain microorganisms. Phosphorus additives can increase microbial growth and the associated odor problems. Some amines, such as dicyclohexylamine, are relatively volatile and can irritate workers. Certain organic acid salts can be irritating to the nose and throat, and several biocide chemistries can produce odors or irritation at higher concentrations. The MRF supplier might be able to recommend alternative fluids or chemistries if odors and biostability issues persist.
Problem: Skin irritation, rashes or dermatitis
Workers can sometimes experience skin problems caused by direct contact with MRFs. The irritation might occur immediately, or in the case of skin sensitizers, workers may experience allergic reactions after they are exposed repeatedly over time. Skin irritation can be reduced or prevented if workers wear suitable gloves, aprons and other personal protective equipment as recommended by the MRF or safety equipment supplier.
An MRF that is too concentrated increases the risk of irritating workers’ skin. Check the MRF concentration at every shift and maintain it in range, then assess whether this change reduces the workers’ skin problems. If irritation issues persist, alternatives should be discussed with the MRF and safety equipment suppliers.
An MRF that is too alkaline (pH above 9.5) can cause skin irritation. If the pH of the diluted fluid is too alkaline even at the weakest recommended concentration, a lower pH alternative should be requested from the MRF supplier.
Contaminants in the MRF (tramp oil, cleaners or metals like nickel, chromium or cobalt) can cause dermatitis, and possibly sensitization, and workers should be required to wear suitable personal protective equipment. Steps should be taken to remove as much contamination as possible and to maintain the fluid as such. If this isn’t feasible, it might be necessary to dump, thoroughly clean and refill the system with fresh fluid. Sources of contamination should be identified and minimized as much as possible by regularly removing metal fines and other contaminants.
Frequent tank-side treatment with certain biocides, including chloromethylisothiazolinone/methylisothiazolinone (CMIT/MIT) and triazine, can cause dosages to exceed the label limits, increasing the chance of skin irritation and sensitization. Keeping good records of bacterial and fungal concentrations, as well as tank-side biocide additions (types, dosages and dates), can help MRF and biocide suppliers diagnose problems; the suppliers might be willing to analyze biocide concentrations, if requested.
Certain other components of MRFs can irritate or defat the skin, and some can cause sensitization. A few corrosion inhibitors, such as mercaptobenzothiazole, are potential sensitizers. Some surfactants and coupling solvents can defat the skin and cause drying and cracking. Many amines can irritate the skin directly or leach cobalt from cemented tungsten-carbide tool materials, increasing the risk of heavy metal dermatitis.
Problem: MRF color is changing
Properly diluted emulsifiable oils form milky white or bluish white emulsions
(see Figure 4). A yellowing of the emulsion could indicate that the emulsion is losing stability. If the color of the MRF changes to creamy or yellow-white, the hardness of the fluid should be checked. If water evaporation has caused the hardness level to increase significantly, a reaction of hardness cations with anionic emulsifiers is probably causing the color change. Soft, or preferably deionized, water should be used for makeup additions, if it is available. If not, a higher fluid concentration might improve stability, or a more hard-water-stable fluid could be needed.
Figure 4. (Left) Properly mixed emulsifiable oils should appear milky white or bluish white. Figure courtesy of Glenn McKechnie, Wikimedia Commons, CC BY-SA 2.0.
Tramp oil can be emulsified into many MRFs, causing color changes and potential loss of performance. If this is the case, leaks should be identified and corrected, if possible. If tramp oil removal equipment is available, ensure that it’s working properly. Ask the MRF supplier to analyze the fluid for tramp oil and, if significant amounts are present, ask the supplier if a comparable oil-rejecting fluid is available.
Dissolved and dispersed metals and their corrosion products can discolor the MRF. The filtration and chip removal equipment should be inspected for proper operation and cleaned as needed. High metal concentrations increase the risk of fluid instability and loss of performance, and certain heavy metals (Ni, Cr, Co, Pb and others) increase the risk of dermatitis, sensitization and other potential health issues.
Microbes can directly cause microbially influenced corrosion, and they also can produce corrosion byproducts such as black iron sulfide. These corrosion products also can cause discoloration of the fluids.
Interacting problems require strategic solutions
Many factors influence the performance of machining systems. Some issues are related to the MRF/MWF, others are influenced by operational variables (covered in Part 1), and many (if not most) factors are interdependent. Regular condition monitoring of the fluid and complete and accurate recordkeeping are critically important. Good communication among all stakeholders can lead to faster problem solving and better long-term solutions.
For more details, consult the resources list in the Webinar article in the April TLT.
Nancy McGuire is a freelance writer based in Albuquerque, N.M. You can contact her at nmcguire@wordchemist.com.